Integrated Approaches to Control Moisture in Buildings
Concrete Foundation Waterproofing
Foundations are necessarily in contact with the earth, which is known as a source of water infiltration into buildings. There are certainly some site-engineering approaches for draining water away from a foundation or adding drainage systems around the outside of a building, and their use is common. However, it is also common to provide some type of waterproofing system to keep any water from passing through the concrete. However, achieving that can be challenging since the formation of cured concrete produces a myriad of air gaps, holes, pores, capillary tracts, and other internal voids. Further, concrete shrinks in size as it cures, although if it is cured properly, that shrinkage can be kept to a minimum. Nonetheless, visible cracks or much less-visible microcracks can occur. The end result is that while concrete may appear strong and impenetrable on the surface, it actually ends up quite porous due to the variety of openings and voids inherent within it. This porosity means that water can penetrate into and even through a concrete structure, causing water seepage that is usually not desirable.
Over time, the inherent water permeability limitations of concrete may get more pronounced in several ways. First, any exposed surface can be physically damaged due to physical force, abuse, weather, etc. Such physical damage can cause the surface of the concrete to crack or break, exposing the inner aggregate and creating a rough surface that is vulnerable to moisture absorption and further deterioration. Secondly, the permeable nature of concrete can allow not only water but also soluble chemicals to penetrate into the foundation and cause deterioration of the concrete or corrosion on any metal components embedded in the concrete. This can include reinforcing steel, anchors, sleeves, post supports, angles, or any other metal that is used with concrete structures.
Surface treatments: In any of these conditions, concrete deterioration fueled by moisture can produce aesthetic, functional, or structural problems if not treated properly or prevented. To overcome these issues, there are several approaches. A common one is to use a surface coating to waterproof the concrete, thus keeping not just water out but chemicals and other harmful substances too. This approach is based on applying a protective coating either in liquid or sheet form over the concrete. Either one has an inherent limitation, however, in that they are not integral to the concrete but rather an applied layer on top of it. This means their success is entirely dependent on the workmanship of the installation and ultimately the full adhesion to the concrete surface to prevent it from separating and peeling off. This can be a particular challenge in locations where the concrete shape is irregular or where different sections meet and the coating needs to conform to multiple underlying shapes.
Admixtures: A different approach to waterproofing concrete is the use of specific chemical admixtures to make the waterproofing completely integral to the concrete itself. Admixtures, in general, have been used for decades to improve the performance of concrete in a variety of ways. Their first widespread use was to extend the temperature range that concrete could be poured without fear of freezing. They also became common to improve the workability of concrete through plasticizers that allowed less water in the mix while still retaining adequate slump (formability). Building on this proven success, some specific admixtures have been developed for waterproofing concrete that are based on filling and sealing all pores, small cracks, and openings with solid crystallized material. Referred to as crystalline technology or crystalline concrete, it has achieved some impressive results.
Crystalline concrete: In essence, crystalline technology takes advantage of the natural and porous characteristics of concrete. When a cement particle hydrates, the reaction between water and the cement causes it to become a hard, solid, rocklike mass. The reaction also generates chemical by-products that lie dormant in the concrete. Crystalline technology adds another set of chemicals to the mixture. With water as the catalyst, specific chemical admixtures are used that react with the natural by-products of cement hydration (calcium hydroxide, mineral salts, mineral oxides, and un-hydrated and partially hydrated cement particles). When these two groups, the by-products of cement hydration, and the crystalline chemicals are brought together in the presence of moisture, a chemical reaction occurs. This reaction forms a nonsoluble crystal that grows to form a web-like crystalline structure within the interconnected pores and other voids in concrete. In this way, the crystalline structure becomes a permanent, integral part of the concrete itself. Because it is nonsoluble, it fills the voids, cracks, capillaries, pores, and other openings to make the concrete impermeable, thus preventing the ingress of water and other liquids even under strong hydrostatic pressure. That means it also protects against liquid-borne chemicals that can deteriorate concrete or corrode steel reinforcing, even in harsh, aggressive environments or under high hydrostatic pressures.
Integral crystalline technology products are manufactured in the form of a dry powder compound consisting of portland cement, very fine treated silica sand, and selected chemicals. It is the chemicals that react with the by-products of cement hydration to produce the nonsoluble crystalline formation. Specific formulations are produced for application either as a coating material, concrete admixture, or dry shake product applied to the wet concrete and troweled in. It can be incorporated into a structure as it is being constructed or later on in the life cycle as a maintenance material that will further enhance its durability. As such, crystalline concrete is a viable method for waterproofing building foundations that can be used as a stand-alone system or as part of an integrated waterproofing system incorporating surface membranes. Crystalline waterproofing can reduce costs, accelerate construction schedules, and be used where other waterproofing methods or assemblies are difficult or impractical.
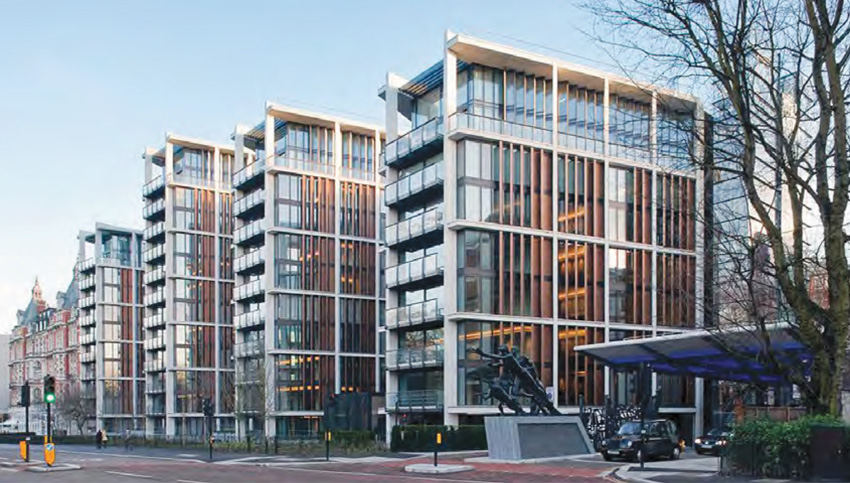
Photo courtesy of Xypex Chemical Corporation
One Hyde Park, designed by Rogers Stirk Harbour + Partners, is tagged as ‘the most luxurious address in London.’ Crystalline concrete was selected for this project as a waterproofing and protection solution for the three-level basement slab and wall areas, attenuation tanks, podium slab, and penthouse roofs. It was also used for the traditionally cast and post-tensioned concrete, while also being utilized as a remedial solution for areas adjacent to the existing structure.
Wood-Framed Moisture Protection
Designing and constructing wood-framed buildings commonly involves several different trades working on the roof and wall systems. As we have already noted, these are places where water- and air-borne moisture can infiltrate a building and cause damage. This is the reason that building codes like the International Building Code (IBC) and the International Residential Code (IRC) require a water-resistant barrier (WRB) on the exterior side of wood sheathing. Achieving that is commonly done with a field-applied material, such as rolls of housewrap or spray, on material over the exterior sheathing. This approach necessarily relies on the skills and capabilities of the installers to achieve a truly continuous, water-resistant solution.
Integrated engineered-wood sheathing: In recent years, alternative products have emerged to address the need for a WRB layer that can be consistent and reliable with less susceptibility to variable labor and field conditions. Referred to as integrated engineered-wood sheathing systems, these products are used as structural sheathing in single-family, multifamily, and light-commercial Type 5 construction projects for non-fire-rated roof decks and exterior walls assemblies. They also have additional properties that have been shown to reduce the risk of moisture damage in several ways. First, and perhaps most significantly, a WRB layer is manufactured (not laminated) in the factory onto the exterior surface of these engineered wood panels. This eliminates the need for designers to specify a separate layer and gives construction crews one less thing to install. Second, integrated engineered-wood sheathing effectively addresses the seams between sheets with a high-performance tape that creates full contiuity of the WRB. Third, states like Oregon or elsewhere are requiring rainscreens or enhanced drainage planes behind the final cladding (siding, masonry, etc.). In response, these products have been tested per the applicable ASTM standards and shown to meet the code definition of an enhanced drainage plane with 90 percent drainage efficiency. Finally, due to the integrated engineering aspect of these products, they not only provide full WRB protection, but they also qualify as an air barrier to keep out unwanted air infiltration. This air-barrier quality means that it helps prevent airborne moisture from penetrating into a construction assembly too.
In order to achieve the needed full protection and continuity of a WRB and air barrier, proper taping and flashing is needed around window and door openings, penetrations, and junctions of different assemblies (wall/roof, wall/foundation, etc.) This can be accomplished in one of two ways:
Tape and flashing products: High-performance tape products that are made from an advanced composite acrylic provide superior adhesion, aggressive bonding, and resistance to ultraviolet (UV) light exposure. Some of these tapes are especially formulated for use with integrated engineered-wood sheathing for full compatibility and should be specified as a coordinated system. Such specialty tape can use a pressure-activated formula with a specific viscoelasticity that provides the right balance to form an ionic bond with the WRB layer. Such tape can also be manufactured and specified with four distinct layers including slip resistance (since it’s used in roof applications), UV protection, a bonding layer, and eight mils of acrylic adhesive.
In addition to sealing the joints of integrated sheathing panels, this tape can be used as flashing to cover the exposed framing and face of the sheathing on window and door heads, jambs, and sills to create a continuous protective layer that seals out water and air around these openings. Such flashing tape is commonly available in 4- and 6-inch widths in both a straight flashing formulation and a stretchable version. The stretchable tape is also available in 10-inch widths to provide the appropriate coverage in a single installation over the full depth and perimeter of the openings as opposed to piecing multiple tape segments together. The fully flashed opening is then ready to receive a window or door unit, which may then be further counter flashed over or around integral flanges using the same flashing tape. In either case, the tape is pressure rolled into place using handheld rollers to assure a complete and uniform bonding. If stretchable tape is used, it is particularly well suited to irregular-shaped window openings or even curved/rounded openings.
Liquid flashing products: Much like other liquid waterproofing products, liquid flashing formulated for integrated engineered-wood sheathing can be applied to create a continuous, seamless condition around windows, doors, and other openings. It is also particularly well suited to variable surface conditions, such as wood to masonry transitions (i.e., wall to foundation), round, curved architectural details, or parapet walls. It is common for products like these to be hand-applied using a towel or a brush onto a surface, such as sheathing, framing, metals, etc. Once applied, it is intended to dry to a complete and continuous water- and air-proof seal around all portions of the condition being flashed. Since it is usually the thickness of the application that is important for quality control, applicators likely need to be trained in the installation of these flashing products, and on-site quality control becomes very important. Such liquid flashing products can also be stronger and higher rated than some tape systems, making them particularly suitable for upper stories in multifamily buildings subject to higher wind ratings.
Part of the effectiveness of liquid flashing is that it can be applied with optimal viscosity to flow easily into irregular shapes and surfaces, such as recessed windows, corners, roof valleys around chimneys, and pipe penetrations. Typically, such flashing can be weather resistant and tack free in as little as 20–40 minutes. Even better, since it is available in a moisture-curing formula, the liquid flashing membrane can bond and cure in otherwise unfriendly site conditions, including wet weather and damp substrates. At least one is backed by a 180-day exposure guarantee, meaning that if it remains uncovered for up to six months, it will still perform. In the end, it is usually the architect’s preference whether to use liquid-applied flashings or other systems, but the versatility and durability of these products cannot be ignored, particularly for long-term solutions on larger and taller buildings.
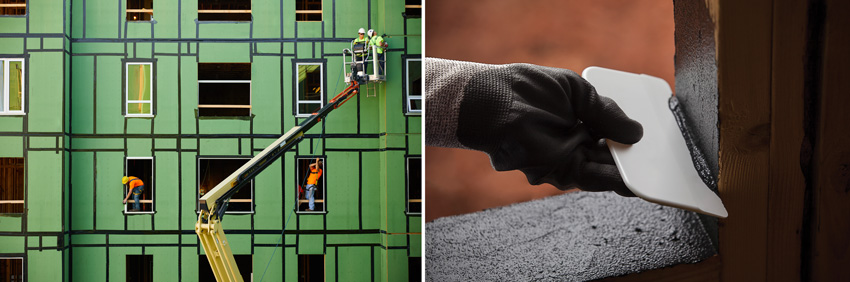
Photos courtesy of Huber Engineered Woods © 2017
Integrated engineered-wood sheathing provides a continuous defense against water in wood-framed construction when paired with self-adhering tape and liquid flashing.
Notice
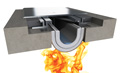
www.inprocorp.com
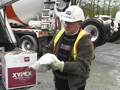
www.xypex.com
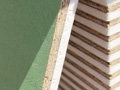
InsulateYourBuild.com