Multifamily Housing - More Popular Than Ever
The design of the flow mechanism and the controls that actuate it allow for good performance using reduced amounts of water. Just as importantly, toilets with dual-flush controls are common, since they allow the user to determine how much water is used for each flush appropriate to the need. With such dual-flush technology built-in, a household or facilities manager can reduce their water usage by thousands of gallons of water per year. In-wall toilet installation systems typically include such dual-flush technology activated by touch (or touchless) panels flush-mounted on the wall above the toilet.
Bluetooth-enabled touchless actuators and buttons are an option for hygiene and water management in both residential and commercial settings for owners and property managers. With an app, the battery level can be checked, and settings can be adjusted from a distance. All devices can be configured and grouped by units or locations, water usage data can be exported, and even a cleaning mode can be set in advance. This provides a time-saving solution to water management and maximizes water savings in individual condominiums or an entire multifamily building.
SPECIFYING OUTDOOR DECK SYSTEMS
Modular pedestal deck systems are versatile and can be incorporated into almost any multifamily project to create usable, sustainable, and affordable outdoor spaces. They consist of standardized components that can be selected, specified, and customized to meet project needs, budget requirements, or green building goals. Regardless of where or how they are used, though, adjustable deck systems commonly incorporate three types of components as described in the following sections.
Deck Supports
Fixed or adjustable height pedestals are the fundamental support system for outdoor decks and have become recognized as one of the most labor- and cost-efficient methods of creating a level deck over a moderately sloped surface. High-density polypropylene plastic makes them impervious to water, mold, and freeze-thaw cycles. Their adjustability offers tremendous design flexibility compared to traditional deck-building materials and methods. Using a gravity system, the supports do not penetrate but rather protect roofing and waterproofing membranes thus causing no damage or harm to the surface below. The pedestals can be used to elevate the deck surface to meet the threshold, therefore providing an even and level transition from one space to another. This allows easy access for building occupants with varying levels of mobility.
Deck Surfaces
The versatility of adjustable pedestal deck supports means that they can be used to elevate a variety of decking surface materials. The common options include pavers made from concrete or stone, such as granite or travertine. Similarly, structural porcelain tiles, fiberglass grating, composite materials, or conventional wood decking systems can be used in a grid pattern to meet different design requirements. Typically, a galvanized steel paver tray is adhered to the back of structural porcelain pavers or other materials prone to breakage to provide impact resilience and additional strength. The paver trays are available in a variety of standard sizes, compatible with large format ceramic tiles, and allow accommodation for thicknesses of 2 cm. With or without a support tray, the deck surface materials can be removed during building use for routine maintenance, repairs to the roof, or to gain access to other systems.
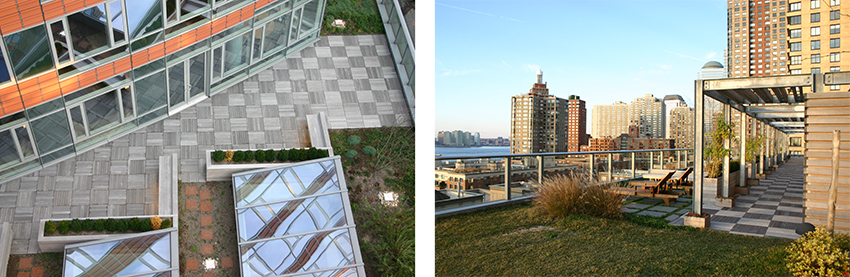
Photos courtesy of Bison Innovative Products
Modular wood tiles on raised deck supports provide a welcome variety of outdoor spaces at the LEED Platinum Certified Visionaire Apartments in New York City designed by the architectural firm of Pelli Clarke Pelli.
If a lighter-weight surface material is preferred or required, wood tiles are a good alternative, weighing only one-third as much as concrete pavers. Typically made from hardwoods in a variety of species, wood tiles are generally commercial-grade products. If maintaining the wood color is desired, wood tiles can be periodically cleaned and sealed. Left to weather naturally, the wood tiles will develop a silvery-gray patina. Wood tiles can be crafted from premium-grade remnants and harvested in an environmentally responsible method designed to preserve the economic viability of rainforest hardwoods.
Some manufacturers of wood tiles associate with governing groups such as the Forest Stewardship Council (FSC) to ensure the quality standards and practices of wood acquisition and plantation farming.
Site Furnishings
Manufacturers of pedestal deck systems also offer coordinated, modular elements that are designed to integrate with their deck systems while giving the architect complete design flexibility. Modular wood or aluminum cubes are available with an array of design options to incorporate seating, storage, and planters. Such cubes are available with a polyurethane lining and drainage holes to host plant life. At other times of the year, the cubes can be repurposed for seating and storage of seasonal items (i.e., cushions and pillows) by placing a manufactured hardwood top on the cube.
SPECIFYING FIRE-RETARDANT-TREATED WOOD
Specifying FRTW is directly linked to the normal process of manufacturing it. There are several primary considerations.
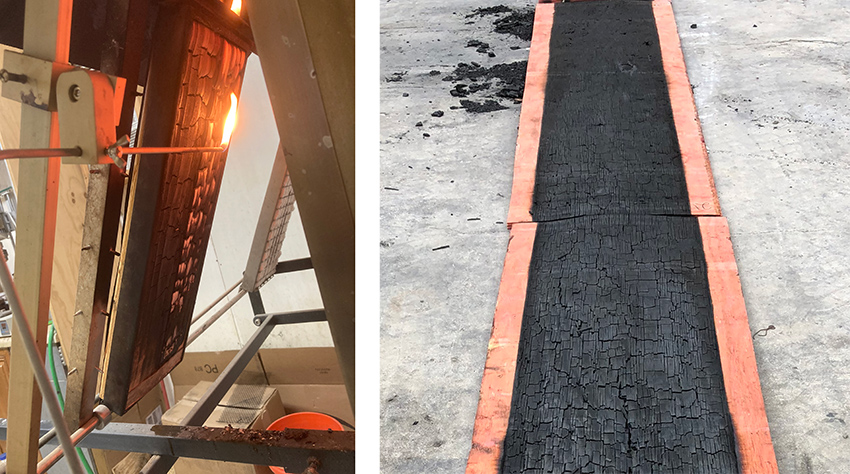
Photos courtesy of ProWood
FRTW is tested according to ASTM E-84/UL-723 standards in designated fire test. When exposed to combustion, the fire retardant treatment forms a char layer to insulate the wood, reduce the flame spread, and inhibit smoke development.
Testing: Specifications need to address the specific testing required by the IBC to be sure the product being supplied is code-compliant. That means it must be tested in accordance with ASTM E84 or UL 723 to achieve a listed flame spread index of 25 or less using the required Steiner Tunnel test method. In order to meet a Class A designation, it must be exposed to testing for 10 minutes with satisfactory results. Note that for fire-retardant wood used in construction, passing a 30-minute test is required–the initial 10 minutes, plus an additional 20 minutes. In this extended 30-minute ASTM E84 test, the flame front must not progress more than 10½ feet beyond the centerline of the burners. (IBC 2303.2 Fire-Retardant Treated Wood). It is incumbent upon the manufacturer to ensure their products meet the testing requirements and then to label their products appropriately according to the requirements of IBC 2303.2.4 – Labeling.
Note that there is a new update in the 2021 version of the IBC related to ASTM E84|UL 723 testing. It involves a change to the tests for plywood by requiring a horizontal rip cut that must be exposed during the test. For pressure-treated FRTW products, that should not be a problem since the treatment impregnates the wood. However, topical treatments are on the surface only and may not have the capability to meet this additional testing requirement–meaning it is not deemed as safe as the pressure-treated method.
Treatment of Products: The untreated wood (lumber or plywood) is impregnated with fire-retardant chemicals. When done using a pressure process, it must be performed in closed vessels under pressures not less than 50 pounds per square inch gauge (psig) (345 kPa) (Per IBC 2303.2.1). Topical applications are also used by some manufacturers, but they don’t produce the same fire-retardant results and should be investigated for appropriateness before specifying. Either way, fire-treated wood often contains a red/orange tinted dye for easy identification so it can be distinguished from non-treated wood on a construction jobsite. FRTW products are available in a variety of wood species including spruce, pine, and fir. Certificates of Treatment are often issued for specific lots of material upon request or if specified.
The fire-retardant elements within most fire-retardant wood products include a blend of phosphate powder (the salt of phosphorus), boric acid powder, and water for dilution. The carbon dioxide reaction of these elements with fire creates a char around the wood, insulating and suppressing the spread of flames and combustion. In addition to suppressing fire, this reaction also suppresses the development of smoke. Some manufacturers can provide certifications related to green or sustainable standards such as UL Greenguard Gold for low chemical emissions.
Kiln Drying After Treatment: The treated wood is moved from the pressure vessels to the kiln to be dried. Fire-retardant lumber must achieve a specified moisture content after treatment per the code. For lumber this moisture content is not to exceed 19% and for structural wood sheathing (plywood) not to exceed 15%. (IBC 2303.2.8) Spacers are placed between the wood to maximize airflow and proper drying. Fire-treated wood remains in the kiln until the specified moisture content is achieved.
Storage and Handling: Exposure to precipitation during storage and installation must be avoided since FRTW is not intended for exterior exposure or applications. If any FRTW product becomes wet, it must be allowed to dry before enclosing in construction. Finished products are wrapped or bagged and stored 6 inches off-ground and under cover whenever possible. It is a best practice to store all FRTW in a dry, covered space on a job site.
Notice
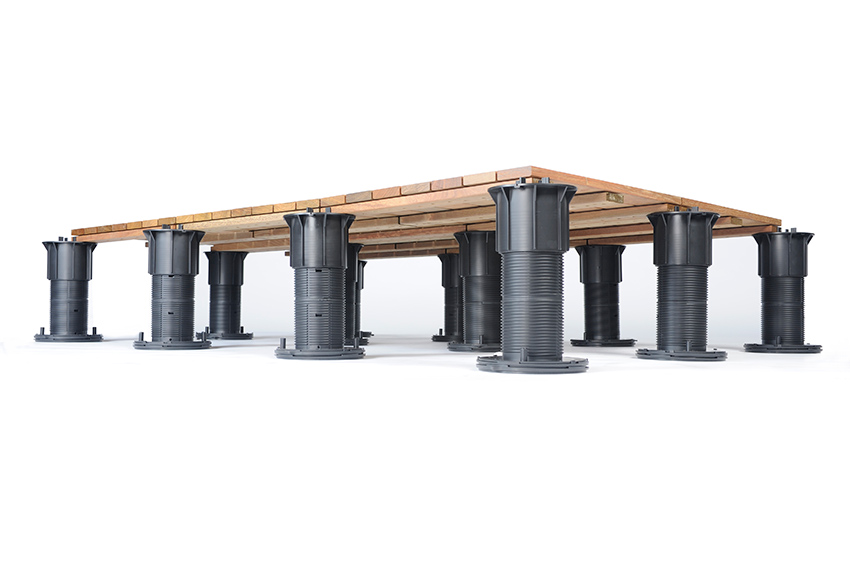
www.bisonip.com
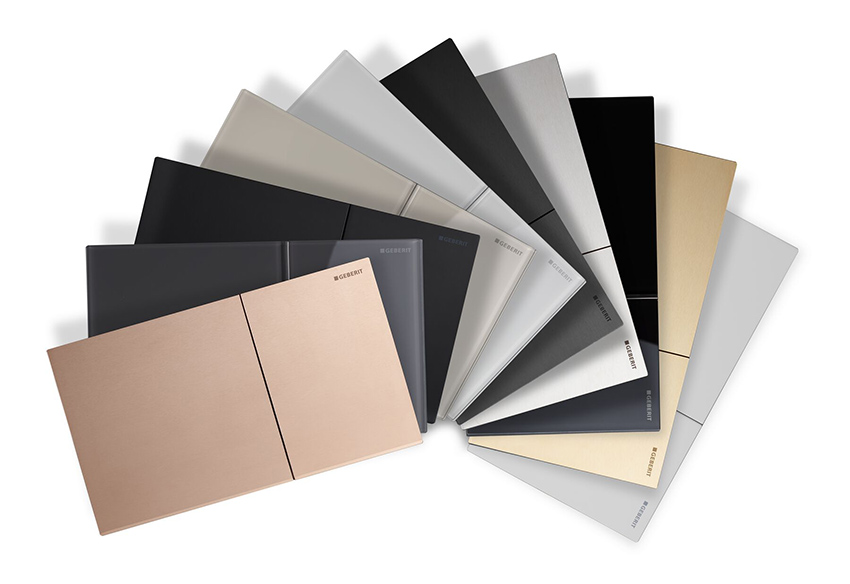
www.geberit.us
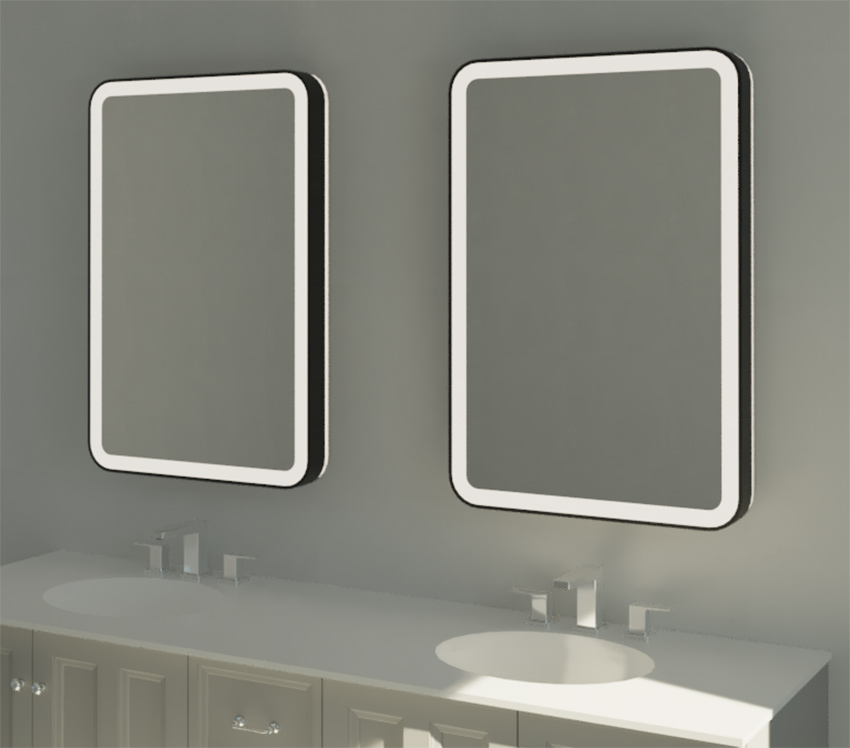
www.meekmirrors.com
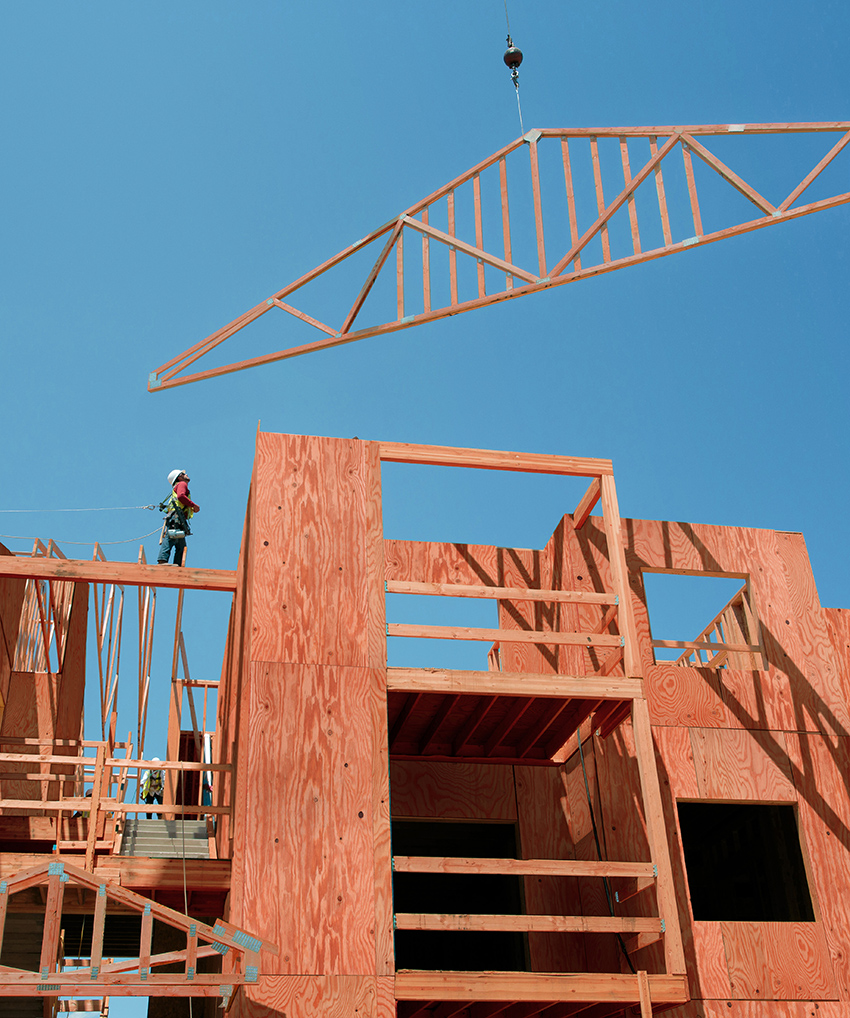
www.prowoodlumber.com