The Sustainability of Automated Parking with EV Charging
When Can Users Charge EVs?
Increasingly in building codes, charging stations for EVs are mandatory, with minimum requirements for the number of EV charging spots that need to be provided, with California leading the way.
Therefore, questions arise concerning the process for charging EVs within an APS where the user does not drive the vehicle around looking for a charging port. How do EVs get charged in the modern scenario of an APS?
Each automated parking company has developed its own solution to the opportunity of charging EVs during a parking session. Here is how EV charging works in a leading APS manufacturer’s system:
Benefits of EV Charging in an APS:
- Less EV Charging infrastructure required
- With a fully automated charging system you can cycle a vehicle underneath the charging gantry at the appropriate time
- DC Fast charging
- Ability to charge an EV up to 80% within 30 minutes
- Entire system can be 100% EV charging accessible
- Can be used in any development application (Private & Public garages)
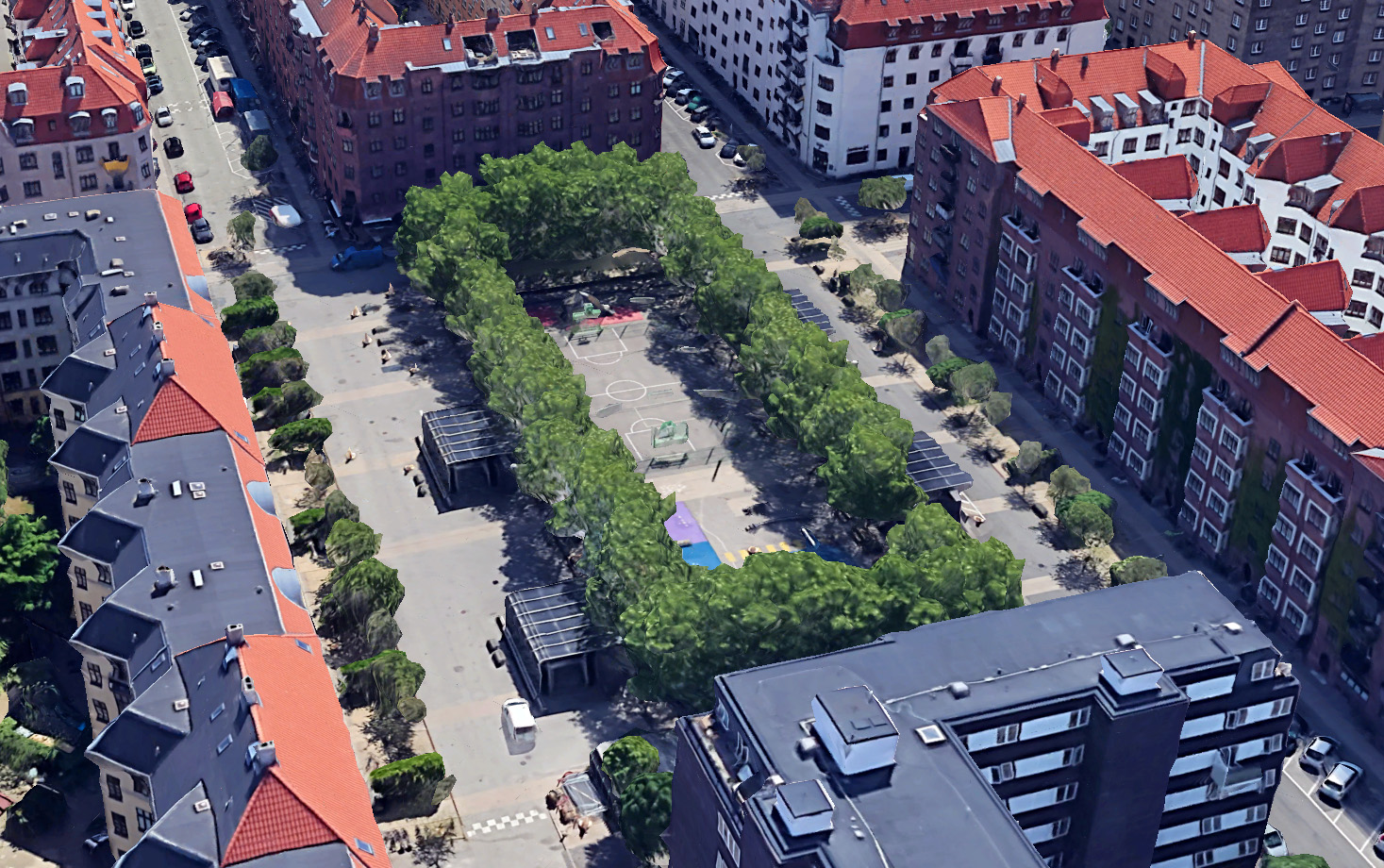
What Features are Built in For Reliability and Redundancy?
Some developers and designers considering an APS wonder: How reliable are these systems, and what happens when there is a power outage or other challenge?
A well-designed, properly installed, and correctly serviced APS should have a system availability of more than 99 percent, which is a function of both minimizing downtime and high reliability.
A system’s downtime can be minimized through:
- Automated fault recognition;
- Automated fault location identification;
- Simple fault diagnosis;
- Availability of spare parts; and
- Properly trained and qualified service personnel.
The first three points above can be achieved through a vendor’s high-quality operating and machine-control software that ideally would have been developed by experienced industrial automation programmers who understand the extra steps necessary to write the code that makes the recovery from faults as quick as possible. The latter two points can be achieved 1) by the vendor utilizing commercially available off-the-shelf parts that are readily available in most locations (rather than specialty items that are difficult to find or items that can only be purchased from the vendor), and 2) by the vendor having its own spare parts and service organization that is properly staffed and trained, and can develop critical and recommended spare-parts lists.
High system reliability can be achieved through:
- Use of high-quality materials;
- Proven designs;
- High-quality manufacturing and installation;
- Properly trained operators; and
- Correct implementation of a preventive maintenance plan.
The use of high-quality materials is obviously going to provide higher reliability than low-quality materials, but these inevitably come at a higher cost. It is simply not possible to provide a highly reliable system at a low cost. Vendors can reduce the capital cost of their systems by choosing to use low-quality materials or components, but this will likely lead to much higher lifetime costs for the customer due to replacing these low-quality components more frequently or an unreliable system. There are several examples of lower-cost APSs being replaced or overhauled a few years after installation due to the unreliability of the “low-cost” system. As the adage goes: buy cheap, buy twice.
Using proven designs increases reliability simply because the system design is based on tried and tested technology that has worked reliably before. Utilizing groundbreaking, state-of-the-art technology can seem appealing, exciting, or cutting edge to some. However, implementing too many unproven designs within an APS can have catastrophic implications on the system itself and the success of the whole development.
The most well-designed, highest-quality APSs still require properly trained and qualified operators to improve reliability and minimize downtime. This is one element where a building operator can make a huge difference in the reliable operation of an APS. Even though an APS typically requires no human intervention to operate, no automated system or machine is completely fault free. Having properly trained operators on-site to quickly deal with issues that arise and liaise with service personnel if required is essential to a system’s reliable operation. In most instances, the smooth operation of a high-quality APS is interrupted by user faults rather than system faults. Typical user faults may be forgetting to complete the parking process and walking away, losing a key fob or ticket, or simply not following instructions. All of these can easily be resolved by professionally trained, courteous operators or building concierges.
According to Tom Scannapieco, president of Scannapieco Development Corporation, which targets the ultra-high-end residential market, redundancy built into the system at 500 Walnut Street project in Philadelphia was extremely important.
“The advantage with the system is that I have two independent shuttles (t-cars)—one on each level,” Scannapieco says. “So if one becomes inoperative, the one from the other level can be transferred and run in place of the inoperative one. This level of redundancy we found very attractive.”
The most well-designed, highest-quality APSs also require the correct implementation of a preventive maintenance plan to function reliably. If a vendor has its own design engineers and service personnel, these teams can work together to develop a preventive maintenance plan that will maximize reliability based upon intimate knowledge of the system designs and previous projects’ fault logs and service histories.
System Longevity and Maintenance
If properly maintained, an APS can have a lifespan from 20 to even more than 30 years. The lifespan for automated parking technology is greatly increased by quarterly maintenance checks on the system. For instance, APSs in Copenhagen, which house more than 800 vehicles, are still running smoothly after 14 years, allowing the people of Copenhagen to park worry free and enjoy more leisure space in their capital city.
Typical recommendations are for preventative maintenance to be performed two to four times per year. This should include:
- General inspection of the APS;
- Review of all safety and operational features;
- Examination of major components;
- Replacement of damaged or worn parts; and
- Lubrication of system components.
Depending on the company, several maintenance packages may be available:
- In the most comprehensive and worry-free package, the APS vendor maintains the system, including corrective and preventative maintenance as well as software support, upgrades, and spare-parts replacement.
- At the next level, preventative maintenance may be arranged by an annual agreement for planned preventative maintenance, labor, and travel cost. This package is customized to a user’s needs.
- The final level may be thought of as “pay as you go.” In this case, the client pays only for the maintenance that is needed, when it is needed.