Stunning Facades with Sintered Stone
Learning Objectives:
- Identify and recognize the code-compliant characteristics and beneficial environmental properties of sintered stone facades.
- Investigate the manufacturing process of sintered stone and the suitability of the product for a full range of building types.
- Assess the functional contributions of sintered stone slabs as they contribute to green and sustainable building design.
- Specify quality control based on updated relevant standards for sintered stone facades for green and conventional buildings.
Credits:
This course is approved as a Structured Course
This course can be self-reported to the AANB, as per their CE Guidelines
Approved for structured learning
Approved for Core Learning
This course can be self-reported to the NLAA
Course may qualify for Learning Hours with NWTAA
Course eligible for OAA Learning Hours
This course is approved as a core course
This course can be self-reported for Learning Units to the Architectural Institute of British Columbia
Designing a building facade, whether commercial, residential, new, or retrofit, can be both artistically enjoyable and technically complex. While part of any series of facade studies looks at the relationships between glazed and opaque areas, the planar and three-dimensional aspects of the building, and the overall building image being created, the specific materials used to create the facade can influence the design process as well as the outcome. Similarly, when the performance characteristics of the facade are being addressed, a host of issues come into play that can overtake the effort expended on glazing options. These include things like noncombustibility, insulated wall assemblies that address thermal bridging, pressure equalization of facades, and other technical issues. From a materials standpoint, the outer surface, or cladding, needs to demonstrate integrity and durability, ease of detailing, manageable weight, and general code compliance. While many traditional materials have been used on facades for centuries to address this variety of design issues, new building technologies and owner requirements have prompted the need for new materials to be considered too.
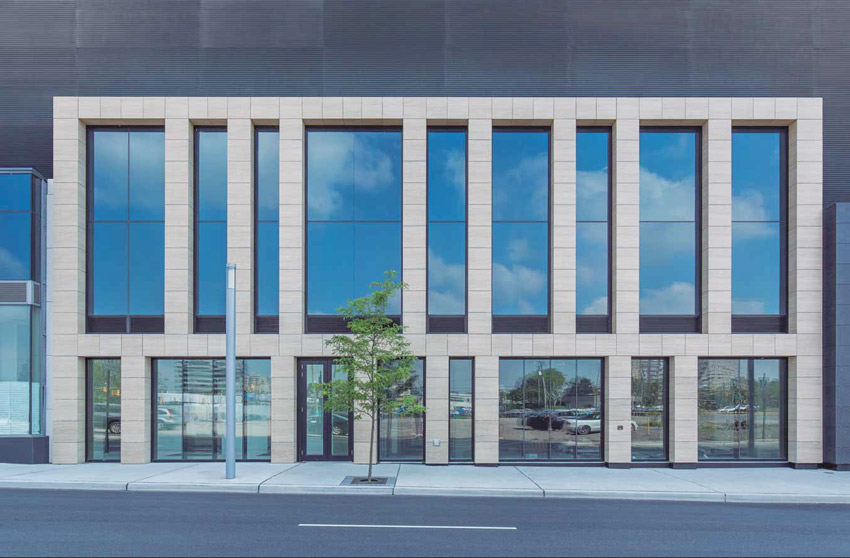
All images courtesy of Neolith by TheSize Surfaces
Building facades using sintered stone help create lighter, stronger, more durable, and more sustainable buildings with a full range of design and performance capabilities.
Sintered stone is an excellent example of such an emerging product that is being discovered by architects around the world for use in building facades. With an array of impressive characteristics, sintered stone helps create lighter, stronger, more durable, and more sustainable buildings. As a product choice, it can provide the artistic appeal, technical performance, and sustainability for green construction to satisfy the wide range of needs for successful facade design. In this course, we will explore what sintered stone is and how its unique characteristics are quickly making it a very popular choice for all types of buildings, particularly those that are green and sustainable.
What is Sintered Stone?
Sintering is a well-known method for creating objects from powders, including mineral, metal, and ceramic powders. As such, sintering has been traditionally used for manufacturing ceramic objects, but there are common applications found across many industrial fields. The study of sintering and of powder-related processes is known as powder metallurgy and is well established. It is basically the process of using natural materials in powder form and processing them, usually under heat, pressure, or both, to create a desired product.
Looking more closely, sintering is based on atomic diffusion of particles, which occurs most quickly at higher temperatures. The atoms in powder particles diffuse across the boundaries of the particles, fusing them together and creating one solid piece. A simple observable example of sintering can be seen when ice cubes in a glass of water adhere to each other. The edges of the ice cubes, although not powder, can become irregular in the relatively warmer water surrounding it. The water atoms in each of the adjacent ice cubes react and bond together, creating one combined mass, even though they were originally separate.
Applying this same process to sintering stone produces a thin, lightweight, and very strong material with properties similar to but more advanced than porcelain ceramic tile. The difference is that sintered stone products are made from selected natural minerals with minimal amounts of water. This combination of powdered minerals densifies first under pressure and then becomes nonporous during firing at temperatures below the melting point of the minerals. The powder particles thus bond together due to the applied pressure and heat, which force all surfaces of the particles to be directly connected to all of the surfaces of the adjacent particles, initiating the atomic sintering to create one mass with a very dense and strong end result.
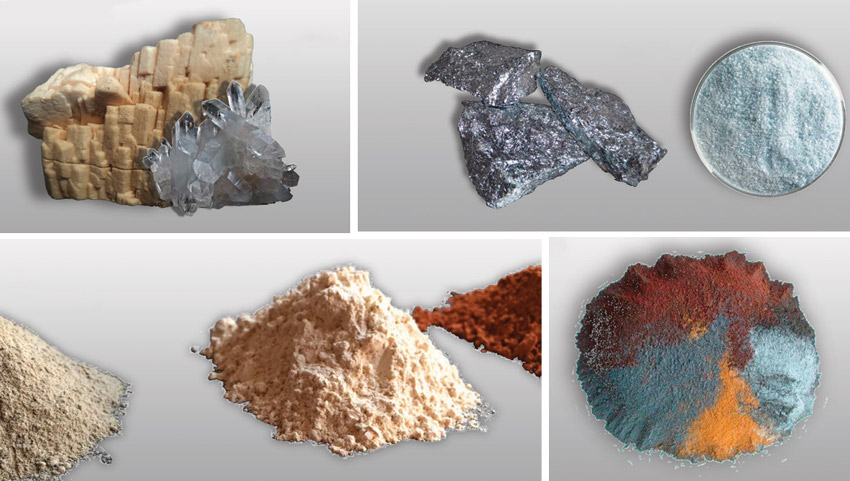
Sintered stone is made of all natural ingredients, including granite materials (quartz and feldspar) for hardness and strength, silica and glass minerals for chemical stability, clay minerals for adhesive properties and whiteness, and natural pigments for chromatic properties.
Manufacturing Sintered Stone
Regardless of how sintered stone is ultimately used, the basic manufacturing process is the same. There are some variations, of course, to produce slightly different end products, but they all start with raw materials, move to a pressing process, are fired in a kiln, and then are put through final product fabrication. We will look closer at these four steps in the following sections.
Raw Materials
Sintered stone typically requires a combination of different materials mined or sourced from different locations. Four specific groups of natural materials are selected based on their ability to provide certain desired characteristics. First are granite minerals such as quartz and feldspars, which are used to provide hardness and strength. Second are silica and glass minerals, which add chemical stability. Third are clay minerals, which contribute adhesive properties and whiteness. Fourth, in order to create different colors or chromatic properties in the final product, natural mineral pigments of different types can be used. Once all of these ingredients are located and mined, they are transported to the manufacturing facility where they are separated and stored until ready for processing. Since these are all natural materials, they can contribute to a green and sustainable design in the context of environmentally responsible mining practices.
Pressing Process
With the raw materials ready and stored at the manufacturing plant, the first step is to process them so they are all reduced to fine powders. These powders are then measured out and mixed into a form until they are evenly distributed to an engineered thickness. The colors and patterns of the sintered stone are directly determined in this mixing and placing of the powdered minerals. Up until this point, everything has been a dry process, but now a very small, predetermined amount of water is added, creating what is referred to as the compact. The mixture is then pressed using a pressing process requiring up to 15,000 psi to properly densify the compact into an unfired slab. Once pressed, it can be further decorated or colored to suit specific design requirements.
Firing
When the unfired slab is ready, it is moved into a large kiln and fired at temperatures below the melting point of the minerals at normal atmospheric pressure. Due to the normal vitrification effects of firing, some limited shrinkage may occur in the slab. Nonetheless, this is the point where the sintering takes place, allowing the material to bond atomically and become nonporous. Note that there is no extrusion involved as is common in other materials. Instead, the pressing plus the kiln heating produce strong, thin slabs on the order of ⅛ inch, ¼ inch, ½ inch, or even ¾ inch when finished. The actual thickness plus the overall face size of the final sintered slab can vary by manufacturer, particularly since many provide metric sizes due to their location in countries that rely on metric measurements. At least one manufacturer, however, offers non-metric sizes in 4-by-12-foot and 5-by-10-foot panels, among others, to match American construction sizes. Once fired, the raw slab will be processed as needed at the factory to cut it to its final size or sizes and smooth the edges. It is then ready for shipping and any final field fabrication.
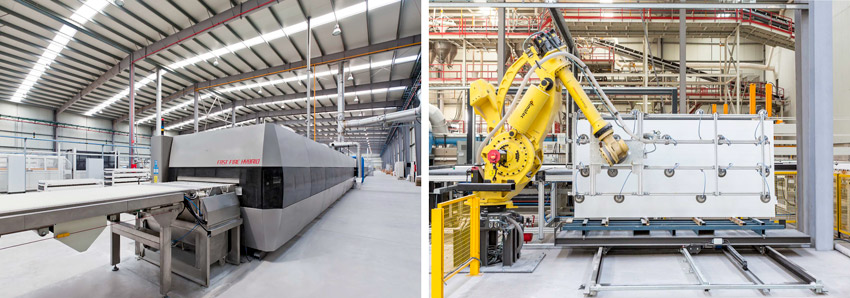
Sophisticated, state-of-the-art equipment is employed to create sintered stone as a strong, durable engineered product.
It should be noted that handling large sintered stone panels is not much different than handling large glass panels, although the sintered products are stronger. Nonetheless, even with the high flexural strength found in sintered stone, handling should always be done using appropriate equipment. That includes metal frames with mechanical suction cups to support and move the panels safely just like moving glass or stone panels. Handling sintered stone tiles should be treated the same as handling porcelain tiles.
Sintered Stone Properties
Sintered stone panels and tiles provide a high-performance product with superior physical properties that can collectively be described as making them virtually ageless in exposed outdoor applications such as building facades. Some notable properties are listed as follows:
- Thickness options: While ¼-inch-thick (6-millimeter-thick) sintered stone is the most common use for building facades, it is also available in ⅛-inch-thick (3-millimeter-thick) panels, which may be suitable for directly adhering over existing facades. For situations where a thicker panel is needed, it is also available in ½-inch (12-millimeter) and ¾-inch (20-millimeter) thicknesses.
- Size options: As noted, some European manufacturers of sintered stone panels provide only metric sizes. However, it is now possible to find at least one manufacturer that makes panels available in 4-by-12-feet or 5-by-10-feet sizes. These panels can be reduced to virtually any width or length at the factory to suit the modular needs of a particular design. It is even possible to consider some cut shapes beyond squares and rectangles.
- Lightweight: Panels that are ¼ inch thick weigh less than 3 pounds per square foot, while panels that are ⅛ inch thick weigh only 1.1 pounds per square foot.
- Scratch and abrasion resistance: As a dense material, it is scratch and abrasion resistant and quite capable of withstanding even extreme abuse. Sintered stone measures 7.8 on the Mohs Hardness Scale, classifying it as vandal resistant.
- Porosity: The very low porosity of sintered stone (less than 0.08 percent) produces several desirable effects. It is virtually waterproof, meaning no extra sealers are required on the outside surface and graffiti doesn’t penetrate, making it easy to remove. Very low porosity and high density also means exposure to freeze-thaw cycles is not a problem.
- Fire resistance: The all-mineral composition of sintered stone products mean they do not burn in contact with fire nor produce smoke or toxic substances.
- UV resistance: Since the color is 100 percent natural, sintered stone doesn’t deteriorate when exposed to the ultraviolet (UV) rays of the sun, meaning the color and integrity of the surface will not degrade.
- Photocatalytic coating: Recent product developments have produced a coating that is used on sintered stone facades that can combat air pollution by converting nitrous oxides (NOx) to much more harmless substances, such as oxygen and nitrates.
- Easy to clean and self-cleaning: The dense, smooth surface of sintered stone makes it easy to clean all by itself, particularly since it is not affected by chemical cleaning agents. However, by adding a nanotech-based coating, it takes on properties of superhydrophilicity, which allows rainwater to completely spread across the surface and provide self-cleaning facades.
- Environmentally friendly: Sintered stone is made from 100 percent natural materials, meaning it is free of resins, VOCs, and other potentially harmful substances. It is also recycling friendly with up to 52 percent recycled content possible and 100 percent available to be recycled at the end of its service life. An option for an additional treatment also allows the material to actually absorb and break down airborne contaminants, thus directly reducing air pollution.
All of these design attributes have helped to promote its use not only on exterior walls but also in interiors for floor and wall surfaces. The material has even been shown to be hygienic and suitable for food contact, which has also led to its use for countertops and food handling surfaces.
Design Options
From a building design standpoint, the surface of sintered stone can provide the look of natural stone, including replicating natural marble, granite, limestone, or travertine in an array of colors and patterns. It is even possible to specify book-matched or end-matched patterns. It can also emulate other desirable exterior appearances, such as wood in a variety of species and finish colors, tile in a variety of solid or patterned colors, and other materials.
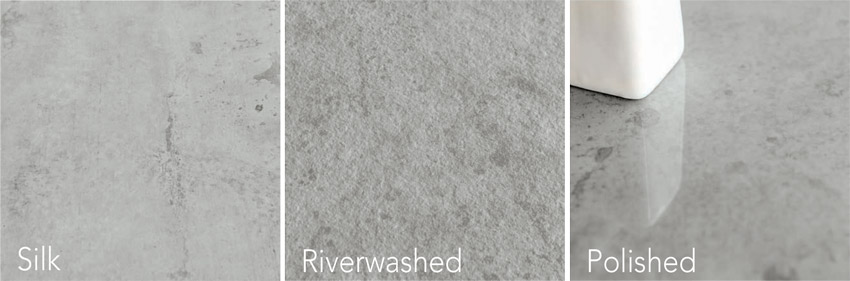
Sintered stone is available in a variety of appearances to simulate stone, wood, and other materials. It is also available in textures of matte or silk finish, a river washed, rougher effect, or highly polished.
Different surface textures are also available to enhance the material appearance or performance characteristics of the facade panels. Such textures include a natural honed surface, a smooth but non-glossy satin/ silk finish, or a more textured river-washed type of finish. For designs calling for a high gloss, a glazed polish surface is available and even a higher smoothness using a nanotech mechanical polish. Combining any of these texture options with the simulated material and color choices can produce stunning facades that are lighter and easier to install than more traditional stone, wood, and other materials.
With all of these high-performance and desirable design characteristics, it is easy to have the misconception that using sintered stone surfaces for a building exterior is expensive. In fact, it is not. It has been proven repeatedly as being very cost neutral when looking at first costs and comparing it to many commodity facade products, including aluminum composite paneling. When considering it over the life of the building and factoring in its anti-graffiti, impact-resistant, and weather-resistant properties, it readily lends itself to being an everyday common-sense solution for many architects and designers. Building owners are also quick to realize its long-term cost saving benefits too when they see that it is completely vandalism proof (scratch, paint/ink, impact) and virtually maintenance free for the life of the building.