Test Webinar Course 1
Case in Point
A recent example of where the building team successfully optimized the use of steel is the Seattle Central Library, which features a steel diagrid facade. In addition to presenting a unique, eye-catching exterior, the structural steel also serves as the facade support and the exposed lateral load resisting system, resisting wind and earthquake forces. In addition, it is part of the building’s shading strategy.
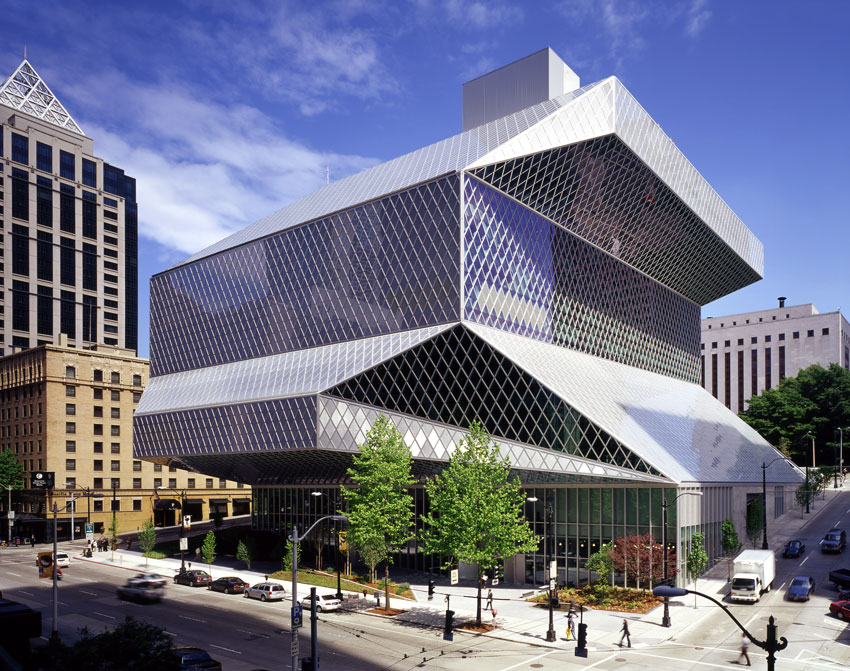
Photo courtesy of Pragnesh Parikh/MKA
For the Seattle Central Library, Magnusson Klemencic Associates designed the structural steel system to serve four purposes: the facade support, shading strategy, exposed lateral load resisting system, and an attractive aesthetic.
According to Davis, 90 percent of the aluminum that would typically go into a facade mullion system was eliminated because the steel diagrid is doing that work directly.
“It takes thoughtful efforts to achieve multifunctional goals like this, but that is where true sustainability comes into a design,” he says. “Finding the optimized multiuses of a single material and expressing it with minimal further adornment is key.”
MKA was also involved with Chicago’s Blue Cross Blue Shield tower expansion. The original design of the building anticipated a future vertical expansion, but when the decision was made to proceed with the expansion, it was discovered that the concrete core was significantly off plumb and the original planned expansion was not possible.
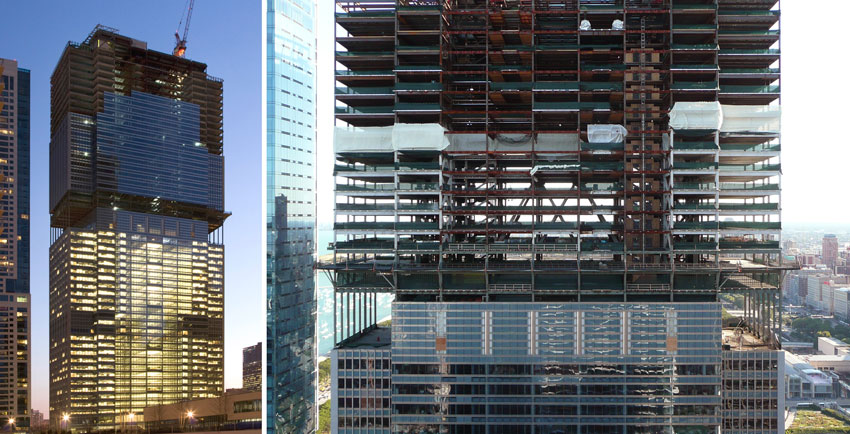
Photos courtesy of MKA
For Chicago’s Blue Cross Blue Shield’s vertical expansion, Magnusson Klemencic Associates designed new steel transfer trusses on the original roof, which was originally designed to support reserve vertical load capacity. In these construction photos, it’s possible to see the transfer trusses between the original structure and the new expansion.
Fortunately, the original design incorporated a steel frame with reserve vertical load capacity and accessible steel column connection points that allowed the use of a structural steel braced frame system for the vertical expansion that minimized loads. In designing new steel transfer trusses on the original roof, this created both an efficient transition to the tower above and an integrated MEP floor with open program spaces between the trusses, explains Davies.
Similarly, a central atrium in the original tower was thoughtfully designed for future elevators and accessible steel framing for attaching new guide rails. This essentially enabled the original building to be occupied outside the atrium during the new construction.
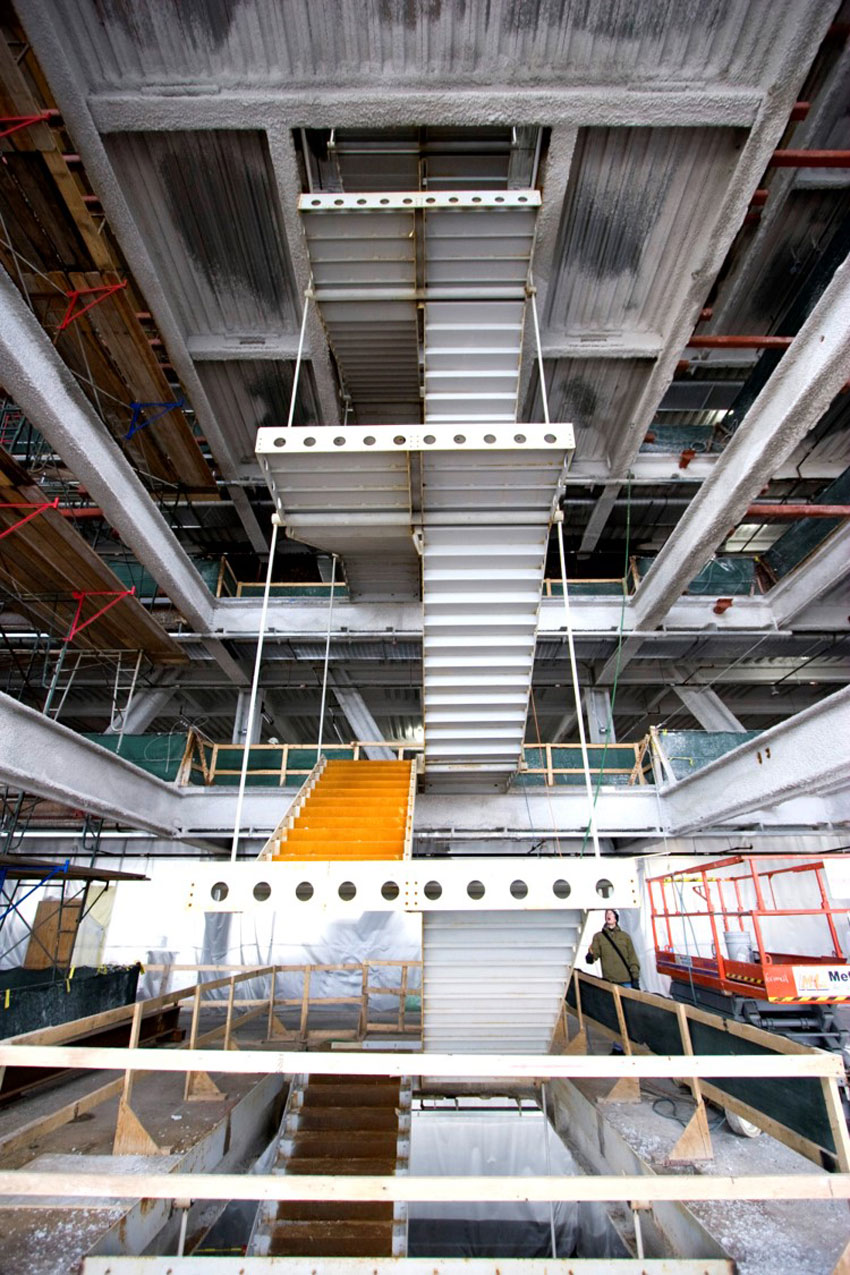
Photo courtesy of MKA
Pictured is the interior steel stairway hanging from the new construction above Blue Cross Blue Shield’s vertical expansion.
“The ability to assemble and disassemble parts of the original steel frame, combined with the lightweight solutions for the tower above, were all only possible in steel,” says Davies. “Being adaptable for future needs was a true sustainability win.”
Another example where early involvement with the steel fabricator led to significant savings is MKA’s design for the Frank Gehry Experience Music project in Seattle, which involved an extensive use of plate steel cut to customized shapes.
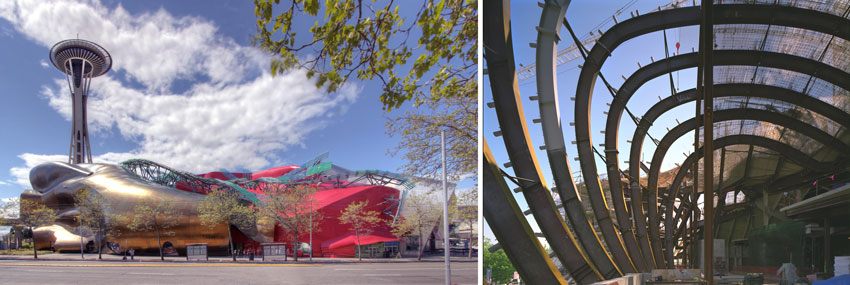
Photo courtesy of MKA
MKA’s design for the Frank Gehry Experience Music project features a steel rib cage, with each rib fabricated in a unique custom shape.
Looking for a way to minimize waste, the fabricator came up with an innovative solution utilizing software from the garment and shoe industry that optimized cutting different shapes out of a flat surface with minimal waste.
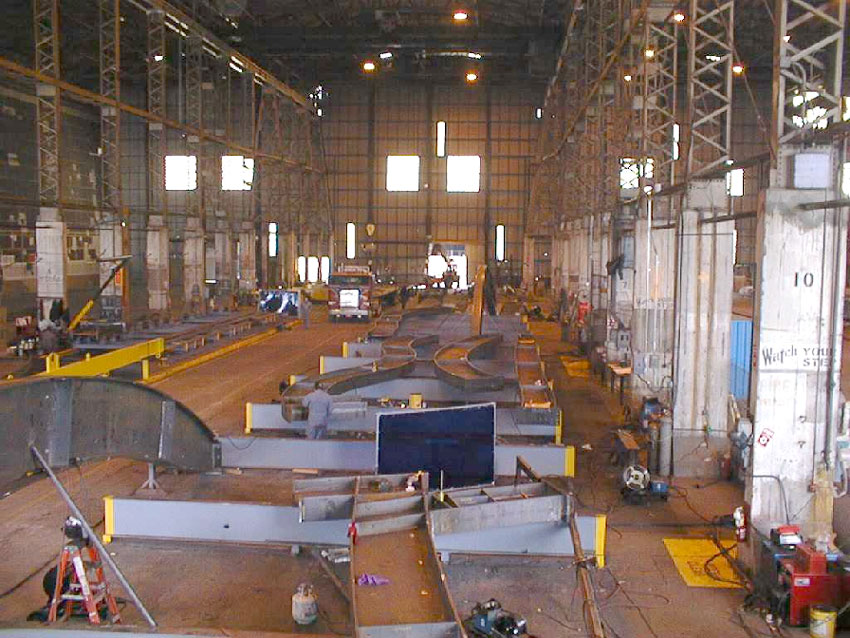
Photo courtesy of MKA
Here the ribs are being welded and laid out in the shop, capitalizing on a software tool from the garment industry.
“It was fascinating to see this kind of cross-industry evolution, and it helped to save both money and material,” relates Davies. “None of us are an expert at everything, and engaging those that know their part of the business best is almost always a winning combination.”
Clearly proving the benefits of the fabricator’s early involvement is the recent Mercy Heart and Vascular Center at the St. Vincent Medical Center project in Toledo, Ohio. The original design-bid-build project delivery model without fabricator input resulted in an over-budget project with a steel package valued at $2.8 million for 910 tons of structural steel. After transitioning to a design-build model that included the steel fabricator on the project team, the steel package was reduced to 772 tons at a cost of $2.35 million, with no change to the owner’s building program.
The global warming impacts associated with the reduction in tonnage fell from 1,056 tons of CO2 equivalent to 895 tons of CO2 equivalent, for a savings of 15 percent. “Additional savings were gained in the simplification of fabrication operations evidenced by a reduction in the per-ton cost of the fabricated steel,” report Cross. “It should be noted that the project schedule was also reduced by 16 weeks, from 52 weeks to 36 weeks.”
Conclusion
As the producer of a highly sustainable, multi-attribute building material, the structural steel industry has a proven track record and continues to stride toward further reducing the material’s environmental footprint.
Since 1990, the industry has posted an overall reduction of greenhouse gas and other emissions of 36 percent, while increasing the average strength of structural steel sections by 40 percent. Similarly, major improvements in mill technology have produced a reduction of the man-hours required to produce a ton of steel from 12 hours per ton in the 1970s to 0.6 man-hours per ton in 2016.
In conclusion, Davies states, “Steel lets us optimize building designs in very materially unique ways. Steel’s ductility when pushed past its yield point is ideal for seismic applications, its strength-to-weight ratio is superior, and its potential for preassembly and disassembly can lead to reuse in ways that other materials really can’t touch.”
Structural steel is truly a cradle-to-cradle, multi-attribute sustainable material.
Barbara Horwitz-Bennett is a trade press journalist who has covered the design and building industry for the past 17 years. She contributes regularly to a number of leading architectural publications.
![]() |
The AISC Steel Solutions Center provides a wide range of technical information and support services for building teams, including information on the sustainable attributes of structural steel. To learn more about structural steel and sustainability, the Steel Solutions Center can be reached at 1-866-ASK-AISC or solutions@aisc.org. |