Focus on Wood
Starts and Stumbles: The Rocky Road to Europe’s Ambitious Timber Construction Targets
BY KATHARINE LOGAN
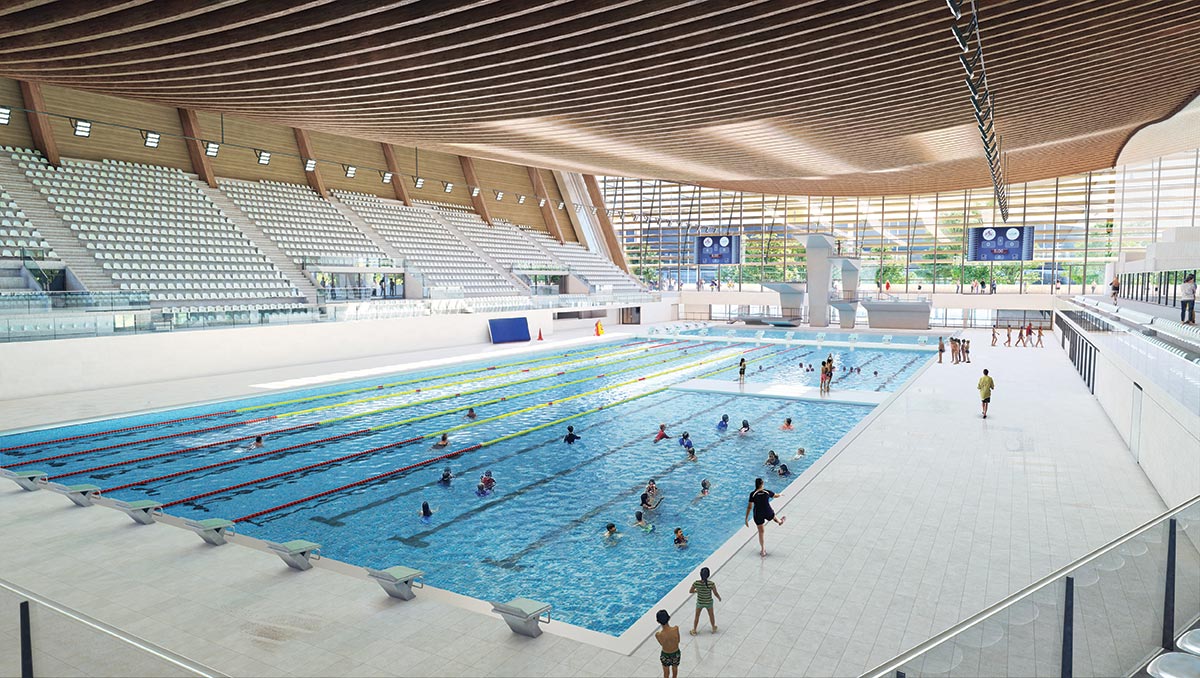
Image © PROLOG
The aquatics complex by VenhoevenCS and Ateliers 2/3/4, for the 2024 Olympics in Paris, will have a vast timber roof.
Europe is a clear leader in mass-timber construction—home to 60 of the world’s 84 tall timber structures (eight-plus stories), according to a 2022 count by the Council on Tall Buildings and Urban Habitat—and there’s no shortage of ambition to scale up. With an eye to the material’s renewable and carbon-storing properties and its fit with prefabrication and circular economies, European jurisdictions have introduced a slew of initiatives to increase building with wood. But, while these measures are important steps, in practice major obstacles remain.
Policies and programs introduced to date are widespread and wide-ranging. In the Netherlands, 32 municipalities and over 80 companies and agencies in the Metropolitan Region of Amsterdam (MRA) have signed a Timber Construction Covenant, agreeing to use wood as the primary structural material for at least 20 percent of residential buildings by 2025. In Finland, targets for the use of wood in public construction aim to reach 45 percent of market share by 2025. In France, public buildings, including those constructed for the 2024 Paris Olympics, are mandated to use bio-based materials. The requirements are set at 25 percent of major refurbishments and new construction by 2025, increasing to 50 percent by 2030. France also mandates life cycle embodied-carbon analysis for residential buildings, schools, and select commercial-building types, with limits set to tighten in stages. In Sweden, life cycle embodied-carbon calculations are a precondition for planning permission for new buildings, with limits on embodied carbon likely by 2027. At a supranational scale, the European Commission is considering an EU-wide requirement to measure construction materials’ life cycle carbon emissions; also contemplated is a provision for EU member states to create national building-renovation plans setting out how they will reduce embodied carbon.
So far, though—apart from small-scale residential projects, which are not going to densify cities using bio-based materials at scale—progress is still a series of starts and stumbles. “There’s a lot of timber plans, but not nearly as many timber-construction sites,” says Mathew Vola, director of sustainable development in the Amsterdam office of Arup. The office provided a range of engineering services to two recent local timber developments: HAUT, a 21-story residential building (with concrete foundation, basement, and core) designed by Team V Architecture and completed in 2022; and Mediavaert, DPG Media’s 495,000-square-foot headquarters (also by Team V), now under construction and set to become Europe’s largest timber-hybrid office building. But even with the MRA’s pro-wood covenant, Vola can count on one hand the number of large-scale timber projects that are actually going up in the Netherlands. “Everyone wants to do timber, but somewhere along the line the ambition gets lost,” he says. “In our experience, it always has to do with the business case.”
While the specific obstacles that burden timber’s business case vary from jurisdiction to jurisdiction, from his experience in the Dutch context, Vola identifies three general sticking points. The first is a lack of financial incentives for making the switch from concrete and steel. For example, in the Netherlands, the cement and steel industries are both exempt from carbon tax: “You could argue that this exemption amounts to a subsidy for those industries,” Vola says.
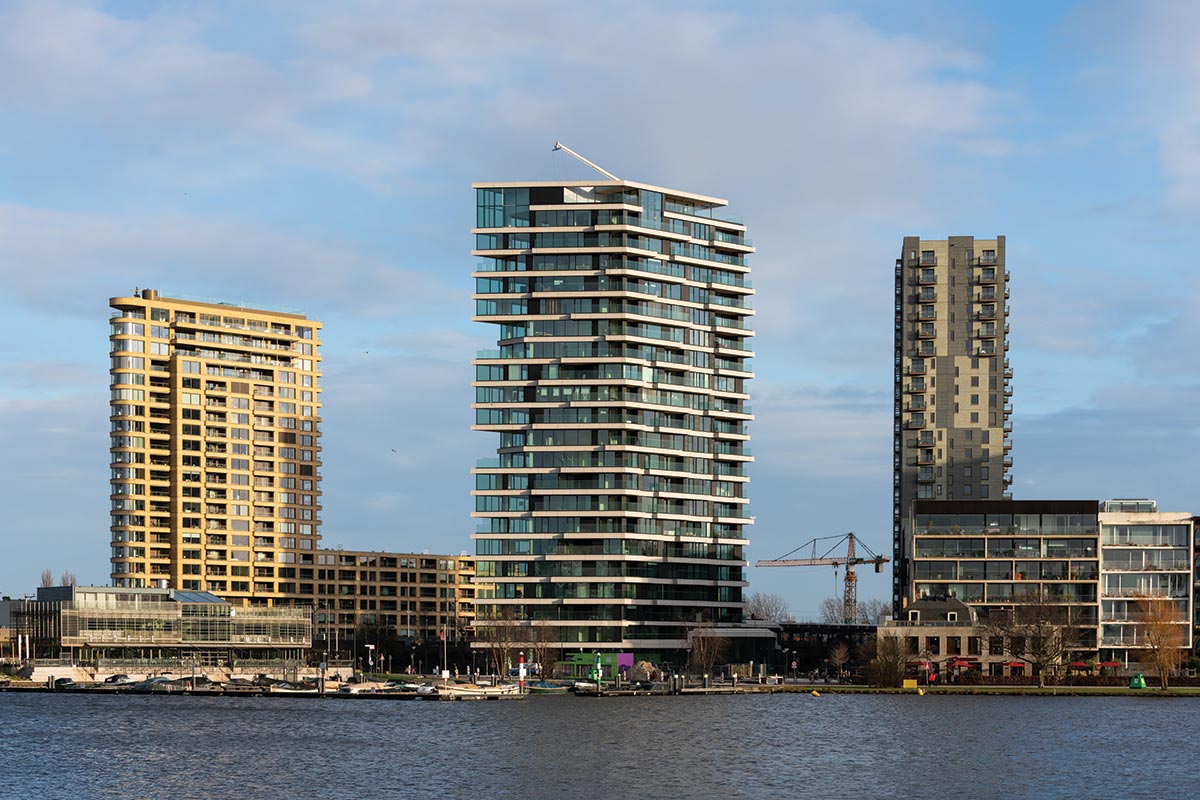
Photo © JANNES LINDERS
HAUT, a 21-story residential building in Amsterdam, is one of relatively few large-scale timber projects in the Netherlands.
It’s difficult to make headway against concrete’s advantages in Finland too, according to Mikko Leino, CEO of Helsinki-based mass-timber fabricator and builder Puurakentajat Group: “Big construction companies often have links to, or ownership of, concrete and cement integrated into their balance sheets,” he said in a recent webinar hosted by the Swedish office of the Programme for the Endorsement of Forest Certification (PEFC). Without incentives, “it takes a long time to turn that ship.”
In the UK, the advantaged competitor is a bit different: there are greater incentives to burn wood than there are to build with it, says Andrew Waugh, founding director of London-based Waugh Thistleton Architects. “The use of wood for construction is taxed and unsubsidized, whereas its use for fuel is subsidized and untaxed. Most of the trees that are cut in the UK are burned.”
The second burden on timber’s business case is supply bottlenecks. The European cross-laminated timber (CLT) market reached 1.6 million cubic meters in 2022, and is expected to reach 2.9 million by 2028, according to a report by the International Market Analysis Research and Consulting (IMARC) Group. But, for the moment, says Vola, demand exceeds supply. Counter-intuitively, the solution may lie in further increasing demand. A 2021 policy-gap analysis of programs promoting timber construction in Norway, Sweden, and Finland found a widespread expectation among sector experts that increasing demand for timber components will stimulate competition in the market and help smooth out supply-chain inefficiencies and shortfalls. In Amsterdam, says Vola, “one of the things the MRA is trying to achieve is a more constant demand for these factories to run.”
The third constriction is a shortage of education among industry players. “You can design timber buildings that are just as safe, just as water-resistant, just as acoustically friendly as concrete buildings—better, even,” says Vola, “but we don’t have enough timber knowledge widespread in the industry to deliver them.” Because of wood’s low weight and sensitivity to moisture, light, and fire, it’s more dependent on careful detailing and construction practices than are concrete or steel. “In a first generation of fairly poorly designed timber buildings, you see quite a number of damage cases,” says Vola. Insurers see them as well. “That’s perceived as risk. Risk translates to added cost.”
Closely related to the need for education is a need for standardized solutions. Technical issues are being resolved project by project, says Lars Tellnes, one of the authors of the Scandinavian policy-gap analysis, but “codes are developed on standards.” This ad hockery feeds the development of diverse and, in some cases, unnecessarily stringent, regulations, which translate into project costs and sector uncertainty. “Apparently, wood burns differently in Turku from how it burns in Helsinki,” Leino says wryly. He describes uneven regulations and, especially, uneven interpretation of them as “a huge attitude issue.”
In England, the attitude issue is compounded by the legacy of the fatal 2017 fire at the Grenfell Tower, a 24-story concrete structure with combustible envelope components. New regulations in response to the tragedy ban combustible materials in external walls of residential buildings over six stories. The inclusion of mass timber among the banned materials has changed the perception of industry members, insurers, and to some degree the public “to a ‘Three Little Pigs’ mentality,” says Waugh, which he describes as an obstacle to timber construction: “In the rest of the world, codes are changing to promote mass timber’s use. That’s just not happening in the UK.”

Photo © JAKE CURTIS
Waugh Thistleton Architects, designer of a six-story mass-timber office building in London, is collaborating on efforts to create prewarrantied wood-construction details for both the residential and construction sectors.
To help the European timber-construction sector through these growing pains, a number of new initiatives are under way. In a project funded by Built By Nature, a philanthropic organization, Waugh Thistleton is
collaborating with University College London and Buro Happold to build confidence in timber construction among UK insurers, code officials, contractors, and clients. Focusing on residential construction up to six stories high, the team is developing a pre-warrantied system of 25 building details along with a suite of specification guides covering fire safety, water management, and construction practice. The resource, to be made available as an open-source document, “will ensure that mass-timber residential buildings can be built to competent standards and will be insurable and able to obtain mortgages,” says Waugh, “hopefully kick-starting low-carbon timber development across the UK.” In another Built By Nature–funded initiative, Waugh Thistleton is collaborating with a diverse consortium, led by engineering consultancy Elliott Wood, to design similar systems for the commercial office sector. These will be made available internationally, including in the United States.
Under the auspices of Build-in-Wood, an EU-funded program based at the Danish Technological Institute, seven cities from across Europe, representing a range of sizes—capitals Amsterdam and Copenhagen, a borough of London, two mid-size cities (Trondheim, Norway, and Brasov, Romania), and two smaller ones (Innsbruck, Austria, and Trento, Italy)—have identified focus areas for boosting timber construction in their jurisdictions. Priorities include strengthening local wood value chains, enhancing training and regional knowledge, and facilitating cooperation between industry and municipal administration. Additional goals include simplifying building codes and promoting timber-positive public-sector procurement. Some of the participants emphasize urban densification through adding new stories onto existing buildings, and facilitating circular economies for wood construction. Build-in-Wood is supporting these seven cities through a program of detailed context analyses, workshops, and implementation guidance. A publicly available policy catalogue, developed in partnership with Bucharest-based planners Urbasofia, presents and analyzes policies and best practices for prioritizing wood in multistory buildings, and will eventually incorporate results from the early-adopter cities. Build-in-Wood has also established an international knowledge-sharing network, with 1,300 members and growing.
Meanwhile, as companies’ success increasingly links to environmental, social, and governance (ESG) factors, private-sector investors are seeing the value of wood in a new light, says Vola, one in which the material’s additional costs bring in additional benefits. “Looking to the future, a carbon-friendly timber building is more interesting to investors than a polluting, non-circular concrete one,” he says. “The hope is that, as this goes through, it does put a more positive spin on the value of timber construction. The business case does make sense.”