This CE Center article is no longer eligible for receiving credits.
Applicable Codes and Standards
The family of codes published by the International Code Council (ICC) includes the building code and fire code which address in detail the requirements for safety and slip resistance in stairs and means of egress as already discussed. It is important to note, however, that while these codes apply in the majority of states in the U.S., some states have adopted either revised editions of these codes or still use their own independent codes. Hence, it is always appropriate to review the prevailing and current code requirements in any given area related to stair and egress design. While this is the appropriate starting point, there are also a number of other applicable standards that come into play and need to be addressed whenever specifying and designing with manufactured treads and nosings:
Handicapped Accessibility
The Americans with Disabilities Act (ADA) sets out specific requirements for barrier-free environments including stairways. Some of this has been codified in American National Standard ICC A117.1 (the Standard) which is appended to most building codes as the prescriptive requirements to achieve such barrier-free environments. Section 504 of this standard specifically addresses stairways indicating more stringent requirements on treads and risers. It states that the vertical risers shall be at least 4 inches and no more than 7 inches tall while the horizontal treads shall be at least 11 inches deep, which is all consistent with the International Building Code requirements for stairs. In Section 504.4 this Standard goes on to state that the surface of a tread must comply with the provisions of a floor surface as described in Section 302. These include being stable, firm, and slip resistant. The Standard and codes do not quantify slip resistance, but the ADA does recommend a coefficient of friction level of .60 or above for walkways and .80 for ramps. It is common for manufactured treads and nosings to achieve coefficient of friction levels on the order of 0.98 – 1.02 or well above the minimum called for. Other requirements in the Standard for floor surfaces include being level within a slope of 1:48 and any openings in the surface must not allow passage of a ½-inch diameter sphere. If these openings are elongated, then they must be perpendicular to the direction of travel. It is worth noting that all these same floor surface requirements also apply to ramps as cited in 405.4 of the Standard.
 |
Cast aluminum treads and nosings
Photo courtesy of Nystrom, Inc. |
Nosings receive a fair bit of detailed attention in Section 504.5. First the leading edge of the tread shall have a maximum radius of ½ inch where it aligns with the riser below. If the nosing projects past the riser it is first limited to 1-1/2 inches maximum past the riser but it must also have the underside of the nosing curved or beveled. The riser below can be angled back from the nosing provided that angle is no more than 30 degrees and the projection remains within the 1-1/2-inch maximum. In terms of specifying a manufactured nosing, all of these details must be provided for to assure both compliance with the standard and that there is no protruding lip that could be a tripping hazard.
Beyond the functional walking aspects of treads and risers, the Standard adds a visual requirement in Section 504.5.1. It requires that the leading 2 inches of the tread is differentiated with a contrasting color from the rest of the tread. This can be either a dark edge on a light-colored tread (e.g., black nosing on a gray concrete tread) or a light-colored edge on a darker-colored tread (e.g., yellow safety nosing on a black stair tread). Clearly, this is meant to help visually impaired people as well as improve the general safety of everyone.
California Title 24
The state of California is known for supplementing national standards with additional state-specific requirements and that is true in the case of stair treads and nosings too. Specifically Title 24 addresses the visually impaired aspect of nosings with a variation on the Standard A117.1 requirements. It calls for the same 2-inch-wide contrasting color strip but specifies that it must be within an inch of the front of the nose of the stair. Some have interpreted this in different ways, but the stair industry has responded by providing a 3-inch nosing that can have all or any 2-inch part of it treated with a contrasting color.
Occupational Safety and Health Administration (OSHA)
Consistent with this federal agency's mission of protecting workers, they have identified requirements for stairs. Specifically in Section 1910.24f of their standards, it states, “All treads shall be reasonably slip-resistant and the nosings shall be of nonslip finish. Welded bar grating treads without nosings are acceptable providing the leading edge can be readily identified by personnel descending the stairway and provided the tread is serrated or is of definite nonslip design. Rise height and tread width shall be uniform throughout any flight of stairs including any foundation structure used as one or more treads of the stairs.” This language addresses the same concerns as the building codes and the handicapped accessibility requirements for stairs, but without the same level of detail. Therefore, by complying with the previous codes and standards referenced, OSHA compliance would seem to be met as well.
ASTM F1637 Standard Practice for Safe Walking Surfaces
The American Society of Testing Materials produces many standard specifications for many things related to design and construction. In the case of walking surfaces ASTM F1637 is the published standard available. It addresses indoor and outdoor walking surfaces indicating that walkway surfaces shall be slip resistant under expected environmental conditions and use. It goes on to state that when wet conditions are reasonably foreseeable, then an abrasive additive, grooving, texturing, or other appropriate means shall be incorporated to render the surface slip resistant. This would apply to the treads as walking surfaces on exterior stairways and they should be treated accordingly.
Clearly, then, there are numerous sources of requirements and safety standards that can be consulted on stair design and on treads and nosings in particular. It is incumbent upon the architect as designer and specifier to address these as part of the stair design and it is incumbent on the construction contractor and manufacturers of treads and nosings to follow through and provide the safe conditions called for.
 |
These examples of extruded aluminum nosings show a ribbed profile (top) and a full abrasive profile (bottom).
Images courtesy of Nystrom, Inc. |
Available Tread and Nosing Products
In writing the specifications for treads and nosings, there are numerous points to consider and understand so that the correct products are called for. First is the material used in the manufacturing process. For moderate-duty treads and risers, extruded products are most commonly made from an aluminum alloy referred to as Alloy 6063 / T5. This alloy contains about 97 percent aluminum mixed with small amounts of other metals including chromium, copper, iron, magnesium, manganese, silicon, titanium, and zinc. Each of these added metals provide added characteristics either to enhance the strength and durability of the aluminum or to make it easier to extrude and machine into shape. For heavy-duty stair treads and nosings, either cast aluminum or cast iron can be specified. The common casting aluminum is referred to as Alloy 319 preferred because of its good sand casting characteristics and machining capabilities. It contains fewer added metals in the alloying process, which are limited to tiny amounts of iron, copper, and zinc for strength and durability. In some interior locations an alternative to cast aluminum is high-quality gray cast iron that complies with ASTM A-48-70. Gray iron has unique properties in the distribution of stress, corrosion resistance, unlimited design, abrasion resistance, vibration absorption, and economy. Ductile iron is available but is generally not selected for stairs since it is better suited to other uses and is notably higher in cost. All of these metal options include the ability to specify recycled content since they are very common building materials.
Once the fundamental decision is made about the metal and type of manufacturing process, the next item is the abrasive material that is added. In extruded shapes, this abrasive material is commonly a combination of aluminum oxide and a two-part epoxy which provides a durable slip-resistant surface for walking on. The aluminum is extruded with ribs running along the surface and the abrasive is placed in between. This creates the common ribbed look and is used extensively. An alternative is to specify a full abrasive product, most common for nosings, where the ribs are shorter and the abrasive material covers over the top of them across the width of the product. For cast products, a continuous coating of silicon carbide at least 1/32 inch thick is used.
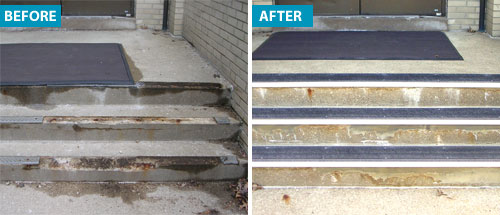 |
Left: Concrete stairs show their deteriorated condition before using renovation treads. Right: The stairs—with new renovation treads installed—have been restored to a safe condition.
Photos courtesy of Nystrom, Inc. |
Steps and stairways are common to most buildings as a key element of circulation and movement of people through individual spaces and the entire building. They also serve as a means of egress in the event of fire or other emergencies and are regulated in great detail by building codes and standards as a result. From a safety standpoint, they are one of the most common locations for people to trip, fall, and be injured. The importance of designing safe and code-compliant stairs cannot be understated particularly since architects are sometimes held liable for damages to people injured on those stairs. Among the most significant safety details to be addressed are the proper design and specifications for treads and nosings installed in a variety of locations and construction types.
Stair Tread and Nosing Design Parameters
Steps and stairways have been constructed out of many different materials and in many different construction assemblies. Historically, all of the stair parts and components were typically made of whatever material was consistent with the rest of the building such as stone, wood, or masonry. Not all of these materials or stair assemblies held up well as the building was used over time with surfaces becoming worn, damaged, or as assemblies settled or became loose. In the late 1800s, cast metal was introduced into stair design to help address some of these issues by providing stronger and more durable components, particularly on stair treads, making them less susceptible to problems. During the 1900s stair design in commercial and institutional buildings became fairly standardized, falling into several familiar material categories: wood, solid concrete, solid metal, and metal pans with concrete fill. At the same time, manufactured treads and nosings emerged as a popular way to treat the walking surface of stairs for increased durability, safety, code compliance, and slip resistance.
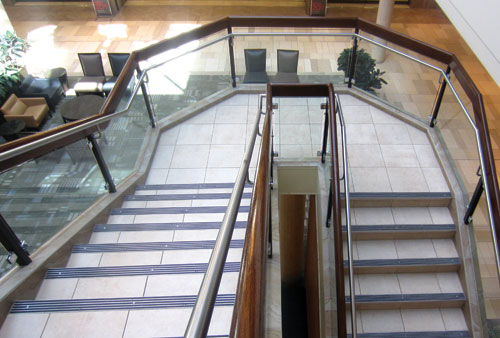 |
Ridgedale Center Mall, Minnetonka, Minnesota
Photo courtesy of Nystrom, Inc. |
Building codes commonly define a stair as “a change in elevation, consisting of one or more risers” with a riser being the vertical portion of the individual steps. They go on to define a stairway as “one or more flights of stairs” and also include “the necessary landings and platforms connecting them, to form a continuous and uninterrupted passage from one level to another.” Hence a stairway is the total assembly connecting levels within a building. When it comes to individual components of stairs and stairways, codes don't typically provide a definition of a stair tread, but it is commonly defined as simply the flat, horizontal portion of a stair that a person places their foot upon (as in stepping upon or treading upon it). Codes typically require a minimum depth of stair treads on the order of 11 inches and mandate consistency in their dimensions along a run or flight of stairs. Stair nosings are a distinct part of a tread that building codes define as “the leading edge of stair treads.” Nosings also apply to the leading edge of landings at the top of stairway flights. The codes address the size and depth of the nosing for different stair profiles and call for them to provide a degree of slip resistance along their surface. For purposes of this article, all of these elements of defining stairs, stairways, and treads and nosings apply. However, we will generally differentiate a tread from a nosing based on the stair industry standard—a nosing is defined as 4 inches or less in depth and a tread is defined as greater than 4 inches in depth (i.e. commonly the full depth of the stair tread).
In light of all of the above, it is common current practice to design and specify stair treads and nosings as distinct elements of the overall stair design. As distinct elements, they can be added to the supporting material of wood, concrete, or steel that the stairs are made from. Further, they can be specified for both new and retrofit/renovation installations. For commercial and institutional buildings with moderate to high levels of foot traffic, extruded aluminum nosings and treads are often selected for both interior and exterior locations. The aluminum extrusions are typically filled with abrasive material running from side to side along the width of the tread or nosing. When using this approach in stair treads, the abrasive material is typically installed in channels in the extrusion, thus forming alternating strips of exposed aluminum and abrasive running across the stair tread. It is also possible to use “full abrasive” treads and nosings which have the abrasive material covering over the top of the extrusions so that only the abrasive material is seen.
In industrial or very heavy foot traffic conditions, full cast aluminum treads and nosings can be used. This approach is also applicable for both new construction and renovation/retrofit applications. These are solid aluminum products on the order of 5/16-inch thickness that are manufactured through a sand casting process instead of an extrusion process. Their profiles are often made specifically to fit onto either new or existing poured concrete or concrete filled steel pan stairs. In cases where only the nosing is desired to be added, they are available in different widths and styles. Where full cast aluminum treads are desired, the nosing is typically integral to the product along the leading edge. In either case, they are finished with an abrasive silicon carbide covering over the top of the cast aluminum. They may also include a diamond or crosshatch safety pattern in the aluminum for greater slip resistance. The cast aluminum will take the brunt of the traffic and any abuse, thus protecting and preserving the concrete beneath it and helping to ensure a well-maintained stair that remains intact and safe over time.
 |
Stair treads are the full horizontal surface that a person steps upon while the nosing is the leading edge of the tread.
Photo courtesy of Nystrom, Inc. |
Applicable Codes and Standards
The family of codes published by the International Code Council (ICC) includes the building code and fire code which address in detail the requirements for safety and slip resistance in stairs and means of egress as already discussed. It is important to note, however, that while these codes apply in the majority of states in the U.S., some states have adopted either revised editions of these codes or still use their own independent codes. Hence, it is always appropriate to review the prevailing and current code requirements in any given area related to stair and egress design. While this is the appropriate starting point, there are also a number of other applicable standards that come into play and need to be addressed whenever specifying and designing with manufactured treads and nosings:
Handicapped Accessibility
The Americans with Disabilities Act (ADA) sets out specific requirements for barrier-free environments including stairways. Some of this has been codified in American National Standard ICC A117.1 (the Standard) which is appended to most building codes as the prescriptive requirements to achieve such barrier-free environments. Section 504 of this standard specifically addresses stairways indicating more stringent requirements on treads and risers. It states that the vertical risers shall be at least 4 inches and no more than 7 inches tall while the horizontal treads shall be at least 11 inches deep, which is all consistent with the International Building Code requirements for stairs. In Section 504.4 this Standard goes on to state that the surface of a tread must comply with the provisions of a floor surface as described in Section 302. These include being stable, firm, and slip resistant. The Standard and codes do not quantify slip resistance, but the ADA does recommend a coefficient of friction level of .60 or above for walkways and .80 for ramps. It is common for manufactured treads and nosings to achieve coefficient of friction levels on the order of 0.98 – 1.02 or well above the minimum called for. Other requirements in the Standard for floor surfaces include being level within a slope of 1:48 and any openings in the surface must not allow passage of a ½-inch diameter sphere. If these openings are elongated, then they must be perpendicular to the direction of travel. It is worth noting that all these same floor surface requirements also apply to ramps as cited in 405.4 of the Standard.
 |
Cast aluminum treads and nosings
Photo courtesy of Nystrom, Inc. |
Nosings receive a fair bit of detailed attention in Section 504.5. First the leading edge of the tread shall have a maximum radius of ½ inch where it aligns with the riser below. If the nosing projects past the riser it is first limited to 1-1/2 inches maximum past the riser but it must also have the underside of the nosing curved or beveled. The riser below can be angled back from the nosing provided that angle is no more than 30 degrees and the projection remains within the 1-1/2-inch maximum. In terms of specifying a manufactured nosing, all of these details must be provided for to assure both compliance with the standard and that there is no protruding lip that could be a tripping hazard.
Beyond the functional walking aspects of treads and risers, the Standard adds a visual requirement in Section 504.5.1. It requires that the leading 2 inches of the tread is differentiated with a contrasting color from the rest of the tread. This can be either a dark edge on a light-colored tread (e.g., black nosing on a gray concrete tread) or a light-colored edge on a darker-colored tread (e.g., yellow safety nosing on a black stair tread). Clearly, this is meant to help visually impaired people as well as improve the general safety of everyone.
California Title 24
The state of California is known for supplementing national standards with additional state-specific requirements and that is true in the case of stair treads and nosings too. Specifically Title 24 addresses the visually impaired aspect of nosings with a variation on the Standard A117.1 requirements. It calls for the same 2-inch-wide contrasting color strip but specifies that it must be within an inch of the front of the nose of the stair. Some have interpreted this in different ways, but the stair industry has responded by providing a 3-inch nosing that can have all or any 2-inch part of it treated with a contrasting color.
Occupational Safety and Health Administration (OSHA)
Consistent with this federal agency's mission of protecting workers, they have identified requirements for stairs. Specifically in Section 1910.24f of their standards, it states, “All treads shall be reasonably slip-resistant and the nosings shall be of nonslip finish. Welded bar grating treads without nosings are acceptable providing the leading edge can be readily identified by personnel descending the stairway and provided the tread is serrated or is of definite nonslip design. Rise height and tread width shall be uniform throughout any flight of stairs including any foundation structure used as one or more treads of the stairs.” This language addresses the same concerns as the building codes and the handicapped accessibility requirements for stairs, but without the same level of detail. Therefore, by complying with the previous codes and standards referenced, OSHA compliance would seem to be met as well.
ASTM F1637 Standard Practice for Safe Walking Surfaces
The American Society of Testing Materials produces many standard specifications for many things related to design and construction. In the case of walking surfaces ASTM F1637 is the published standard available. It addresses indoor and outdoor walking surfaces indicating that walkway surfaces shall be slip resistant under expected environmental conditions and use. It goes on to state that when wet conditions are reasonably foreseeable, then an abrasive additive, grooving, texturing, or other appropriate means shall be incorporated to render the surface slip resistant. This would apply to the treads as walking surfaces on exterior stairways and they should be treated accordingly.
Clearly, then, there are numerous sources of requirements and safety standards that can be consulted on stair design and on treads and nosings in particular. It is incumbent upon the architect as designer and specifier to address these as part of the stair design and it is incumbent on the construction contractor and manufacturers of treads and nosings to follow through and provide the safe conditions called for.
 |
These examples of extruded aluminum nosings show a ribbed profile (top) and a full abrasive profile (bottom).
Images courtesy of Nystrom, Inc. |
Available Tread and Nosing Products
In writing the specifications for treads and nosings, there are numerous points to consider and understand so that the correct products are called for. First is the material used in the manufacturing process. For moderate-duty treads and risers, extruded products are most commonly made from an aluminum alloy referred to as Alloy 6063 / T5. This alloy contains about 97 percent aluminum mixed with small amounts of other metals including chromium, copper, iron, magnesium, manganese, silicon, titanium, and zinc. Each of these added metals provide added characteristics either to enhance the strength and durability of the aluminum or to make it easier to extrude and machine into shape. For heavy-duty stair treads and nosings, either cast aluminum or cast iron can be specified. The common casting aluminum is referred to as Alloy 319 preferred because of its good sand casting characteristics and machining capabilities. It contains fewer added metals in the alloying process, which are limited to tiny amounts of iron, copper, and zinc for strength and durability. In some interior locations an alternative to cast aluminum is high-quality gray cast iron that complies with ASTM A-48-70. Gray iron has unique properties in the distribution of stress, corrosion resistance, unlimited design, abrasion resistance, vibration absorption, and economy. Ductile iron is available but is generally not selected for stairs since it is better suited to other uses and is notably higher in cost. All of these metal options include the ability to specify recycled content since they are very common building materials.
Once the fundamental decision is made about the metal and type of manufacturing process, the next item is the abrasive material that is added. In extruded shapes, this abrasive material is commonly a combination of aluminum oxide and a two-part epoxy which provides a durable slip-resistant surface for walking on. The aluminum is extruded with ribs running along the surface and the abrasive is placed in between. This creates the common ribbed look and is used extensively. An alternative is to specify a full abrasive product, most common for nosings, where the ribs are shorter and the abrasive material covers over the top of them across the width of the product. For cast products, a continuous coating of silicon carbide at least 1/32 inch thick is used.
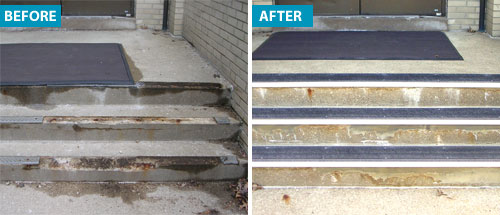 |
Left: Concrete stairs show their deteriorated condition before using renovation treads. Right: The stairs—with new renovation treads installed—have been restored to a safe condition.
Photos courtesy of Nystrom, Inc. |
Properly specifying treads and risers is directly linked to the type of stairs that they are being installed on. There are four basic choices available:
Poured concrete stair installation. Nosings are typically set along the edge of the concrete treads immediately after the concrete is poured and is intended to be flush with the surfaces of the treads and risers.
Steel pan installation. Nosings or treads are set into the concrete supported by the steel pan. Typically, this means a slightly different edge condition to assure that there is no lip protruding past the metal riser that might cause a tripping hazard.
Wood stair installation. Commonly this is a full tread application that sets into or over the wood.
Retrofit installation. This is also a full tread installation that is designed to cover over de-teriorated concrete or wood stairs and restore them to a safe condition.
Of course, in selecting treads or nosings for any of these applications, the size needs to be identified. Three- and four-inch nosing widths are standard since 3-inch or larger nosings will satisfy the requirements of virtually all codes and standards. Nonetheless, sizes ranging from 2 to 12 inches are commonly available for nosings and treads and need to be selected according to the size of the stairs and their construction accordingly.
 |
Two-stage nosing used in metal pan concrete filled stairs
Images courtesy of Nystrom, Inc. |
Cast products typically don't offer many other choices beyond size, but extruded products offer numerous other options including the following:
Single-part products. These are the most commonly used tread and nosing products. They are installed as one piece into poured concrete stairs, onto steel pan concrete filled stairs, or onto wood stairs. In addition to choosing the width, the specific product nosing profile can be selected. For example, the front edge of the nosing will typically be aluminum that can be a short or long piece as appropriate to the installation. If long, then it can be made to suit a 90-degree riser or one that is sloped back. These products are also available as flat pieces without any nosing for use in ramps to provide the needed slip resistance for handicapped accessible and other sloped walking surface situations.
Two-part products. These are popular in steel pan concrete stair applications where concern about protecting the tread and nosing during construction is important. These work particularly well when the stairs need to be done early on a project and there are months of construction foot and equipment traffic going up and down the stairs. As the name implies, there are two pieces installed separately. First, a base plate unit is installed in the concrete fill as with the single part products. However they are shipped with a piece of plywood installed in place of the nominal 3-inch nosing. Later, after construction is nearly complete, the plywood is removed and the finished nosing is installed. Either ribbed or full abrasive nosings are available for this type of product.
Vision line. A contrasting color can be applied to the leading edge of ribbed treads in any color combination. This is particularly important in meeting vision-impaired handicapped accessibility requirements.
Range of colors. The abrasive aluminum oxide in treads and nosings can be specified in as many as nine common colors including black, safety yellow, brown, gray, red, burgundy, orange, green, and blue. Luminescent strips that glow in the dark when first exposed to light are also available in response to some recent code revisions calling for luminescent markings in stairways, particularly in the northeasternUnited States.
 |
A vision line tread with contrasting color for meeting vision-impaired handicapped accessibility requirements and general safety needs
Photo courtesy of Nystrom, Inc. |
Taped tops. For protection during the initial pour, single-stage products can be shipped in some cases with protective tape covering the top or exposed part of the product. Tape must be removed immediately after the stair tread is set, however, so it only offers very short-term protection.
Painted undersides. To prevent a possible reaction between the concrete and the aluminum, the undersides of the treads and nosings can be specified to be coated with a protective paint to separate them from the concrete.
End miter cuts. In design situations where traffic direction changes or stairs turn a corner, it is possible to have the manufacturer or fabricator provide miter cut corners and edges for treads and nosings. The nature of extrusion manufacturing, however, does not lend itself to a curved stair tread with a radius shape.
Hardware. A range of anchor options are typically available including wood screws for wood stair applications, wing anchors with machine screws for concrete or steel pan applications, and nylon expansion shields with screws for renovation treads installed into existing concrete.
Adhesive. In some cases, construction adhesive may be the most appropriate means to secure renovation treads and is available as an option if anchoring is not possible or practical.
Building Information Modeling (BIM) for Treads and Nosings
With all of the choices and options available in design and construction and with the need to coordinate building components more closely, many architects, contractors, and building owners are increasingly turning toward building information modeling (BIM) as an effective and preferred tool in the process. BIM helps the entire project team investigate the options and visualize alternative conditions quickly and easily. It also reveals in three dimensions places that are in conflict so they can be resolved during design rather than the more costly resolution during construction.
Because there are many manufactured products that are documented and available in BIM format, it is more straightforward than ever to use this available library to make a final selection and actually customize products to suit a project's needs. In particular, it is increasingly common that manufacturers will offer tread and nosing computer files in a BIM format so they can be coordinated with the rest of the stair construction. Using the manufacturer's BIM files in the overall computer model will allow for full visualization of the appearance and functionality on different stair surfaces and allow the designers to make the best informed decisions on product selection.
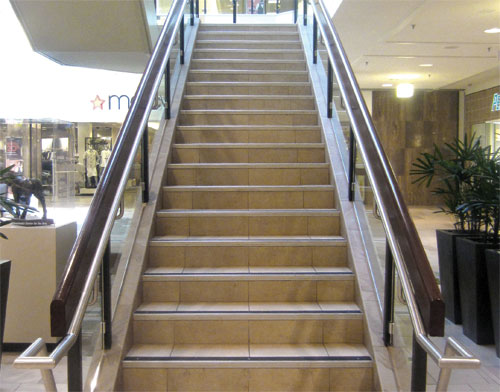 |
The use of a BIM model will help everyone on the design and construction team visualize a finished stair and safety tread installation while avoiding potential conflicts of materials in the field.
Photo courtesy of Nystrom, Inc. |
When architects and engineers are considering BIM objects prepared by building product manufacturers to incorporate into an overall model, they should look for the following characteristics in those objects:
Up-to-date information readily available. Access to information when it is needed is critical to keeping a project on schedule. But that information has to be current and up to date, otherwise a lot of time is wasted detailing the wrong things. Historically, the architect has relied on manufacturer's representatives to update the office library with catalogs, CDs and other information for handy reference. The shortfall in this process is the possibility that the catalogs become out of date without a designer realizing it. Recognizing this, many product manufacturers offer their entire product and design information electronically on their company website. Others are working through independent company sources that provide manufacturer information in catalog and electronic format and are becoming sources of a growing library of BIM objects. Obviously, working with a manufacturer that can provide up-to-date, readily available BIM objects for inclusion in an overall BIM model will be easier than creating a generic object in the design studio.
Accurate visual representation. The BIM model needs to predict the built condition as closely and as accurately as possible. Hence the same is true with building products that are inserted as objects into that model. It is important that the visual characteristics of the computerized object match the detail and properties of the actual physical object. This is easily revealed by comparing the computerized object to photos or samples of the physical object and looking for similarities and discrepancies in details and features.
Complete embedded information. This is where the value of BIM for products really shines. All of the relevant information associated with a selected product should be readily accessed and readable from the BIM object. That means that manufacturers' make and model numbers, full product specifications, cost/pricing information, production and delivery requirements should all be readily available. For the long-term benefit of the owner, it should also include a link to the warranty, maintenance, and replacement information related to the product.
 |
Over filling or over spraying of concrete in metal pan stairs can damage the stair nosings and render their slip resistance to be compromised.
Photo courtesy of Nystrom, Inc. |
Parametric modeling capability. Most BIM software programs allow for automated interaction between different objects. This interaction is governed by a set of computer programming rules that an object must follow anytime a modification or insertion of an object is made. This process is referred to as parametric modeling and is one of the key advantages of using BIM. It means that an object not only provides data about itself, it also has the ability to interact with the rest of the model, such that a change in the object triggers a corresponding change to other parts of the model. For example, inserting a tread into a stair means that the concrete stair has to change to accommodate it. If the tread is one of several and a schedule or chart is part of the model summarizing the details of all of them, then the schedule has to be updated. And if a particular tread has several options built into it, the selection of those options should automatically be reflected in all aspects of the model. In simple terms, parametric modeling is the means to make this all happen.
Complete and open interoperability. Anyone who has ever tried to open a computer file that produced either an error message related to non-compatibility or a display of unintelligible characters will readily understand the need for seamless integration of information from multiple sources. That is what is meant by interoperability—the ability to access complete and accurate information regardless of the source of the different parts of the information. The data from building manufacturers, then, needs to be provided in a format that is accessible by all software identified as important on the project.
Overall, then, while the use of BIM may not be the only way to design a building, it certainly is emerging as a preferred way by many project teams. Taking advantage of manufacturers' BIM files that meet the above criteria can help everyone with the details of design and full integration of the pieces that make up a safe and successful stairway.
Installation and Cleaning
Anti-slip metal safety stair nosings and treads are designed to be installed fully embedded into a substrate such as concrete or secured directly over a flat surface such as wood or existing concrete, any of which need to provide total support for the stair nosing. Actual installation of metal treads and nosings will obviously vary, then, based on the types of stairs they are being installed upon. Wood stair installations are perhaps the most straightforward, in that the wood stairs first simply need to be complete and clean. Then, the metal safety stair treads are simply screw attached to the wood treads and are ready to use.
For cast concrete or metal pan concrete filled stairs, the installation may require a bit more diligence for a successful outcome. Once all of the aluminum products are staged for installation and the concrete forms or metal pans are ready, then the concrete should be poured. Next, the safety nosings should be placed into position in the concrete. Installers need to tamp the safety nosings to insure proper concrete formation around the anchors on the underside and eliminate any voids. This action will prevent the occurrence of hollows and voids, which can lead to flexing and cantilevering of the nosing. Therefore, it is vital that the installer tamp down the stair nosing to totally seat it into the substrate and fully rest upon any riser return such as in pan-filled steps.
Note that metal safety nosing placement may be difficult in concrete with a very low slump (mass). Be certain the concrete mix is of the proper consistency: not too dry, not too wet. Further, the use of very large aggregate in the concrete mix may make installation of the safety nosings difficult and should be avoided. Concrete installers should be aware that over-spraying of the concrete can fill the abrasive area with a concrete coating that will render the slip resistance and appearance ineffective. Further, aggressive finishing and overflow of the concrete has the potential to crack a full abrasive tread or nosing or dislodge the abrasive material from the treads altogether. Obviously, all of these adverse conditions need to be avoided. However, in the event they do happen, manufacturers can provide repair kits for small areas that have been damaged or abused. Note however that repair kits are primarily for aesthetic purposes and do not offer the same stability of treads manufactured at the factory. Typically the kits are shipped with three components—the abrasive in any of the standard colors specified, epoxy hardener, and epoxy resin. Manufacturers' instructions must be followed carefully when using these repair kits to assure that the finished outcome is fairly consistent with the rest of the installation. If defects are found in the material itself, rather than an installation issue, then the products should be covered under a one-year warranty. In that case, they will need to be exchanged or replaced which means that inspecting the products before they are installed in concrete will be much better than afterwards.
For renovation stair tread installation, the industry standard is to provide a 9-inch-deep renovation tread on each step and an 11-inch-deep tread at the top of each run at each intermediate landing. Renovation tread widths should be determined by measuring the width of the existing step to be covered and deducting 6 inches to provide a 3-inch margin at each side. Existing stairs that are badly worn or dished will need to be re-leveled with a fast-setting leveling compound such as an underlayment and patching compound. This will provide a level surface for installation of the renovation treads and usually sets in two to four hours. Once all is ready, the treads can be installed. Renovation treads are typically furnished with two rows of drilled and countersunk holes. An application of construction adhesive to the underside perimeter of the renovation tread as well as around each drilled hole will stop water penetration under the tread. On wooden steps, renovation treads are fastened with wood screws. For attachment to metal steps, bolts and nuts or self-tapping screws can be used. For masonry steps, expansion shields and screws are typical. On any type of exterior stair, most manufacturers recommend stainless steel fasteners. After installation of the renovation treads, the exposed areas of the existing steps, stringers, and risers can be painted to create a fully finished appearance.
Cleaning and maintenance of all of these products is fairly straightforward to specify both at the end of construction and during use. Treads should be swept with a broom or vacuumed with a heavy-duty commercial vacuum cleaner at least once a week. When needed, scrub surfaces vigorously with a stiff bristled brush using a mild detergent but do not use any product containing solvents such as acetone. Rinse thoroughly with water after cleaning. Scuff marks on the aluminum nose can be removed by rubbing with a fine steel wool and a commercial cleaning agent. To remove snow and ice on exterior stairs, sodium chloride salt can be used.
Conclusion
Manufactured safety treads and nosings are available to be incorporated into stairs in literally dozens of styles of extruded aluminum and cast type products. Products can be selected that are suitable for either new construction or renovation and for interior and exterior stairs. They are specifically designed to offer choices that are compatible with wood stairs, poured concrete stairs, metal pan concrete stairs, renovations, and ramps. They create a safe stair environment that complies with building codes and OSHA regulations as well as barrier-free codes and standards for the physically impaired. They are specifically manufactured with epoxy abrasive materials that produce superior slip resistance in a variety of colors that are locked into the epoxy abrasive mixture and will not fade or wear off. Designing and specifying such safety treads and nosings into stairs and ramps produce safer walking surfaces for all users of those areas. They also meet a reasonable standard of care for providing safe environments as part of architectural practice.
Peter J. Arsenault, FAIA, NCARB, LEED AP, practices, consults, and writes about sustainable design and practice solutions nationwide. www.linkedin.com/in/pjaarch
 |
Nystrom is a global supplier of complementary building products and services which include miscellaneous and specialty construction items. Nystrom partners with clients to simplify specifying and procurement—minimizing cost and time associated with the construction project workflow. www.nystrom.com |