Designing Sustainable, Prefabricated Wood Buildings
Types of Prefabricated Wood Components
Prefabricated wood components may include light-frame walls, floors, and roof trusses or mass timber elements such as cross-laminated timber (CLT) panels, nail-laminated timber (NLT) panels, dowel-laminated timber (DLT) panels, and glue-laminated timber (GLT) columns and beams.
Light Wood Frame
Light wood-frame construction has long been the go-to framing choice for low- and midrise and, increasingly, commercial buildings. Cost-effectiveness, material use efficiency, ease of assembly, minimal environmental impact, and the ready availability of labor and materials make light wood-frame construction the most common type of wood construction in North America. Typical light-frame roof and floor systems consist of repetitive framing members such as rafters or trusses with wood structural panel decking. Framing components include solid sawn dimension lumber, I-joists, structural composite lumber, and parallel chord and pitched trusses. Oriented strand board (OSB) and plywood are used interchangeably as decking and sheathing material for floors, walls, and roof decks. There are several approaches to light wood-frame construction, and each is suited for a specific application, most often in Type III and Type V categories. As mentioned, on-site framing for light-frame construction is still the industry norm, but increasingly elements of these buildings are prefabricated off-site and assembled on the job.
Cross-Laminated Timber
Mass timber is a category of framing styles typically characterized by the use of large solid wood panels for wall, floor and roof construction. Cross-laminated timber panels are formed by stacking and gluing together successive perpendicular layers of wood. The layered stacks are then pressed in large hydraulic or vacuum presses to form an interlocked panel. The panel is then sized and shaped with a CNC machine into a construction-ready component. The number of layers in a panel can range from three to seven or more, and panels can have door and window openings as well as routings for electrical and mechanical systems installed before shipment to the building site. In addition to glued CLT, manufacturers have also developed a mechanically fastened CLT using carefully engineered fastening patterns rather than adhesives and pressure.
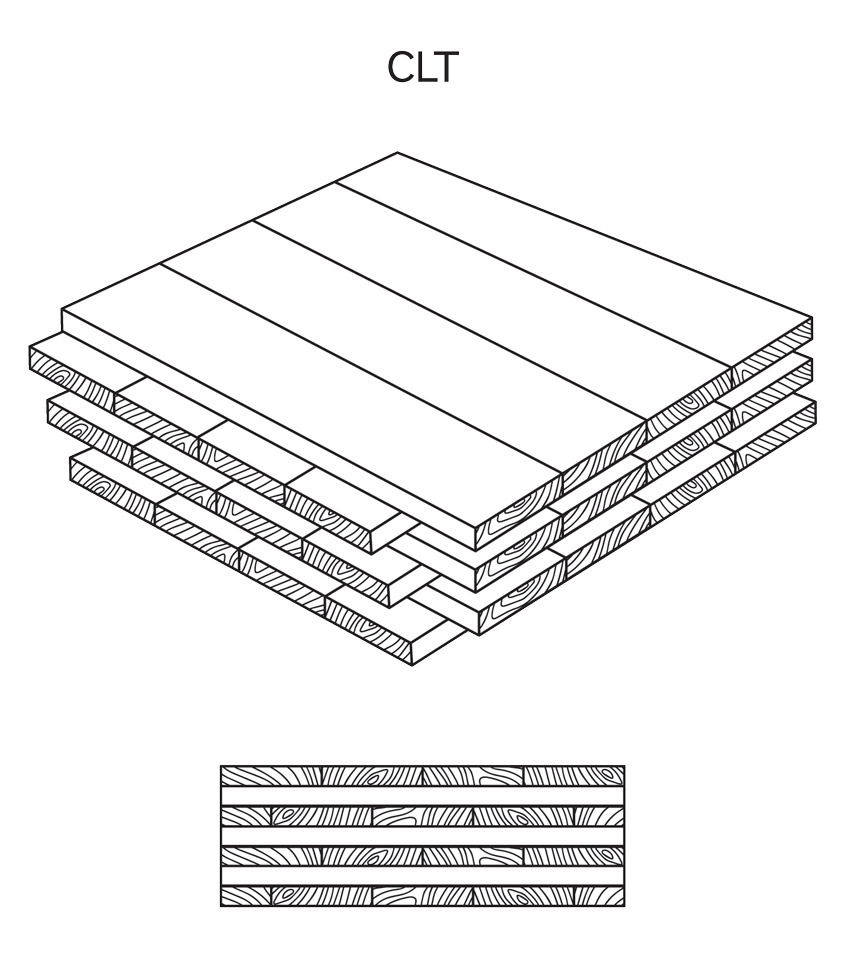
Cross-laminated timber panels are formed by stacking and gluing together successive perpendicular layers of wood. Often all machining and milling of holes is performed at the CLT producer’s plant based on the fabrication drawings and CNC machine files, and the product is shipped straight to site.
The cross-lamination process provides improved dimensional stability to the product, which allows for prefabrication of long, wide floor slabs, long single-story walls, and tall plate height conditions needed for clerestory walls or multistory balloon-framed configurations. By the nature of its design, CLT has inherent load-bearing strength and can serve as material for both vertical and horizontal assembly applications. Since wall, floor, and roof sections made of CLT are formed off-site in a factory, on-site construction time is much shorter. CLT can be used as a structural system in Type III, IV, and V buildings today and in tall wood buildings under alternate means.
Often all machining and milling of holes is performed at the CLT producer’s plant based on the fabrication drawings and CNC machine files, and the product is shipped straight to site. Other times, the product is shipped to a fabrication shop for further fitting of steel connections to speed up site erection.
Nail-Laminated Timber
Nail-laminated timber is a mass timber panel system that can be used for floor, wall, and roof structures. NLT floor and wall assemblies have been used for more than a century, particularly in warehouses where solid, sturdy floors were required; it is now being recognized again as a valid substitute for concrete slabs and steel decking in commercial and institutional buildings and residential buildings where it is often exposed to create a unique aesthetic. NLT is created from dimensional lumber stacked on edge—2x4, 2x6, 2x8, 2x10, or 2x12 at 11⁄2 inches on center—and fastened together with nails. Plywood sheathing is often added to one top side to provide a structural diaphragm. Plywood sheathing also allows the product to be used as a wall panel element.
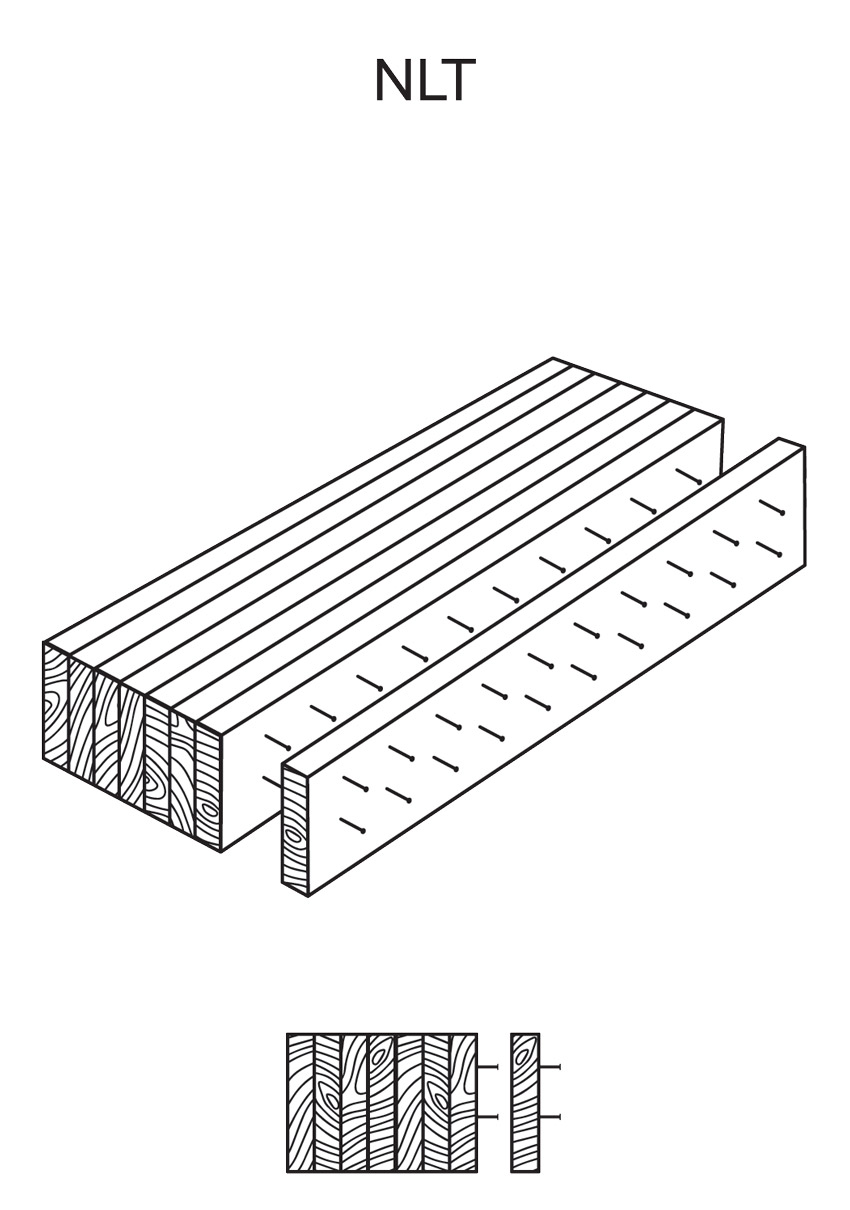
Nail-laminated timber is created from dimension lumber stacked on edge and fastened together with nails. Plywood sheathing is often added to one top side to provide a structural diaphragm and allow the product to be used as a wall-panel element.
Glue-Laminated Timber
Glue-laminated timber (also called glulam) is a structural engineered wood element commonly used for beams and columns in residential and commercial applications. To form a glulam component, dimensional lumber wood laminations are positioned according to their stress-rated performance characteristics. In most cases, the strongest laminations sandwich the beam in order to absorb stress proportionally and ensure the member’s longevity. The laminations are jointed end to end, allowing for long spans, and are bonded with a durable, moisture-resistant adhesive. The laminations’ grains run parallel with the member’s length to improve its strength.
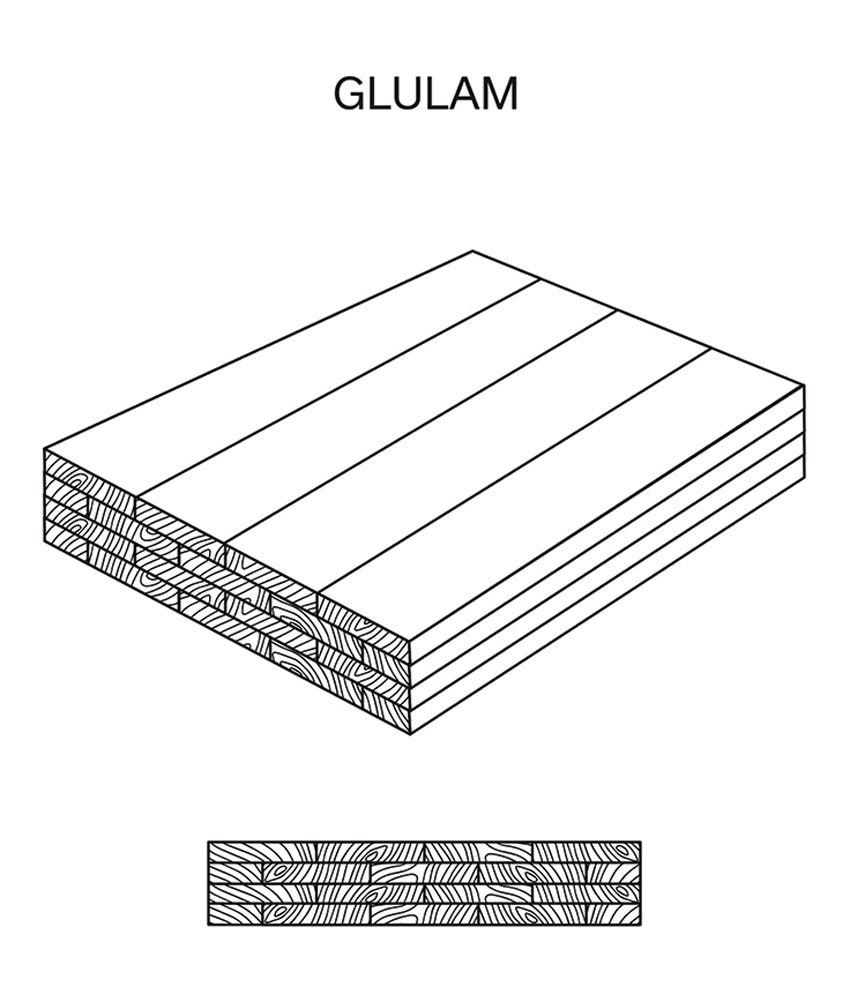
Glulam is stronger than steel at comparable weights, and it is stronger and stiffer than dimensional lumber.1 That makes the material a cost-effective choice for long, structural spans and tall columns with minimal need for additional support.
Glulam is stronger than steel at comparable weights, and it is stronger and stiffer than dimensional lumber.2 That makes the material a cost-effective choice for long, structural spans and tall columns with minimal need for additional support. Glulam is a highly visible form of mass timber in contemporary projects, with long spans framing signature designs that have been left exposed to take advantage of wood’s natural aesthetic. In addition to being used in floors, decks, and roofs, GLT and NLT mass timber panels are now used for timber elevator and stair shafts in six-story, light wood-frame residential midrise apartment buildings.
GLT also offers the advantage of being fabricated in controlled environments based on certified manufacturing standards. Like CLT, machining and milling of holes is often undertaken at the producer’s plant before the product is shipped to the site. Other times the panels are shipped to the fabricator’s shop for further fitting of steel connections.
Dowel-Laminated Timber
Dowel-laminated timber is a mass timber product that is wood and uses wood dowels as the connector. From larger panel sizes (12 feet by 60 feet) for faster erection times to a wide variety of wood species, DLT is a mass timber product that is ideal for floor, wall, and roof structures. DLT does not include any glue, chemicals, volatile organic compounds (VOCs), or nails, equating to a healthier indoor environment. And because there are no nails or metal fasteners, DLT is easy to process through CNC machines. Unique to DLT as a mass timber product, a wide variety of profiles can be integrated inexpensively into the bottom surface of the panel. Profiles are fully customizable to suit the particular performance and aesthetic requirements of each project.
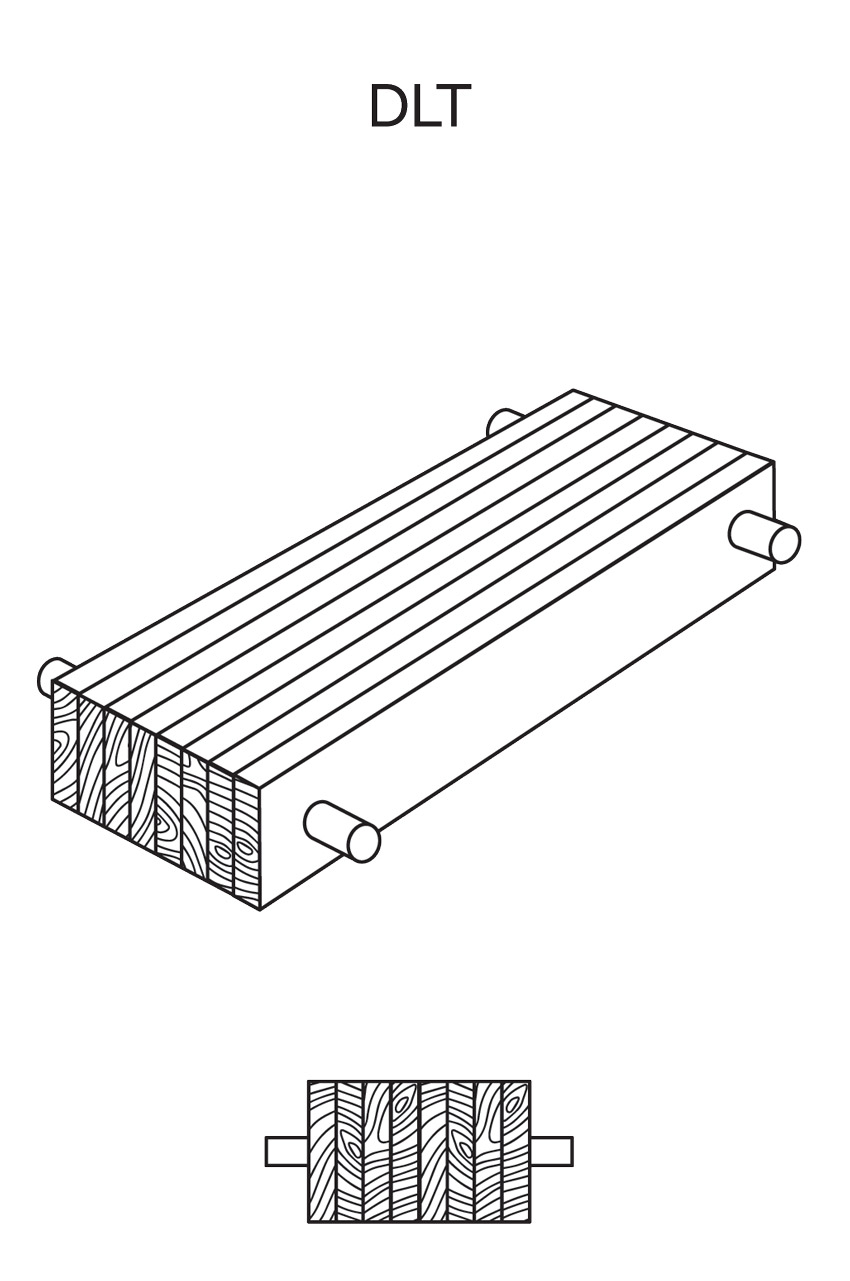
Dowel-laminated timber is a mass timber product that uses wood dowels as the connector and is ideal for floor, wall, and roof structures.
Benefits of Building with Prefabricated Wood Components
Speed and Installation Efficiency
Because wood panels are manufactured for specific applications, they’re well suited to a high degree of prefabrication at the plant, equating to speed and efficiency of installation. Panels are prefabricated, complete with pre-cut openings for doors, windows, stairs, service channels, and ducts, and shipped directly from manufacturer to job site so they can be quickly and efficiently lifted into place. This can shave months off the construction schedule. Many manufacturers ship panels with preinstalled lifting straps; contractors then use cranes to lift panels into place. In addition, prefabrication is safer because fewer crew members are needed to climb high on scaffolding. Because panels are designed for specific end-use applications, they are often delivered and erected using a “just-in-time” construction method, making wood products ideal for projects with limited on-site storage capacity. Prefabrication may also reduce the exposure of building components to wet weather. That being said, efficient construction can only be achieved when sequencing and project scheduling are determined up front and managed appropriately.