Dramatic, Durable Interiors Using Sintered Stone
Learning Objectives:
- Identify the characteristics and beneficial properties of sintered compact surfaces for building interiors.
- Investigate the manufacturing process of sintered compact surfaces and the ability of the product to provide beauty and durability to interior building applications.
- Assess the functional contributions of sintered stone as it contributes to green and sustainable building design.
- Specify sintered stone in a variety of green and conventional buildings, including proper installation techniques for thinset applications.
Credits:
Sintered stone is a new product category for interior surfaces that is becoming more popular in the United States and Canada due to several very appealing characteristics. To begin with, it is available in a wide range of standard or custom appearances and colors that allow it to look like natural stone, wood grain, or uniformly finished panels, among others. Unlike using the materials it may look like, though, sintered stone provides superior hardness and durability, making it very well suited for commercial and institutional building areas subject to heavy use. In terms of cost effectiveness, sintered stone panels are typically available in large-format sizes, requiring less labor and allowing for shorter installation times. In addition, they are readily installed using known site cutting and handling techniques for large-format tile coupled with common thinset application processes. Altogether, these products are becoming a preferred choice for many wall, floor, and other interior surfaces in commercial, residential, and institutional buildings of all types.
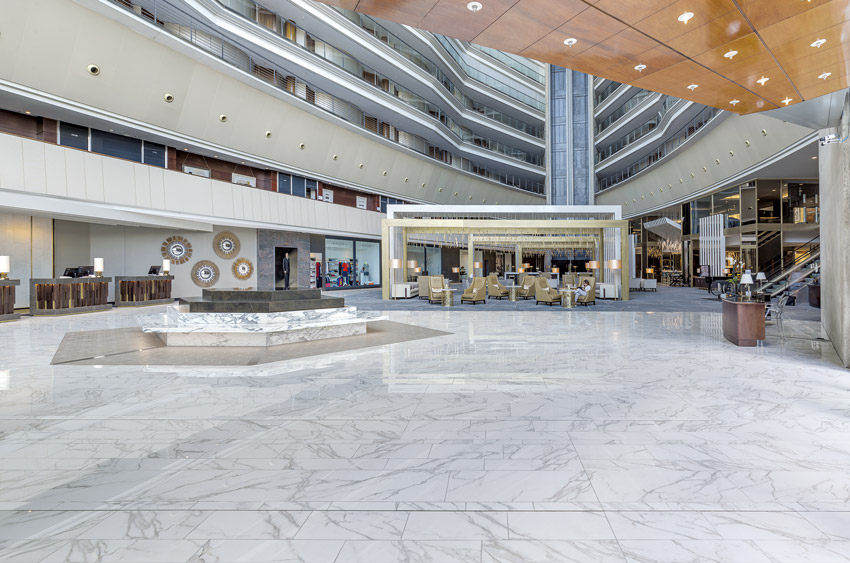
All images courtesy of Neolith, a division of TheSize Surfaces SL
Sintered stone is a new product that is being used increasingly more often for interior floors, walls, and other surfaces because of its extensive design options and extremely strong performance characteristics.
What is Sintered Stone?
Sintering is a manufacturing process that has been around for a long time. It is a method to create objects from powders, including mineral, metal, and ceramic powders. As such, sintering has been traditionally used for manufacturing ceramic objects, but there are common applications found across many industrial fields. It is basically the process of using natural materials in powder form and processing them, usually under heat, pressure, or both, to create a desired product. In the case of sintered stone for building products, stone and other natural materials are ground to a powder and subjected to specific heat and pressure to produce the desired end results.
Looking more closely, sintering is based on atomic diffusion of particles that occurs most quickly at higher temperatures. The atoms in powder particles diffuse across the boundaries of the particles, fusing them together and creating one solid piece. A simple observable example of sintering can be seen when ice cubes in a glass of water adhere to each other. The edges of the ice cubes, although not powder, can become irregular in the relatively warmer water surrounding it. The water atoms in each of the adjacent ice cubes react and bond together, even though they were originally separate. The same thing happens in stone and other powders when they are sintered together atomically.
Applying this process to create thin, lightweight, and very strong sintered stone panels may lead some people to mistakenly think that the finished result is the same as porcelain ceramic tile. However, there are real differences that become evident just by comparing the characteristics. While traditional ceramics might have one characteristic in common with sintered stone, no single ceramic product possesses all of the characteristics, including stain, scratch, chemical, and heat resistance, that sintered stone does. These characteristics come about in part because sintered products are made from selected natural minerals that are different than those to make tile. The combination of powdered minerals with a minimal amount of water is referred to as the compact, which densifies first under pressure and then becomes nonporous during firing at temperatures just below the melting point of the minerals. The powder particles thus sinter and bond together due to the applied pressure and heat, which force all surfaces of the particles to be directly connected to all of the surfaces of the adjacent particles, creating a very dense and strong end result. Due to its all-mineral composition, sintered stone has high heat and fire resistance, while its density makes it virtually waterproof—it has a porosity less than 0.09 percent, meaning no sealers are required.
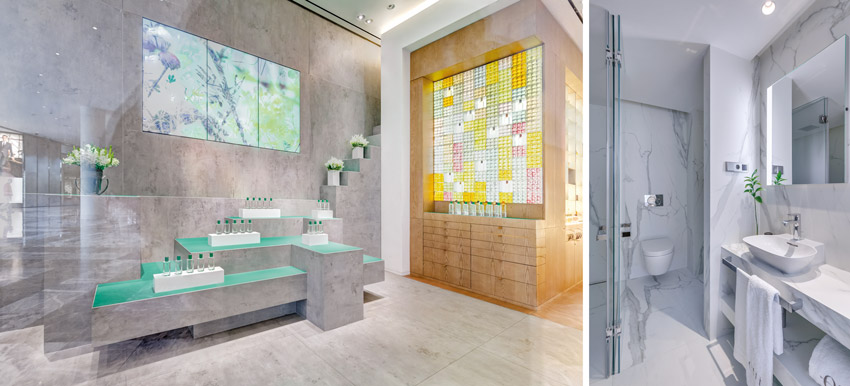
Sintered stone panels are available in a wide variety of colors, finishes, and textures to suit a variety of room and building types.
From a design standpoint, the surface of sintered stone can provide the look of stone, tile, wood, smooth, or textured surfaces in a variety of colors and hues. However, it is lighter in weight than many other materials, coming in at only 1.1 to 1.5 pounds per square foot for a 1/8-inch-thick panel. For those who maintain the building, they find the dense, nonporous surface easy to clean, including the removal of graffiti so the appearance and color are maintained over time. Even harsh chemicals aren’t a problem to use since sintered stone is chemical resistant. The material has even been shown to be hygienic and suitable for food contact, which has also led to its use for countertops and food-handling surfaces. All of these design attributes have helped to promote its use not only on interior walls and floors but also on building exteriors.
With all of these high-performance and desirable characteristics, it is easy to have the misconception that using sintered stone for a building surface is expensive. In fact, it has been proven repeatedly as being very cost neutral when looking at first costs and comparing it to many other commodity interior finish products. When considering it over the life of the building and factoring in its anti-graffiti, impact-resistant, and wear-resistant agelessness, it readily lends itself to being an everyday common-sense solution for many architects and designers. Building owners are quick to see its long-term cost saving benefits too when they realize that it is completely vandalism proof (scratch, paint/ink, impact) and virtually maintenance free for the life of the building.