Designing for Extreme Environments
Design Solutions
With an understanding of some of the design issues and standards surrounding tornadoes, hurricanes, and flooding, we can turn our attention to some ways to deal with those issues in buildings. The intent is to find ways to appropriately mitigate the effects of the severe weather on buildings and in doing so protect the occupants.
Floodproofing
The primary structural stresses responsible for flood damage on buildings comes from horizontal hydrostatic pressure that builds up on the outside of enclosure walls, thus pushing the walls inward. There may also be some vertical buoyancy forces on the foundation or first floor seeking to lift or float the building. This is compounded in buildings with enclosed sub-grade space, such as a finished basement, where saturated soil hydrostatic pressures and greater buoyancy forces under the basement floor can cause both lifting and collapse of a building. There are certainly some existing buildings that have this problem, but new construction or renovation that avoids any finished or habitable space below the base flood level will help avoid some of the effects of these lateral and vertical hydrostatic forces. Those that don’t address these forces typically find that as water rises up around a foundation, the wall cannot withstand the hydrostatic load and can crack, give way, or collapse inward.
Recognizing the significance of these hydrostatic forces, codes and regulations require mitigation efforts in the design and construction of buildings in flood zones. Specifically, all new construction and substantial improvements of fully enclosed areas (including crawl spaces and garages) below the lowest floor that are subject to flooding must be designed to automatically equalize hydrostatic flood forces on exterior walls by allowing for both the entry and exit of floodwaters. This means that the walls should not be designed to resist the hydrostatic pressure, but to offset it by allowing water to flow into the enclosed space and create equalized pressure on both sides. This is true whether the space is used for parking of vehicles, building access, storage, or any other function. Taken to the extreme, this approach would provide no walls at all, just “stilts” or piers that support the building and allow the water to fully pass under the first floor and around the supporting structure. While that may be appropriate for some design situations, it isn’t for all.
For foundations where perimeter foundation walls are required or desired, a technique known as “wet flood proofing” is common. This approach relies on achieving an equalized water pressure by using permanent openings in the wall with their size and placement calculated to allow the water to flow in and out quickly and evenly. If an equal depth of water exists on both sides of the wall, then the hydrostatic pressure is equalized on both sides, keeping the wall intact. This is regarded as the smart approach to floodproofing a building since it maintains flood storage capacity under a structure and allows the floodwater to take its natural path. Keep in mind that water from a flood could come quickly in multiple directions or slowly in one direction toward a building. Proper flood openings, also called flood vents, need to allow for the automatic entry and exit of floodwater regardless of the direction of flow of that floodwater. In the case of water entering slowly, that flow into an enclosure can cause outward pressure on an opposite or adjacent wall, so water needs to flow out as easily as it flows in. Further, debris is a fact of floods, and it’s something that the design of a flood opening needs to address so the debris passes through the opening and doesn’t clog it.
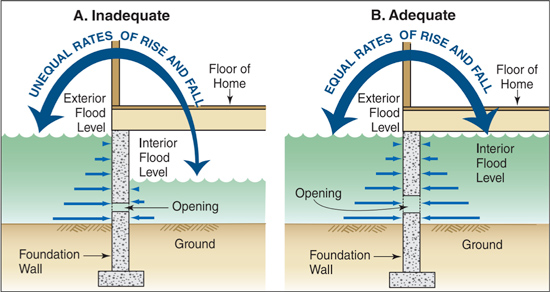
Image courtesy of Smart Vent Products, Inc.
Floodwater pushing against an enclosure wall needs to be equal in height on both sides in order to equalize the pressure on both sides of the wall.
The most critical criterion of a wet flood proofing design is keeping the buildup of head pressure within 1 foot on both sides of the wall. More than 1 foot of head differential on either side of the wall at any time during a flood event is considered a failed flood opening with the potential of the wall itself incurring significant structural damage or collapse. To prevent that from happening, engineered openings are certified to meet all of the codes and standards. ICC-ES Certified Engineered Openings provide passively operated, mechanical devices that float open to create an unobstructed area for floodwaters to travel through without the need for human intervention. In addition, they provide about five times more coverage than a non-engineered opening, which can be things like crawl space air vents or other products intended for other purposes. Non-engineered openings characteristically create unwanted obstructions to water flow and are notorious for collecting debris since they are usually fixed opening products with insect screening of some type. Hence, engineered openings are the only reliable solution.
To be fully effective, flood vents must be installed in at least two different walls. Further, the bottom of all openings must be within 12 inches of the highest adjacent grade directly below the opening to allow no more than 1 foot of head. When using ICC-ES certified flood vents, keep in mind that they must have an unobstructed, 3-inch-diameter opening or larger, and must pass a debris flow test. All flood openings must be passive, and they also must be bi-directional. In addition, designs must comply with the local floodplain management ordinances, as they sometimes go above and beyond the minimum NFIP requirements. As a design assistance resource, manufacturers of flood vent devices can provide a service to review architectural plans and calculate the quantity, placement, and type of flood vent devices for a particular building. They can help to ensure that designs are compliant with FEMA, NFIP, and construction codes, and may have CAD and BIM design files available to be easily implemented into floodplain building designs. Working together, the overall health, safety, and welfare of the occupants within that building or home remain the primary focus by assuring the integrity of the building structure during a flood.
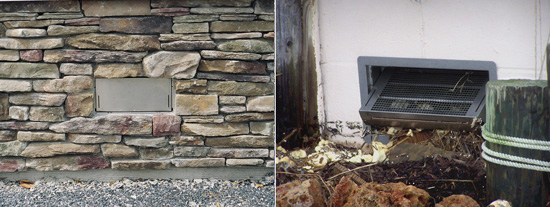
Photos courtesy of Smart Vent Products, Inc.
Insulated flood vents, when not activated, can blend into construction of a perimeter wall (left). Shown on the right, a dual-function flood vent, activated in the open position during a flood event, allows water and debris to flow freely into or out of the enclosed space.
Tornado Resistance
Resistance to both high winds and air-borne debris or “missiles” blown through the air have been shown to be critical in the design and construction of tornado safe rooms. The room construction, including all doors assemblies, needs to meet or exceed the requirements of ICC-500 and FEMA P-361 or P-320 as appropriate. The good news is these door assemblies are readily available from manufacturers who offer products with superior life-safety protection, while still allowing architects a good bit of freedom in design. Certified tornado resistant door assemblies are available in single opening sizes up to 4 feet by 8 feet and in paired openings up to 8 feet by 8 feet. Tornado shutters are also available in sizes as small as 2 feet 6 inches by 3 feet and go up from there. All of the above are available to be either in-swinging or out-swinging. Since these tornado-resistant safe rooms can also serve a dual purpose as community room, gymnasium, classroom, or assembly space, other door criteria may need to be specified, such as fire resistance and handicapped accessibility, which manufacturers can provide. Further, tornado doors, frames, and hardware can in some instances also provide blast-resistant openings, meet the acoustic requirements of LEED for Schools or the Collaborative for High Performance Schools (CHPS), or even meet the Department of Defense UFC 4-010-01 Minimum Antiterrorism Standards for Buildings.
When specifying tornado-resistant door assemblies, the first thing to look for is a single source for a complete package solution, including the frame, door(s), and hardware. This helps with quality control and the coordination of all elements working together toward the desired end of total safety meeting or exceeding the FEMA and ICC-500 requirements. Some manufacturers offer the option of factory installation of multipoint deadbolt systems to further enhance quality control. Such deadbolts can be critical components to the successful performance of the door and can come in a variety of types or styles consistent with other door hardware. Internal or concealed vertical deadbolts travel within the door and are typically reinforced by stainless steel guides. Surface-mounted bolts are also an option in traditional style or can tie directly into surface-mounted lock bodies for doors without mortise openings or pairs of doors without a mullion. Another option, to avoid using vertical bolts that secure the bottom of the door to the floor, is to utilize horizontal bottom bolts that project from the side door edge into the frame about 12 inches off the floor. This avoids costly maintenance efforts, and enhances reliability and aesthetics of the opening. When these doors are used for other room uses in buildings there is also hardware available that allows control of the deadbolts going from a single-point lock during regular use and becoming a multi-point lock during emergency conditions.
Installation of the door assembly in the field is the final but important step in having a tornado-resistant door become part of a safe room or shelter. Some manufacturers offer certified installation courses to contractors because they recognize that the field installation is critical to life safety. With such a certification course, architects and owners can have some peace of mind that once installed in the field, the door assembly performs the same way it does in the testing lab. To streamline field installation, some manufacturers also offer factory installation of the multi-bolt security hardware in the door. When specified by the architect, this ensures proper installation and function of the hardware so that all life safety and functionality is maintained. This option can offer a net savings to the project, as the manufacturer can normally install the device more efficiently in the factory environment than can be accomplished in the field.
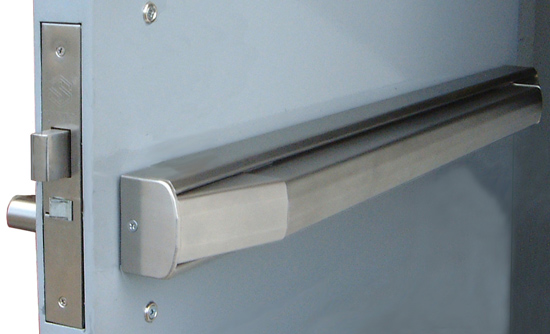
Photo courtesy of AMBICO Limited and Securitech Group, Inc.
Certified and labeled door assemblies include heavy-duty latch/lock hardware and deadbolts in either horizontal or vertical locations, or both.
Notice

www.ambico.com and www.securitech.com

details.mpofcinci.com/extreme-environment-signage/
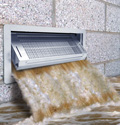
www.smartvent.com