Using Charred Wood for Exteriors and Interiors
Cost Considerations
Since this is a vernacular material, affordability has always been associated with yakisugi in Japan. It tends to maximize millwork tradecraft, so making it is more knowledge-based than expense-based. That means it should have good value compared to other cladding options, although a particular vendor’s price might reflect custom millwork, high overhead, or pricing strategy. In reality, the Japanese heat treatment process does not add much production cost to the wood product so yakisugi should not be much more expensive, if at all, compared to other stain-grade wood siding options. Of course, when long term durability and little need for maintenance is considered, long term cost performance is usually quite favorable.
GREEN BUILDING CONTRIBUTIONS
When yakisugi is incorporated into a building design or renovation, there are several contributions that may be made based on green building standards due to their inherent material make-up, the way that they are used, and general characteristics. These can include the following.
Materials and Resources
Life cycle assessments show that wood cladding in general is better for the environment compared to other building material choices—1/15th the carbon of cement board, for example. In terms of carbon capture, wood planking, including yakisugi, can be carbon neutral or even carbon negative with up to 2 kg of carbon captured for every 1 kg of material shipped. Yakisugi by nature is less carbon-intensive to manufacture since it is air-dried before being subjected to a short- duration heat treatment in a recirculating type of kiln. Other wooden siding products, especially chemically treated wood or thermally modified wood by the Finnish process, are subjected to a days-long kiln drying process. The amount of energy consumed to modify yakisugi is therefore lower by nature than modern wood modification treatments. The long life and durability of yakisugi also support a favorable life cycle assessment since replacement is not needed for many years into the future.
Since authentic yakisugi cannot be made without the traditional manufacturing processes described, it is never made from reclaimed wood, driftwood, or chemically treated wood. Nonetheless, it can be sustainably harvested in Japan. While the Forest Stewardship Council (FSC) is recognized in the U.S., internationally, PEFC, the Programme for the Endorsement of Forest Certification is more commonly referenced. This non-profit, non-governmental organization is a leading global alliance of national forest certification systems. Manufacturers who adhere to their standards and programs produce a chain of custody certification for sustainably grown and harvested wood, including sugi cedar.
When looking at product delivery, it is notable that finished products are more efficient to ship than raw materials. Further, ocean freight has a much lower carbon footprint than regional trucking or even transcontinental rail freight in terms of pounds moved per mile (the typical ratio is ocean = 1, trucking = 7.1, rail = 4.9). Hence, it is not a given that a locally produced product is more sustainable than one that is shipped from a distance.
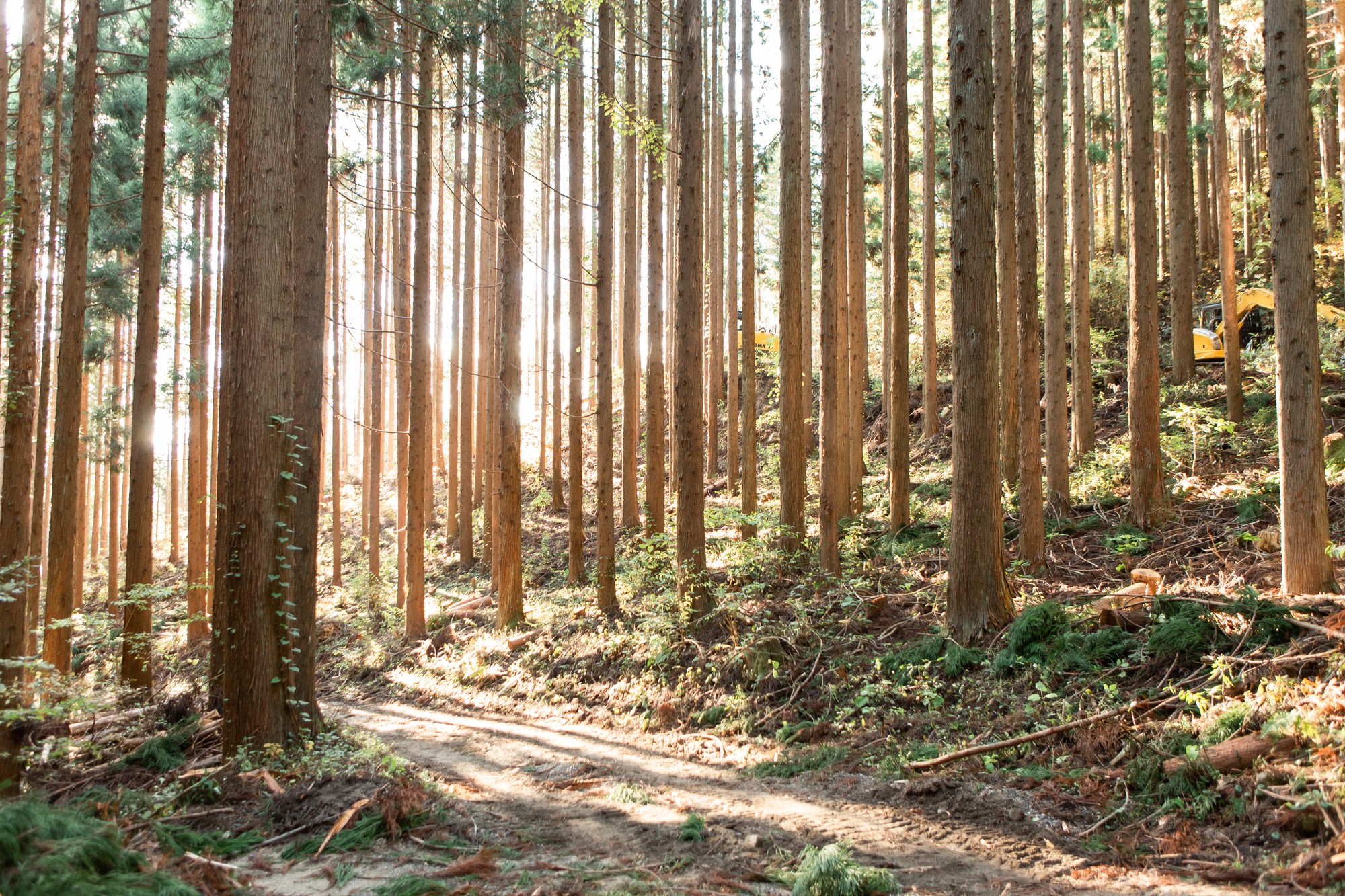
Photo courtesy of Nakamoto Forestry North America
Japanese or sugi cedar can be sustainably harvested from forests that are managed and certified following international protocols.
Indoor Environmental Quality
When used for interior applications, it is significant that yakisugi is a low-emitting material. Coatings are generally used by manufacturers to seal in the soot, but low- VOC plant-based coatings can be specified. Uncoated yakisugi is also common for ceiling applications. Relatedly, a growing interior design trend that has been directly related to human health and welfare is the use of biophilia in buildings. Defined literally as a love of living things or a love of nature, biophilic design is a concept focused on increasing occupant connectivity to the natural environment in creative ways. Theorists argue that this approach taps into the hard wiring of human beings who, over the span of history, have developed an affinity for the life-supporting aspects of the natural world. Independent researchers have long been aware of the health and wellness benefits of such features in many different building environments. Natural or heat-treated wood used on the interior of a building supports this biophilic design approach. It is also notable that cedar lumber has some positive effects on indoor air quality. First, it is prone to off-gas beneficial chemicals such as terpenes that improve emotional health by providing a relaxing effect and easing pain. It reportedly can also filter pollutants from the air as the wood is exposed to them—yakisugi has historically been applied to ceilings as an air purifier in interior applications.
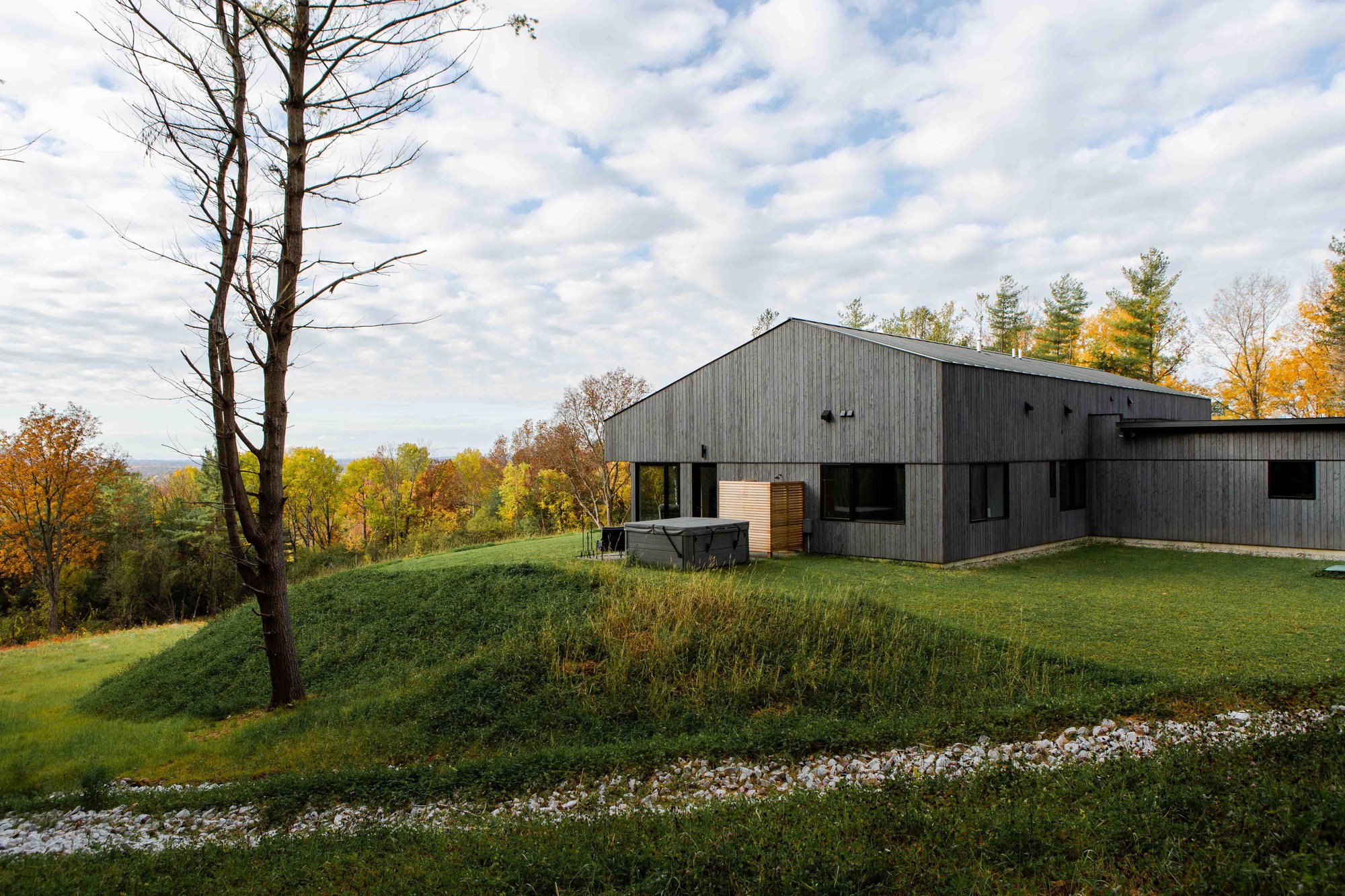
Specifying different finishes, different fasteners, and different types of yakisugi products can produce notable designs and strong performance.
SPECIFYING YAKISUGI IN BUILDINGS
When specifying yakisugi it is advisable to first talk with manufacturers or suppliers of such products to understand and assess the available product offerings and possibilities. It is also helpful to review industry standards and model specifications that can be edited for specific projects, whether new construction or renovation. In a standard, three-part specification format following the CSI MasterFormat system, charred wood siding, and paneling are commonly found in Division 06 Wood usually under Section 06 26 00 or a subsection thereunder. Some of the relevant items to address are highlighted as follows.
Part 1: General
The scope or extent of specified work as well as any definitions should be called out along with references to other related work. Quality control can reference ISO 21930 and ISO 14025 products and manufacturers. Submittals and samples can be requested based on the project needs, including the request for any green building standard documentation if any relevant credits are being pursued. Project conditions and product storage should all be addressed in a typical fashion with a particular emphasis on temperature and moisture. It is also advisable to have the material acclimate at the project site for at least 14 days.
Part 2: Products
All of the different performance and material criteria for the different products specified need to be called out. This includes the sizes, treatments, material choices, and textures for rainscreen furring, exterior siding, interior paneling, fasteners, and adhesive. If factory- finished products are called for, then the details of finish material, color, and number of coats need to be specified and differentiated for different applications or locations as shown on drawings. Any related materials or accessories provided by others should either be specified in this spec section or be referenced in other relevant specification sections.
Part 3: Execution
As with any site-installed product, the instal- lation requires multiple steps that need to be clearly articulated in the specification in order to achieve the best results.
- Examination and Preparation: The importance of this step should always be stressed. The installer and general contractor or construction manager should review and examine the substrate for conditions that may affect the installation or the overall performance of the wood siding or paneling. Any issues will need to be corrected, likely by the general contractor, if they are found to be out of compliance with the stated requirements.
- Installation: Furring first needs to be installed for rainscreens followed by the yakisugi products in the pattern and layout designed. When the yakisugi needs to be cut, only a sharp, ultra-fine carbidetipped finishing saw should be used. All long joints should align (butt joints may be staggered) and be nailed to a solid bearing behind. Wood siding should be installed after any adjacent masonry is installed since masonry work can be rather dirty and find its way onto the wood. The recommendations and procedures of the product manufacturer as well as the applicable requirements of codes and standards should be followed in all cases.
- Cleaning and Repairing: Once installed and finished, the surface should likely be able to withstand use by the remaining construction personnel on the project. However, the general contractor should be instructed to cover and protect any surfaces that are vulnerable to damage or abrasion, particularly in high-traffic areas. Most products are factory-oiled
to lock in the soot and minimize any transfer to adjacent surfaces, but handling and cutting the wood may release some.
It is recommended that all yakisugi and adjacent walls should be washed down with a hose or wet rags. The final step is to touch up any blemishes from handling and installation by dabbing with touchup oil and blending with a rag.
When designed, specified, and installed correctly, yakisugi siding or paneling can readily provide the desired look, the general health and wellness benefits, and the long- term performance characteristics which are intended.
CONCLUSION
Yakisugi/shou sugi ban is a unique and organic wood product, with different characteristics and specifications from standard millwork. Form follows function with these products, and rigid millwork and drying protocols need to be followed for the planks to stay straight through the high-temperature heat treatment process. While grading and millwork produce consistent products, it is somewhat exotic, and sooty, and will patina over time for a variety of design outcomes. Architects should become completely comfortable with the product design and performance capabilities before specifying it for any project. Ultimately, it contributes to buildings that are beautiful, sustainable, and durable.Peter J. Arsenault, FAIA, NCARB, LEED AP is a nationally known architect who has authored nearly 300 continuing education courses focused on advancing building performance through better design. www.pjaarch.com, www.linkedin.com/in/pjaarch