The Use of Extruded Concrete in Rainscreen Applications
Learning Objectives:
- List the water-management, fire-resistance, strength, and durability benefits of including rainscreens in commercial buildings.
- Identify the common materials used to manufacture rainscreens.
- Compare and contrast the performance characteritics of common rainscreen materials.
- Explain the processes of creating and installing prefabricated panelized systems.
- Describe the benefits of extruded concrete and how the material contributes to a building’s longevity, energy efficiency, and aesthetics.
Credits:
This course is approved as a Structured Course
This course can be self-reported to the AANB, as per their CE Guidelines
Approved for structured learning
Approved for Core Learning
This course can be self-reported to the NLAA
Course may qualify for Learning Hours with NWTAA
Course eligible for OAA Learning Hours
This course is approved as a core course
This course can be self-reported for Learning Units to the Architectural Institute of British Columbia
Rainscreen systems can help protect a building from wind, rain, and all forms of extreme weather. Until recently, the materials available for rainscreens were aluminum panels, phenolic panels, or fiber cement panels. The availability of extruded concrete is changing the game. Appropriate for both rainscreen applications and other exterior facade features, extruded concrete is thin, light, strong, and noncombustible. It is available in many colors and even can be incorporated in panelized or unitized applications. This course will compare extruded concrete to other rainscreen material options and describe the many benefits of using extruded concrete in your next rainscreen application.
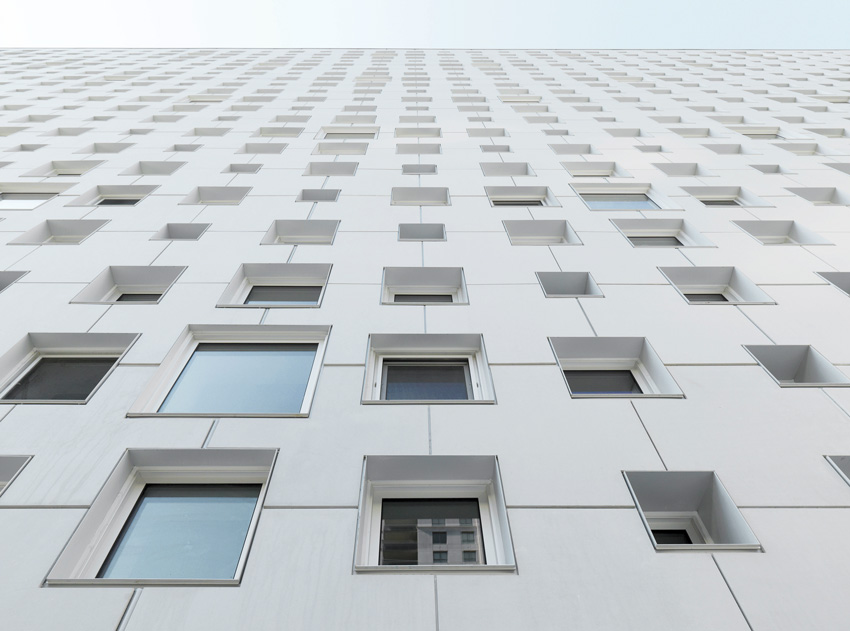
© Ditz Fejer
Available in many organic colors, thin, light, and durable extruded concrete panels can be part of an effective rainscreen system.
What is a Rainscreen?
A rainscreen is an exterior wall detail in which the exterior cladding or siding is installed with a small air gap between the cladding and the rest of the wall assembly. This space helps to create a capillary break and provides a path for moisture to exit the building envelope. This strategy not only enhances the durability and longevity of the building, but it also contributes to the health and well-being of occupants.
While some refer to the air gap and others to the cladding material when discussing rainscreens, in actuality, a rainscreen is a system that includes three essential components: the exterior cladding (the “screen”), a sealed air gap, and a water-resistive barrier, or WRB. The rainscreen assembly also must include openings or vents that connect the air gap to the outside. Some rainscreen systems only include vents (or “weep holes”) at the bottom of the assembly, while others include vents at both the top and bottom of the wall. These components work together to protect the structure by controlling external moisture so that it does not reach the building’s substructure.
How Rainscreens Work
A rainscreen assembly helps keep water out of the building interior by providing a barrier against the water outside and controlling any water that makes it past the cladding. The internal air gap and WRB ensure that any water that makes its way in either evaporates or is drained through the gap and back outside. Some systems work to force air through the wall cavity/air gap to moderate the pressure differential between the exterior and interior wall, thus reducing the amount of moisture that is drawn into the building.
The air gap creates a path for liquid water to drain out of the envelope; it also creates a capillary break between the cladding and the WRB. An assembly that includes ventilation at both the top and bottom of a wall can dry out more quickly. This is because air rises as it is heated, a phenomenon known as the stack effect. A gap as small as 1/16 inch will provide a capillary break; however, most rainscreen assemblies include an air gap that is at least ¼ inch and up to 3/4 inch wide.
There are several ways to create the air gap. Many builders use vertical wood furring strips that are made on-site and attach directly to the studs. Other options include plastic mesh and textured or “bumpy” housewraps. Some of these materials allow for horizontal air movement as well as vertical venting.
Moisture management is a rainscreen’s raison d’etre. The main benefit of a rainscreen is that it facilitates the drying of the sheathing should moisture accumulate there. It also helps cladding that has become wet from precipitation dry out. The long-term benefits of moisture management include a healthier, more durable building. To understand these benefits, let’s take a look at the ways moisture can intrude upon the building envelope.
The Risks of Water Infiltration
When it comes to understanding the behavior of moisture in buildings, it’s important to remember that water follows the path of least resistance. Buildings receive moisture in the form of “bulk moisture.” This liquid moisture can contact buildings in the form of precipitation (rain and snow) or as flowing groundwater (flooding). Moisture in the air will condense on surfaces when the surface temperature falls below the dew point. Water also can enter a building at the time of construction if building materials aren’t adequately dry.
Roofing and exterior walls receive the impact of bulk water when it rains or snows; however, while roofing systems are designed to shed water downward to the eaves, exterior walls are more exposed to variations in water flow.
The exterior material impacts how water behaves. For example, because masonry is porous, a masonry wall will absorb water unless it has been protected with a water-resistant seal. Water that permeates through an unsealed masonry wall will eventually dry unless it encounters a weak spot in the joints.
When water encounters a nonporous material—for example, metal or glass—it follows the path of least resistance and trickles downward. However, wind can push it in any direction, even up under a roof. Wind can also push water through weak points in the exterior cladding.
Moisture damage is every builder’s nightmare. Moisture damage can compromise a building’s structural integrity, and groundwater entry from flooding can cause lasting damage to the building’s foundation. Trapped moisture can create conditions that lead to rot, mold growth, and/or insect infestation.
Increasingly, building professionals are recognizing the link between moisture and the health and well-being of building occupants. Many moisture-compromised materials release volatile organic compounds (VOCs) as they degrade, which can negatively impact health with long-term exposure. Moisture inside buildings can lead to mold and mildew growth, and it also creates ideal conditions for certain bacteria and dust mites. The presence of these, in turn, can aggravate allergies and respiratory conditions such as asthma. Often occupants suffer symptoms for months without realizing their homes or workspaces are making them sick.
A Comprehensive Strategy
Most building codes do not require rainscreens, although Oregon requires them in new residential construction, and British Columbia requires them in coastal areas. Though rainscreens require additional labor and materials, the benefits usually far outweigh the cost, and rainscreens have become standard practice in areas such as the Pacific Northwest.
Because moisture in buildings is such a serious problem, building professionals should plan a comprehensive water mitigation strategy early on in the design process. In environments that experience high humidity and frequent rainfall—for example, coastal zones—a rainscreen system can play a key role in a comprehensive strategy for keeping water out of the building.