Picking the Proper Mortar for Adhered Veneers
Thin Bed Adhesion Mortar
Thin bed mortar (also called “thin-set”) means ¼ inch mortar thickness instead of ½ inch which is standard for other mortars. It is available as a premium preblended polymer-modified thin-set mortar that has the best bond strength compared to standard AVM and PMAVM. It is intended to bond any manufactured veneer product (manufactured stone, brick, concrete products, or tile) or natural stone to a variety of substrates. Those substrates include hardened scratch coats with a smooth finish, concrete (properly prepared and free of curing compounds), concrete masonry units, cement backer boards, and interior gypsum wallboard with or without a primer (consult with the primer manufacturer for suitability). It can also be applied over suitable air and water barriers (AWBs) in exterior walls if they can support the weight (i.e., load-bearing AWBs).
Thin bed mortar can be blended to have an anti-sag formulation and use optimized sand gradation to provide superior workability, adhesion, and durability appropriate to both interior and exterior applications. Thin bed mortar also has the best freeze-thaw capabilities of mortar materials. However, it is not intended to be used as either a scratch coat or as a jointing material—it is to be used as an adhesion mortar only.
Thin bed mortars typically meet ASTM C270, CSA A179, and ASTM C1714 applicable requirements plus the ANSI 118.4 and/ or ANSI 118.15 standards when tested in a pre-blended condition. They also meet the TMS 402/602 Building Code Requirements and Specification for Masonry Structures shear strength requirements when tested in accordance with ASTM C482. When used with tile, it should follow the Tile Council of North America (TCNA) Handbook for Ceramic Tile Installation.
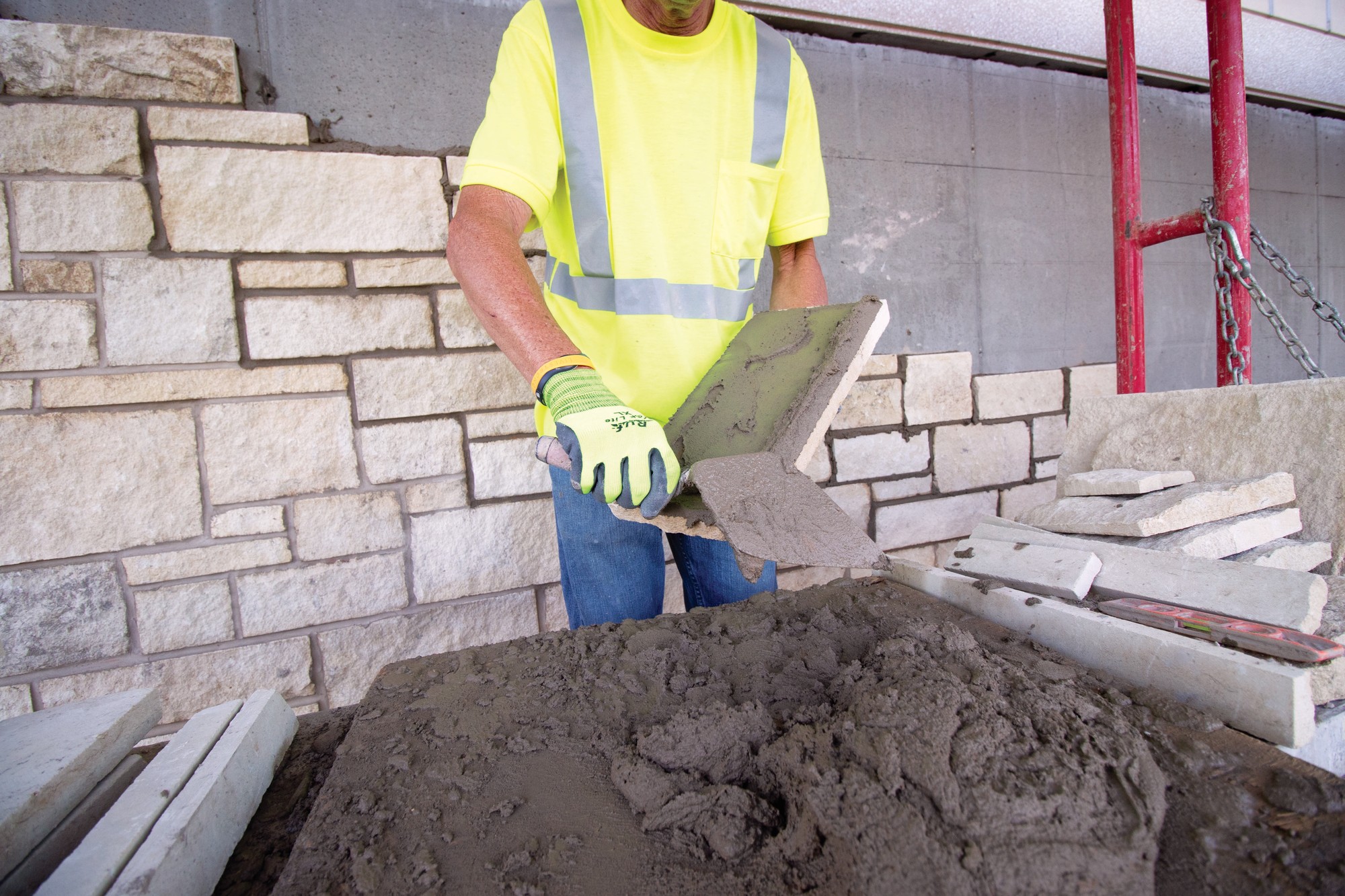
Photo courtesy of SPEC MIX
Modifying adhered veneer mortar with polymers improves performance characteristics, particularly for heavier pieces of stone or masonry products.
Mike Rolf is the National Sales Manager for Masonry Products at SPEC MIX and regularly sees the range of pre-blended mortars that are needed on many different projects. He notes, “Masonry mortars, particularly adhered veneer mortars, are engineered to meet the properties of the masonry units being installed. Whether it’s the unit’s density, porosity, or initial rate of absorption, all of these properties are considered to make customized mortars for high shear bond strength between the unit and the wall’s substrate.”
GREEN BUILDINGS AND MORTAR
Cement-based products, such as mortar and concrete, have received a lot of attention recently centered around their embodied carbon content in the manufacture and delivery of these products. In response, the industry associations and individual companies have been pursuing strategies to operate with responsible sustainable management to reduce their carbon footprint by reducing operations CO2 emissions. There is also ongoing collaboration within the industry for manufacturers to reduce their emissions and carbon footprint of cement-based products overall. Selecting products made by manufacturers with this commitment is a first step in meeting green building goals.
In terms of product makeup, mortar can be manufactured to meet specifications promoting the use of pre-consumer recycled content such as fly ash and or supplementary cementitious materials. Percentages of recycled content vary for each product and the properties are well measured by weight to meet rigorous standards of ISO14021 (International Standardization Organization).
On the project site, there are methods in place available to use pre-blended mortars in ways that reduce waste and encourage recycling. One such method is to have large packages of dry mortar shipped to the project site and then use a portable silo to store, mix, and aid in installing the mortar and veneer material. This approach helps contractors reduce overall job site pollution and waste by controlling the product production based on material needed at any given time during a project’s production schedule. This system also minimizes the need to dispose of unused products or discarding of empty bag waste that ultimately impacts the environment. The bulk bag system and nature of using preblended materials eliminate the need for sand and other aggregate piles that could leach into the groundwater, discharge into stormwater systems or blow into the atmosphere, lending to a high priority for health and safety. For every recyclable bulk bag of premixed construction product distributed to a project site, it is estimated that as many as 14 paper bags will never be produced nor disposed of in landfills.
Manufacturers of pre-blended mortars can also strive to minimize the carbon footprint of trucking goods. There are many North American production facilities strategically located close to metropolitan areas where the bulk of construction activity takes place. These facilities extract, process, and package their products for regional, if not local community distribution. It is, therefore, quite easy to find mortar plants and extraction points located within a 500-mile radius or less from jobsites.
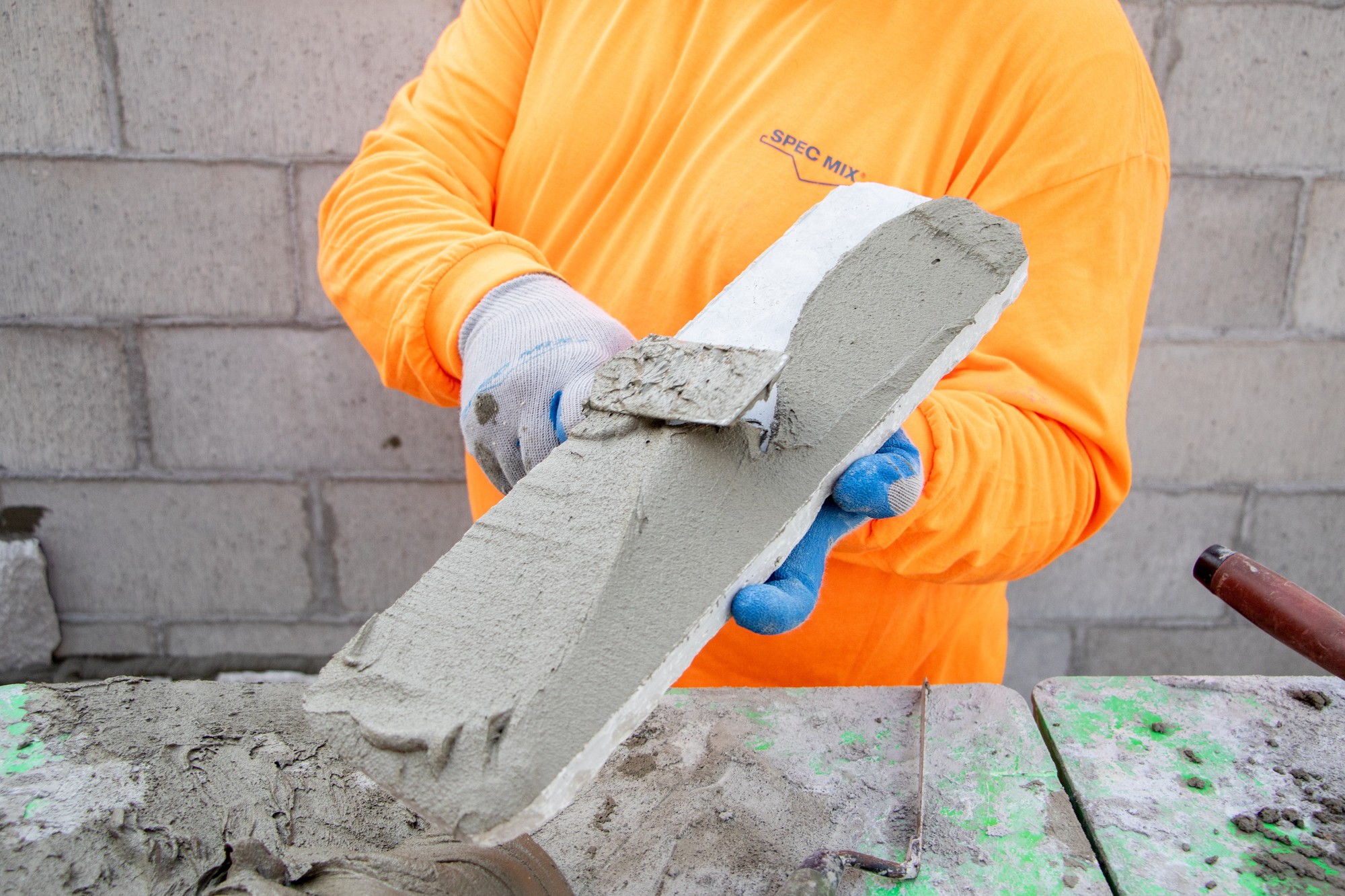
Photo courtesy of SPEC MIX
Thin bed mortar, also called thin-set mortar, is available in a premium, higherperforming blend for many different applications.
DESIGN AND CONSTRUCTION CONSIDERATIONS
It is important to note that any discussion of mortar also needs to address the importance of some of the design, detail, and installation methods of the veneer materials being installed. This helps to avoid the potential of someone claiming there is a “mortar issue” after the project is completed, when in fact a problem or imperfection may be related to some other part of the assembly. With that in mind, consider all of the following:
- Veneer Units: Different types of masonry veneer products have their own industry standards and installation guidelines. Following these documents for the proper installation of manufactured stone, natural stone, thin masonry, tile, etc. is the best way to achieve predictable performance. For example, the 5th edition of the Concrete Masonry Hardscapes Association (CMHA—formerly NCMA) Installation Guide for Manufactured Stone Veneer (MSV) (the basis for information in this entire section) covers many of the design, detail, and installation considerations needed to achieve a quality installation. MSV units installed in accordance with this guide must meet the minimum requirements of ASTM C1670/C1670M. “Standard Specification for Adhered Manufactured Stone Masonry Veneer Units.” NCMA Tek Note 20-01 “Key Installation Checkpoints for Manufactured Stone Veneer” is a supplement to these documents and should also be consulted. For installations that use lath, the appropriate standard should be followed such as ASTM C1063 “Standard Specification for Installation of Lathing and Furring to Receive Interior and Exterior Portland Cement-Based Plaster” should be consulted.
- Flashing: In exterior applications, flashing is likely to be needed and incorporated into the installation, either as an attached product or a self-adhered “tape”. Such flashing must be installed at all through-wall penetrations and at lower boundaries of adhered veneer installations. All flashing and flashing accessories must be corrosion-resistant and integrated with the WRB materials (if present). Generally, flashing is not required for interior applications if they are not exposed to water—if water is present then the installation should be treated like an exterior installation. In all cases, follow applicable building codes and manufacturer recommendations for flashing installation locations and material compatibility. Before installing an adhered veneer, verify that all flashing, including roofing kickout flashing, has been properly installed. Flashing material should extend above horizontal terminations, roofing material, and drainage planes or drainage products.
- Rainscreen Systems: Rainscreens have become a popular way to allow drainage in an exterior wall so any water or moisture can escape rather than be trapped behind claddings. Such a system can be part of an adhered veneer system if a rainscreen product such as drainage mats or formed polymer sheeting is installed properly as the substrate for the mortar to adhere to. Similarly, construction techniques such as strapping or furring can be used to create a capillary break or air space between the cladding and the water-resistive barrier (WRB). Manufacturer’s recommendations should always be followed for rainscreen / drainage system applications with adhered veneer wall systems. Note that building code requirements for rainscreens vary by region and can change between different versions of the code and should be verified in all cases.
- Weep Screeds and Casing Beads: Weep screeds and casing beads must be corrosion resistant, with weep screeds having a minimum vertical attachment flange of 3.5 inches that terminates behind the water-resistive barrier (if present). The minimum thickness of metal weep screeds and casing beads should not be less than 0.0179 inches (26 gage). For plastic weep screeds or casing beads, the minimum thickness is 0.050 inches. Some applications may not require the use of flashing, weep screeds, and casing beads to prevent water penetration. In cases where there is no WRB present, a weep screed is usually not required but a weep screed or casing bead can still be used for aesthetic purposes. In cases where a drip edge is needed based on a cladding transition, then flashing is required. The use of both flashing and a weep screed simultaneously is not typically necessary. Nonetheless, all flashing material should be integrated with water-resistive barriers to mitigate water penetration into the structure. The WRB should overlap the weep screed flange.
- Movement Joints: Different elements and materials within any structure move differently in response to applied loads or as a result of fluctuations in temperature or moisture content. Therefore, design consideration should be given to where differential movement is expected such as the intersection of dissimilar materials or at the transition between a framed backup assembly and a concrete masonry assembly. Consideration should also be given to placing movement joints in the substrate where recommended by industry standards. Different standards exist for scratch coat, CMU, and cement board substrates and movement joints should follow through the adhered veneer. The layout of the movement joints falls to the design professionals for a project.
- Lath: Many different lath materials have been used successfully for the installation of adhered veneers including self-furring metal lath meeting ASTM C847, welded wire lath complying with ASTM C933, 18 gauge (or heavier) woven wire lath meeting ASTM C1032, or others. All lath products need to be consistent with the veneer manufacturer’s installation instructions and ideally have an evaluation acceptance report from an accredited evaluation service showing compliance with code. All lath and lath accessories must be corrosion resistant, consisting of either galvanized or stainless-steel materials or consisting of materials complying with AC 275, and ASTM C1788. All lath material must be self-furred or use self-furring fasteners.
- Cement Board: Cement board may be used in place of lath and scratch coat if desired. When used, cement board must comply with ASTM C1325 “Standard Specification for Fiber-Mat Reinforced Cementitious Backer Units.” When using cement board, only modified mortars complying with ANSI A118.4 or ANSI A118.15 should be used as the setting bed mortar. Do not use conventional mortars with cement board installations. Refer to ASTM C1780 “Standard Practice for Installation Methods for Cement-based Adhered Masonry Veneer” and manufacturer recommendations for additional details on cement board installations.
- Fasteners: Corrosion-resistant fasteners need to be used to secure flashing and lath or cement board to the structural system. A variety of fasteners can be used such as staples, screws, and nails, provided the heads or washers of these fasteners are large enough to not pull through the lath or cement board and the fastener is of sufficient length to penetrate into the supporting material. For specific fastener selection criteria, refer to ASTM C1861 “Standard Specification for Lathing and Furring Accessories, and Fasteners, for Interior and Exterior Portland Cement-Based Plaster.” Generally, for wood or metal framing or panels using lath, corrosion-resistant staples, corrosion-resistant roofing nails, or corrosion-resistant screws and washers are needed. For cement board, corrosion-resistant cement board screws as recommended by the cement board manufacturer. Fasteners must be of sufficient length to penetrate a minimum of ¾ inch (19 mm) into framing members. For masonry or concrete walls or panels, corrosion-resistant concrete screws or powder-actuated fasteners (or cap fasteners) are recommended.
- Surface Preparation: Surfaces that are to receive adhered veneers must be structurally sound, free of any coatings or materials that would inhibit bonding, and capable of supporting the intended system. Masonry walls, poured-in-place concrete walls, and concrete tilt-up panels must be free of dirt, waterproofing, paint, form oil, or any other substance that could inhibit the mortar bond and must readily accept/absorb water in order to achieve good bond. The surfaces intended to receive adhered veneer units must have a rough texture to ensure good mortar bond. The International Concrete Repair Institute, (ICRI), provides guidance for concrete surface preparation and assessment. Refer to ICRI Technical Guideline 310.2 for additional information on concrete surface preparation, including information on Concrete Surface Profile (CSP), a standardized method to measure concrete surface roughness. A CSP equal to or greater than 2 is usually acceptable for installation over concrete and masonry assemblies. If necessary, cleaning may be done with power washing or mechanical methods (i.e. shot or bead blasting). If a bondable surface cannot be achieved, attach lath and scratch coat before installing any adhered units.
- Clearances: On exterior frame walls, weep screeds, and other base flashings should be held a minimum of 4 inches above grade or a minimum of 2 inches above paved surfaces. This minimum can be reduced to ½ inch if the paved surface is a walking surface supported by the same foundation that supports the wall. Where the backing is concrete or masonry, maintain 2 inches clearance from grade or ½ inch from a paved surface provided that frost heave of adjacent surfaces is taken into consideration.
- Cold Weather Application: Adhered veneer applications should be protected from temperatures below 40°F (4°C) during and immediately following installation. The use of anti-freeze admixtures to lower the freezing point of the mortar is not recommended. Accelerating admixtures may be used provided they comply with ASTM C1384 “Standard Specification for Admixtures for Masonry Mortars” and that admixtures containing calcium chloride are not used. Any veneer pieces containing visible frozen moisture shall not be installed.
- Hot Weather Application: If the environmental conditions during installation exceed 90°F (32°C), additional water may be needed on the scratch coat surface and the backs of the adhered veneer being installed. Providing shade and/or frequent misting of the wall may be required. Consult with the mortar manufacturer to determine if hot-weather mortar mix options are available.
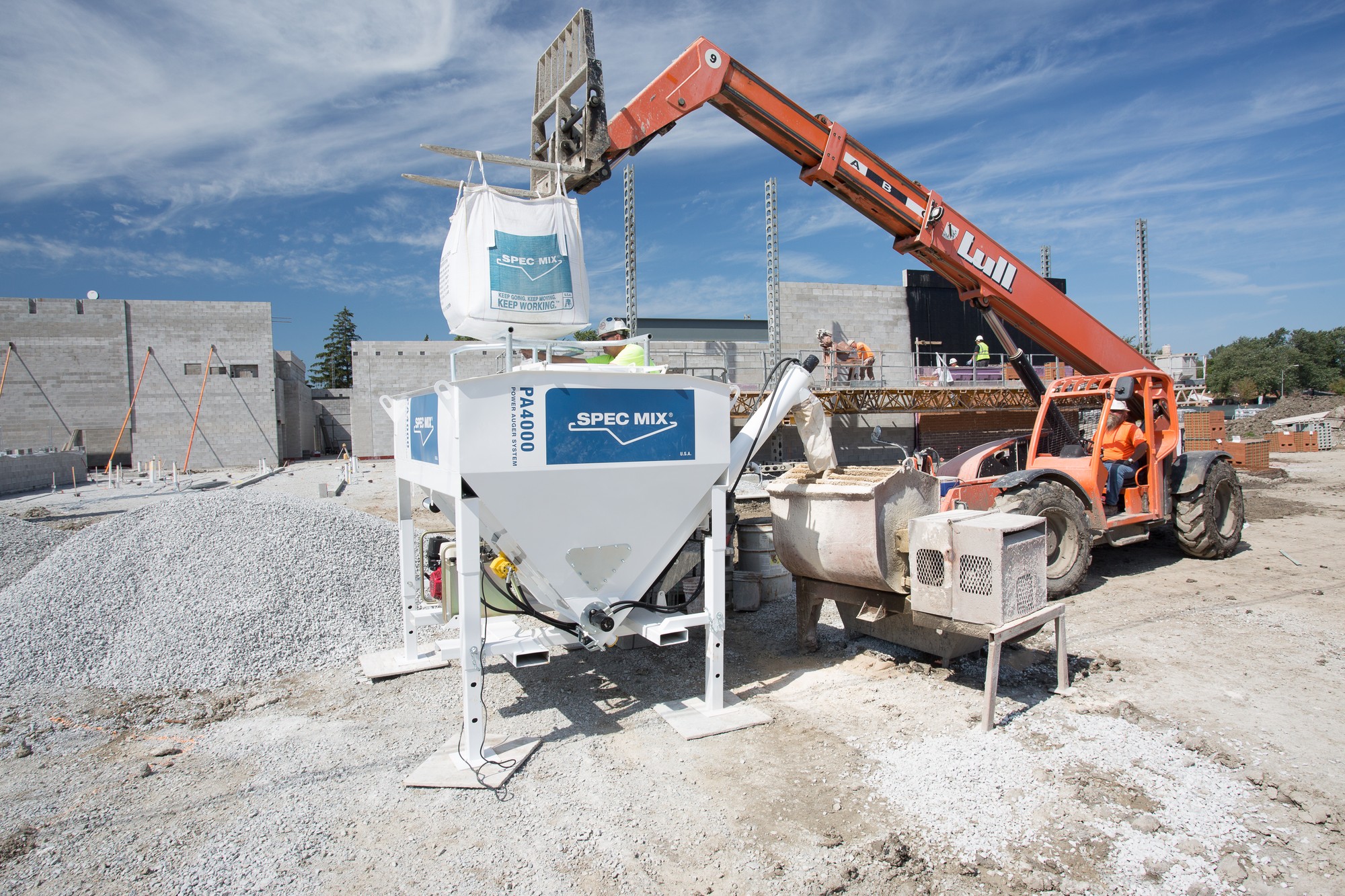
Photo courtesy of SPEC MIX
Using preblended mortar that is delivered in bulk with silos for adding water and processing manages resources and eliminates waste.