Using Charred Wood for Exteriors and Interiors
Wood Plank Details
Beyond the pattern and appearance, there are two other fundamental design decisions to be made related to the wood. The first is the grade of the wood to be used. The standard grade will contain some knots visible in the grain which may be visible if a wire-brushed product is selected with an unfinished, transparent, or semi-transparent finish. That may be quite desirable since the look can be dramatic, showing and enhancing the contours of the grain. In other cases, a premium grade may be preferred with no knots and a smoother, more contemporary appearance. The premium grade comes with a corresponding premium price, of course, so it would not make sense to use that for an unbrushed charred surface but solid stains, like acrylics and alkyds often look quite good with premium clear grade wood since the texture is so noticeable.
The second choice is to be clear on where shiplap-edged boards are used and where square-edge boards are to be used. Commonly, the siding boards rely on the shiplap edges to create the joints between them, however, 9/16-inch square edge boards are also used, particularly in rainscreen applications where the boards are separated slightly. Trim pieces at siding edges, around openings, etc. are commonly 5/4 stock square- edged material. The distinction between these should be made on design drawings and followed through in project specifications.
In order to put all of the above in an overall design context, William Belek, President of Nakamoto Forestry, North America points out what he often discusses with architects. “People are so focused on the coating, but the lumber and the millwork are the real essence of the products. That’s the real secret—the quality of the lumber and the quality of the milling should be used to identify the quality of the finished product.” He also points out a caution when comparing products or samples indicating “Finishes are certainly used, although not needed with quality products. However, heavy coatings can be used by some producers to hide low-grade millwork.”
PERFORMANCE CHARACTERISTICS
Based on the foregoing, it is easy to see why yakisugi is a rather sophisticated manufactured material with heat processing or charring much more than just a finish. When properly produced, authentic yakisugi combusts away the hemicellulose in the wood fibers, making the material much more resistant to the weather including airborne rain and moisture and ultraviolet rays (UV) from the sun. The lack of hemicellulose along with the high mineral content and fast drying times of the finished boards means that bugs, termites, and fungi have nothing to feed on so are not attracted to it. There is also less likelihood that rot and mold will set in. All of these factors add up to a product that has increased durability and can last longer than many other siding options.
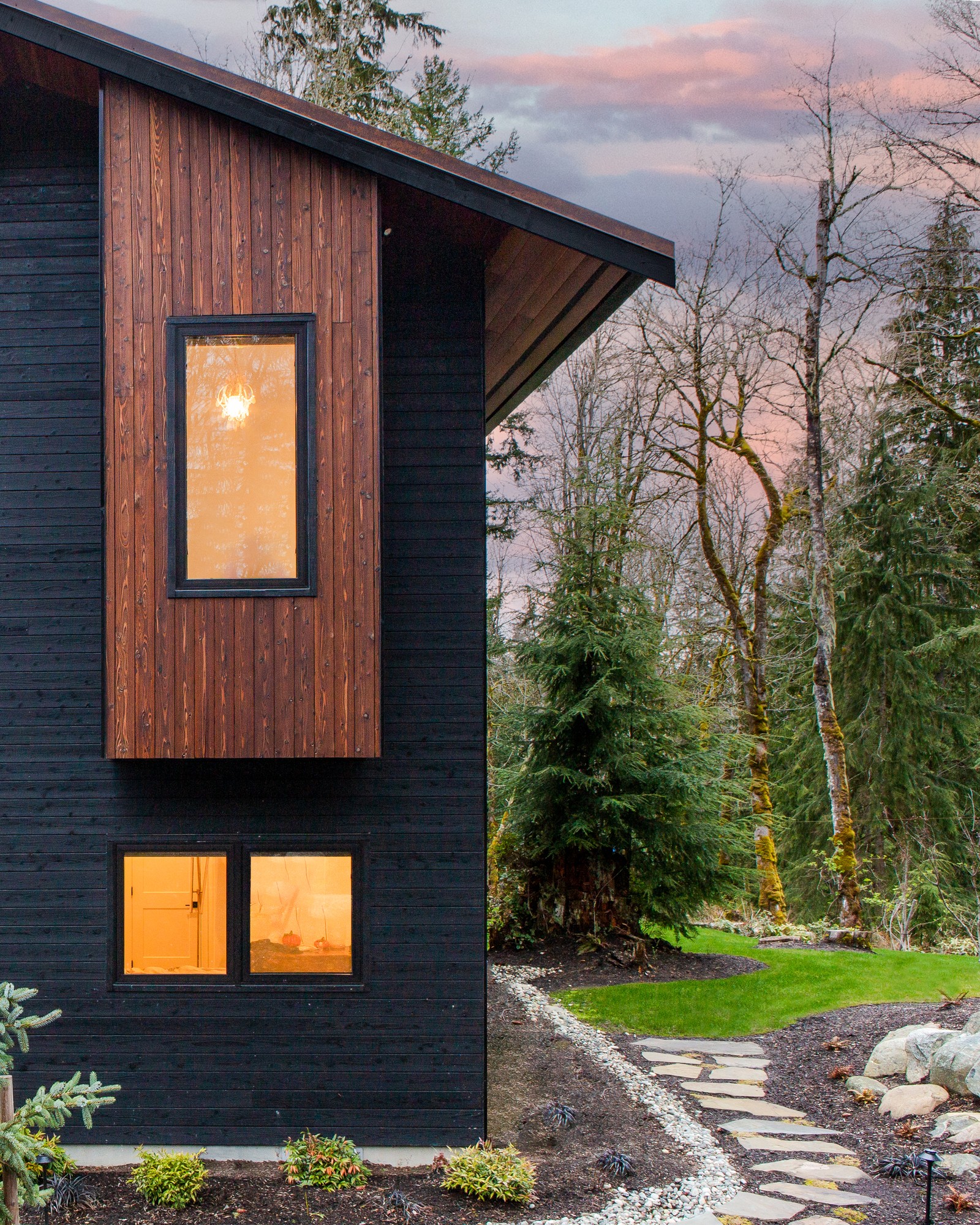
Photo courtesy of Nakamoto Forestry North America
Using different orientations of siding and different finish treatments can provide dramatic design results.
In terms of fire resistance, the charred, hardened, lignite surface also means that it takes longer for fire to affect the wood. Attesting to this fact, ASTM E-84 testing standards have been used resulting in Class A fire resistance ratings available for many yakisugi products. If required for a particular project, yakisugi can also be treated with a flame retardant—consultation with a manufacturer is suggested if that is the case.
Yakisugi is time-tested in Japan which is a long country (north to south latitudes) with climates ranging from semi-tropical to Siberian. Due to its durability yakisugi has been used primarily along the coast and in the humid south for hundreds of years. This suggests that yakisugi will probably outlast any other softwood in any climate. It does need to be installed properly in a wall assembly, though.
Exterior Wall Design
Exterior siding or cladding of any type is not intended to be a waterproof barrier, rather it is meant to shed water and protect the wall assembly behind it, especially the primary water barrier, from UV. Water will always get behind any siding and one of the critical aspects of the long-term durability of all wood siding is that the cladding allows water to weep away and dries quickly. The common way to achieve this is to use a rainscreen wall design.
For purposes of residential or low-rise commercial buildings, a rainscreen is an exterior skin system made up of siding/ cladding installed so that it is separated from the structural wall with an air gap that allows for drainage and ventilation, both of which allow for drying. The important surface is the weather-resistive barrier (WRB) that is installed continuously over the exterior face of the structural wall (e.g., wall studs with OSB or plywood sheathing). In the case of wood siding, the air gap is often created using furring strips nailed through the WRB and substrate. The siding is then installed onto the furring strips creating the space for ventilation and drainage resulting in drying. The air gap also allows any water vapor that’s expelled from the structure’s interior to escape instead of condensing and becoming trapped between the WRB and siding, creating an environment where fungi can grow.
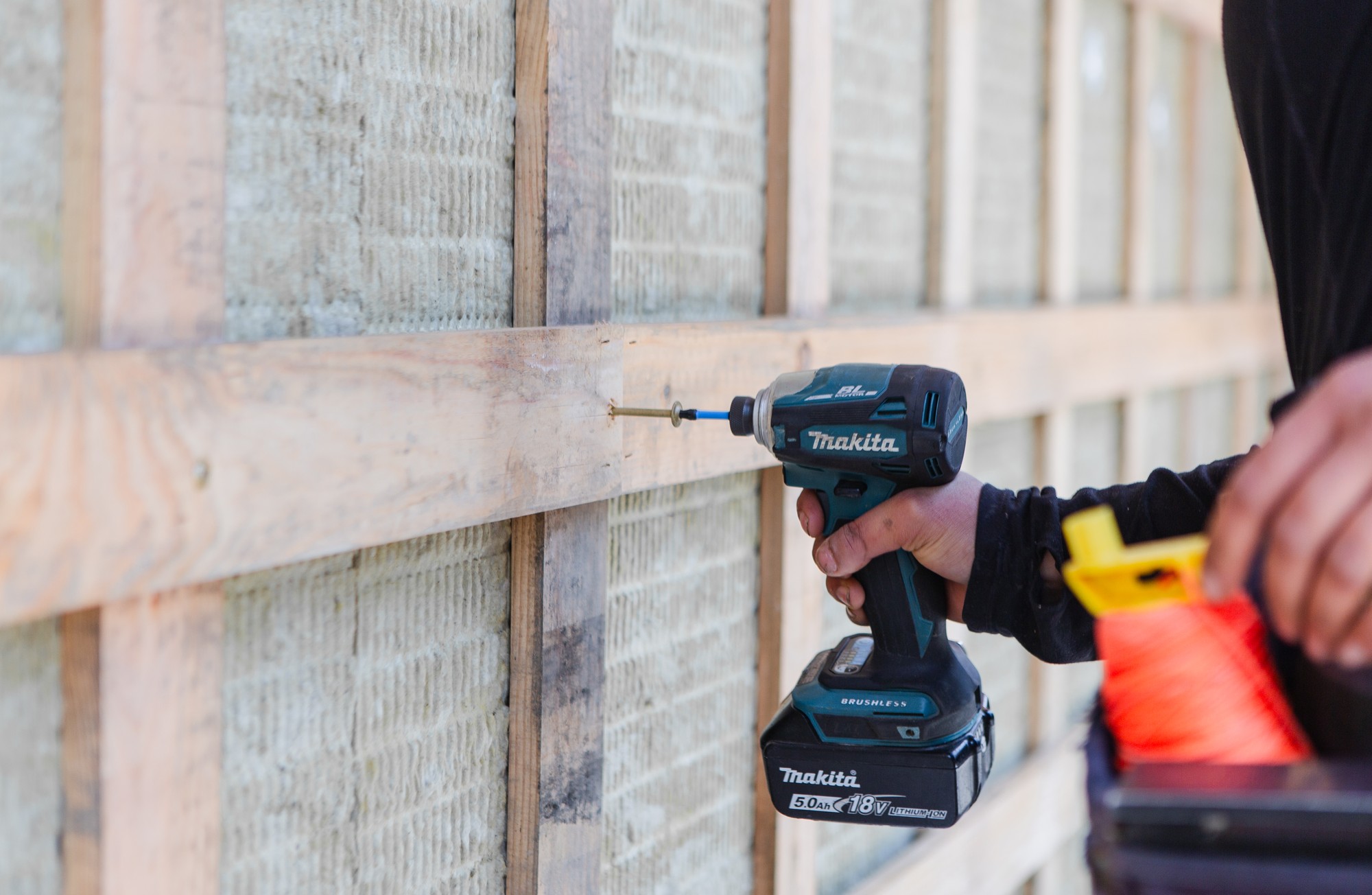
Photo courtesy of Nakamoto Forestry North America
The use of rainscreen construction is regarded as a best practice for all types of cladding on exterior walls.
It is worth differentiating between furring used for drying (ventilation and drainage) compared to furring used only for siding attachment. Horizontal siding layouts work well since vertical furring provides both drying and siding attachment with fasteners penetrating into the substrate. However, vertical siding layouts need more attention. One layer of horizontal perforated engineered furring can be used that allows drying and fasteners that penetrate into the substrate. Alternatively, two layers of wood furring can be used—first a vertical layer for drying, and a second horizontal layer with sufficient siding fastener pull-out strength. Properly installed, furring does not need to be treated with a rot preventative since it generally stays dry and will dry out very quickly if wet.
Directly related to a rainscreen wall design is the shape of the siding and the manner in which it is secured. Some people believe that tongue and groove (T&G) boards are best because they keep water out best and should be blind nailed for best appearance. The fact is that T&G profiles create more water tension at the board joints which weeps and dries slower than shiplap or square planks. That means T&G will wick water and rot on an exterior unless it is covered by a roof. Proper millwork and heat treatment correctly executed for yakisugi produce a dimensionally stable material, so a locking-type T&G pattern is not necessary. Additionally, a thin T&G profile can’t be burned deeply enough to heat treat. The square edges on T&G (or channel lap) will melt if thoroughly burnt and wavy parallel lines simply do not look good. Based on all of the above, the best choice for a siding profile is shiplap.
Relatedly, exterior wood cladding, particularly yakisugi, cannot be blind nailed since hidden fasteners cannot be tightened during future maintenance. The wood will always move over time due to moisture fluctuation and latent instability in the planks. Face-nailed siding will move less and look better over time since headed fasteners have higher strength and can be easily tightened up periodically with a hammer. Also, due to the high-temperature heat treatment process, yakisugi is by nature a thin-stock material too thin for hidden fasteners.
The recommend face-nailing fasteners include headed, ring-shank stainless nails or screws at least 1-3/4” long. Some custom- ordered black factory-painted stainless nails and screws are also available from manufacturers to blend in with black or dark-finished boards. Other nail colors such as brite, brown, white, or gray are commonly available depending on the design intent. For interior applications construction adhesive and finish nails work well. case study #2
Maintenance Considerations
Historically in Japan, no maintenance is done at all to yakisugi until it starts to fall apart after about a hundred years. At that point it is patched or replaced, provided that the building is still in good usable condition. During the useful service life of the siding, weathering from the elements leaves a patina, or a “wabi-sabi” aesthetic—the beauty from variations or imperfections as it is expressed over time and change.
In North America, building owners may or may not be accepting of a color and appearance change over time. Either the color change can be accepted as it progresses, or an oil stain can be applied to restore or change the appearance. While in Japan yakisugi is rarely re-oiled, in the West, fresh color via re- oiling is the cultural norm. Color longevity is usually the main object, but regular re-oiling will also allow the siding to last longer.
The only other recommended maintenance is to tighten up fasteners after a few years and then every decade or two over time. The substrate and siding will naturally move due to weather and pull out the fasten- ers little by little. So gently tapping them back in with a hammer will return the siding to a flat plane again. This is usually optional and often unnecessary.