A Number and a Story
In contrast, “concrete clearly produces a lot of CO2,” Paull says, analyzing the component processes: “You have the CO2 in mining the limestone; you have to heat the limestone and the clay and the sand to 2,700°F, which not only releases carbon dioxide from the limestone but requires a lot of energy from hydrocarbon fuels such as natural gas. And then you grind up the resultant product called clinker, which requires more energy, and mix it as a binder in concrete. Cement by itself can only produce around 6,000 psi concrete. So about the early part of this century, the buildings got bigger, the demand on the concrete got higher, and we needed to get the strengths 8, 10, 12, 14,000 psi, and there’s no way to do that with Portland cement, so we started replacing Portland cement with slag and fly ash, slag being the byproduct of the steelmaking industry, and fly ash being the byproduct of coal-burning power plants. In simple terms, what those two products do is use the byproducts that aren’t gluing the concrete together and make more cement, and that allows us to get to a higher strength; it also reduces the temperature gain, which limits thermal cracking issues, which can weaken concrete. But no one really was concerned about CO2; we were concerned about the performance of the concrete. But inadvertently, we reduced the CO2 content of Portland cement. My opinion is, we’ve probably gone as far as we can with Portland cement” in improving its carbon footprint.
However, Paull mentions some companies experimenting with low-EC alternatives to Portland cement, using electrolysis processes or chemical admixtures (including captured CO2) rather than high heat, that may eventually revolutionize the concrete industry as EAFs have revolutionized steel. As with many novel products, challenges include availability of both the materials and the expertise in using them, Hendel notes. “Contractors, when faced with it at the start of construction, are understandably going to say, ‘Well, if it limits the people who can bid on this project to one, we’re not going to do it.’” If a contractor is on board with using new materials, he recommends, “ask them who their subs are going to be, who their likely bidders are going to be, and if there are producers locally who have this technology.”
Driscoll notes that AECOM, as “the first construction management firm to have SBTi [Science Based Targets Initiative]-approved targets... the most aggressive carbon targets of any large contractor in the U.S.,” is in a position to pull the market to some degree. But not all firms can persuade clients to expand their comfort zone with new materials. “You’ve seen it a million times: great sustainability strategies in design come down to value engineering, and then half of them don’t make it to the finish line. And so we’re trying to de-risk that by understanding where the premium is. And we do it at a point where we have leverage, because those ready-mix suppliers have not yet won the job.”
“We really need the concrete industry to mimic what the steel industry is doing,” Meola summarizes. She estimates that with substitution of low-EC concrete and related processes, “hopefully in the next ten years we’ll see improvement.” At present, the experimental or niche status of advanced concrete stands in contrast to the EC-reduction gains already established by steel.
THE MATERIAL COSTS OF SIGHTLINES AND ATRIA
Clients present a range of levels of receptivity to the information-intensive activity of EC reporting, balancing it with other imperatives. Paull points out that business metrics, material metrics, and other aims can diverge. “We like to optimize weight, but our main goal is to optimize cost,” he says. “And optimizing cost doesn’t necessarily mean we’re optimizing weight. So there are strategies to take more steel out of a building, but it would add a lot of cost.” Designs intended to increase rentability or “to build a statement building” are also frequently profligate with materials and thus inefficient from the EC perspective, he adds: “We want to minimize material. But having column transfers, over-height floors, massive lobbies, that all takes a lot of material to do that. [At] the top of buildings, once upon a time, the building would go up, and we’d just square off the top, and that’s it. You don’t see that anymore; you see massive concrete or steel structures sitting at the top of the building that aesthetically are very pleasing but really don’t do anything.... If you’re putting a big hat on top of a building, that’s going to increase your carbon footprint.”
Structural design choices, Cropper points out, are powerful determinants of material volume and thus of EC—for better or worse, pitting tenants’ desire for column-free space (and thus a building’s leasability in a difficult commercial market) against EC metrics. “The further we space columns apart, the harder our structure is going to work,” he says, and “the more material we’re going to need. And what we tend to see is that the floor slabs and floor framing are big drivers of the embodied carbon in our structures. Vertical elements are less so, typically, especially if you’re talking about concrete buildings. Steel is the same way: a driver of tonnage is the column-grid spacing.”
On one project, Cropper recalls studying EC savings comparing a 30-by-45-foot office grid against a 30-by-30’-grid, “and it was [roughly] 30 percent right off the bat. I tell architects, ‘I’m not here to tell you that we need to go to 30-by-30 grids everywhere,’ but at the same time, maybe we need to think about that.... Every pound per square foot we can take off our building, we can reduce the material that we’re using in the building structure, and that reduces the embodied carbon. Going above and beyond code limits, there’s a balance between providing future flexibility and providing material in the building that we don’t need.”
HOK’s Hendel points out that “it’s not just about finding the lowest weight for your structure” in every situation. Early in his career, after assuming that the most lightweight structures would also be environmentally optimal, he discovered that “weight may be in direct conflict with another consideration.” Curtain wall, with its multiple elements, is often high in EC; “if you’re able to go with a lighter-weight structure, but it results in a really deep floor... you can add a little bit of weight but cut your floor depth down by a foot and take out a foot of curtain wall for every floor of a building. That’s a tremendous amount of material.”
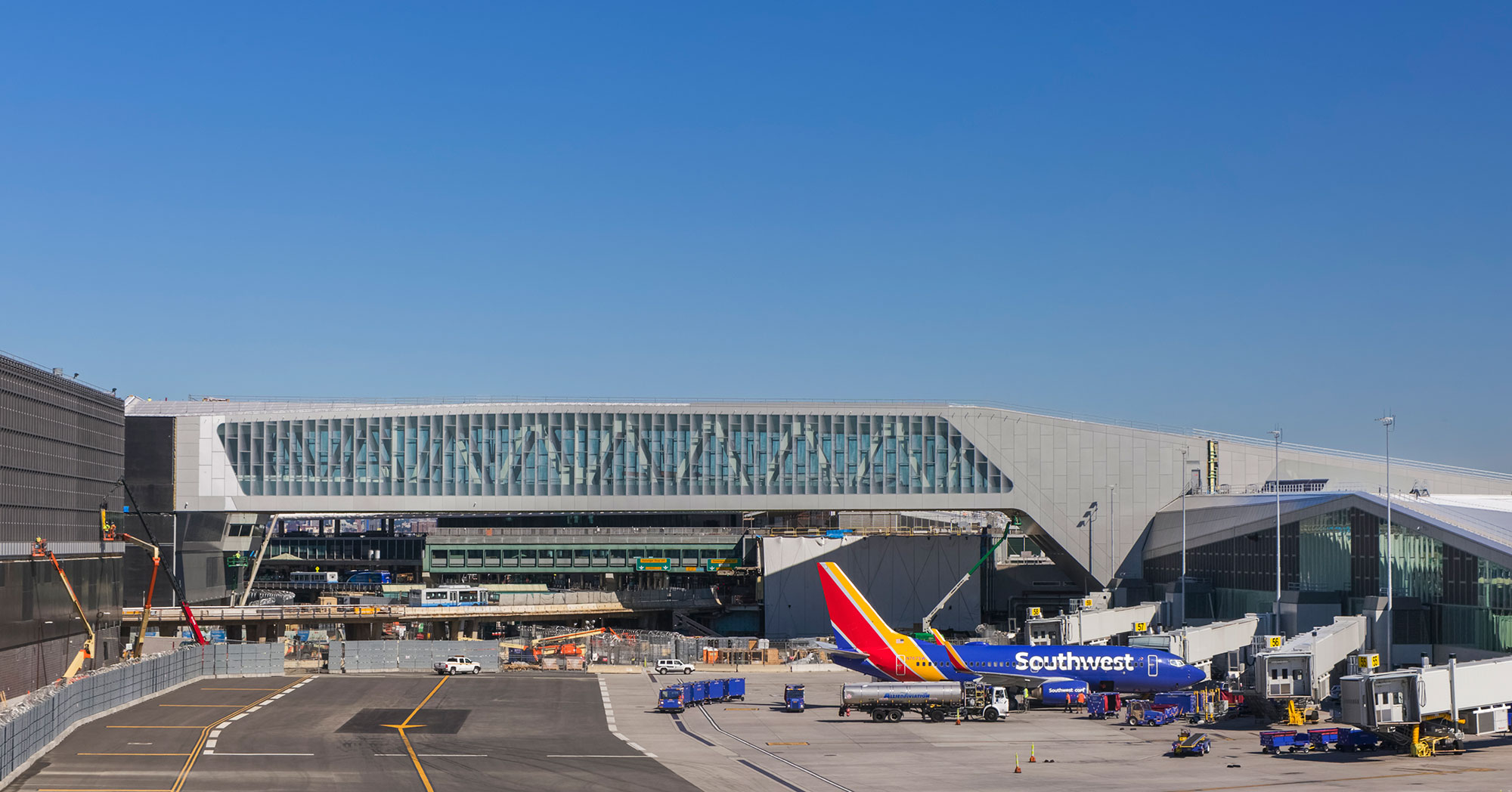
Photo courtesy of LaGuardia Gateway Partners/Jeff Goldberg
Figure 2. Pedestrian bridge connecting headhouse to island at LaGuardia Terminal B.
New York’s LaGuardia Airport Terminal B, transformed in 2022 from an outdated, congested facility to a spacious multiple-award winner, offers a salient example of precise attention to embodied carbon, note Hendel and Meola of HOK (part of a design-build team also including WSP, Thornton Tomasetti, Skanska Walsh, Meridiam, and JLC Infrastructure). The poor flood-plain soil beneath the airport required a bed of long piles extending some 180 feet into the ground, even taller than the building itself, reports Meola. Designing the foundations of the structure (a concourse headhouse linked to islands by 450-foot pedestrian bridges above active taxiways; see Fig. 2) and determining the appropriate amount of material, in the midst of a complex construction process that could not interrupt airline operations, called for precise optimization studies.
“A pile is essentially a step function,” Hendel says; “if a pile has a 300-kip capacity and you have 350 kips on that capacity, you need two piles, but those two piles are really underutilized, and that’s a waste of material and money. We did all these studies where we looked at the bay spacing, the thickness of the slab on the first floor—which was going to need to be a structured slab spanning between foundations, not resting on grade—and did an optimization to reduce, significantly, the number of foundations required.” Skanska’s fact sheet notes that design optimization, including the pile design, reduced the project’s overall EC by 10 percent. “The design of the pedestrian bridge,” Hendel continues, “was driven by reducing the overturning moment at the concourse end, and there were some gymnastics that we did there in order to get the number of piles down.... It’s all underground; you don’t see it; but after we started on our design, we cut the number of piles by 40 percent.”
This optimization process was one aspect of an all-hands-on-deck sustainability effort by the firms working with the LaGuardia Gateway Partners consortium, addressing both embodied and operational carbon. Terminal B is the world’s first air terminal to receive a LEED Gold rating under version 4 (which recognizes EC reduction and material selection based on EPDs), and its accolades to date include the first-ever Envision Platinum award from the Institute for Sustainable Infrastructure.
Another recent project where structural engineering optimized material efficiency is the expansion of an eight-story 1975 concrete-frame office building in the Penn Quarter section of downtown Washington, D.C., 600 Fifth Street NW (Figures 3-4). The goal was to give the Rockefeller Group/Stonebridge partnership a trophy-class commercial building that makes the most of the site’s location between Capital One Arena and the National Building Museum, with superb public transportation options as well as views and amenities. Adding four new steel-framed floors (three office floors and an occupied penthouse) and a new lateral system, reports Cropper, Thornton Tomasetti (working with New Haven-based design architects Pickard Chilton and Houston’s Kendall/Heaton as executive architects) moved the building’s side core to a more central position and recreated its parking ramp, all without requiring any new foundations or below-grade construction–a particular challenge, since the building sits atop the Red Line tunnels of the Washington Metro system (in its previous incarnation, it served as Metro’s headquarters for nearly 50 years). “A tear-down scenario was studied,” Cropper says, “but ultimately the project schedule, budget, and sustainability goals drove a transformation approach–in essence, a conversion from office to ‘better office.’”