This CE Center article is no longer eligible for receiving credits.
Traditional Wood-Frame Construction
For centuries in North America, the dominant method of building homes and low-rise apartments has been wood frame construction, which has shown strength, longevity, and stability. Mid-rise light wood-frame structures are widely considered to be cost effective, due to relatively low material costs, reduced construction time, availability of resources and labor.4 The development of prefabricated component systems increases the strength and affordability of wood frame construction. Also, when built according to building codes and industry standards, wood-frame structures can provide hurricane and seismic resistance.
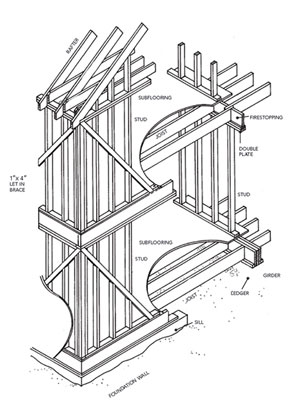 |
Platform framing uses shorter lengths of lumber for the studs, generally 2x4s spaced 16 inches on center.
Image courtesy of American Wood Council |
Wood-frame construction entails the use of wood-framing members, typically dimensional lumber, I-joists, or prefabricated wood trusses, spaced relatively close, and used with sheathing or decking to create a structure that can withstand loads. Modern wood framing essentially includes three types: balloon, platform and semi-balloon framing.
Balloon Framing
With long lumber lengths, vertical load-bearing framing studs run continuously from foundation to roof. Intermediate horizontal floor joists are nailed to the sides of the vertical studs and bear on a ledger. The ledger is notched into the stud. Typically this system is more common in two-story buildings due to the stud length availability. However, a variation of this method could be used in increments of two stories. The advantage to this is that it would eliminate the shrinkage that may occur from the floor joists.
Platform Framing
Over time, platform framing replaced balloon framing as the dominant framing method. Platform framing uses shorter lengths of lumber for the studs, generally 2x4s spaced 16 inches on center. The walls are typically framed with a sill or sole plate, studs and two top plates, then floor joists bear on the top plates. Platform framing does not require hangers, while semi-balloon framing does as described below.
At each story, joists are covered by subflooring providing a platform, or work surface, on which walls and partitions are easily erected. The benefits of platform framing include the fact that walls can be constructed on the ground and less effort is involved in lifting them into place than in balloon framing. Notching of the stud is not required, and after one story is constructed, the framers can utilize it to construct the next story. Platform framing also accommodates various prefabricated methods.
Semi-Balloon Framing
Semi-balloon framing is a cross between balloon framing and platform framing. Where balloon framing has a continuous stud from foundation to roof, semi-balloon framing does not. Balloon framing does not require hangers, whereas semi-balloon framing does.
While platform framing is more dominant overall, modern semi-balloon framing, in which the floor joist hangs from the double top plates, is more common in buildings that are five stories and up, and is ideally suited to certain circumstances. According to Michelle Kam-Biron, P.E., S.E., senior technical director, lead for mid-rise construction for WoodWorks, “In the U.S., where most states follow the International Building Code, semi-balloon framing is often used as an alternative to platform framing in structures where fire requirements or shrinkage may be a challenge.” Type III construction requires non-combustible exterior walls but there is an exception in the code that allows for fire-retardant treated wood (FRTW). “Designers will sometimes utilize semi-balloon construction, hanging the joist off the top plates and eliminating the penetration of the exterior wall building envelope,” Kam-Biron says.
 |
(Left) Semi-balloon framing is more common in buildings five stories and higher; (Right) it is often used as an alternative to platform framing where fire requirements or shrinkage may be a challenge.
Photo courtesy of US WoodWorks |
Mid-rise construction is becoming increasingly popular as a means of boosting densification, containing urban sprawl, and respecting infrastructure limits while maintaining neighborhood charm and community appeal. Multi-family construction in particular has grown, increasing 46 percent between 2009 and 2011. This year, the sector is expected to continue to advance, rising 23 percent over 2011.1
Wood has a key role to play in mid-rise construction. It has proven to be more affordable than concrete or steel, and has a lower environmental footprint than either material. Architects for Stadhaus, a nine-story wood apartment building in England, found that compared to concrete, a wood building offered cost savings of more than 15 percent,2 and that 186 tons of carbon were sequestered within its structure.3
Codes now allow wood as a structural material in five- and six-story wood-frame structures, in most U.S. states and throughout Canada. Traditional wood-frame construction is a proven solution for current mid-rise structures up to six stories, and mass timber is a possible solution for even taller buildings. Both are being used to achieve durable, code-compliant, economical mid-rise developments that add vibrancy at a human scale.
This article will provide a high-level comparative overview of the systems themselves. Wood-frame construction systems including balloon, platform, and semi-balloon framing will be discussed as will mass timber solutions including cross-laminated timber (CLT), glue-laminated timber (glulam), and laminated strand lumber (LSL). Case studies will showcase how architects are using these systems to full advantage either through code-compliant situations for additional stories or by turning to alternative solutions—methods of construction that are not included in the building code per se, but can be used to meet the intent of code—to build taller, smarter, and more efficiently with wood.
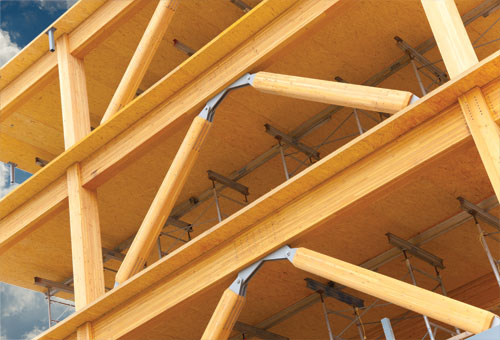 |
The University of British Columbia Earth Sciences Building is a five-story wood structure that uses CLT, glulam, and LSL. Architect: Perkins+Will Canada Architects Co.
Photo by K. K. Law |
Traditional Wood-Frame Construction
For centuries in North America, the dominant method of building homes and low-rise apartments has been wood frame construction, which has shown strength, longevity, and stability. Mid-rise light wood-frame structures are widely considered to be cost effective, due to relatively low material costs, reduced construction time, availability of resources and labor.4 The development of prefabricated component systems increases the strength and affordability of wood frame construction. Also, when built according to building codes and industry standards, wood-frame structures can provide hurricane and seismic resistance.
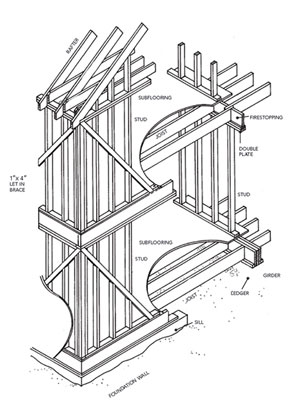 |
Platform framing uses shorter lengths of lumber for the studs, generally 2x4s spaced 16 inches on center.
Image courtesy of American Wood Council |
Wood-frame construction entails the use of wood-framing members, typically dimensional lumber, I-joists, or prefabricated wood trusses, spaced relatively close, and used with sheathing or decking to create a structure that can withstand loads. Modern wood framing essentially includes three types: balloon, platform and semi-balloon framing.
Balloon Framing
With long lumber lengths, vertical load-bearing framing studs run continuously from foundation to roof. Intermediate horizontal floor joists are nailed to the sides of the vertical studs and bear on a ledger. The ledger is notched into the stud. Typically this system is more common in two-story buildings due to the stud length availability. However, a variation of this method could be used in increments of two stories. The advantage to this is that it would eliminate the shrinkage that may occur from the floor joists.
Platform Framing
Over time, platform framing replaced balloon framing as the dominant framing method. Platform framing uses shorter lengths of lumber for the studs, generally 2x4s spaced 16 inches on center. The walls are typically framed with a sill or sole plate, studs and two top plates, then floor joists bear on the top plates. Platform framing does not require hangers, while semi-balloon framing does as described below.
At each story, joists are covered by subflooring providing a platform, or work surface, on which walls and partitions are easily erected. The benefits of platform framing include the fact that walls can be constructed on the ground and less effort is involved in lifting them into place than in balloon framing. Notching of the stud is not required, and after one story is constructed, the framers can utilize it to construct the next story. Platform framing also accommodates various prefabricated methods.
Semi-Balloon Framing
Semi-balloon framing is a cross between balloon framing and platform framing. Where balloon framing has a continuous stud from foundation to roof, semi-balloon framing does not. Balloon framing does not require hangers, whereas semi-balloon framing does.
While platform framing is more dominant overall, modern semi-balloon framing, in which the floor joist hangs from the double top plates, is more common in buildings that are five stories and up, and is ideally suited to certain circumstances. According to Michelle Kam-Biron, P.E., S.E., senior technical director, lead for mid-rise construction for WoodWorks, “In the U.S., where most states follow the International Building Code, semi-balloon framing is often used as an alternative to platform framing in structures where fire requirements or shrinkage may be a challenge.” Type III construction requires non-combustible exterior walls but there is an exception in the code that allows for fire-retardant treated wood (FRTW). “Designers will sometimes utilize semi-balloon construction, hanging the joist off the top plates and eliminating the penetration of the exterior wall building envelope,” Kam-Biron says.
 |
(Left) Semi-balloon framing is more common in buildings five stories and higher; (Right) it is often used as an alternative to platform framing where fire requirements or shrinkage may be a challenge.
Photo courtesy of US WoodWorks |
Mass Timber Products and Systems
Advancements in wood technology, systems and products, together with performance-based building codes have fueled interest in building with mass timber in mid-rise construction and even taller buildings. Engineered wood products offer the architectural community alternate materials and systems with comparable or better performance and environmental attributes than other construction materials. Canadian architect Michael Green, in fact, sees mass timber—CLT, parallel strand lumber (PSL), and LVL—playing a major role in buildings up to 30 stories5. Performance-based building codes are accommodating the use of such new technology. While some of this new generation of wood products are not referred to specifically in the building code, architects can propose them as an alternative solution. As an example, buildings that were previously permitted only to be of non-combustible construction, can now be built of wood, provided it is sufficiently demonstrated that the structure provides equivalent fire safety.
Differentiated from dimensional lumber by having minimum dimensions required by the building code, modern mass timber6 refers to a family of products including sawn stress-grade lumber, timber tongue and groove decking, glulam, and CLT—that offer advantages in terms of increased strength, and also have quickened the construction process and enabled the use of wood products as solid walls, floors, elevator shafts, and columns to construct an entire building. Modern heavy timber products are particularly suited to mid-rise/multi-family housing, schools, large-span recreation centers, and supermarkets—buildings that must stand up to extreme loads caused by strong winds, heavy snow loads, and earthquakes.
 |
Panel sizes vary by manufacturer. CLT is currently available in North America with dimensions up to 19-1/2 inches thick, 18 feet wide and 98 feet long.
Image courtesy of FPInnovations |
CLT is one type of new mass timber assembly that is comparable in strength to steel and concrete,7 but weighs less. A CLT panel has at least three glued layers of boards placed in orthogonally alternating orientation to the neighboring layers. In special configurations, consecutive layers may be placed in the same direction, giving a double layer to obtain specific structural capacities. Modern CLT exemplar include the eight-story H8 in Bad Aibling, Germany, which was completed in three weeks. Experts maintain that the structural performance of CLT makes it possible in situations where wood has never been used before.8 In North America CLT solutions are emerging in mid-rise buildings, setting records for versatility and speed.
Case Studies on Traditional and Innovative Wood Systems
The following case studies illustrate a variety of ways in which architects approach wood-frame mid-rise construction utilizing both traditional and new methods to maximize functionality. These examples cover a wide array of conditions and challenges, including cost, climate, seismic activity, and adherence to safety codes.
Balloon Framing as a Means to Reduce Shrinkage |
 |
Designers used balloon framing to prevent shrinkage on this Vancouver Island development.
Photo courtesy of Misra Architect Ltd. |
Located on the southern tip of Vancouver Island, the six-story Skyline Condominiums enjoy an idyllic location and postcard views.
Designers used balloon framing to reduce the potential for shrinkage. “Normally, the wood member shrinks approximately 3/8 of an inch per floor for 12 percent moisture in the wood. To avoid that, we used plywood, joist hangers for the joists, and balloon framing,” says Pradip Misra, principal, Misra Architect Ltd. Because wood shrinks to a greater degree across the grain than parallel to grain, it's the horizontal members, such as the sills and joists than can be problematic, rather than the posts and studs. “The joists are hung from the side of the bearing walls. This eliminates the floor shrinkage in the total building shrinkage,” says Steve Hoel, P.Eng., Struct.Eng., principal, JSH Engineering Ltd.
Skyline's location is prone to humidity, seismic activity, and wind. This resulted in more than a few design challenges. Buildings in this area are required by code to withstand the most severe earthquake loads in Western Canada, and there is always a tendency to build with either steel or concrete. However, the design team and the owners went with wood. Wood-frame structures, which have numerous nailed joints, have more load paths and are inherently more ductile than those with a rigid connection—which make them more flexible and allows them to dissipate energy when subjected to the sudden loads of an earthquake. “The mass of the building also contributes,” says Sukh Johal, technical advisor for WoodWORKS!BC. “Wood buildings are lightweight, but perform well structurally.” Since forces in an earthquake are proportional to the weight of a structure, wood-frame buildings that are properly designed and constructed perform exceptionally well. Misra says that mechanical options were also a factor in seismic design, notably “hold-downs,” known as continuous tie rod systems or 1-inch diameter steel bars that extend from the concrete slab to the upper floors. “This is a self-adjusting system to keep all floors intact in the event of seismic forces.”
Wood also offered advantages in terms of cost. Developers, who opted for a six-story structure in response to the increased height allowed in B.C., compared the costs of concrete, steel, and wood in an extensive study. “A concrete-and-steel superstructure ran 20 to 25 percent more than wood, and a structured steel superstructure 12 to 15 percent more than wood,” says Biki Kang of Kang & Gill Construction Ltd. “Wood was found to be the most economical choice.” |
Platform Wood Construction Brings Affordable Urban Appeal |
 |
Photo courtesy of Tien Sher Group of Companies |
The Quattro 3 condominium opened in September 2012, the first multi-family six-story building in Metro Vancouver, built from wood. The project used platform framing to increase affordability and occupant comfort. Featuring 164 units from studios to two-bedrooms and one floor of commercial space, Quattro 3 is part of a larger planned community that will include up to 1,900 homes.
While experts say that mid-rise wood frame construction is too new to B.C. to make a definitive statement about the cost competitiveness of wood, what can be said is that based on projects under construction in 2011 the above-grade cost of wood mid-rise construction will reduce costs by ten percent vs. steel or concrete construction. “There's always a difference between concrete and wood in terms of affordability,” says Charan Sethi, president and CEO of the Tien Sher Group of Companies, developers of Quattro 3. “In the Surrey market, concrete units sell for $50 to $75 per square foot more than comparable wood units.” Sethi feels the mid-rise wood building benefits from lower per-unit land costs and construction costs that can then be passed along to the consumer. “We're always looking for ways of bringing affordability to the working class market,” Sethi says.
Sustainability, locally sourced materials, and ease of construction were other factors that drew Sethi to wood. Sethi says, “Construction was completed by our experienced framing crew and on-site staff. The process was efficient.”
Occupant comfort was a prime concern. Noise transmission is a performance challenge in any multi-family building and in wood construction there are several solutions to mitigate sound transmission, including greater mass, increased stiffness, sound-absorbing insulation, resilient metal channels, and structural discontinuity between noise and occupant. At Quattro, 1.5-inch lightweight concrete topping between floors was used for additional soundproofing and robust insulated double 2-inch-x-6-inch framed party wall construction was employed to minimize vibration and sound transfer between homes.
Fire experts maintain that six-story wood-frame buildings are as safe as any other form of buildings. “For a sprinklered occupied building, there is absolutely no safety issue,” Sethi says. According to Len Garis, Surrey's fire chief and president of the Fire Chiefs' Association of B.C., “the fire safety of people living in six-story wood-frame buildings should be equal to the safety in any other building.” Garis was quoted as saying, “These buildings are fully sprinklered and our research suggests to us that in a sprinklered building, a fire is likely to never leave the room of origin, has historically never left the floor of origin in a building. Where the sprinkler system needed to operate to put the fire out, it put the fire out.”9
Quattro 3 makes an ideal introduction to mid-rise wood buildings in Metro Vancouver not only in terms of affordability, but in occupant comfort and safety as well. |
Seattle Hybrid: Wood Platform Framing and a Concrete Podium |
 |
Photo by Matt Todd Photography, courtesy of WoodWorks |
The Marselle is a hybrid wood and concrete structure consisting of five stories of wood-platform framing plus a wood mezzanine and a six-story concrete podium, of which, two stories are above ground. The combination of “five and one-half over two” made Marselle the tallest modern wood-frame structure in Seattle.
Marselle's main distinction lies in the way wood framing was used to maximize the value of the finished space. Two key code requirements allowed that to happen.
The City of Seattle's 2003 Building Code (SBC), under which the Marselle was built, was based on the 2003 International Building Code (IBC). Under the 2003 IBC, mezzanines were limited to 33 percent of the floor area beneath. However, SBC allowed five stories of wood construction over two stories of Type I construction plus 50 percent for a mezzanine. Mezzanine levels are not considered floors. Under the SBC, Type V-A construction allowed a fully sprinklered 70-foot maximum height for five stories while Type III-A allowed a fully sprinklered 85-foot maximum height for five stories. Zoning regulations allowed a maximum height of 85 feet. Therefore, the design team took advantage of Type III-A construction by adding a mezzanine level on top of the allowed five-story structure, to fill in the building envelope to the 85-foot maximum zoning height allowed.
The other criteria concerned construction type. According to architect Michael Shreve with PB Architects, “under the 2003 SBC, section 504.2, the allowable height for buildings of Type III-A construction in Group R-2 could be increased to five floors of wood-frame construction above two stories of Type I concrete construction and an 85-foot maximum height. The two floors of concrete construction were required to be Type I construction with a three-hour horizontal fire rating separating the wood construction from the concrete construction.”
“Once built, the top level units would have water views of Seattle's Lake Union,” explained structural engineer Panos Trochalakis, P.E., S.E., principal with Yu & Trochalakis, PLLC. “For obvious reasons, the developer wanted to take advantage of that.” The extra half-story mezzanine added about $250,000 to the construction cost of the building, but the architect and builder estimated that the added height and space increased the value of the complex by $1 million and afforded revenue-generating views on the top floors.
Attention was devoted to maximizing the strength and durability of the wood members, with architects designing for potential shrinkage. As is typical with wood-framed podium structures, Marselle's contractors used a continuous rod tie-down system with a shrinkage compensation device to limit deflection and avoid wall separation due to wood shrinkage under wind and seismic forces. They also included an expansion joint in the cladding; were careful to specify proper panel spacing in the exterior wall sheathing; and included a provision in the mechanical system to allow for movement.
The use of wood also had a positive impact on schedule and budget factors, with pre-panelized walls enabling a speed of construction that made a big difference. The panels, which ranged from 4 to 20 feet long, were pre-assembled by a local framer in an off-site warehouse, and then quickly and easily lifted into place at the job site by crane. “If you can install the walls on a building the size of Marselle in less than two weeks per floor, then you lower construction costs significantly,” Trochalakis says. “Lower construction costs were the number one reason to use wood. Wood-frame construction is virtually impossible to beat in terms of cost.”10 |
Mass Timber for a Simplified Design and Greater Structural Capacity |
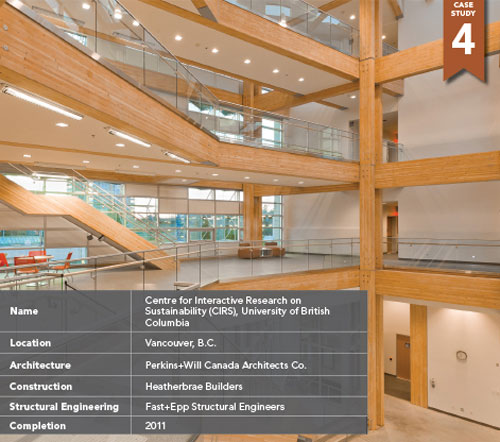 |
Photo courtesy of UBC |
Billed as the most innovative high-performance building in North America, the Centre for Interactive Research on Sustainability (CIRS) at the University of British Columbia is expected to be the university's first LEED® Platinum building, and is on track to receive Living Building Challenge recognition. The building was envisioned as a new baseline in sustainable high-performance buildings, and incorporated regenerative design—an emerging alternative to current green design practices that seeks not merely to reduce harmful environmental impacts, but to actually improve both the natural environment and the lives of their human inhabitants. Mass timber played an important part in achieving these goals. CIRS features a simple structural design, comprised of a combination of glulam members, dimensional lumber, plywood, and a minimal amount of concrete. The moment frame structure was designed to create an open, column-free floor plate for flexibility of use and interior arrangements, and to allow for large openings in the walls that maximize daylight and views11. The members' size and solidity make the structure non-combustible heavy timber construction under British Columbia Building Code—a designation that simplifies the building design.
In order to reinforce external charring in case of fire, designers sized all members slightly larger than required. A building-wide sprinkler system and on-site water supply and water pump were also incorporated to enable the heavy timber wood structure to meet the requirements for non-combustible construction required by code.
Designers opted to size the structure to support a live load of 100 pounds per square foot (4.7 kilonewtons/square meter), double the requirements of the British Columbia Building Code, to achieve an increased capacity that allows for additional equipment and future changes in use. Structural members were larger where larger loads required more support, notably in the auditorium where beams and columns were sized to handle both a long span over the seating and the load of the green roof. “From a structural point of view, the modern engineered materials...have increased the strength of wood so that they have a much greater structural capacity,” says Paul Fast, managing partner, Fast+Epp. |
CLT, LSL, Glulam in a five-Story Academic Building |
 |
Construction of ESB, five-story wood structure at UBC using CLT.
Photo by K. K. Law, naturally:wood |
The University of British Columbia's Earth Science Building (ESB) at the Point Grey Campus in Vancouver is composed of two five-story wings connected by an atrium. The ESB's new five-story north wing will house the academic research, lecture, and office spaces and, unlike its neighboring concrete laboratory south wing, uses wood as the primary structural material. Designed for LEED® Gold status, the north wing is supported by glulam columns and beams; floors consist of LSL and concrete; and the roof and canopies are built with CLT. According to the University, it is North America's largest panelized wood project and its largest application of CLT to date.12
Composite floor system. The floors in the north wing are constructed predominantly of a composite system that was first adopted in Europe and is well regarded for its engineered technology and ability to achieve long spans. The floor system consists of 3.5-inch-thick laminated strand lumber panels topped with foamed board insulation and four inches of reinforced concrete poured in situ. Hybrid floors in Europe are often a prefabricated element; however, this being one of the first hybrid floor applications in North America, it was fabricated on site for this project.
The composite connectors are secured into slots cut into the face of the wood panels. These plates extend past the layer of the insulation to support the reinforcing bars for the concrete topping. The insulation provides an acoustic break and also acts as a barrier to prevent moisture infiltration while the concrete sets. This assembly is over 50 percent lighter than a solid concrete floor, allowing for larger spans which increase the 'loose fit' opportunities for designers. The ends of the 22-foot-long wood-composite floor panels are supported by steel beams above the first floor of the ESB project, and on glulam beams to create the ceilings for floors two through four.
The University plans to implement the floor system at its Okanagan Campus Fitness and Wellness Centre in Kelowna. 13
Vibration. Designers chose a wood-concrete composite floor system in part to provide a high level of vibration performance. With a sandwich of 3.5 inches of LSL, one inch of foam board insulation and four inches of reinforced concrete, the wood-concrete composite system's acoustic performance offers excellent sound absorption.
 |
During a fire, the exterior layers of wood will char creating a layer of insulation that prevents the interior from burning, thereby maintaining structural integrity. Crosssection taken from 3-ply CLT panel protected by two layers of ½-inch gypsum board and exposed to the standard fire exposure (CAN/ULC S101) for 1 hour and 15 minutes.
Photo courtesy of FPInnovations |
Fire resistance/building code. As the British Columbia Building Code prescribed fire safety requirements did not allow an entire heavy timber or wood-frame construction, an engineering assessment was documented in a peer-reviewed Building Code Alternative Solution. The assessment examined how the wood construction might perform in both the pre-flashover and post-flashover fire environments. Flashover is the point in a developing fire when all combustibles within a room ignite nearly simultaneously and begin to burn. This phase of fire's growth is critical since environmental conditions are not survivable and the heat impact on walls and ceilings becomes severe. To stop fire before it reaches this phase, designers specified an automatic sprinkler system, and a fire retardant coating to alter the surface burning characteristics of the woods interior finishes, a technique used to slow or completely eliminate fire from growing across the wood's surface. Further, analysis showed the risk of fire growth and spread would inherently be limited by the building's many separate, individual offices and rooms, creating many compartments each capable of containing a small fire. The wood structure was also engineered to account for the charring of the wood members and the gradual loss of cross-sectional area. Sufficient uncharred fiber remains so the wood elements continue to resist the expected gravity loads during the fires duration.
Steel beams to wood columns. Wood performs favorably in compression circumstances when forces act in parallel to the grain, as opposed to when the grain is perpendicular to the load path. On the ESB's second level, long steel beam spans connected to wood required a butt connection in which the top flange of a steel beam is notched into a glulam column and pinned for structural support.
Wood beams to wood columns. Throughout the project, the structurally engineered timber systems used quick, safe and efficient connectors. Approved for load bearing timber construction, these connectors are designed for easy assembly of even the most complicated nodes. Like the traditional dovetail connection, these connectors consist of two parts that lock into place to create a form-fitting connection. With each connecting system designed, forces are transferred perpendicular to the installation direction for tension and compression purposes. The hardware can be factory pre-installed in the beams and columns, ultimately reducing on-site assembly time. Connectors are completely concealed, and would be protected during a fire by the insulating char layer that would form on the encapsulating wood members.
Heavy timber shear bracing. As part of the Seismic Force Resisting System (SFRS), at the end walls of each story, diagonal glulam heavy timber braces were integrated to provide controlled resistance to the shear loads across the structure. Since the glulam members themselves do not have the ability to dissipate energy, the system relies on the predictable ductility of the connections, achieved by using multiple steel knife plates with a large number of tight-fitting, small-diameter pins. The slots in the glulam where the knife-plates are inserted were designed with longitudinal slack, which leaves room for controlled movement under shear loading that allows the tight-fit pin connection to yield in tension and compression. The precision required for these sophisticated connections was enabled by prefabricating both wood and steel components with computer numerically controlled (CNC) machinery.
Full-story transfer truss connections. Throughout the second story, steel diagonal braces and steel beams, together with the glulam columns and glulam beams with an integrated concrete top plate, create a type of truss structure. The first story above grade consists of a building-wide assembly space, with the ceiling structure of the second floor supporting the entire building above it. To carry this load, full-story steel glulam hybrid transfer trusses were designed to essentially convert the entire second floor structure into a 'roof truss' capable of carrying the load of the remaining floors across the entire span of the structure below.
'Free-floating' staircase. Located within the impressive atrium linking the academic and laboratory wings is a five-story free-floating cantilevered solid timber staircase. The clean and elegant lines of the massive timber demonstrate the innovative aesthetic and structural capabilities of wood in construction. Based on a German wood-steel composite, the rigid composite of the wood with glued-in steel connectors pushes the envelope of load bearing capabilities of wood construction. Adopted from projects in Germany, this system uses similar steel plates but for the slots that are cut into the ends of the glulam slabs and glued into place with special adhesives.
 |
A five-story ‘free-floating’ cantilevered staircase is built entirely of solid timber.
Architect: Perkins+Will Canada Architects Co. Photo by K. K. Law. |
|
The Future of Wood in Mid-Rise Construction
When it comes to mid-rise development, architects have a code-compliant, cost-effective resource in wood. Over the years, wood-frame construction has shown strength, longevity and stability, and is widely considered economical, with low material costs, reduced construction time, and availability of resources and labor.14 Mass timber products including sawn stress-grade lumber, timber tongue and groove decking, glulam, and CLT offer an accelerated construction process and the increased strength to serve as structural systems for taller buildings. Developments in both wood-frame and mass timber are bringing mid-rise wood buildings to a new level of affordability and transforming our understanding of what is possible with wood construction. In some cases, it is necessary to use alternate solutions to meet the intent of the building code. Pursuing this route is well worth the effort—architects throughout North America have and will continue to use alternate solutions to save time and money, to debunk myths surrounding fire safety and, to set new standards in affordable green design.
Wood also plays a key role in reducing a project's environmental footprint. Wood products have less embodied energy, are responsible for lower air and water pollution, and have a lighter carbon footprint than other commonly used building materials.15 The wood materials in the University of British Columbia's Earth Sciences Building, for example, will sequester some 2,600 tons of CO2 (which equate to 497 cars off the road for one year or energy to operate a home for 221 years). The University's CIRS project is a net positive building because of wood—the project sequesters about 600 tons of CO2 (which equate to 115 cars off the road for one year or energy to operate a home for 51 years) in its wood structure which is more carbon than all the carbon emitted by the construction process, and all the carbon emitted in the manufacture of all the other materials in the building.16
As increasing numbers of wood mid-rise structures take shape throughout North America consistent with stringent building codes, the message is becoming clear. Affordable and energy-efficient with a unique ability to sequester carbon, not only is wood a viable, even preferable, option for buildings of six stories and above, it is creating a new paradigm in building construction.
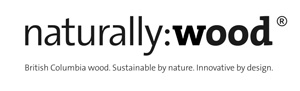 |
naturally:wood is a comprehensive information resource that brings together the latest data about wood performance, green building, variety of wood products, manufacturers, and sustainable forest practices. Visit
www.naturallywood.com for more info. |