Green Building Certification
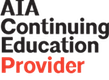
Learning Objectives:
- Summarize the goals of the Living Building Challenge (LBC), its structure, and the requirements for certification.
- Identify typical regulatory and economic hurdles to LBC certification.
- Explain the strategies employed by the featured projects to meet LBC requirements for energy, water, and materials.
- Explain concepts relating to LBC, such as “scale jumping.”
This course is part of the Biophilia Academy
Ingenuity was also needed to meet LBC’s net-positive-energy mandate. Despite energy-saving features such as air-source heat pumps, radiant heating and cooling, heat recovery, and best-in-class lighting, the PAE Building’s power demand will exceed the capacity of the PVs that will fit on the roof. In addition, the location in a dense urban environment and in a historic district meant that designers could not extend the area for mounting PVs with roof overhangs. To meet demand, the team took advantage of what LBC refers to as “scale jumping,” a concept introduced with Version 1.3 of the certification system, released in 2008. In certain circumstances, it allows projects to go outside their site boundaries in order to satisfy some imperatives. In this case, the developers will install a 130kW PV array on the PAE Building, and have donated a 207kW one for Renaissance Commons, an affordable-housing project in another part of the city. “The arrangement is a win-win,” says Marc Brune, PAE principal. “They get the power, and we get the renewable-energy credits.”
Despite the hurdles, LBC is not only gaining momentum for privately developed projects, but also with public projects in forward-looking cities. One such building pursuing Living certification is a recently completed 50,000-square-foot addition to the Art Deco city hall of Santa Monica, California. Designed by Frederick Fisher and Partners (FF&P), the three-story glass-clad annex consolidates office space that city agencies had previously been renting elsewhere in Santa Monica. LBC is a particularly good fit for the beachfront city, given its environmental goals, which include carbon neutrality by 2050, zero waste by 2030, and a target for water self-sufficiency that is shockingly close—2023, when it plans to stop importing water and rely only on groundwater.
With the aim of staying within a water budget that could be met with the 141⁄2 inches of rain that fall in Santa Monica in a typical year, the $60.8 million project relies on three separate strategies. It has foam-based composting toilets; a system that captures graywater and condensate from the cooling system’s air-handling units for irrigation; and a rainwater-to-potable-water system that collects rainfall from the roof, storing it in a 40,000-gallon cistern. The city hall addition will be the first public building in California in which rainwater comes out of the drinking fountains, according to Joseph Coriaty, FF&P managing partner. The permitting process was involved, he says, since there were few precedents for these systems, and agreement on their design was needed from city, county, and state agencies.
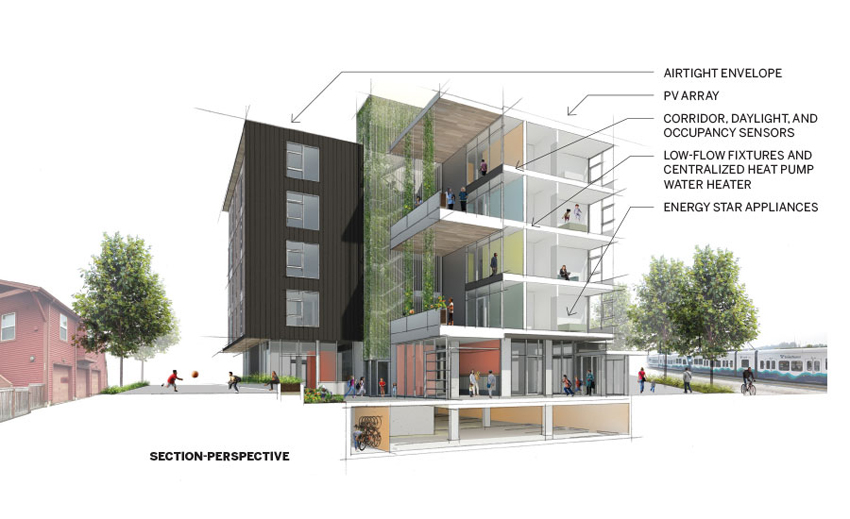
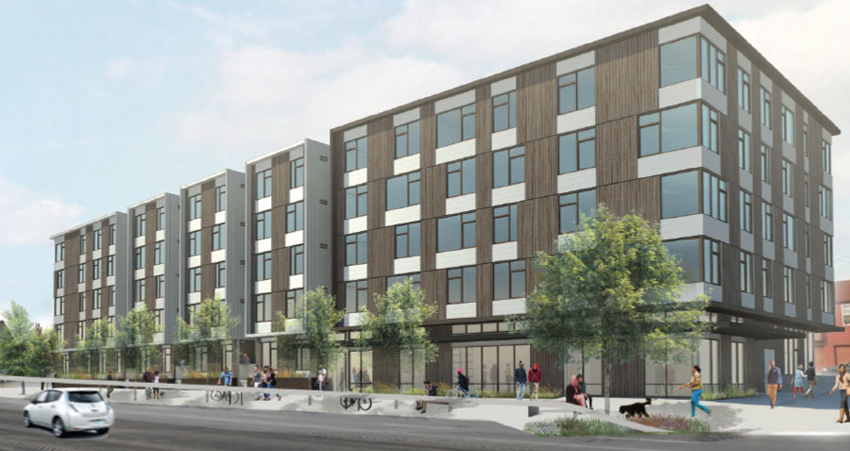
IMAGES: COURTESY SUNDBERG KENNEDY LY-AU YOUNG ARCHITECTS
OTHELLO, a 68-unit affordable cooperative building slated to break ground this spring in Seattle, is pursuing the Materials Petal of the LBC, and will have fiberglass, rather than vinyl, windows.
Although obtaining permissions for the unconventional systems can be labor-intensive, the consensus among sources is that vetting materials for Red List ingredients is the most time-consuming aspect of an LBC project. And for buildings where budgets are exceptionally tight, the obstacles to finding suitable products are compounded. “The affordable-housing sector is really tied to business as usual,” says Gladys Ly-Au Young. Her firm, Sundberg Kennedy Ly-Au Young, is pursuing the Materials Petal for the Othello, a 68-unit affordable cooperative building slated to break ground this spring in Seattle. She notes that, while there are incentives and funding that can help pay for energy-efficiency measures, such as the grant the project received from a local utility for its heat pump hot-water system, there are no equivalent programs for materials.
For Othello, eliminating vinyl (a Red List ingredient omnipresent in products typically used in affordable housing) was particularly vexing—especially when it came to the windows. But, ultimately, the architects were able to find a manufacturer willing to fabricate fiberglass windows during slow periods, thereby allowing them to match the price of vinyl while evening out their production cycles, explains Ly-Au Young.
Shining a light on the roadblocks to creating ultra-green buildings—like those in obtaining healthy materials encountered on Othello, or other impediments, whether they are related to regulations, technology, or economics—is what the LBC is all about, says McLennan. He’s encouraged that barriers are falling, one by one. But he warns that, in order stall global warming, the pace will need to further accelerate. “We are losing the climate battle and destroying habitat and biodiversity,” he says. “The world needs Living Buildings now more than ever.”
Supplemental Material
Living Building Challenge 4.0, International Living Future Institute, June 2019 (Through page 27)