Designing Sustainable, Prefabricated Wood Buildings
Prefabricated Wood Construction
Prefabricated wood buildings are no longer limited to single-family housing and smaller temporary workspaces but are now being constructed for innovative buildings demanded by tenants and owners. Sectors with redundancies, such as multifamily housing (e.g., condos, student housing and senior housing), education buildings, commercial retail, health-care, and institutional buildings, are more likely to be built prefabricated.
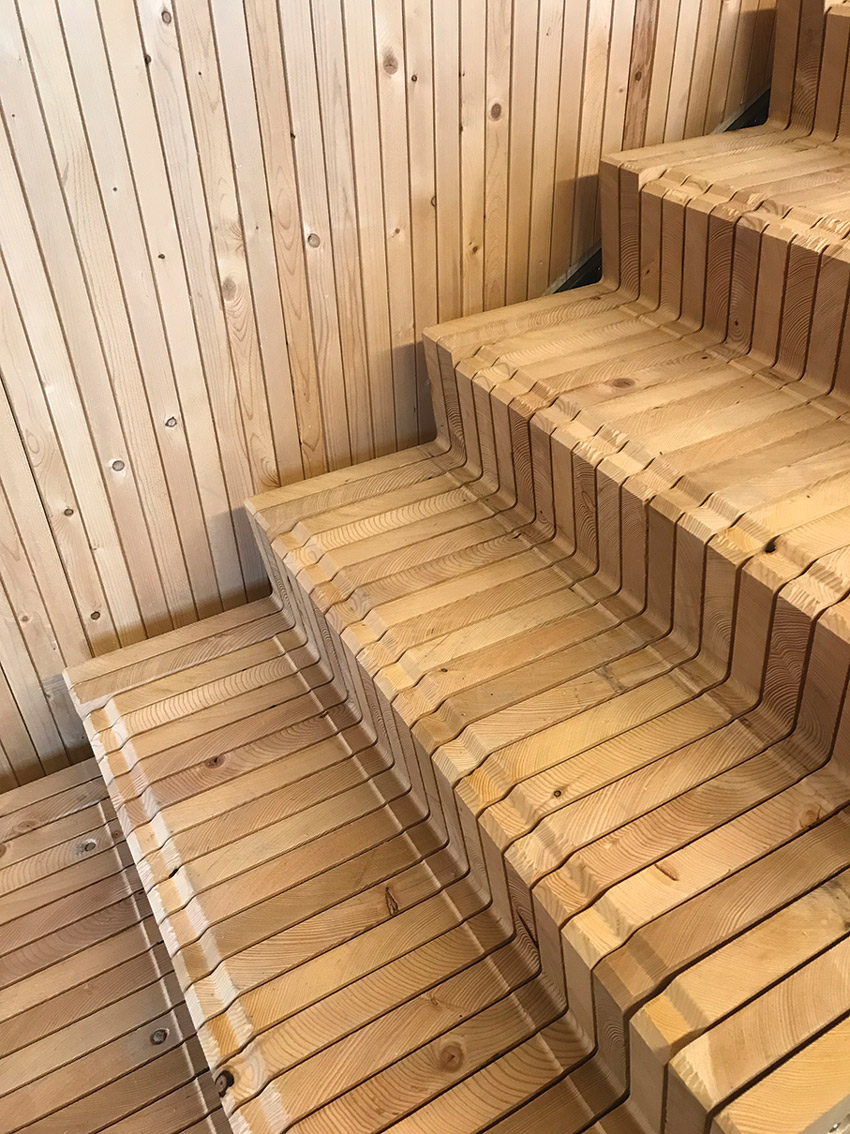
Image courtesy of StructureCraft
Computer numerical control machining technology is used at the plant to profile wood panels for installation, and sophisticated connection systems with a high degree of accuracy and efficiency are incorporated during prefabrication.
Wood has many benefits to the building industry, including aesthetics, environmental performance, strength and rigidity, lighter weight (compared to concrete), and energy efficiency. In prefabricated buildings, wood is particularly beneficial; it has the structural simplicity needed for cost-effective projects and design versatility, and it can be rapidly installed with reduced waste.
Prefabricated wood wall and floor panels offer easy handling during construction, and a high level of prefabrication facilitates rapid project completion. This is a key advantage, especially in midrise construction from five to 10 stories. Lighter wood panels mean that foundations do not need to be as large and smaller cranes can be used to lift panels higher. For example, at the four-story John W. Olver Design Building at the University of Massachusetts Amherst, four 60-foot-tall cross-laminated timber (CLT) panels comprising one of the building’s shear wall cores were lifted and dropped into place with a crane and anchored to the foundation, all in one weekend.
Panelization means framing of dimension lumber or mass timber walls produced with a high degree of accuracy in a factory. Computer numerical control (CNC) machining technology is used at the plant to profile wood panels for installation, and sophisticated connection systems with a high degree of accuracy and efficiency are incorporated during prefabrication. Panelizing lowers cost and speeds up the delivery of walls to a site where framing crews install quickly when compared with on-site framing. The faster and safer contractors and developers can finish a building, even if off-site construction methods are more expensive, the greater the return on investment. For light wood-frame construction, on-site framing is still the norm because it continues to make sense from a quality vs. cost perspective, but that is slowly changing. In the future, larger projects that demand panels be erected quickly and en masse are more likely to be prefabricated for light wood-frame construction.
Types of Wood Prefabrication
There are two types of industrialized approaches to prefabricated buildings: building kits (kit of parts) and finished modules. Building kits include prefabricated elements or sections that are then delivered and assembled on-site. These may include the roofing package (roof panels, fascia, gutter, etc.), roof structure (ceiling deck and beams), glazing package (windows and entrances), and building structure (wall panels, beam pockets, columns and shear paneling). The kit-of-parts approach, via panelization, is typical for midrise wood buildings.
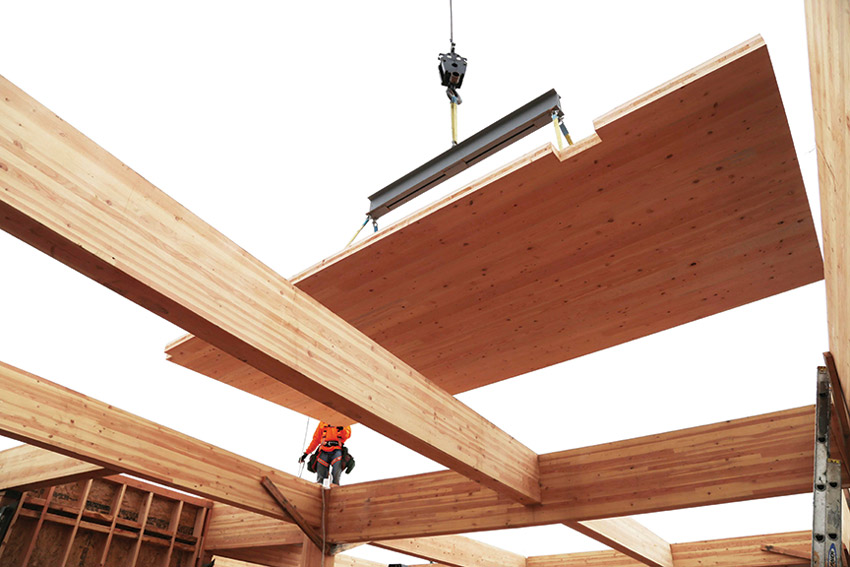
Image courtesy of LEVER Architecture
Building kits include prefabricated elements or sections that are then delivered and assembled on-site. The kit-of-parts approach, via panelization, is typical for midrise wood buildings.
Within panelization, it is helpful to understand the difference between open structural panels vs. closed structural panels. Open structural panels are a preassembled wall framework that is later fitted with other elements, such as insulation, exterior cladding, and weather barriers on-site. While this aids in time savings and flexibility, there is still a lot of site work involved. By contrast, closed structural panels are complete preassembled wall panels that may include windows, doors, plumbing, ducting, electrical, finishes, etc. Closed structural panels are larger and heavier so a crane is typically needed for on-site assembly.
Finished modules, on the other hand, are an entire building delivered and assembled on-site. Individual modules are joined together to make a single building. They are built in a factory, transported to the site, and when on-site, the modules can be placed side by side, end to end, or stacked, allowing a wide variety of configurations and styles in the building layout. Finish levels on modular units leaving the factory generally include plumbing, electrical, paint, flooring, fixtures, cabinets, and appliances. After the modules are craned into place, licensed sub-trades make electrical, plumbing, mechanical, and structural connections before finish work is completed and the building is prepped for occupancy.