Roof Hatches Simplified
A building's type and size generally will determine the method of egress, which, in turn, determines roof hatch size. For example, a large building, such as a manufacturing facility with high ceilings, may require the use of a fixed ladder to gain access to a roof area, but an office building or school could incorporate a staircase into a structure's upper level.
Frequency and reason: The frequency and reason individuals need to access a roof area can also affect hatch size. If maintenance personnel will be required to carry large tools or parts onto a roof for service, a larger hatch with stair access should be considered.
In addition to personnel access, larger roof hatch sizes are available for installing or removing equipment from a building. Whether a building is an office building, hospital, or manufacturing facility, equipment type, and dimensions will determine its roof hatch size.
Roof hatches designed for equipment access are generally two-cover models custom-manufactured to specific size requirements. When determining the size of a hatch for a particular piece of equipment, it is essential to contact the roof hatch manufacturer to verify the hardware locations on the hatch and the clear opening of a specific size.
Material Choice and Corrosion Resistance
Another important consideration when selecting a roof hatch is its material. Typically, this decision depends on cost, aesthetics, maintenance considerations, and a hatch's geographic location. Hatches are manufactured in galvanized steel, aluminum, and stainless steel.
Galvanized steel is the most common material choice. It provides basic corrosion resistance and is typically supplied with a primer paint finish. Aluminum hatches have a mill finish and are slightly more expensive than galvanized steel. However, they offer a higher level of corrosion resistance, particularly in coastal areas, and require little or no finish maintenance.
Stainless steel roof hatches are also available, but there is a significant premium for these products. Stainless steel hatches offer the highest corrosion resistance and are installed in environments such as chemical plants or coastal areas with extreme weather conditions.
Energy Efficiency
Energy efficiency is essential for all buildings, and a properly constructed roof hatch will help maintain the energy performance levels of an efficiently constructed building. To help maximize energy efficiency, selecting hatches that feature fully welded corners and insulation in the cover and curb is crucial. Many hatch manufacturers also offer insulation options for enhanced thermal performance. Roof hatches should also feature an overlapping cover design and a full perimeter gasket to ensure complete weatherproofing.
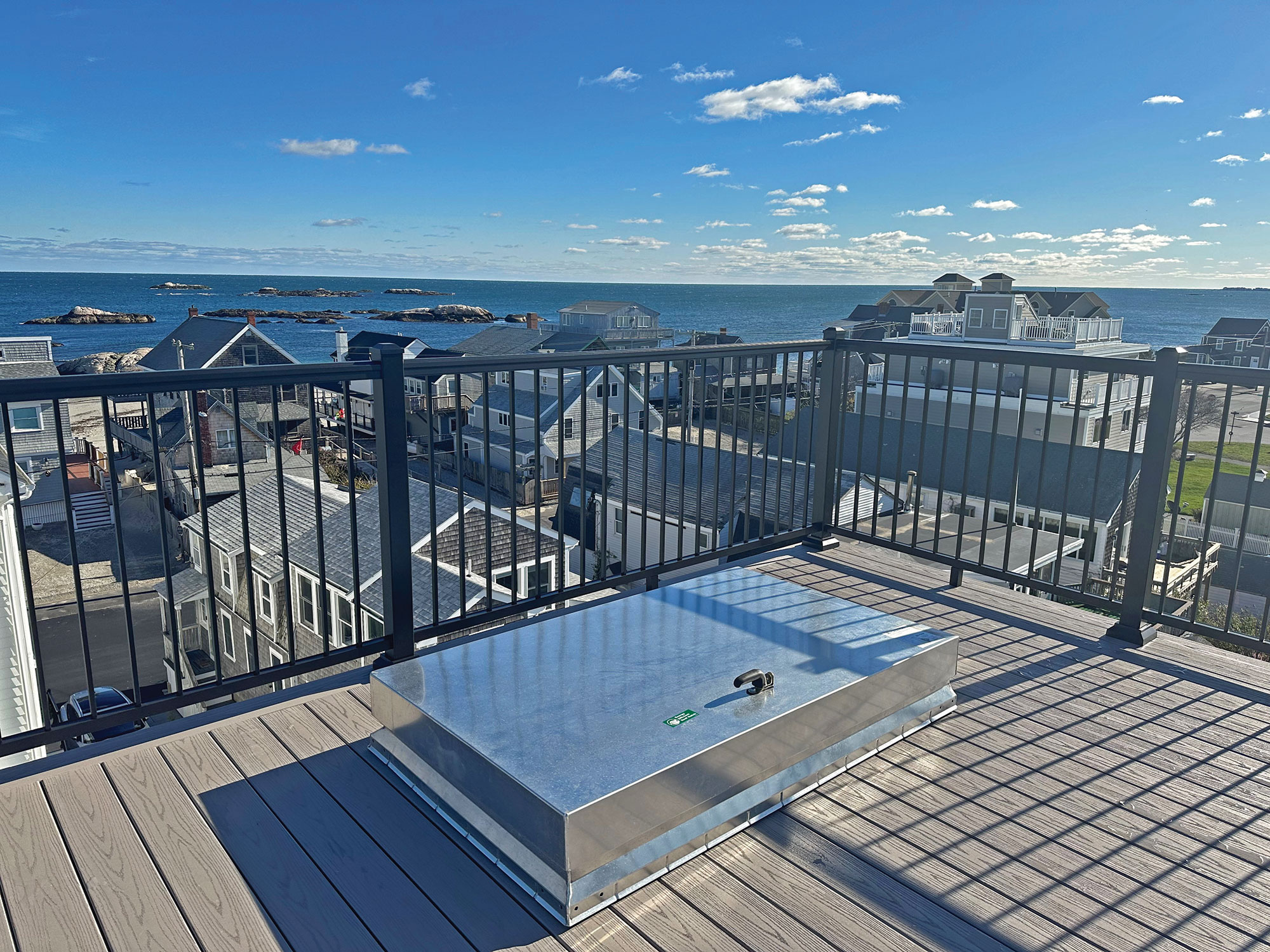
Photo courtesy of Lee Cormier and The BILCO Company
Energy efficiency is essential for all buildings, and a properly constructed roof hatch will help maintain the energy performance levels of an efficiently constructed building.
Lifting Mechanism
Operation is one of the critical factors to consider when specifying a roof hatch. Workers usually need to raise a hatch upward from inside while standing on a ladder or stairs, often carrying tools, so every hatch should be equipped with properly designed lift assistance. These devices should provide uniform lift assistance to ensure smooth, easy operation and minimize the effort required to open and close the hatch.
In addition, proper lift assistance and an automatic hold-open arm ensure the cover will not slam shut on users while entering or exiting a hatch.
Another option is an electric motor operation to open and close covers with the push of a button. The motor operation provides a convenient means of ventilating work areas in manufacturing facilities. The product typically includes a built-in motor operator, a push button control station, and a wiring diagram.
Roof hatches can also be supplied with manual winch operation to open and close covers remotely. Winch operation provides a convenient means of ventilating work areas in manufacturing facilities and is a less expensive alternative to electric motor operation. The product usually includes a manual winch and wall mounting bracket. Cable and additional pulleys can generally be supplied at additional cost.
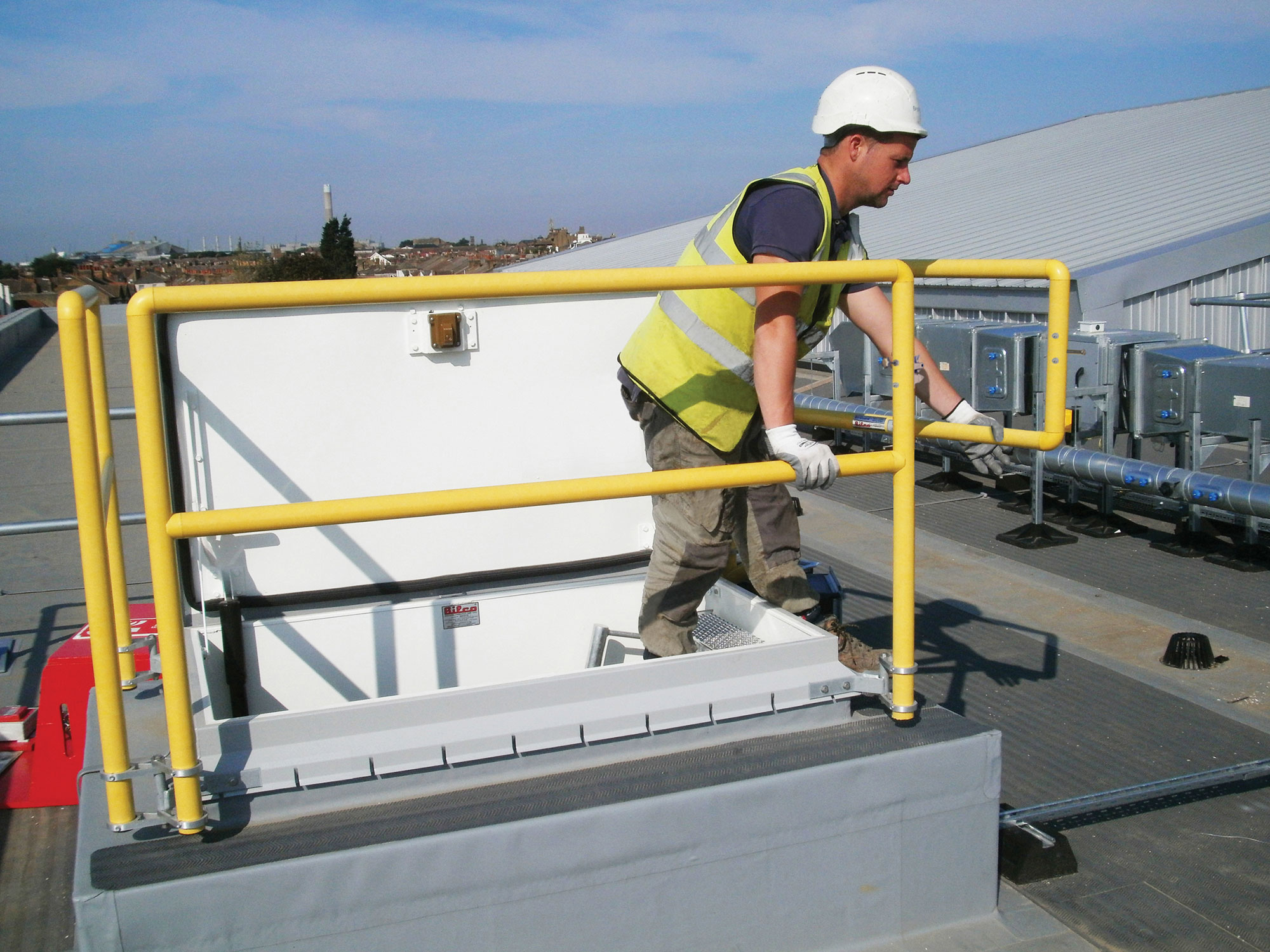
Photo courtesy of Lee Cormier and The BILCO Company
Fall protection is the main function of a roof hatch safety railing system.
Locking Options
Most roof hatches are supplied with interior and exterior padlock hasps as a standard feature to prevent unauthorized access. Custom security options can include keyed cylinder locks and contact switches for alarm systems. For high-security buildings such as prisons, banks, or pharmacies, hatches can be fabricated from heavier gauge materials and modified with numerous options to enhance security.
Meeting OSHA Safety Requirements
A safety railing system on a fixed roof hatch provides a permanent means of fall protection for roof hatch openings. In addition to OSHA fall protection regulations (29 CFR 1910.29), it is important to consider the features and benefits developed by manufacturers for hatch railing systems.
Some common factors to consider when choosing a railing system are:
- The design should allow the railing system to be installed on the roof hatch without penetrating the roofing material. If designed otherwise, the installation of a railing might result in a potential leak path.
- Installation should be simple and require only basic hand tools with no installation training or certification necessary.
- The railing system should be constructed of corrosion-resistant materials such as stainless steel, or aluminum.
- The railing system manufacturer should provide a warranty to ensure product quality.
The roof hatch industry also has made products available to complement railing systems for additional worker safety. One such product is a ladder safety post, an extension device that permanently mounts to the top two rungs of a fixed ladder. It provides a steady handhold that enables workers to enter or exit an opening in an upright, balanced position. This product type should feature adjustable mounting hardware to accommodate any ladder rung size or spacing.
In addition to safety options for roof hatches, the OSHA minimum required size for ladder access roof hatches often comes into question. For many decades, the industry standard for ladder access has been 36 inches (width) by 30 inches (length) hinged on the short side. OSHA 29 CFR 1910.27 fixed ladders standard defines the requirements for design and installation of fixed ladders and associated components, such as roof hatches and cages.
This standard states that ladder rungs are required to be at least 7 inches from the ladder mounting surface as measured to the centerline of the rungs. If a ladder is installed so that the climber’s back faces a smooth wall, the minimum distance from the centerline of the rung to the wall is 27 inches. In this case, the required minimum hatch width would be 34 inches, and the industry standard size would be compliant. When a smooth wall is not present, the minimum distance to any obstruction behind the climber as measured from the centerline of the rungs is 30 inches. This dimension, coupled with the 7-inch rung clearance, equals 37 inches, which causes some confusion in the market regarding the use of the industry standard 36-inch-wide ladder access roof hatch.