Circular Construction
Learning Objectives:
- Understand the role of construction in carbon pollution and explain how circular practices can reduce such emissions.
- Describe strategies for the reuse of numerous materials, including structural and enclosure components and finishes.
- Identify policy decisions that could further develop the marketplace for circular construction.
- Explore emerging software applications that aim to support circular construction.
Credits:
This course is approved as a Structured Course
This course can be self-reported to the AANB, as per their CE Guidelines
Approved for structured learning
Approved for Core Learning
This course can be self-reported to the NLAA
Course may qualify for Learning Hours with NWTAA
Course eligible for OAA Learning Hours
This course is approved as a core course
This course can be self-reported for Learning Units to the Architectural Institute of British Columbia
View course on architecturalrecord.com »
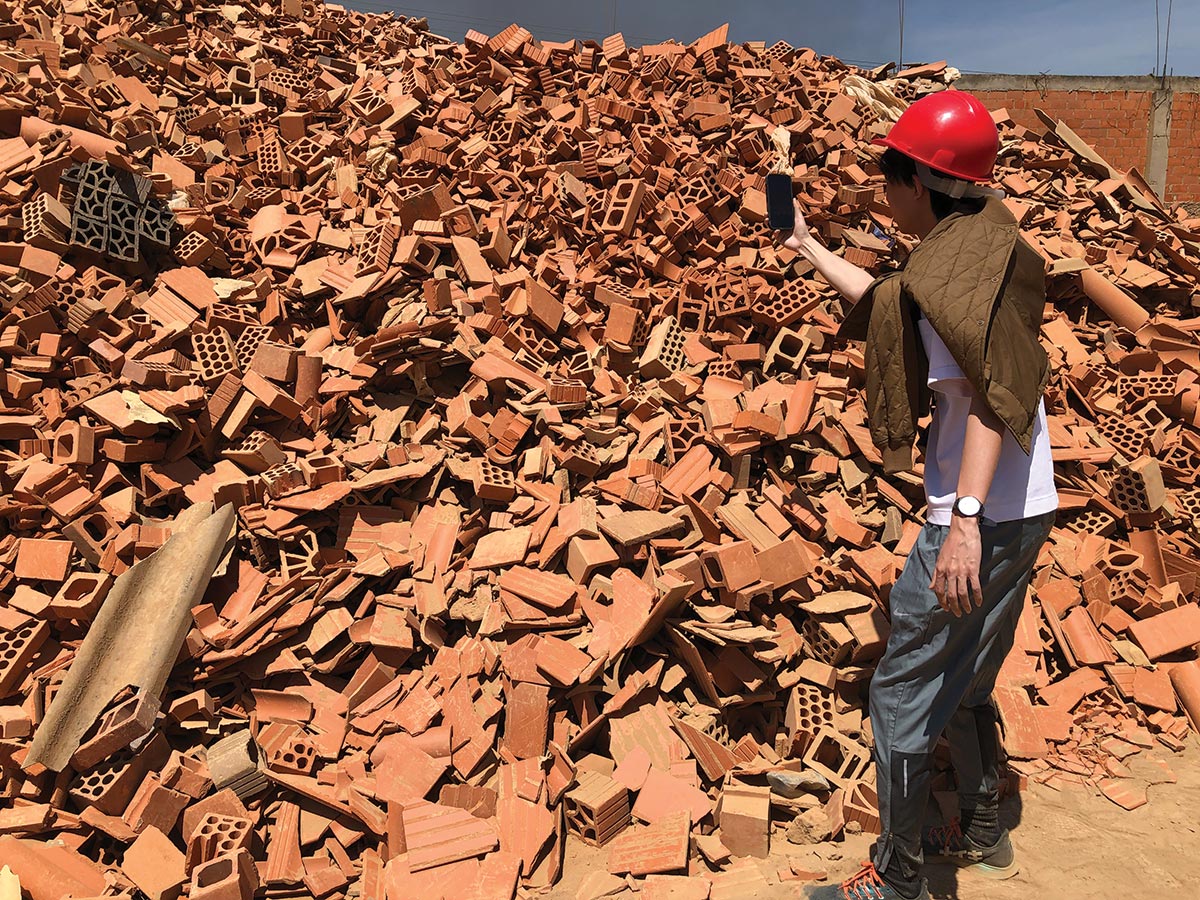
Photo © MIT ODDS & MODS Initiative
An MIT student scans waste bricks at the COMEXTESA factory in Puebla, Mexico.
The building industry has a waste problem. According to the Ellen MacArthur Foundation, a British nonprofit focused on accelerating the transition to a circular economy, upward of 50 percent of demolition-materials waste ends up in landfills. It is a great squandering of financial and materials resources and their associated embodied carbon, with the manufacture of steel and cement alone accounting for over 15 percent of annual global emissions. But there is an alternative path, through the reuse and recycling of building materials in a process dubbed circular construction. That practice is nothing new; the Romans even had a term for it, spolia, for the stone elements taken from old structures and reused for structural or decorative applications. Matters are more complicated in the modern age, with fine-tuned building systems and rigorous codes; and, with global supply chains geared toward take-make-waste (or linear) models, optimal logistical infrastructures to deliver circular-construction projects at scale are often lacking. However, designers and educators are exploring different avenues to utilize these mountains of debris, and are developing design strategies to reduce waste in the first place, such as adaptive reuse and design for longevity or for ease of disassembly.
Arup, the global engineering giant, is no stranger to developing novel solutions for seemingly intractable problems. In 2022, the firm, in collaboration with the Ellen MacArthur Foundation, launched the Circular Building Toolkit, which offers designers a comprehensive framework to reduce the use of virgin and nonrenewable products and improve material efficiency, among other strategies. For Arup Americas chair Fiona Cousins, the Toolkit is also an open-access platform that helps architects, and the overall construction market, differentiate between the subject of circular construction, which focuses on where materials come from and where they are going, and the larger conversation of embodied carbon and how materials are made.
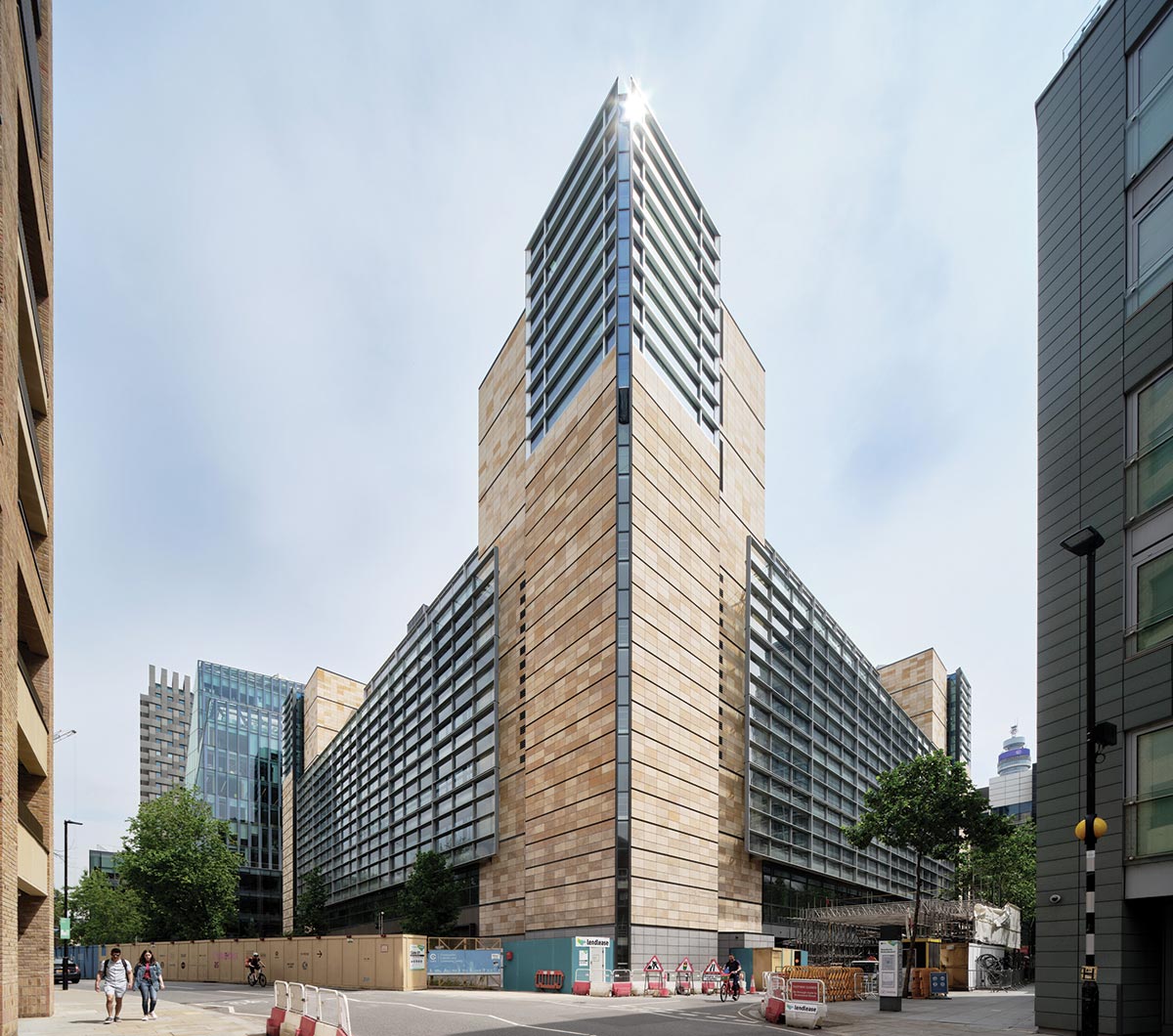
PHOTOGRAPHY: © SIMON KENNEDY
One Triton Square, in London, was originally designed by Arup in the 1990s, and the firm led its comprehensive retrofit more than two decades later.

PHOTOGRAPHY: © SIMON KENNEDY
The curtain wall was disassembled and refurbished at a temporary fabrication site in the metropolitan region.
A framework is only as good as its implementation, and Arup is rolling out practices outlined in the Toolkit, such as material passports, which log information about materials, products, and components, within BIM models, across a range of projects. Notably, according to Frances Yang, Arup associate and leader of its sustainable-materials practice in the Americas, the firm focuses those efforts toward high-value or higher-churn building components, like ceiling tiles and door systems, where greater impact can be had. “Overall, we realized that you need to be strategic about the documentation, and to avoid an all-or-nothing approach that is daunting for clients and burdensome in terms of data collection.”
London has emerged as a testing ground for putting these ideas into practice owing to the city’s rollout in 2022 of mandatory circular-construction guidelines (preceded by a set of voluntary instructions in 2019). The regulations require whole-life-cycle carbon assessment and circular-economy statements to receive planning approval for large buildings, with the aim of furthering London’s goal to reach net zero emissions by 2030 through discouraging demolition and encouraging reuse. One Triton Square, a commercial building designed by Arup and completed in 1998 as the First National Bank of Chicago’s London outpost, now follows these principles, having wrapped up an all-encompassing retrofit at the tail end of 2021. The retrofit of the limestone-and-glass-clad concrete building was also led by Arup, for developer British Land, which committed to a circular approach to the project. It helped that Arup kept drawings of the building’s original systems and materials, reducing the cost and time associated with development of a digital twin BIM model from an entirely new building survey.
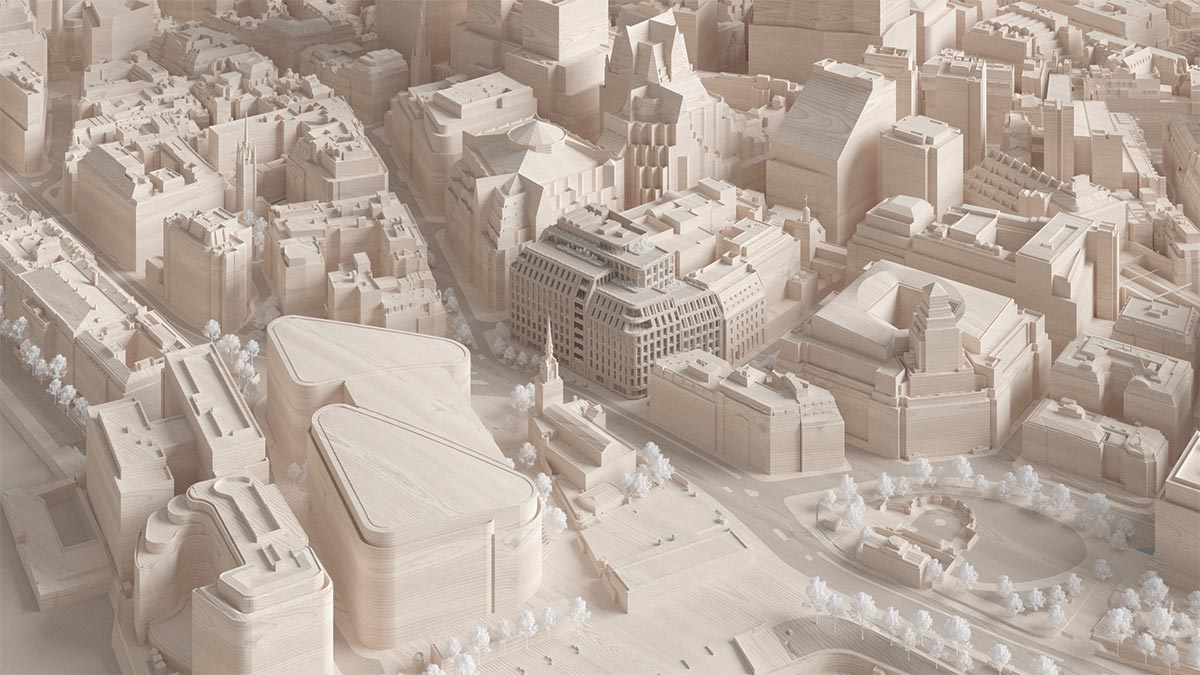
IMAGE: © 3XN GXN
The Mark will consolidate and build over existing buildings a few blocks from the Tower of London.
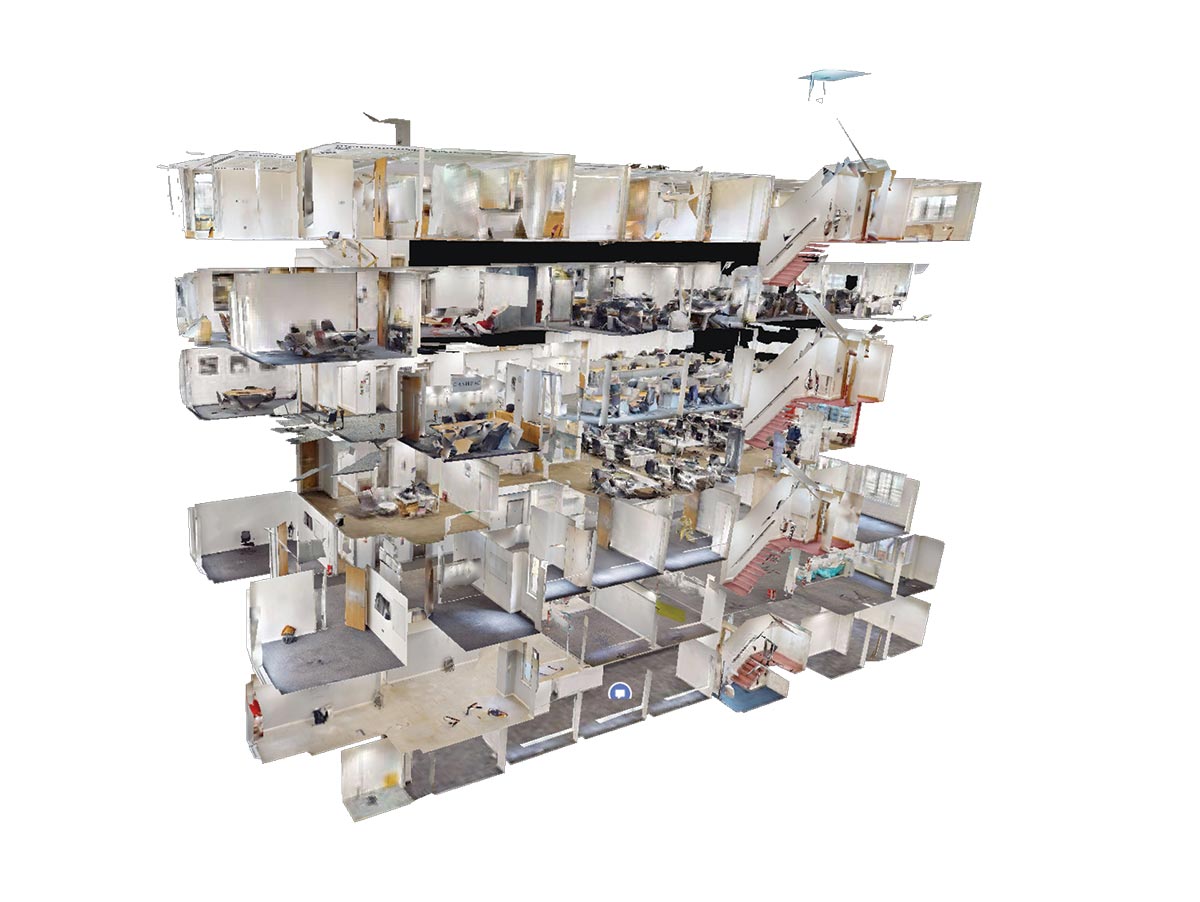
IMAGE: © 3XN GXN
3XN scanned the buildings to produce digital models.
The redevelopment of 1 Triton Square included the addition of three stories to the existing six, with substantial expansions to the floor plate within the building’s atrium. The design team supported the additional load by expanding the diameter of the structural columns from 8 to 10 inches and, in several circumstances, wrapped them in fiber-reinforced polymer for further strengthening. At the exterior, the original aluminum-and-glass curtain wall system was disassembled, and was refurbished with new gaskets and glass coatings, for greater thermal efficiency, at a pop-up factory less than 30 miles away, and reinstalled. For new construction, the design team sourced lower-carbon cement replacements (blast furnace slag makes up 70 percent of binder used for the concrete) and successfully integrated updated mechanical infrastructure within previously allotted m/e/p channels. In total, the retrofit of 1 Triton Square saved some 35,000 tons of concrete and nearly 2,000 tons of steel that, with additional measures, translated to 40,000 tons in carbon dioxide savings—while, at the same time, reducing the project budget and construction schedule as compared to new construction.
GXN, a research studio founded by Danish architecture firm 3XN in 2007, is also leading the way in circular construction, with several projects on that model in London. The group, which works with its parent firm, recently received planning approval for The Mark, an approximately 320,000-square-foot commercial project that will combine four existing buildings into a single entity. “We are increasingly working in London around these new policies, and, in advising clients, we help determine which materials they should focus on and how they can use them in their own scheme, or in others,” says Kåre Stokholm Poulsgaard, GXN partner and head of innovation. “A large part of this is developing the workflows that align with the needs of the client, the contractor, the cost consultant, and the material conveyer. What kills off circular projects are the unknowns.”
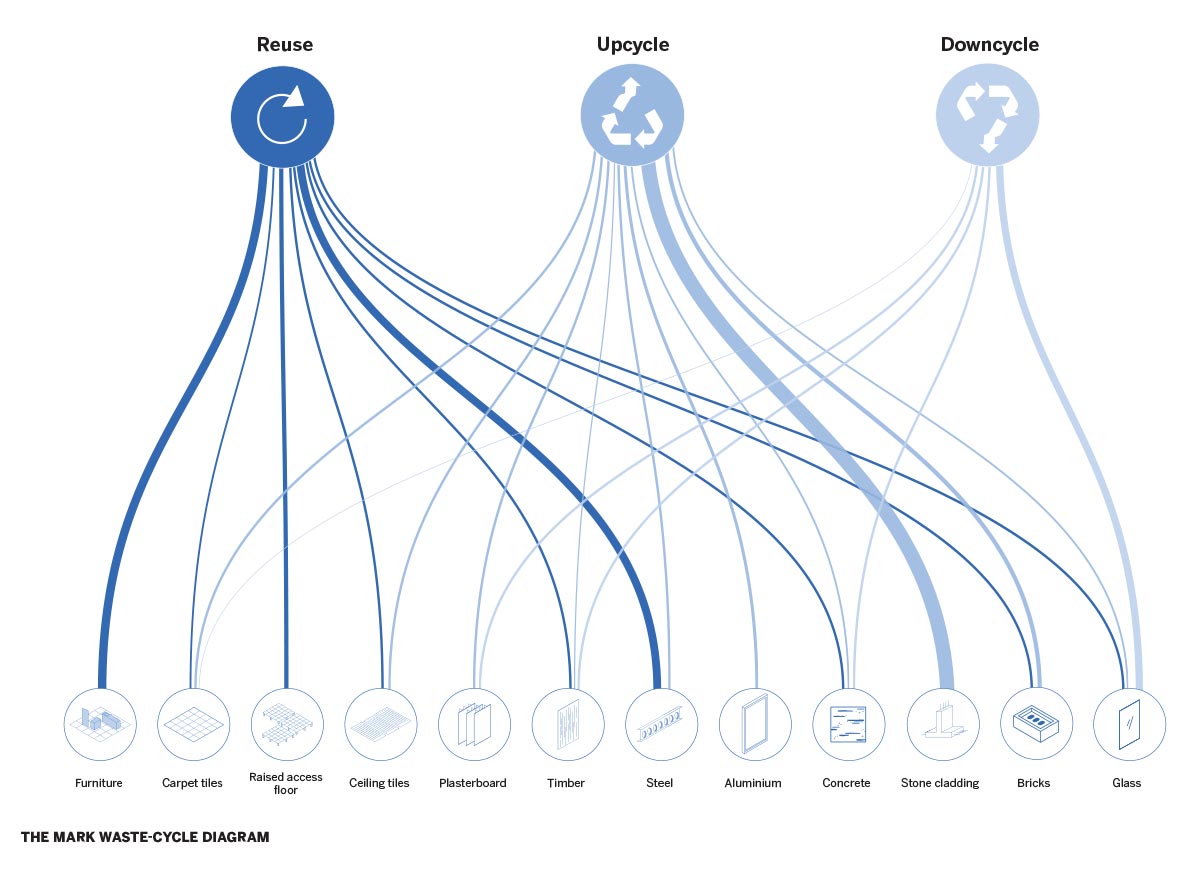
IMAGE: © 3XN GXN
THE MARK WASTE-CYCLE DIAGRAM
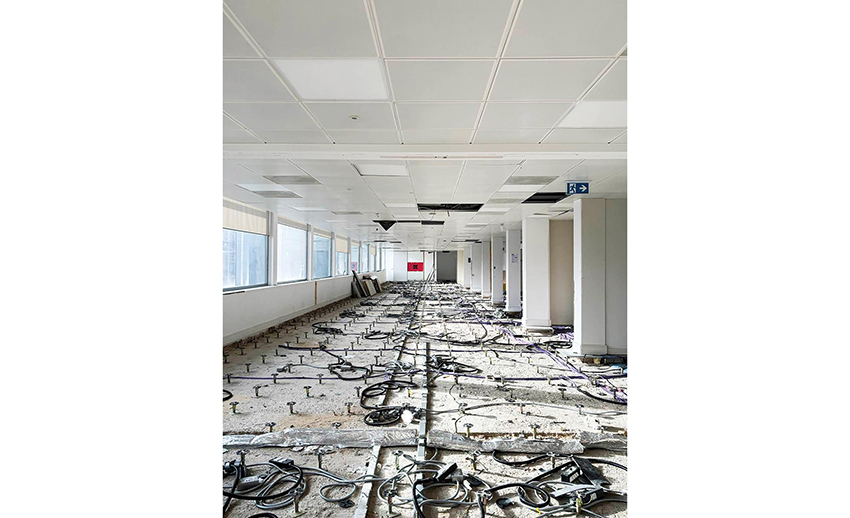
Photo courtesy of 3XN GXN
The Mark has been soft-stripped of materials like raised access floors and carpet tiles.
Work began in May 2022 with a pre-demolition audit using Matterport, a 3D-mapping application, which informed, with the help of their own in-house software, the design team’s identification of areas for the greatest reuse and recycling potential. Soft stripping, or the removal of nonstructural elements, began in early 2024 with such items as raised-access flooring, and ceiling and carpet tiles, among others, offered on the Excess Materials Exchange, a digital platform for salvaged materials; the design team’s aim is for most of those items to be reused on other London construction sites. In addition to maintaining the structural frame, they are also investigating the reuse of materials found on-site for new purposes, such as placing the original stone facade as flooring in the front-of-house areas.
London is not alone in its attempt to become a global circular-construction hub. This year, the New York City Economic Development Corporation (NYCEDC) launched its own circular-design guidelines, to be implemented across its expansive $9 billion portfolio of capital projects starting in 2024. The guidelines are ambitious and aim for a 50 percent reduction in embodied carbon, largely through circular practices, such as reducing construction, and deconstruction material for disposal, by 75 percent; reusing or recycling 95 percent of concrete and soil generated by either construction or deconstruction for highest-use value; and for 25 percent of all virgin materials used to be low-carbon, such as mass timber. The goal, according to NYCEDC’s chief strategy officer Cecilia Kushner, is not only to support New York’s green transition, but to harness the economic heft of the NYCEDC to engender a larger market of circular construction for private actors across the city.
The Science Park and Research Campus (SPARC), in the Manhattan neighborhood of Kips Bay, will serve as a five-acre laboratory for the NYCEDC’s guidelines. The 2 million-square-foot project, to be designed by Ennead and Dattner Architects, with structural-engineer Buro Happold and master-planner SOM, will replace the existing Hunter College Brookdale Campus. The design team was awarded the project in March 2024 and, at this nascent stage, has not developed a completed scheme for SPARC Kips Bay, though the existing-building survey, with digital scans, has commenced. With that information in hand, the team will do an audit to best determine the project’s circular-construction opportunities and begin deconstruction during summer 2025. Construction is scheduled to begin by 2026 and should be complete in 2031.
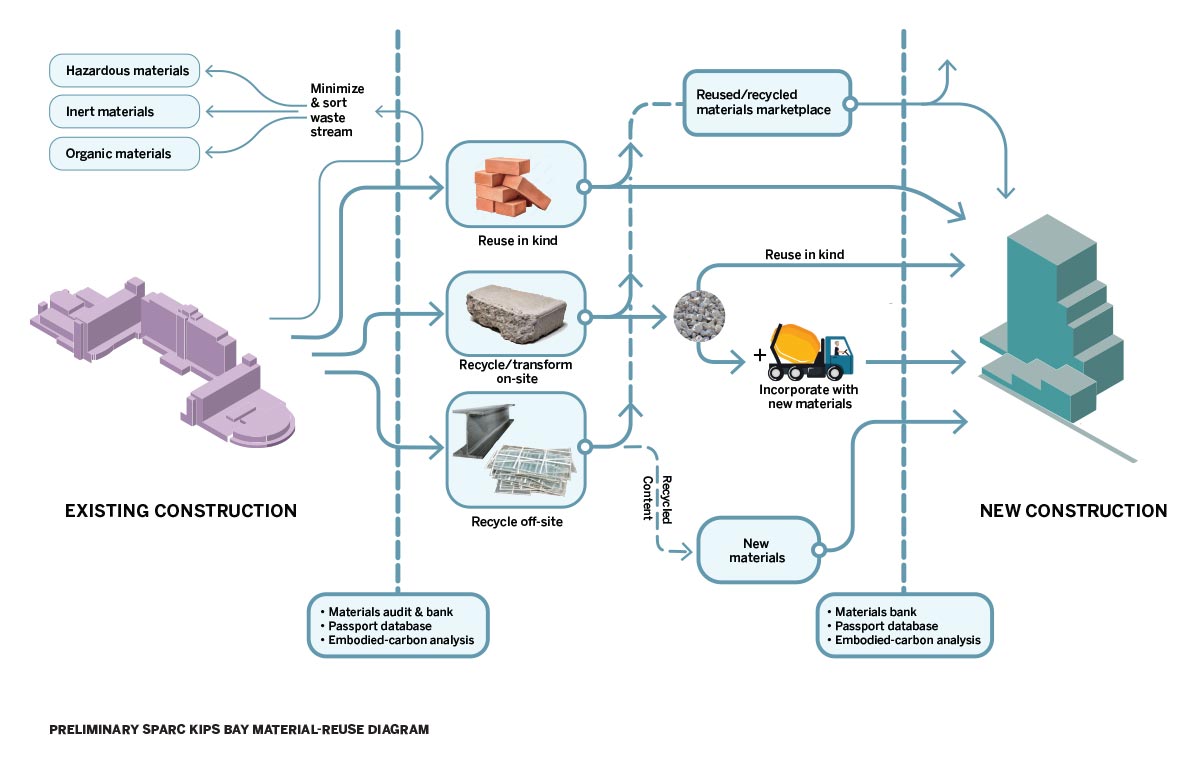
IMAGE: © ENNEAD & DATTER
PRELIMINARY SPARC KIPS BAY MATERIAL-REUSE DIAGRAM
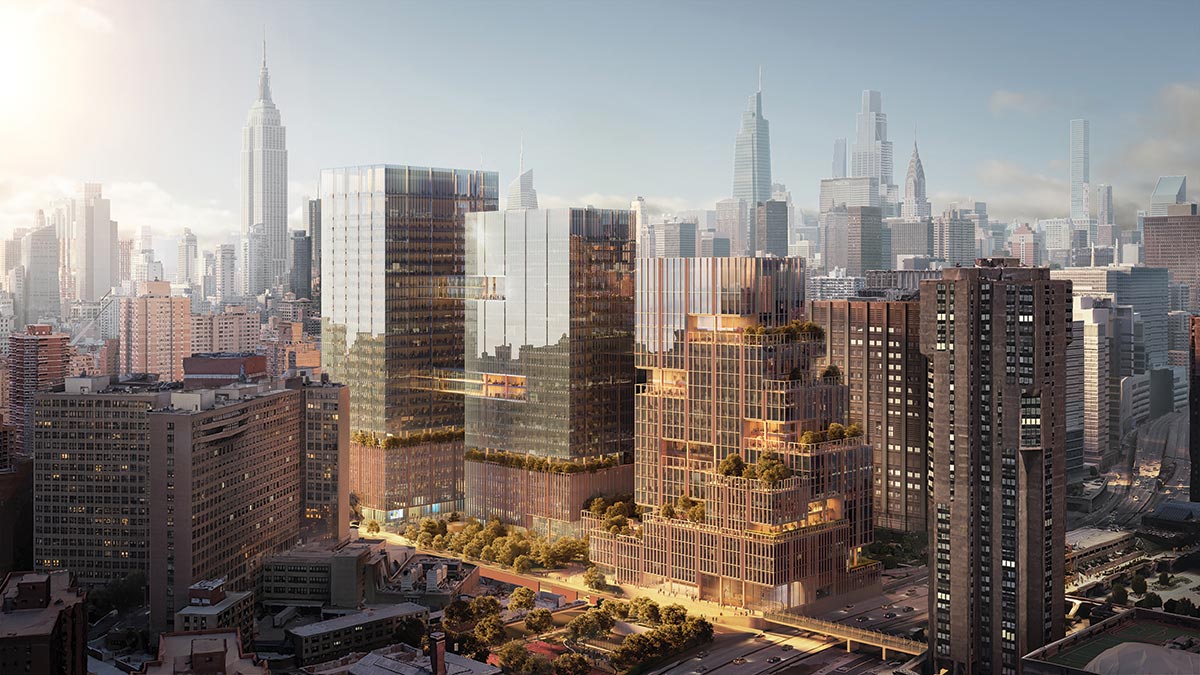
IMAGE: © SOM
Sparc Kips Bay is a full-block site.
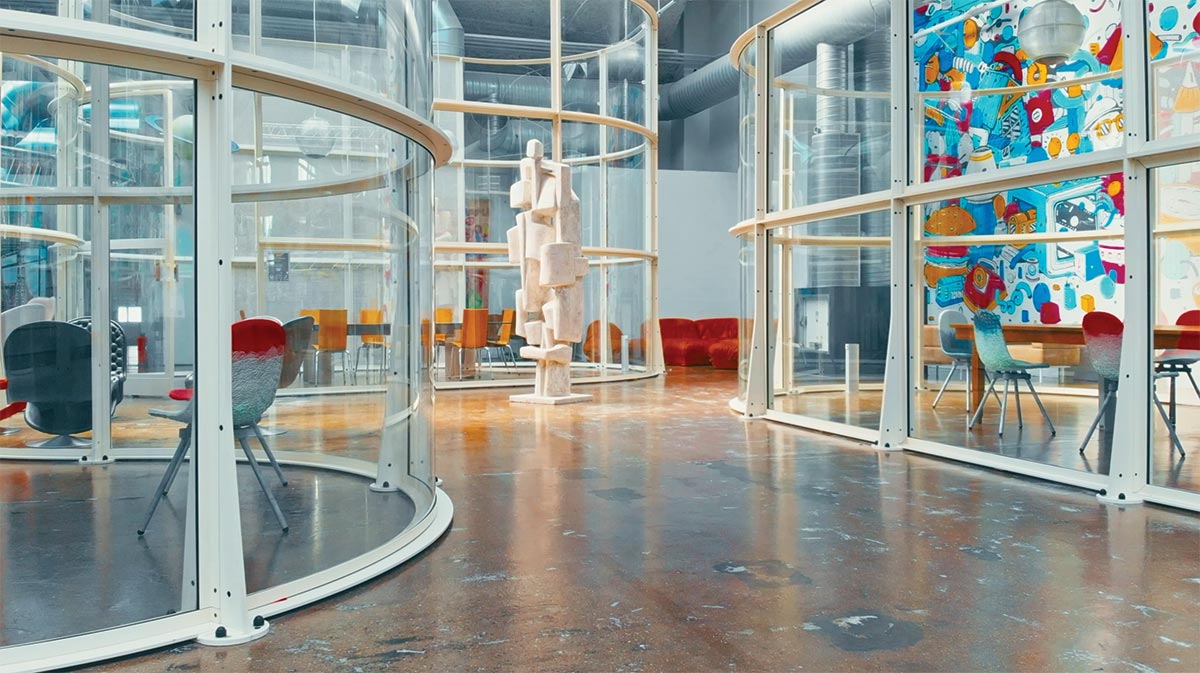
IMAGE: © MAXIMUM ARCHITECTURE/ALEXANDRA ATTIAS
The Centre Pompidou’s curved glass panels were reused as office partitions.