Masonry Construction
Air-cured bricks that incorporate a small amount of cement have a significantly smaller carbon footprint than those that are fired. But researchers are studying ways to make modified earthen bricks even more green with additives that could replace the Portland cement, which has a high embodied energy due to a manufacturing process that includes heating limestone in a high-temperature kiln. MIT professor Elsa Olivetti, who teaches in the materials science department at MIT, is working with Ochsendorf to explore the potential of industrial by-products, such as boiler ash, which contains silicates and aluminates. These substances could chemically harden bricks in the same way that Portland cement does, but with fewer environmental consequences, she says.
One way to offset the negative impact of brick is to reuse it. That is what the architects, local firm Archi-Union, did for the Chi She Gallery in Shanghai. They repurposed much of a 70-year-old aircraft repair building, including the brick, and converted it into galleries and workspaces for several artists. Archi-Union stripped down the building to its concrete walls and floor slabs and raised the roof level to allow for a clerestory that lets daylight into an upper-level gallery. The ground level contains a multiuse space and studios.
The most distinctive feature of the project is the rippled brick facade. Made from the salvaged gray-green bricks of the original building, the non-load-bearing wall billows out over the entry. In addition to endowing the structure with a new sculptural presence, the designers made the facade appear lighter and screenlike near the top by omitting bricks in its Flemish bond (a pattern that alternates stretchers, or bricks laid flat with the long face exposed, with headers, or those turned so the short end is exposed).
To achieve the complex curvilinear geometry, the firm tapped into the new technology of robotic bricklaying, which is conceptually similar to CNC (computer numerical control) fabrication techniques. But instead of relying on machines for cutting, milling, or grinding, here a robotic arm was programmed to propel itself along a track while applying mortar to each brick and placing it with precision. Because the technology is not yet sufficiently developed to perform fine finishing tasks, masons followed behind the robot to strike, or shape, the mortar joints between the bricks.
For projects where crisp lines and uniformity are important, bricks that have a consistent hue and surface treatment are available and can be combined with robotic technology. But, like pottery, the elemental beauty of a hand-laid wall of bricks with subtle changes in color and texture is part of our 10,000-year love affair with the material. For a studio for ceramics artist Le Duc Ha near Hoi An, Vietnam, the architects at Ho Chi Minh City–based Tropical Studio show how simple forms can be enriched by taking advantage of variations in locally sourced brick as well as its potential for pattern-making and composition.
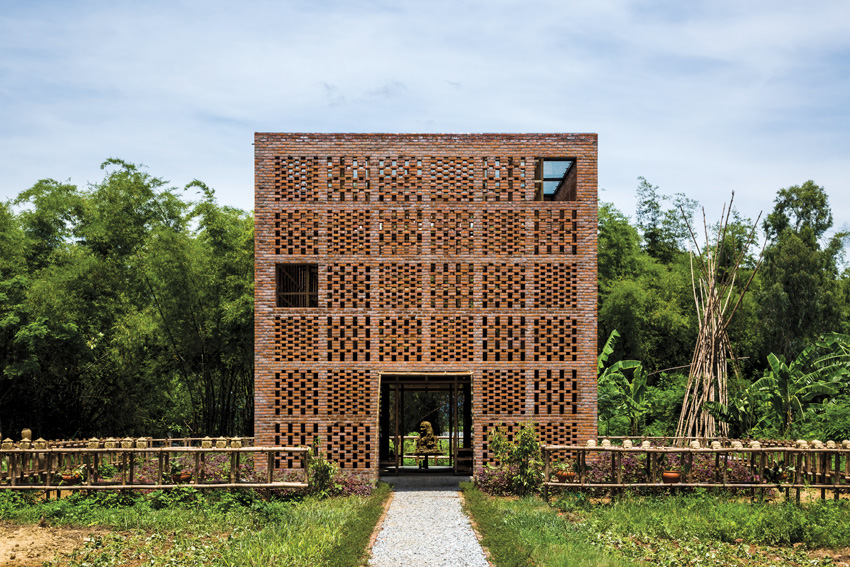
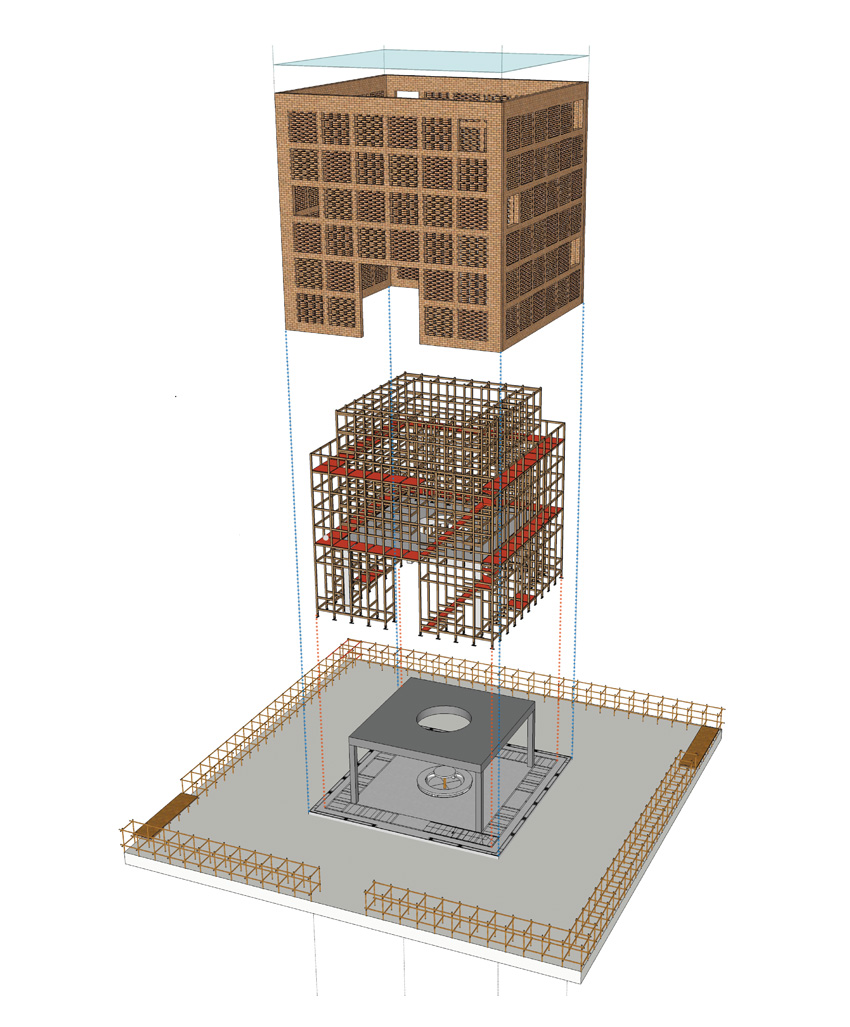
IMAGES: © OKI HIROYUKI (TOP); COURTESY TROPICAL STUDIO (BOTTOM)
GRANNY SQUARES
Tropical Studio organized the four walls enclosing a studio for a ceramist near Hoi An, Vietnam, so that they resemble a quilt, each with a grid of 36 squares. Within these squares, some bricks are omitted to create different patterns with various levels of transparency.
According to Tropical Studio principal Tran Thi Ngu Ngon, the firm envisioned the shape of the building as being as elemental and strong as the clay that forms the artwork. The cubic structure, 21 feet in all dimensions, contrasts with its pastoral setting, the edge of a field overlooking the Thu Bon River.
One goal was to relate the building to the historic brick construction of the region, says Nguyen Hai Long, a partner in the firm. Brick construction in central Vietnam dates to the 4th century, when the Champa culture began building Hindu temples in sacred complexes throughout the area, according to Nguyen. The site organization of the studio, with a path centered on the intricately detailed building, recalls the ceremonial layout of the Champa period.
The walls of the studio were constructed by first pouring a concrete frame for the exterior. To respond to the client’s desire that the studio provide shelter but be open to sunlight and cool river breezes, the architects devised a grid of openwork panels. Each wall is divided into 36 squares made up of several patterns of brick screens with various levels of transparency—created by leaving voids in the brickwork—fitted like patchwork pieces to make the larger square.
Masons laid the brick so that the concrete frame would be hidden both inside and out, with the brick sawed to fit around the concrete members. The resulting perforated walls are about 8 inches thick, the length of one brick.
Inside the two-story volume, four concrete columns support a stout 16-inch-thick concrete slab. Because the slab is separated from the brick walls by a 2-foot gap, it forms a tablelike pedestal between the lower and upper levels. A timber frame surrounds the workspace and passes up through the gap between the slab and the exterior wall to extend to a flat glass roof. This wooden matrix houses shelves for display and stairs to the upper level.
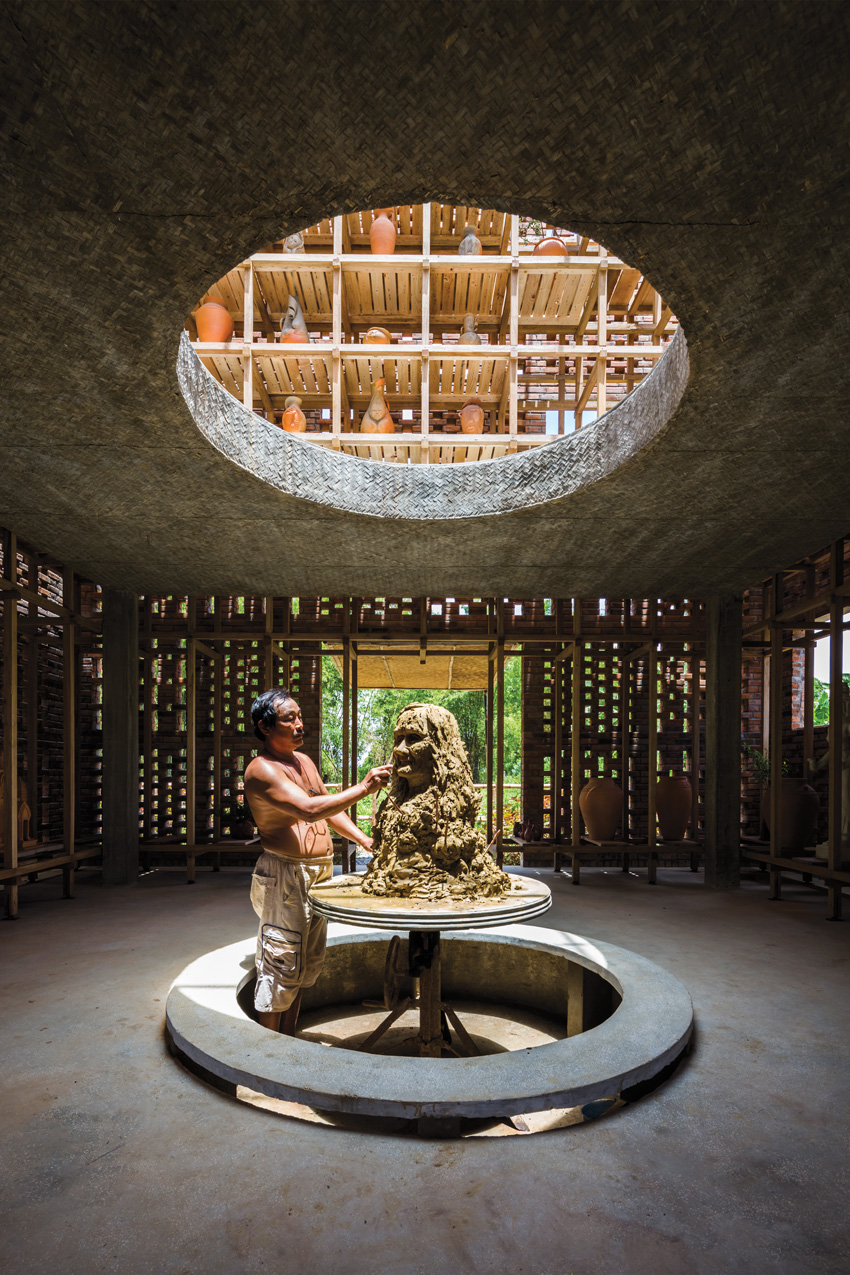
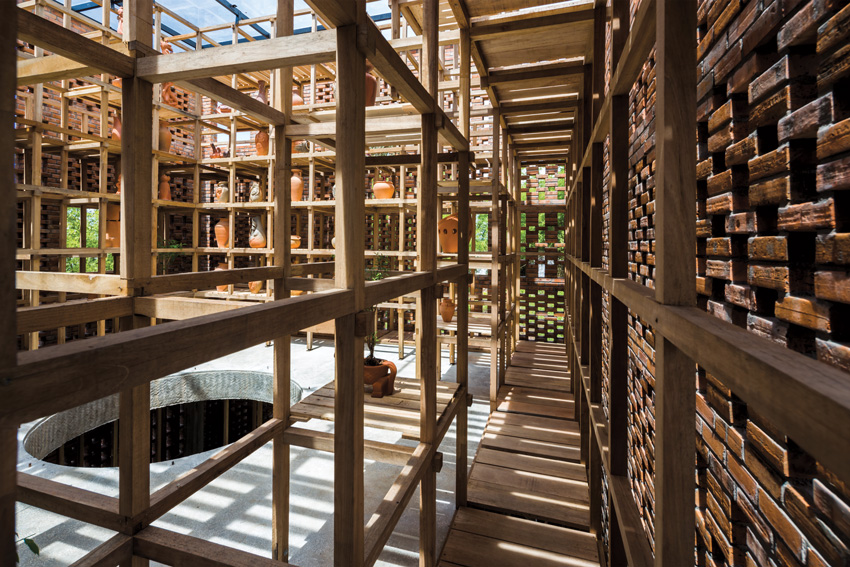
PHOTOGRAPHY: © OKI HIROYUKI
BEHIND THE VEIL
Inside the two-story ceramist’s studio, a stout 16-inch-thick slab is supported on four concrete columns (top). Between this slab and the exterior brick screen, a timber frame extends to a second level and to the building’s glass roof (bottom), housing stairs and shelves for display.
At the center of the ground floor, Le’s potter’s wheel sits directly below an oculus that penetrates the floor slab. Daylight fills the upper-level display space and focuses a Pantheon-like disk of light on the artist’s workspace below.
The elemental purity of the ceramist’s studio, along with the dynamic expression of the Shanghai gallery and the structural elegance of the droneport project, prove brick’s continued relevance. “Great buildings often go through considerable complexity to reach simplicity,” says Foster + Partners’ Sagoo. In selecting materials for these three projects, the designers found that simplicity in a humble and age-old material.
Michael Cockram is a freelance writer and director of Bowerbird Design in Fayetteville, Arkansas.