Stunning Facades with Sintered Stone
Four Types of Building Facade Applications
Recognizing the advantages of sintered stone panels, including their lightweight and highly durable properties, many architects are using them for their facade designs. Construction crews are then finding that they are easy to work with and that large sizes reduce installation time compared to other materials. The use of this thin product means it can be installed over existing surfaces, avoiding demolition and waste disposal in retrofit or renovation projects. It’s very light size-to-weight ratio also means that the supporting wall does not typically need any extra reinforcement; rather, it can easily be installed on conventional light-gauge metal framing wall systems.
With all of this in mind, we will look at four common ways to design and install sintered stone as part of a building facade. Of course, it is always prudent to be sure they are installed per manufacturers’ recommendations for specific types of applications and conditions.
Thin-Set Veneer
In the simplest form, panels can be attached using common thin-set adhesives to create a chemical bond between the sintered stone panel and an appropriate, relatively smooth substrate. This is particularly attractive for retrofit installations where a preexisting, relatively smooth facade is already in place but is in need of updating. Provided the existing material is sound and can be cleaned to receive the thin-set adhesive, then large-sized sintered stone panels can be applied directly over the existing surface, joints, cracks, etc. In new construction, the same process can be undertaken over new exterior sheathing or masonry building materials.
There are a number of benefits of this direct-set installation, not the least of which is the complete lack of any need for mechanical fasteners. The adhesive attachment is done completely on the back side of the panel, which means the panel joints are all that is seen on the face. From a performance standpoint, this type of mounting uses the continuous nature of the chemical-elastic bonding to distribute stress evenly, preventing any concentration of stress in the adhesion surface and minimizing critical points where ruptures could begin. The flexibility of the system reduces or eliminates the transfer of vibrations between materials in contact and helps prevent failure in the connection due to fatigue. The nonconductive properties of such anchoring enables the connection of different types of materials and prevents galvanic corrosion.
Ventilated Rainscreen Systems
A popular building facade design approach is to use a rainscreen system that works on the principle of separating the exterior cladding from the full wall assembly. The space between the two is intentionally designed to allow for air to enter and ventilate the wall as well as allow any water that enters to drain out of the bottom and away. The assumption is that rather than try to completely isolate water from penetrating the exterior cladding, that some water or moisture will indeed get in at some point, so go ahead and plan for its escape. In this case, the cladding is simply the first line of defense against the weather, and the full air- and water-sealed wall surface behind it is the second. Sintered stone can be used quite effectively as a cladding for this type of exterior wall facade.
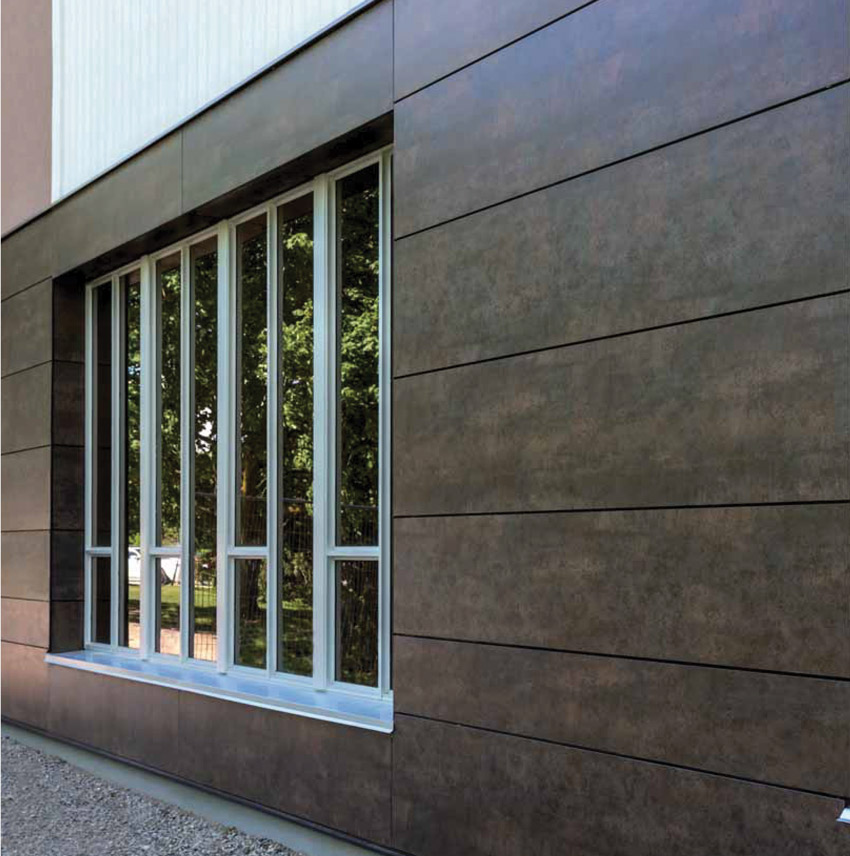
Sintered stone panels used for rainscreen applications allow water to drain away behind the cladding.
For tall buildings subjected to higher wind loading, ventilated rainscreens need to be looked at a bit closer. Higher wind loads mean more pressure is applied to the exterior cladding, and that can cause problems either to the cladding or the systems behind it. The solution is a pressure-equalized rainscreen, which relies on creating smaller compartments across a facade rather than one continuous ventilation cavity. These ventilation compartments respond independently to constantly changing wind pressure. When wind-driven air enters openings in the bottom of the sintered stone panels and finds no way to exit, the air pressure inside the cavity matches the wind’s pressure and “pushes back” against it, preventing wind-driven rain from entering. If a small amount of rain is driven into the cavity, the same openings allow the water to drain. Since these systems perform well under severe conditions, they can be shown to meet the approval of specific regional regulations, such as Miami-Dade County for hurricane resistance.
Curtain Wall Systems
Curtain walls are a popular means of enclosing a multistory building. In this case, individual wall panels are assembled either in a factory as a unitized system or on-site as a component system. Either way, the completed assembly is secured to the building structure and runs continuously outside of it, passing over columns, beams, floor structure, and other building elements to encase and enclose the building. Most curtain wall systems contain a combination of glazed and insulated opaque sections following the specific design of the architect. The opaque sections could be spandrel glass or some other material appropriate to the design.
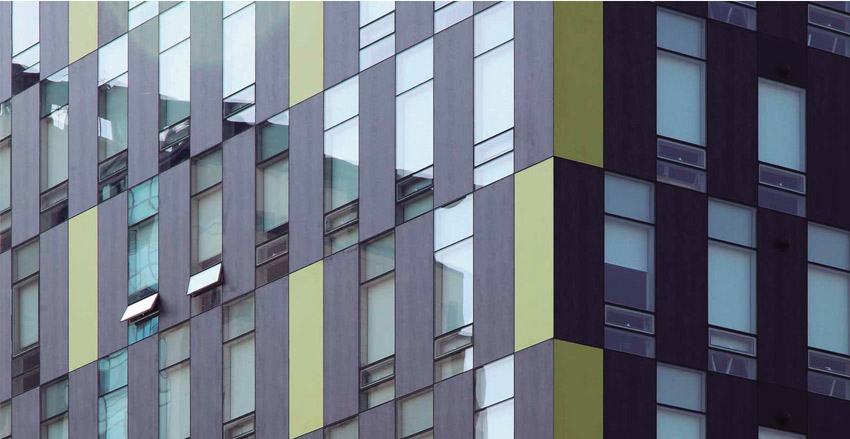
Sintered stone panels can be incorporated into a curtain wall system for building facades.
The thin and lightweight nature of sintered stone panels allows them to be readily substituted for spandrel glass or other opaque materials in a curtain wall system, often with the same detailing. The sintered stone panels simply fit into the curtain wall where the glass would have otherwise gone. Further, they can fully conceal and protect the area behind the panels, allowing those portions of the wall to be fully and continuously insulated. All of this allows the building to be constructed in a conventional, familiar manner but with the appearance and other attributes of the sintered stone.
Carrier Support Systems
In some cases, it is desirable to have a full mechanical support system that attaches to a building wall assembly and then receives the sintered stone cladding. This is particularly true for rainscreen installations but can also be desirable in cases where there is not a suitable substrate for attachment. It can also be appealing when an existing building is no longer square and level and a support system can be adjusted to allow for a corrected facade. Either way, the common approach is to use some engineered aluminum extrusions that attach to the building and receive the sintered stone facade panels on the exterior. Such systems can use visible support squares or safety clamps to which the panel edges are secured. With these support square clamps, it is possible to adjust the location of the panel and achieve proper levelling. The support square clamps are secured to the vertical sections of the support system, commonly with stainless steel screws, allowing the panels to be quickly and easily replaced if needed. To ensure the stability of the system, a line of elastic adhesive can be placed all along a vertical T-profile support. This elastic adhesive also improves the system’s reaction to wind pressure or suction and loads since the possible vibrations caused by these forces are absorbed by this adhesive.
Alternatively, there are many cases where using concealed fastening is preferred so that no clips or anchors are visible on the facade. There are several choices in this regard. The first is to use a support system designed to connect to the unexposed rear side of a sintered compact panel. This approach is available from manufacturers based on creating angled grooves in the back side of the panel and securing horizontal aluminum channels into the grooves. In at least one case, this is achieved with a double groove at opposing 45 degree angles (like a dovetail in carpentry terms), where two aluminum profiles are inserted and fixed with structural adhesive to secure the channels to the panels. The connected channels are then secured to the aluminum support system holding up the whole facade. The panels can hang and be levelled either to align with adjacent panels or be staggered without needing to increase the number of vertical supports. In all cases, this method of attachment allows the support system to become invisible due to the concealed fastening and aluminum members. This approach also eliminates the risk of panels separating from the structure in the event of breakage, which is why this system is considered to be among the most secure available on the market. It also allows for easy removal and replacement of panels when necessary.
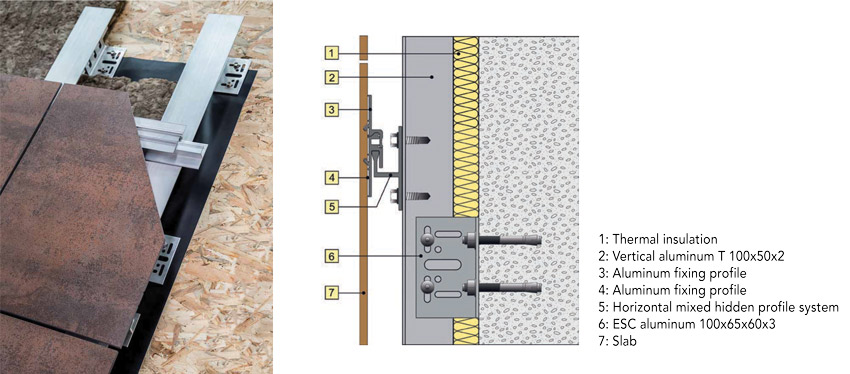
A carrier support system with concealed mechanical supports that is currently available relies on grooves being placed in the back side of sintered stone panels with aluminum support channels inserted and secured.