Designing Sustainable, Prefabricated Wood Buildings
Learning Objectives:
- Demonstrate why prefabrication is an efficient and sustainable building practice.
- Evaluate the use of wood components in sustainable prefabricated buildings as well as design and engineering challenges that wood can solve.
- Discuss the advantages of building with prefabricated wood components in terms of speed and efficiency of construction, design flexibility, waste reduction, environmental performance, and improved life safety.
- Analyze, through case studies, the different stages of wood building prefabrication from design to installation.
Credits:
This course is approved as a Structured Course
This course can be self-reported to the AANB, as per their CE Guidelines
Approved for structured learning
Approved for Core Learning
This course can be self-reported to the NLAA
Course may qualify for Learning Hours with NWTAA
Course eligible for OAA Learning Hours
This course is approved as a core course
This course can be self-reported for Learning Units to the Architectural Institute of British Columbia
Prefabrication Then and Now
Prefabricated wood buildings should be considered when designing and building both multifamily and commercial buildings, such as multifamily housing, education, retail, health-care, and institutional buildings, as prefabrication is an efficient and sustainable building practice. Prefabricated wood components used in both light wood-frame and mass timber construction can help to solve many design and engineering challenges, such as material and process efficiency, environmental performance, and life safety.
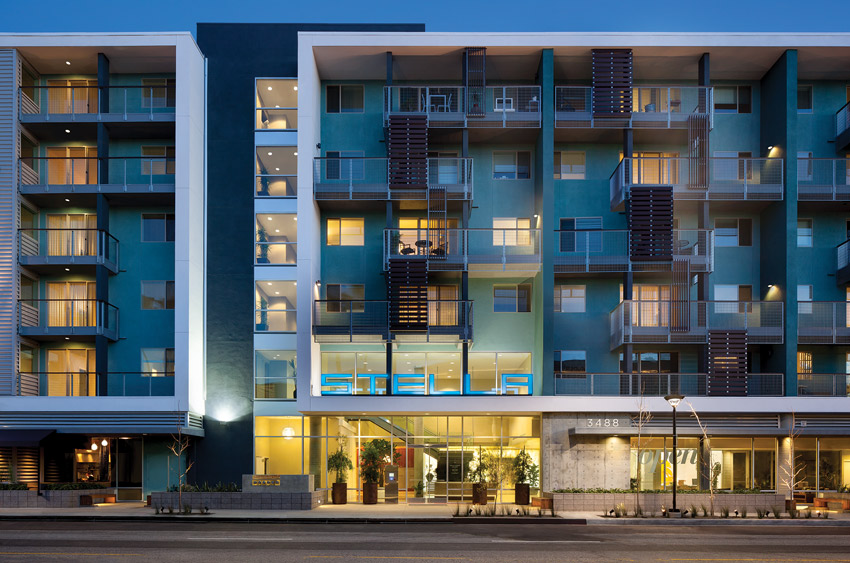
Image courtesy of Lawrence Anderson
The practice of prefabricating building elements in a factory was adopted in the United States only in the past century. Prior to that, most buildings were constructed on-site. There was a boom in kit-of-parts building post World War II. Consumers were enthralled with industrial production and replication, aka mass production, and prefabricated buildings helped fulfill the need for affordable, quality housing post war. Although mass production has remained vital to our economy and almost all industries, interest in prefabricated buildings fell off in the 1970s. The design and construction industry did not fully embrace the concept because it wasn’t well integrated into its traditional business model.
The building industry is now embracing digital tools such as 3D modeling, building information modeling (BIM), and computer numeric control (CNC) machines, making prefabrication and communication amongst building professionals easier. As James Timberlake, FAIA, says in the foreword of Ryan Smith’s book Prefab Architecture: A Guide to Modular Design and Construction, “We are now capable of sending a fully visualized and virtually formed model to a production line, bypassing the document interpretation phase, with all of its back-and-forth checking, redrawing, and margin for additional errors and omissions, ultimately improving the quality of the final product.” Also, improved safety measures and greater productivity are now high priorities, which prefabrication can help achieve. The off-site construction environment is a way to provide workers with safer working conditions to reduce the risks of accidents and related liabilities.
An increase in productivity is especially important because of the high demand for but short supply of skilled labor in the construction industry. Some believe that standardizing and automating construction in a factory setting deskills the traditional trades. In reality, it upskills the industry and prepares the trades to efficiently deliver buildings through technologically advanced design, fabrication, logistics, and assembly. “We think the recession actually benefited our industry,” says Thomas Hardiman, executive director of the Modular Building Institute. “During the last recession, many skilled laborers left the construction industry and did not return. That, coupled with developers needing to find greater efficiency, made prefabricated buildings more appealing. The construction industry is very reluctant to change. When things were going well, developers and general contractors may not have felt the pain or need to change. Now they do, and there’s no turning back.”
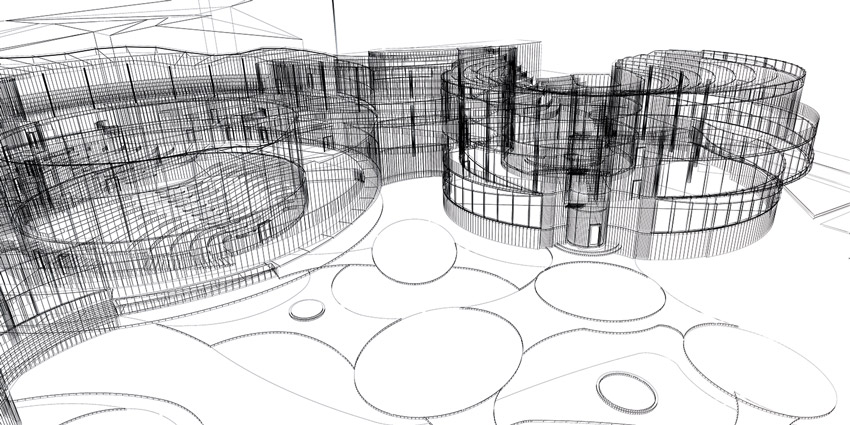
The building industry is now embracing digital tools such as 3D modeling, building information modeling, and computer numeric control machines, making prefabrication and communication amongst building professionals easier.
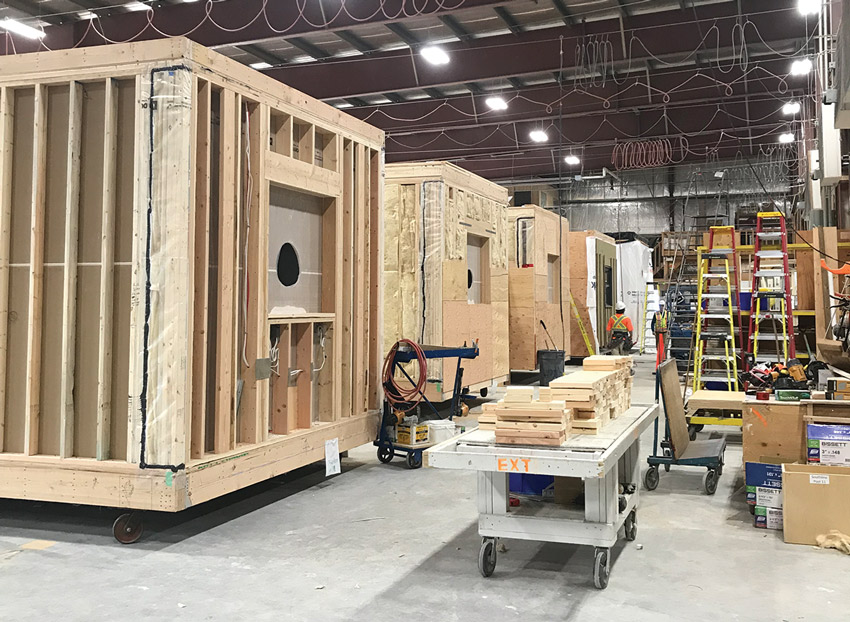
Wood prefabrication has a multitude of benefits, including process efficiency, a controlled environment, a greater return on investment, material efficiency, reduced waste both on- and off-site, and sustainability.
In addition, environmental views are changing regarding construction waste, the product supply chain, reuse of building materials, and carbon footprint. Wood buildings, particularly prefabricated components, can help designers balance cost objectives, function, and environmental impact. Timberlake says, “Integration modeling, the backbone of off-site fabrication and manufacturing, leans the product supply chain, helps architects and contractors manage the number of materials needed, and allows for a positive repurposing of the leftover materials. Further, off-site assembly offers the promise of disassembly and re-use.”
Benefits of Wood Prefabrication
Wood prefabrication has a multitude of benefits, including process efficiency, a controlled environment, a greater return on investment, material efficiency, reduced waste both on- and off-site, and sustainability. All of these benefits help to meet demands from owners, designers, and tenants for better buildings. Process efficiency is possible at every stage, from design to fabrication to construction. Detailed planning allows construction processes to be standardized and streamlined, including construction efficiency that meets aggressive schedules and decreases on-site assembly time. Sequencing is improved, as prefabricated components are sorted and loaded onto trucks, minimizing on-site handling. The process is also more integrated with better communication amongst parties, which reduces costly change orders.
Because prefabricated components are produced in a controlled environment, quality and precision of components improve, fabrication productivity increases, safety for tradespeople improves, and weather is not a factor in slowing down the construction process. Budgets should be easier to meet because redundancies and waste in both materials and time are streamlined. Although building components are often more expensive up front, the complete installed cost is usually less because on-site construction is minimized. Material efficiency results because prefabricated components are made off-site and typically via modeling technologies that provide extreme precision. Reduced waste both on- and off-site minimizes the environmental impact of a project, as specific sizes and dimensions of components are determined in advance and components are made or cut to tight specifications. This also relates to the sustainable nature of prefabrication.
According to Ryan Smith, author of Prefab Architecture: A Guide to Modular Design and Construction, “The environmental impact of building requires a quantifiable measurement of impact in total life cycle from design through facilities management. By controlling the means and methods by which buildings are produced through prefab, architects and construction professionals are able to ensure more sustainable materials and practices for construction as well as have a greater opportunity to predict future energy performance. Prefabrication may be used as a method to revamp the sustainability of construction from the perspective of the total life cycle of a facility, especially regarding demolition or reuse, as the case may be. The capacity of prefab to deliver buildings that respond to time, change, and reuse/recycle may be its greatest benefit toward total life-cycle sustainability in the future.”
We will review several case studies that demonstrate these benefits, including an extensive case study to conclude the course that details the process of erecting a prefabricated building from design to construction.