Next-Level Glass Performance and Sustainability
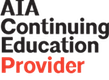
Learning Objectives:
- Identify and recognize the ways that high-performance glass and glazing products address operational carbon emissions by reducing energy use in existing and new buildings.
- Examine relevant building codes, standards, and regulations and how they are driving performance improvements in facade systems.
- Discuss best practices for using Environmental Product Declarations, or EPDs, for glass.
- Recognize existing glass product solutions that provide next-generation performance.
This course is part of the Glass and Glazing Design Academy
Glass Recycling Opportunities and Challenges
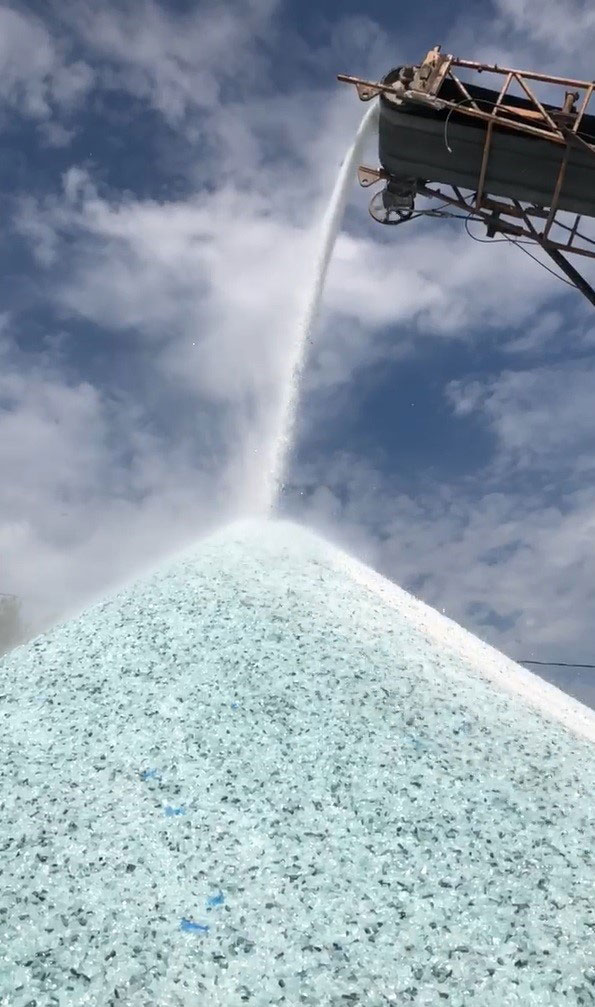
Photo courtesy of NGA
From recycling back into the melt furnace, recycled glass materials can be used in various industries to make new windows, glass containers, road grade, fiberglass, reflective highway paint, landscaping products, countertops, and coastal restoration materials.
Higher recycled material content is a key element for future decarbonization efforts for the glass industry. Glass can be infinitely recycled in flat glass and bottling operations, so continued reuse further supports the glass industry, supports a circular economy, and reduces waste and landfills. These benefits drive material choice decisions, such as using glass containers instead of less recyclable materials such as single-use plastics.
Glass recycled materials can be used in various industries, from recycling back into the melt furnace to make new windows, glass containers, road grade, fiberglass, reflective highway paint, landscaping products, countertops and coastal restoration materials.
Recycled glass is valuable. Recycled glass, or cullet, helps reduce the energy and emission burdens on glass manufacturing by:
- Reducing the need for raw material mining.
- Reducing trucking and related emissions, as making 1,000 tons of glass requires 1,000 tons of cullet or about 1,200 tons of raw material, or “batch.”
- Reducing furnace emissions. Batch material and firing fuels are both off-gas during the glass-making process. Increased cullet usage significantly reduces the emissions from production.
- Reducing gas usage. Cullet is easier to melt than batch, so lower furnace fuel is required.
- Reducing the global warming potential of glass, as less energy is needed to make glass when cullet is available.
Recycling glass supports domestic supply and workforce.
- Cullet should be considered a viable, reusable and sustainable domestic material supply chain.
- The glass recycling industry creates jobs and tax benefits.
Glass recycling is challenging.
- Economics and glass quality requirements present challenges for glass recycling.
- Freight costs typically drive recycling decisions. Long hauls of heavy products often make recycling a cost challenge.
- Sorting and cleaning of cullet for certain applications can be expensive. In contrast, landfill costs are generally inexpensive in the United States.
- Contamination from even trace amounts of certain elements like nickel and aluminum can dramatically impact glass quality.
Solutions in Glass
This section presents a range of next-level performance technologies available from the glass industry, including improved IGUs, VIG, and thin-glass solutions. Additionally, it looks at dynamic glass, which provides solutions for solar control, and at BIPV, which can provide on-site energy generation.
Advanced IGUs
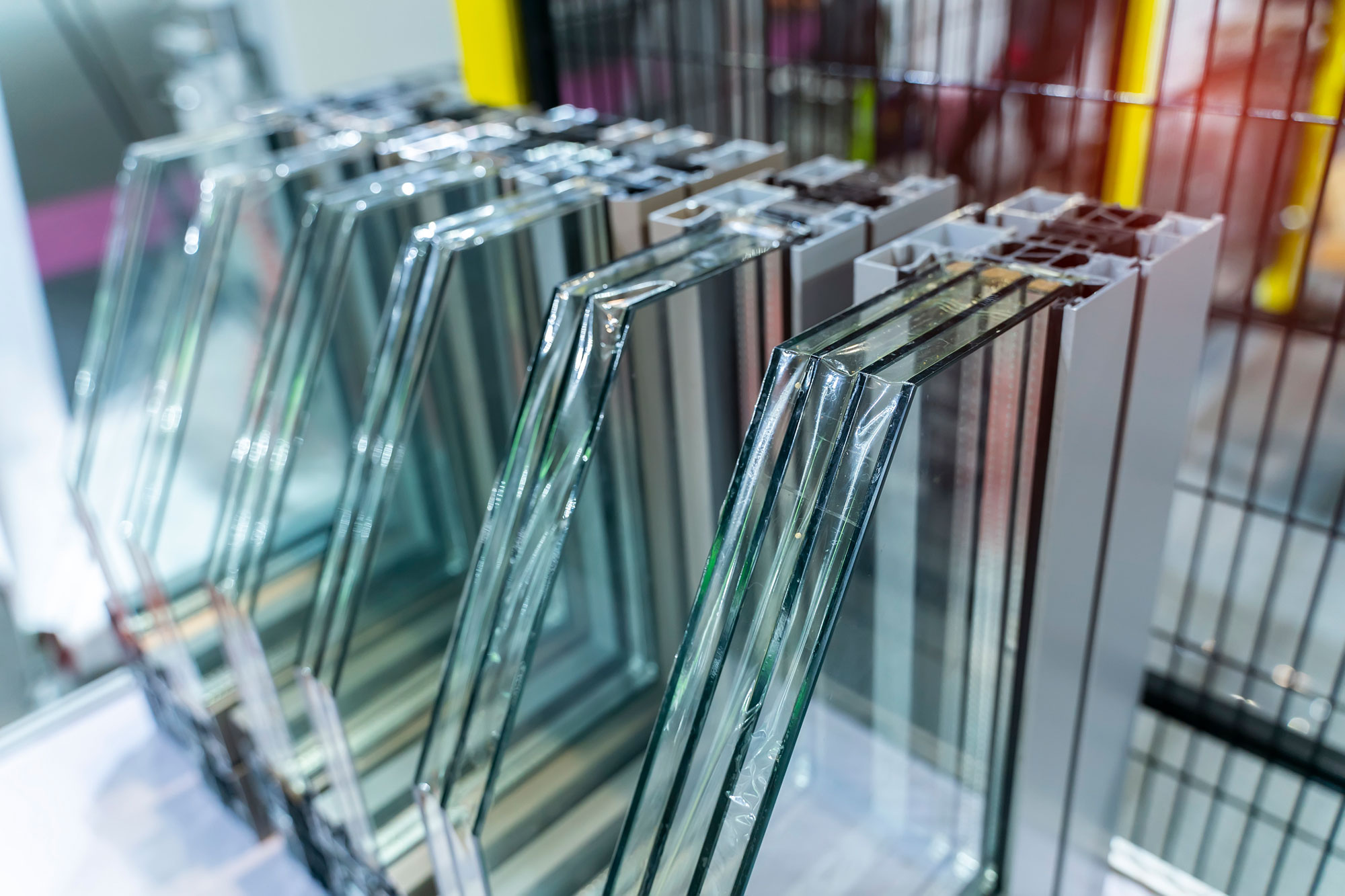
Photo courtesy of NGA
Advanced IGUs offer additional performance improvements through a variety of methods, including filling the air space with gas, using warm-edge or other higher thermal performance spacers, or adding additional lites.
Basics: Widely used in commercial and residential construction since the 1960s, IGUs consist of two or more lites of glass separated by a hermetically sealed air space to provide more thermal, sound, and solar insulation than possible with single-glazed fenestration. Advanced IGUs offer additional performance improvements through a variety of methods, including filling the air space with gas (argon, or, for even better performance, krypton), using warm-edge or other higher thermal performance spacers, or adding additional lites (and thus additional cavities) to the unit. For better solar control, low-e coatings can be added to the No. 2 surface, and now, thanks to advancements in coatings, the No. 4 surface, of a traditional double-glazed unit.
Performance: Highly insulating glazing solutions—doubles with improved spacers and two low-e coatings, or multi-cavity units—will likely be required to meet the more stringent energy codes and standards mentioned in the previous section, says Culp. The U-factor requirements in the New York and Massachusetts stretch codes, for example, will push for “triple glazing or fourth-surface low-e, with gas fill and better frames,” he says.
The updated Energy Star requirements will also pose challenges. In the previous version, about 80% of the residential window market met the 0.27 center of glass U-factor requirement for the Northern climate. Energy Star 7.0 moves that number to a U-factor of 0.22. Only the very best-performing double-glazed units currently on the market would be able to meet the new requirements, Selkowitz says. “For the first time in 20 or 25 years, we’re having to take a hard look at that standard double-glazed, argon-filled, low-e unit.”
History: The double-glazed IGU was patented in the U.S. in 1865 by Thomas Stetson and was commercialized in the 1930s. According to estimates from Ducker Worldwide, IGUs accounted for about 12% of the U.S. market share of new residential glazing in 1970, and quickly grew to about 70% by 1980. By 1990, nearly all new windows sold into the residential market were insulating.
The popularity of improved IGUs with low-e coatings accelerated quickly in recent decades, and the product now accounts for about 80% of the market, according to Ducker. However, multi-cavity IGUs represent only a slim market share for residential glazing at about 3%.
IGUs with emerging technologies—such as VIG, suspended film or Aerogel—remain more niche performance solutions.
Development: The global IG window market is projected to reach U.S. $17.2 billion by 2026, growing at a compound annual growth rate of 6.1% from 2021 to 2026, according to ResearchAndMarkets.com. The growing trend of green rating systems in various countries is likely to contribute to the growth of the IG window market, with North America projected to be the largest regional market.
The insulating market has also become more complex with the addition of several emerging IG technologies that offer a step change in thermal performance. Such technologies include VIG and thin-glass multi-cavity IGUs, which are both explored in-depth later in this article. Other technologies include IGUs with a suspended film, which has been available on the market for several decades, or units with Aerogel in the cavity, which is currently available but only in a translucent state.
Challenges: The North American IG market has faced challenges moving beyond traditional double-glazed units. Traditional multi-cavity IGUs, while popular in Europe, have gained only minimal traction in the U.S. “There are obstacles to triple pane. Many manufacturers say it is too heavy, too wide, too expensive. It has long ROIs,” says Selkowitz.
The industry is also facing new challenges with krypton gas-filled insulating units. Krypton has gained popularity in recent years as a higher-performing gas option for IGUs. However, the cost of krypton has increased due to higher demand for krypton in the communication sector and due to new difficulties in accessing krypton, which is sourced in large part from Ukraine and Eastern Europe, says Selkowitz.
Resources: The NGA published the Performance Improvements in IGUs glass technical paper in 2016 and updated it in 2022. Resources: The NGA published the Performance Improvements in IGUs glass technical paper in 2016 and updated it in 2022. Download the resource.
Additionally, watch a webinar from Selkowitz discussing the latest IGU technologies—and the research and development still in progress—that will aid in the reduction of a building’s carbon footprint and bring us closer to the goal of a net-zero energy building.