Designing for Multifamily Housing
TOTAL FLOOR SOLUTIONS
Floor construction in multifamily housing of all types is a significant factor in the way people perceive the quality and comfort of a living unit. It also impacts fire resistance, acoustics, longevity, appearance, and the budget. Let’s turn our attention to some of the important decisions that can impact this critical aspect of construction of multifamily buildings.
Composite Floor Structures
When designing multi-story multifamily buildings, there are a number of ways to provide the floor structure. One that has been gaining in popularity is the use of composite steel deck and concrete floor systems, which combine features beneficial to any multifamily housing design. Architects have been particularly interested in this system when they recognize that floor type selection encompasses more than structural design. Floors influence space design and convertibility, sound transmission, room temperature, and fire resistance. Composite steel and concrete systems address all of these factors favorably. Further, they install quickly to help keep schedules in line, integrate with any type of support frame, and are completely adaptable to MEP pass-through needs. From a ceiling finish standpoint, composite steel and concrete systems can be exposed and direct finished or covered with a ceiling material of choice.
The key to the composite system is the metal deck that connects to the structural steel frame and receives reinforced concrete above it. The size and height of the metal deck profile directly influence its structural strength and maximum span capabilities. A fairly shallow system with a metal deck on the order of 2½ to 3½ inches in height and a total height of 4½ to 7 inches with the concrete in place can typically span 12 to 25 feet. Taller composite deck systems on the order of 8 to 11½ inches are capable of spanning 25 to 36 feet. These are dramatically thinner floor systems than other conventional floor framing systems of wood or steel, which can require two or three times these thicknesses for similar structural span capabilities. It should be pointed out that other systems may also require additional thickness to match the two-hour fire rating of the concrete and steel composite system. Also, in taller systems, the composite system can be applied to the bottom flange of structural steel beams, thus creating an “upset” beam condition, eliminating the beam from being exposed down into the living space. Alternatively, a composite beam that incorporates specifically fabricated steel profiles with structural concrete fill can be incorporated with similar low-profile capabilities.
The implications for using this type of system in multifamily buildings are numerous. We have already noted the very favorable span-to-depth ratio compared to joist systems, which can translate into fewer supporting columns or walls. The shallower floor system depth provides designers with greater control of the floor-to-floor heights and the overall building height, allowing either higher ceilings or a potential increase in the number of building stories where zoning ordinances limit overall building height. From a usability standpoint, acoustics can be enhanced such that the sound transmission class (STC) and impact insulation class (IIC) results can be a very favorable rating of 60 or more. Fire-resistance of the non-combustible system can achieve two- or four-hour ratings (unprotected), which makes it ideal for many multi-story settings. Placement of mechanical, electrical, and plumbing features are simplified using cast-in-place sleeves or reinforced slab beams at larger openings such that no concrete sawing or hole-cutting is required. Further, in some deck systems, the profile forms a series of plenums that are available for conduit, small light fixtures, plumbing lines, sprinklers, and other items.
Since this type of composite floor system can be customized and installed by steel and iron workers, some manufacturers offer specialty support services for both design and construction. This can include determination of shoring needs (if required) and specification of deck, concrete, and slab reinforcement requirements based on construction and in-service loading and floor penetration requirements. On-site training can also be provided for quality control covering the use of specialized tools and installation procedures. Overall, this integrated approach helps coordinate efforts between the design team and deck manufacturer so that job-site deliveries and installation can meet the project schedule.
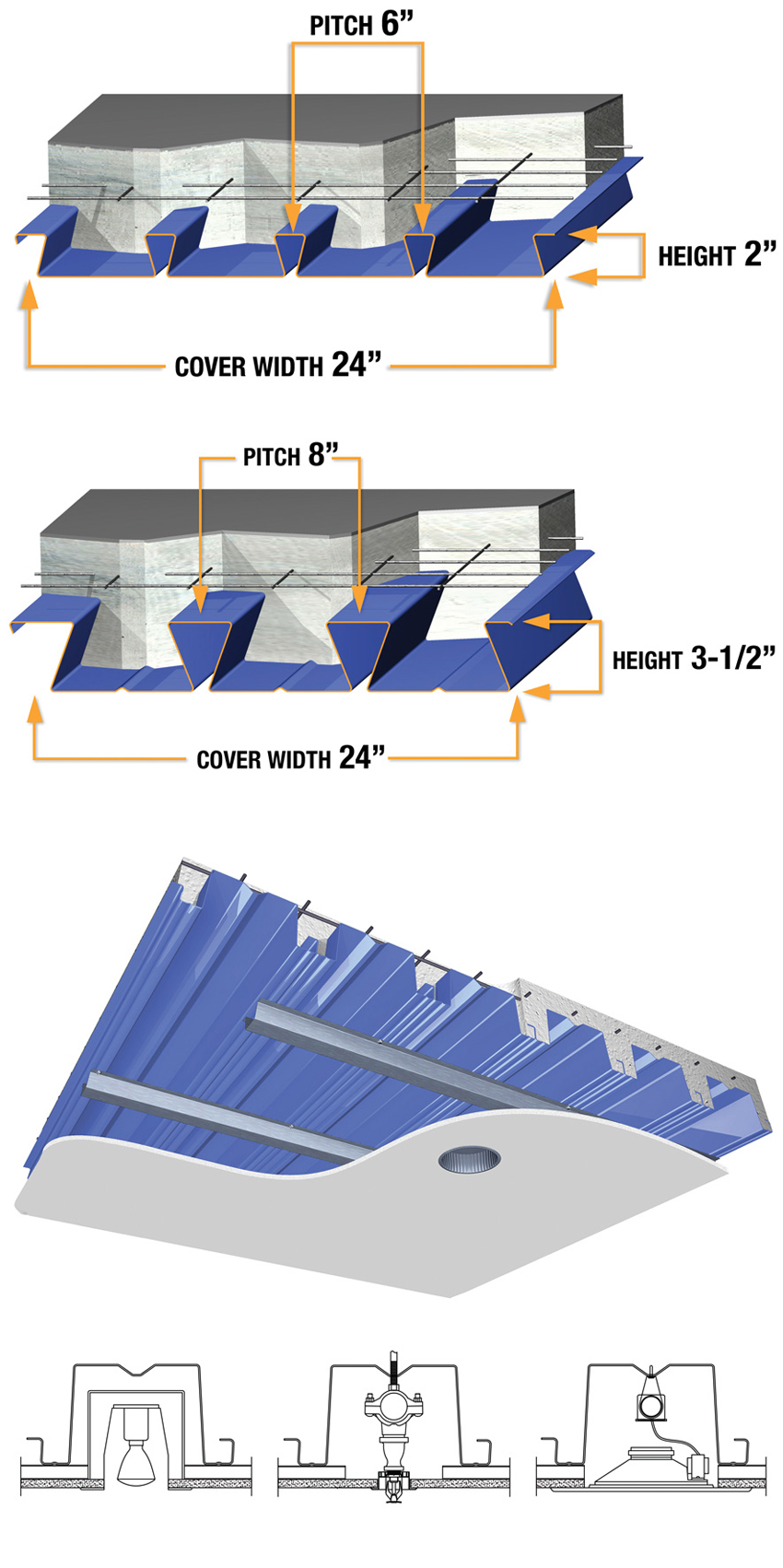
Images courtesy of New Millennium Building Systems
Composite concrete and steel floor systems gain their strength from the shape and height of the metal deck that receives the concrete. In some profiles, the underside spaces are large enough for small utilities to be run, such as lighting, sprinklers, or sound components.
Flooring Underlayment
Once the floor structure is in place, it is important to consider selection of an underlayment that, installed between the structural surface and the finish flooring, can add real value to the overall floor assembly. Underlayment improves resilient floors, such as vinyl or linoleum, but also works particularly well under hardwood, engineered wood, laminate, luxury vinyl, and tile floors. Flooring underlayment, typically sold in rolls or sheets, can be specifically engineered to achieve particular goals. These may include improving acoustics by deadening sound in a room and to rooms below, helping manage unwanted moisture, and helping ensure a smooth and warrantable surface for the installation of the finish flooring. In addition, some underlayment products are designed with sustainability in mind and are carefully manufactured to meet the most rigorous standards for indoor air quality (IAQ).
Careful selection of a particular underlayment can be an important factor in multi-family housing when aiming to minimize sound transmission between floors, whether from people walking on the floor, from items that bounce or drop, or from loud music or TV—all sounds that can annoy downstairs neighbors and, possibly, lead to complaints from tenant to landlord. This is true for any type of flooring but particularly for hard surface flooring. When looking to install a floor assembly that can achieve “less noise” between floors, look for acoustical underlayment that has been tested for and carries good STC and IIC ratings that exceed the minimum requirements.
The ability of an underlayment to address moisture management helps protect the finish flooring from moisture that may be released from the subfloor. That moisture might come from wood or concrete that is not 100 percent dried when the flooring is laid down. Some underlayments are engineered to prevent moisture from pushing up and causing damage, separation, or mold growth under the flooring. An underlayment that is designed to address moisture management may also have the ability to wick moisture to the edges where it can evaporate over time, as long as the source of the moisture is addressed.
In cases where a fire-rated assembly is important, specifying an underlayment with attributes that enhance the performance of the floor can benefit the new floor, from installation all the way through the life of the floor. Common practice, particularly where a fire-rated assembly is required in a wood framed building, is to embed a sound control mat on top of the subfloor before gypsum concrete is poured. There are also acoustical underlayments that do not need to be embedded in the gypsum concrete but rather placed on top beneath the finished flooring, which provide the needed sound control and potentially reduce project costs. Certain fiber underlayments will not only help dampen sound but also add a variety of performance-enhancing benefits to the base of the flooring material, without impacting the fire rating.
For projects designed to meet green building standards, there are underlayments available that combine many of the aforementioned attributes and are made from materials that address environmental concerns. In fact, some resource-friendly underlayments are third-party certified to be made entirely or substantially from recycled materials, which can be used to contribute to earning LEED credits in the Material and Resources category. Some of these products may also be certified as manufactured from low-emitting materials, satisfying criteria for contributing to earning credits in the LEED category of Indoor Air Quality.
Underlayment products are available in a variety of materials, including rubber and textiles that can meet all of the above needs for multifamily projects. For multifamily housing projects where multiple types of hard surface floors will be used, it can be a very good choice to select a single universal underlayment that can be laid under all of them. Universal rubber underlayment made from 100 percent virgin latex rubber, for example, can have a well-formulated mix of physical properties that make it suitable for use under a variety of flooring choices. If the project has flooring that needs to be installed in a variety of ways, universal underlayment is available that can also be installed in numerous ways. It can be floated, nailed, stapled, single-glued or double-glued, thus further enabling use of one product across a project. Some of the properties to look for in such universal underlayments include thickness, density, and thermal resistance (measured as an R-value). If luxury vinyl is being used, then it is also a good idea to specify an underlayment with a compression set of at least 15 or 16 percent, which helps minimize impressions and indentations. As for acoustical performance, the IIC and STC ratings are generally excellent with this type of universal underlayment. For example, one product, when tested in an assembly made up of a 6-inch concrete subfloor, no ceiling assembly, and luxury vinyl planks covering over the acoustic underlayment, resulted in an IIC-52, a rating that exceeds the standard for many high-rise installations. That underlayment also carried a Green Label Plus Certification for Low-Emitting Materials and is recyclable at the end of the underlayment’s useful life.
A second excellent choice of material for high-performing acoustic underlayment is one made from recycled textile fibers. This type of product is designed specifically for use under glue-down or nail-down hardwood and engineered wood floors. In addition to dampening impact noise and decreasing airborne sounds from traveling to the room below, it also protects flooring from potential plank gapping. A premium upgrade is found in an acoustic and insulating pad designed especially for floating wood and laminate floors. This type of underlayment has superior acoustic capabilities, is available VOC-free, and can contain 94 percent post-industrial/pre-consumer fibers. This premium textile-based product has filaments that are randomly air-laid, creating a capillary effect to cushion the floor, absorb sound, and help make laminate floors sound more like real wood. The underlayment can also use the capillary effect to absorb and wick moisture away to the edges of the flooring where it can be released to the air.
Regardless of the type of product specified, acoustic underlayment enhances the performance of the overall floor assembly in multifamily housing units. The choices available address the varying needs of specific types of floors or buildings. In multifamily housing projects where sound control between floors is important, acoustic underlayment can make a very noticeable and positive difference.
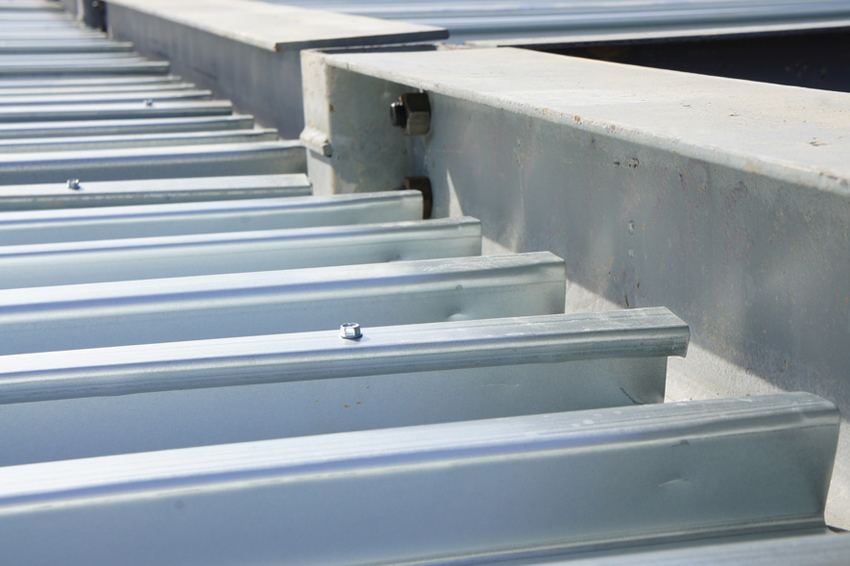
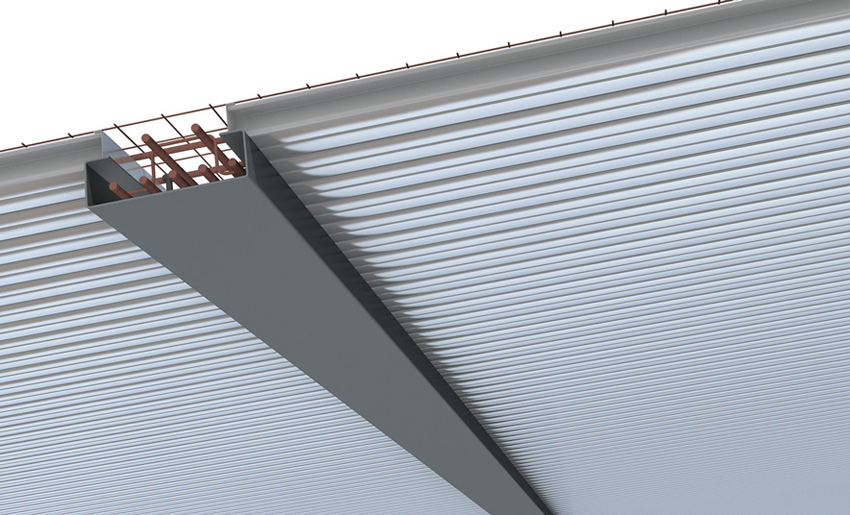
Images courtesy of New Millennium Building Systems
Composite floor metal deck systems can be designed with “upset” structural steel beams or with specially fabricated composite steel and concrete beams.
Notice
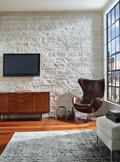
www.eldoradostone.com/modern
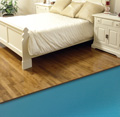
www.mpglobalproducts.com
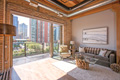
www.nanawall.com/applications/multi-family
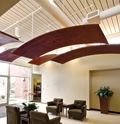
www.newmill.com
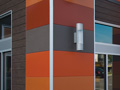
www.xtremetrim.com
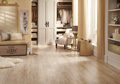
www.tarkettna.com
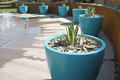
www.tournesolsiteworks.com