Multi-Family, Mid-Rise Wood Buildings A Code-Compliant, Cost-Effective and Sustainable Choice
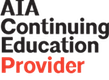
Learning Objectives:
- Identify the sustainability and economic benefits of using wood construction for mid-rise multi-family or mixed-use buildings.
- Summarize building code requirements and provisions for mid-rise multi-family wood-frame structures.
- Discuss wood framing solutions that address issues such as shrinkage, fire protection and seismic requirements while minimizing the carbon footprint of the building.
- Explore innovations in wood framing design techniques and wood product technologies that enhance energy efficiency.
This course is part of the Mass Timber Academy
Initial MC, or MC at the time of manufacture, is typically specified on a project’s structural drawings. In many parts of the country, the specification would read “a maximum MC of 19 percent.” To achieve this, lumber is generally kiln dried. Although there are regional variations, less commonly used green lumber (which typically hasn’t been kiln dried and has a MC above 19 percent), surface dried lumber, or KD-15 (i.e., kiln dried lumber with a maximum MC of 15 percent at time of manufacture) may also be specified. The American Softwood Lumber Standard, PS 20, a voluntary product standard under the rules of the U.S. Dept. of Commerce, defines dry lumber as “lumber of less than nominal 5-inch thickness which has been seasoned or dried to a maximum moisture content of 19 percent.”
Ways to minimize shrinkage include (among others) specifying kiln dried lumber, letting the wood dry during construction before closing in the walls, and using products and systems such as pre-engineered metal-plate-connected wood trusses for floor and/or roof framing, and engineered wood products (laminated veneer lumber, I-joists, cross-laminated timber, etc.). I-joist floor systems are dimensionally stable and offer minimal inter-floor shrinkage.
Additionally, some overall settlement of the building may occur due to gaps in the building construction that can contribute to the overall vertical movement. Some designs will address this by distributing the dead load throughout the height of the building and allow time for the building to acclimate to the environment and/or air dry prior to installation of the drywall, thus allowing the building to naturally settle.
Fire Safety During Construction
Although less than 2 percent of building fires occur during construction, this phase presents unique risk scenarios that make any building more vulnerable, regardless of material used.
IBC Chapter 33 provides minimum safety precautions for fire during construction, and guidelines for the protection of adjacent public and private properties. The section also includes provisions for fire extinguishers, standpipes, means of egress, and sprinkler system commissioning. The International Fire Code also contains detailed requirements. Fire safety measures such as extended fire watches, site security, safety inspections, and record keeping are now incumbent on owners and contractors during construction.
The most common causes of fire in wood-framed buildings under construction are arson and hot work, making site security, rigorous procedures for workers, and access to fire hydrants critically important. Education is also important, since fires that occur during this phase can spread more quickly when required elements such as gypsum wall coverings, fire doors, smoke alarms, and sprinklers have not been put in place. The Construction Fire Safety Coalition is a resource for codes, standards, and best practices in fire prevention.12
Differential Movement
Allowing for differential movement between wood and non-wood structural elements and building finishes is critical. Steel, concrete, and brick continue to expand and contract over time due to temperature changes, while wood generally maintains its dimensions after having reached its EMC.
Differential movement occurs when, for example, floor joists are supported by a wood-framed wall at one end and by the masonry block of an elevator shaft at the other end. Areas such as stairwells, shafts, and vaulted ceilings require attention for differential movements as do plumbing, electrical, and mechanical systems. Using flexible joints such as flexible pipe, conduit, couplings, and elbows and tees for electrical, mechanical, and plumbing between floors can prevent potential mechanical problems. Design of joints between building envelope components, such as windows and doors, must also allow for differential shrinkage.
Seismic Requirements
While earthquake and seismic requirements are a well-known aspect of building design on the west coast, other parts of the country are not immune to earthquake activity and must also comply with seismic codes. Wood construction provides high strength with relatively low weight, and the high strength-to-weight ratio makes wood a good choice for earthquake-resistant construction.13,14 In wood-framed buildings, walls and floors are often used to transfer lateral loads from winds and seismic forces.
Wood-frame construction also provides numerous load paths through shear walls and diaphragms, which typically have hundreds of structural elements and thousands of nail connections, adding ductility and redundancy to the system. Redundant load paths give additional assurance that loads will be transferred if one connection fails. In contrast, structures supported by heavy non-wood frames have relatively few structural members and connections, resulting in fewer load paths. Moreover, the large number of walls in a typical multifamily project reduces the loads shared by each individual wall. Tests and observations from past earthquakes show that wood buildings have performed well. For example, a six-story light-frame wood building tested on the world’s largest shake table in Japan resisted a major earthquake (projected to occur, on average, approximately every 2,500 years) with minimal damage.15
Building code requirements for wood diaphragms, shear walls, and hold-down devices work effectively in creating earthquake-resistive structures. Horizontal diaphragms in roofs and floors transfer the horizontal forces to the shear walls. Shear walls with hold-downs, such as a continuous tie-down rod system, resist tension forces in an overturning scenario, while wood studs or columns absorb the compression forces. Wood structural panel shear walls are typically used throughout the building to provide vertical lateral resistance.