Next-Level Glass Performance and Sustainability
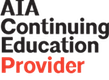
Learning Objectives:
- Identify and recognize the ways that high-performance glass and glazing products address operational carbon emissions by reducing energy use in existing and new buildings.
- Examine relevant building codes, standards, and regulations and how they are driving performance improvements in facade systems.
- Discuss best practices for using Environmental Product Declarations, or EPDs, for glass.
- Recognize existing glass product solutions that provide next-generation performance.
This course is part of the Glass and Glazing Design Academy
State Stretch Codes
States such as New York and Massachusetts, have adopted or are nearing adoption of new stretch energy codes that set more stringent thermal performance requirements than the national energy codes, says Culp. While the stretch codes initially start as voluntary standards, they become mandatory when adopted by the local jurisdiction, including significant cities such as New York City and Boston. The stretch codes “are very aggressive,” says Culp. Where adopted, the codes will require that new buildings include the highest-performing glass units, including the use of new products such as vacuum glazing as well as triple-pane assemblies.
Inflation Reduction Act
The Inflation Reduction Act of 2022 included numerous provisions that will drive performance improvements in buildings. According to Culp, the IRA includes $1 billion in state and local government grants intended to accelerate the adoption of the latest energy codes and a zero-energy code. The IRA also expands tax deductions for energy-efficiency improvements in commercial buildings and includes tax incentives for high-performance building products. Two notable inclusions include sizable tax credits for electrochromic glass and for PV and BIPV.
Payback of High-Performance Windows and Retrofits
The following is based on the NGA document, High-Performance Windows Can Help Save the World.
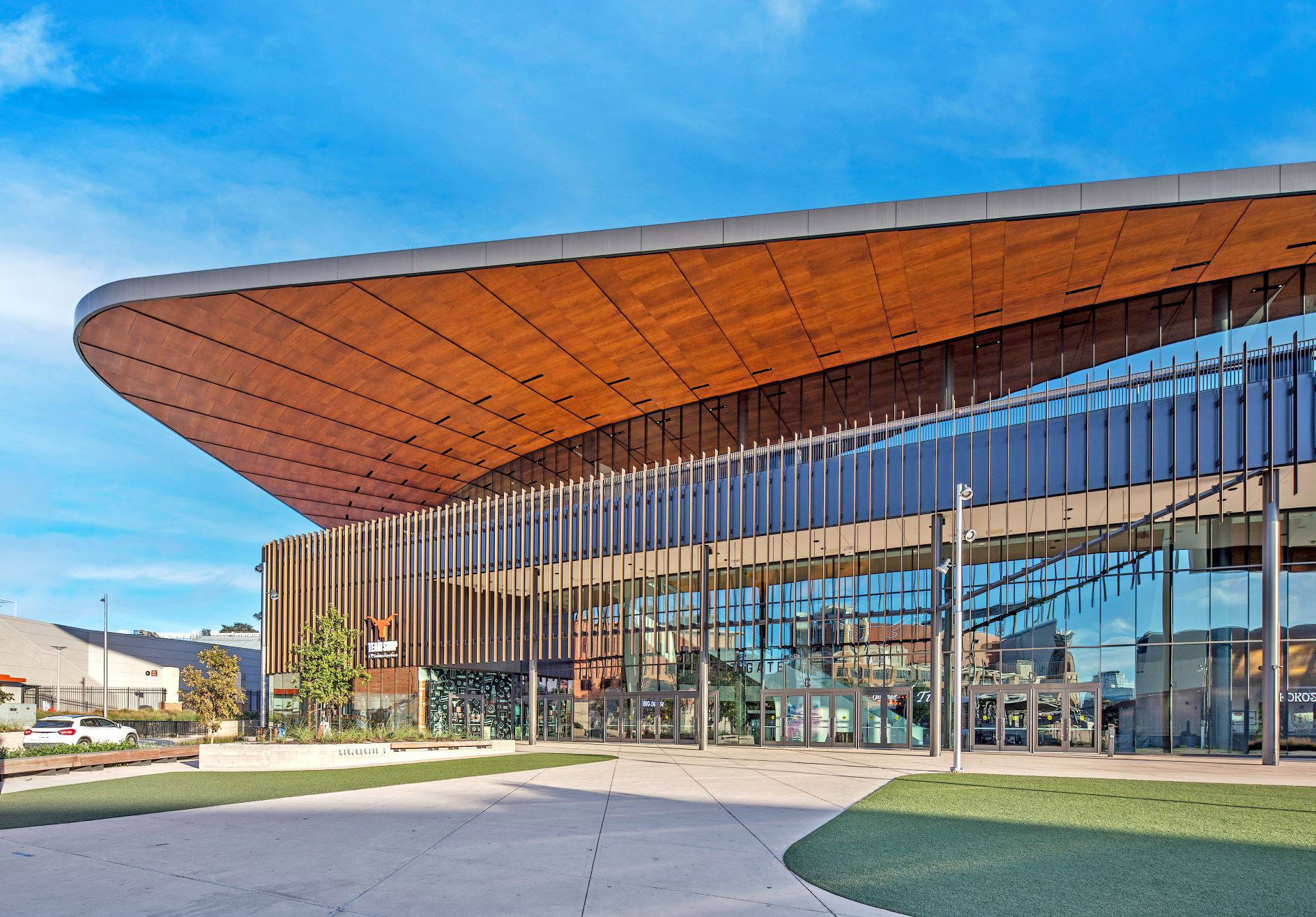
Photo courtesy of Tom Kessler
The Moody Center on the University of Texas at Austin campus boasts a sweeping 360-degree curtainwall design featuring Low-E glass.
Higher-performing facades mean higher-performing buildings, resulting in improvements in operational carbon. Some considerations about retrofits, the payback of high-performance systems, and building resiliency:
Window Retrofit is Key to Decarbonization
Residential and commercial buildings are responsible for almost 40% of North America’s carbon dioxide emissions and energy usage. For example, existing buildings with inefficient windows account for about 70% of New York City emissions. Additionally, 80% of buildings that will exist in 2050 already exist today, meaning retrofits will be critical to improving operational carbon on a large scale in decades to come.
High-performance windows are up to 80% more efficient than standard windows. New residential windows that qualify for the Energy Star Most Efficient designation are up to 40% more efficient than new standard windows. Upgrades in window technology in the last 20 years have significantly improved heat-loss performance for residential and commercial structures.
New windows can pay back embodied carbon in less than a year. Glass is typically 2% to 5% of a building project’s embodied carbon. Upgrading to a more efficient glazing system will initially add some additional embodied carbon. However, in both commercial and residential installations, operational energy/carbon savings from the more efficient windows will offset that initial increase in six to 20 months in a cold climate, and thereafter, provide additional annual carbon savings.
Decarbonization efforts should include both embodied and operational carbon. Existing legislation targeting embodied carbon does consider the long-term benefits that glazing materials provide by mitigating annual carbon impacts through ongoing operational cost savings. Upgrading installed windows improves total building energy performance by up to 20%, improves comfort and health for occupants, and reduces operational costs and carbon emissions.
High-performance glass is used in on-site renewable energy products. High-performance glass is a key component in the domestic supply of solar panels and BIPV. Increased use of on-site renewable energy is critical to achieving net-zero energy and carbon targets, and will also help improve grid resiliency and U.S. energy independence.
High-performance windows improve building resiliency. In the event of extended power disruption, high-performance windows enhance building resiliency and maintain habitable interior temperatures for longer periods of time. Improvements allow for the downsizing of replacement mechanical systems and more effective use of funding while increasing building resiliency in extreme weather and blackouts.
Retrofitting buildings with high-performance windows creates job opportunities for a skilled workforce. The installation of high-performance window products supports the creation of skilled workers’ jobs along with urban renewal. At the local level, changes in building performance standards requiring improvements in existing buildings are taking off, but adoption among cities is scattered. Federal-level initiatives encouraging window and building envelope upgrades, as well as lighting and mechanical system updates, would create additional manufacturing demand and related jobs.
Glass EPDs and Caution Over Comparison
The following is based on the NGA Glass Technical Paper, General EPD Education.
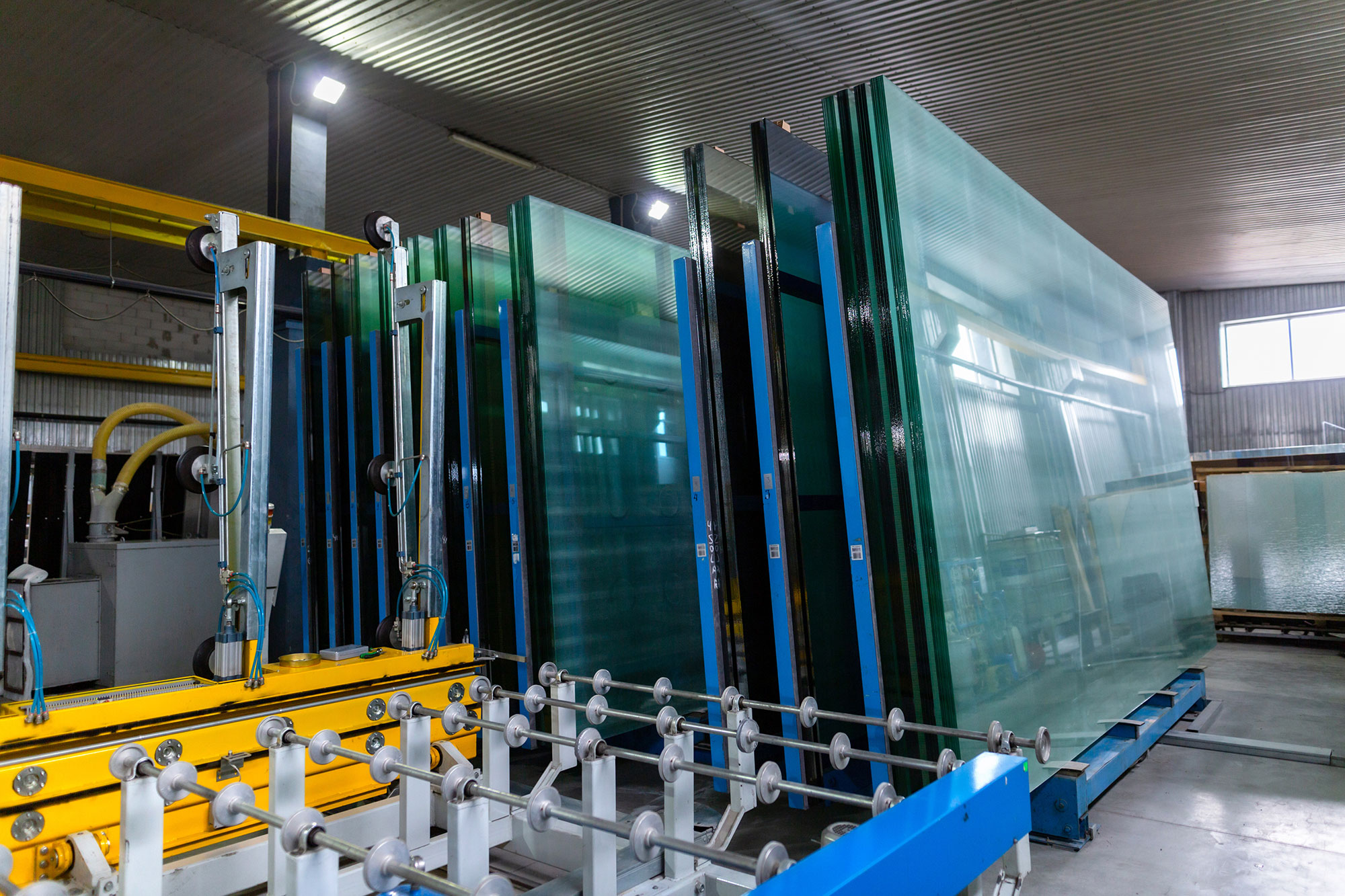
Photo courtesy of NGA
Glass is typically 2% to 5% of a building project’s embodied carbon. Upgrading to a more efficient glazing system will initially add some additional embodied carbon.
Environmental Product Declarations enable the assessment of the environmental impact of products and label them accordingly. They contain extensive and independently verified environmental data about a product, from raw material procurement to disposal. EPDs allow consumers or design professionals in the building and construction industry to make better-informed decisions about the environmental impacts of the building material products chosen for projects.
However, it has been observed in the marketplace that architectural, engineering and construction professionals are trying to compare EPD values, which is not encouraged, nor always appropriate, and could lead to misleading conclusions.
Flat Glass EPD
It is important to understand how to properly read, interpret, and utilize the data published in the industry-average Flat Glass EPD, developed by the NGA. This is especially critical when attempting to compare this data to manufacturer-specific flat glass EPDs, as well as the EPDs of other materials and systems.
NGA and its member companies created the industry-average Flat Glass EPD to better understand their glass products’ environmental performance from cradle-to-gate. The NGA EPD conforms to the NGA Product Category Rule, or PCR, for Flat Glass, which was published by NSF in September 2020 and describes the format and requirements for conducting lifecycle assessments and creating EPDs for flat glass products. The Flat Glass PCR requires that EPDs include the following disclaimer advising against comparisons:
“This EPD was not written to support comparative assertions. Even for similar products, differences in declared unit, use and end-of-life stage assumptions, and data quality may produce incomparable results. It is not recommended to compare EPDs with another organization, as there may be differences in methodology, assumptions, allocation methods, data quality such as variability in data sets, and results of variability in assessment software tools used.”
Caution Against Comparison
In general, EPDs may be used to inform and comply with the requirements of green building rating systems and legislative actions. The purpose of an EPD is to provide information on several environmental impacts of a product over the lifecycle, either cradle-to-gate or cradle-to-grave.
EPDs typically rely on estimations of impacts, therefore the accuracy will differ for any particular product line and reported impact. EPDs are not meant to be comparative assertions and may not be comparable or have limited comparability. According to clause 5.5 of ISO 21930:2017: “Comparison of construction products using an EPD shall be carried out in the context of the construction works. Consequently, comparison of the environmental performance of construction products using the EPD shall consider all the relevant information modules over the full lifecycle of the products within the construction works.”
This is reinforced in “Critical Issues When Comparing Whole Building & Building Product Environmental Performance” from the MIT Concrete Sustainability Hub: “Only compare building products in the context of a whole building. With regards to building products, unless the thermal properties, such as thermal conductance and thermal diffusivity, and envelope permeability are exactly the same, use of the products under comparison would cause different operational energy consumption.”
LEED V4.1
In acknowledgment of the challenges associated with comparing EPDs, LEED v4.1, option 2, attempts to address this by limiting comparisons to be made using an individual product EPD and demonstrating measurable improvements in different versions of that EPD. This is in contrast to LEED v4.0, which compared an EPD to an industry-average EPD. LEED v4.1 states: “To encourage the use of products and materials for which lifecycle information is available and that have environmentally, economically, and socially preferable lifecycle impacts. To reward project teams for selecting products from manufacturers who have verified improved environmental lifecycle impacts.”
Critical Characteristics
EPDs are developed, particularly those per ISO 14025, with critical characteristics unique to that published document. Extreme caution should be used when comparing EPDs and the resulting global warming potentials. Significant differences may exist in some attributes, even for similar products. Comparing EPD values with differences in the characteristics below can yield large errors between the values and should be considered. When comparing EPDs, at a minimum, ensure the following are identical:
- The same Product Category Rule is used
- Declared unit (comparison of EPD results on a mass basis is insufficient; the technical performance of the product should be considered)
- System boundary (use and end-of-life stage assumptions)
- Data quality, such as variability in data sets and broad error margins in data
- EPD methodology and assumptions
- Allocation methods
- Variability in assessment software tools used
- Program manager (program operator)
- Data sources (GABI version, for example) on which assumptions are based
- Manufacturer-specific versus industry-wide
- Facility-specific versus multiple facilities
- Suppliers/supply chain
- Age of the EPD