Multi-Story Wood Construction
Learning Objectives:
- Identify the sustainability and economic benefits of using wood construction for mid-rise buildings.
- Summarize building code requirements and provisions for mid-rise multi-family wood-frame structures.
- Discuss wood framing solutions that address issues such as shrinkage, fire protection, and seismic requirements while minimizing carbon footprint.
- Explore innovations in wood framing design techniques and wood product technologies that enhance energy efficiency.
Credits:
Cost-effective, code-compliant and sustainable, mid-rise wood construction is gaining the attention of design professionals nationwide, who see it as a way to achieve higher density housing at lower cost—while reducing the carbon footprint of their projects. Yet, many familiar with wood construction for two- to four-story residential structures are not aware that the International Building Code (IBC) allows wood-frame construction for five stories and more in building occupancies that range from business and mercantile to multi-family, military, senior, student and affordable housing.
“Once designers know that wood offers all the required safety and structural performance capabilities and meets code requirements for mid-rise, the most appealing feature of wood tends to be its price,” says Michelle Kam-Biron, P.E., S.E., director of education for the American Wood Council. “Multi-family housing was one of the first market segments to rebound from the recession—because it's more affordable than single-family housing while offering advantages such as less upkeep and, in most cases, closer proximity to amenities. Wood construction is attractive for multi-family projects because it offers a high percentage of rentable square footage at a relatively low cost, but its benefits are equally applicable to other occupancy types.”
Among their benefits, wood buildings typically offer faster construction and reduced installation costs. For example, after completing the first phase of a developer-funded five-story student housing project using steel construction, OKW Architects in Chicago switched to wood. “The 12-gauge steel panels were expensive, very heavy and difficult to install; and welding and screwing the shear strap bracing was very time consuming,” says project architect Eileen Schoeb. “Using wood was far more economical for the second phase.” Farooq Maniar, president of California-based Farooq Maniar, Inc. and structural engineer for a number of senior apartment projects also finds wood construction less costly. “The lead time and construction time are far less than they are for steel.”
Wood construction also offers advantages for project teams seeking green building certification or simply to reduce the environmental impact of their buildings. Wood grows naturally and is renewable, and life cycle assessment studies consistently show that wood offers environmental advantages in terms of embodied energy, air and water pollution, and other impact indicators.1
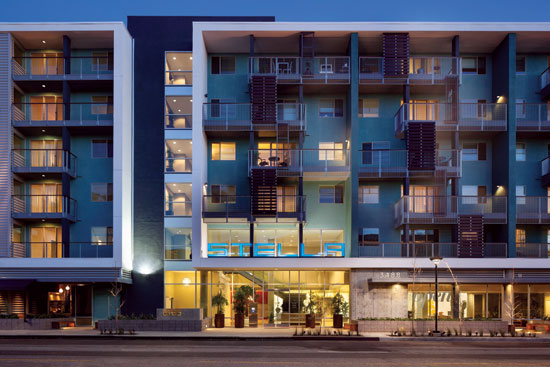
Photo: Lawrence Anderson, www.lawrenceanderson.net
Stella
Marina del Rey, California
Architect: DesignARC
From a carbon footprint perspective, wood continues to store carbon absorbed during the tree's growing cycle, keeping it out of the atmosphere for the lifetime of the building—or longer if the wood is reclaimed at the end of the building's service life and reused or manufactured into other products. The manufacturing of wood products also results in less greenhouse gas emissions than other materials.2 For example, according to one online carbon calculator,3 the new Stella apartment complex, which includes one four-story wood-frame building and one five-story wood-frame building on a shared concrete podium, has a carbon benefit equivalent to 14,049 metric tons of CO2. This includes 4,495 metric tons of CO2 stored in the wood products and 9,554 metric tons of avoided CO2 emissions. According to the U.S. Environmental Protection Agency's Greenhouse Gas Equivalencies Calculator, this equates to emissions from 2,683 cars for a year or from the energy required to operate an average home for 1,194 years.4
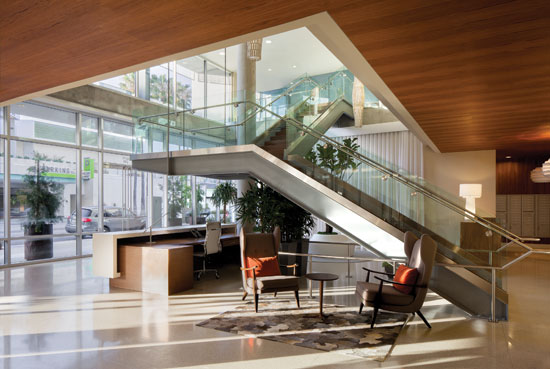
Photo: Lawrence Anderson, www.lawrenceanderson.net
Interior of Stella, a contemporary apartment building in Marina del Rey, California.
“Wood is also versatile and adaptable,” says Kam-Biron. “Modifications on the jobsite tend to be straightforward and are easily made.” A survey of 227 buildings demolished in Minneapolis/St. Paul found that buildings are often torn down within 50 years, regardless of material, because of changing needs and increasing land values as opposed to performance issues.5 Overall, wood buildings in the study had the longest life spans, showing that wood structural systems are fully capable of meeting a building's longevity expectations. However, when you consider the embodied energy in demolished buildings and the implications of material disposal, the fact that wood is adaptable—either through renovation or deconstruction and reuse (with minimal additional processing)—is a significant advantage.