Versatility of Design and LEED Certification with Metal Composite Materials
Aluminum Environmental Impact
In the wake of the green movement, there is an increase in demand for energy efficiency from consumers, as well as regulations and mandates set by the government.
Aluminum plays a crucial role in the sustainability of new buildings and the renovation of existing structures. Due to its performance properties, aluminum largely contributes to new buildings’ energy performance, safety, and comfort. It also plays an essential role in producing renewable energy from solar sources.
Aluminum’s ability to reflect 95 percent of solar energy significantly reduces cooling costs; energy efficiency is a key qualifier for LEED building standards.
Recycling Process of Metal Composite Material
At the end of its very long lifespan, MCM’s aluminum is 100 percent recyclable without losing its material properties. This is in contrast to recycling other materials, such as plastic, which can lose the strength of its properties during the recycling process.
Environmental Product Declaration (EPD)
An EPD offers a standardized, internationally recognized way to evaluate and specify a product with a low environmental footprint. An EPD can be produced for one specific manufacturer’s product (proprietary EPD) or for a particular product type (industry-wide or generic EPD).
EPDs are created using life-cycle assessment (LCA) data specified by the product category rules (PCRs) and based on ISO 14025 standards. PCRs determine product information collected and define the type of LCA data to be evaluated. EPDs are included under LEED v4 in the Materials and Resources category criteria—Building Product Disclosure and Optimization—Environmental Product Declarations.
Metal composite material manufacturers that hold EPDs have invested time and money in gathering LCA information. This information is useful for identifying processes and ingredients that negatively impact the environment and human health. Architects can use this information to look for evidence of improvement in the environmental impact of a product across its life span. The LCA information identifies what the company acted upon and what positive changes an MCM manufacturer has made.
Using an EPD to compare the environmental impacts between the same or similar products can be tricky since few are available where the same PCR has been used, with the same life-cycle phases evaluated. However, they can start a discussion about a company’s sustainability goals.
LEED v5 in 2025
The latest version of LEED should be rolled out early in 2025. The key goals of the new LEED v5 for BD+C are:
- Decarbonization
- Quality of life
- Ecological stewardship
The first public comments on the new version occurred in April and May 2024. The second round of public comments occurred in September and October of 2024.
Some of the categories in LEED BD+C: New Construction v5 may include:
- Climate Resilience Assessment
- Human Impact Assessment
- Carbon Assessment
- Integrative Design Process
- Compact and Connected Development
- Electric Vehicles
- Equitable Development
- Sensitive Land Protection
- Transportation Demand Management
- Minimize Site Disturbance
Though the new LEED version will be released, projects can still use the current LEED v4.1. At this time, there is no date planned to sunset v4.1
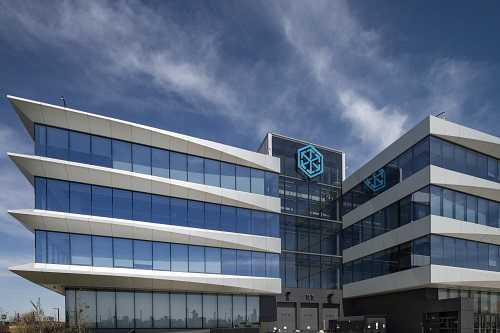
Mark Kempf Photography; courtesy of 3A Composites, USA Inc.
C.H. Robinson flagship operation, designed by Skidmore, Owings & Merrill.
NOTEWORTHY PROJECTS WHERE MCM HELPED ACHIEVE LEED CERTIFICATION
Several LEED-certified projects with MCM panels have already been presented in this course. Here are a few more:
LEED Project: Wide Array of Metal Exterior Components Used in LEED-Certified Design
The LEED Silver Residence Inn Marriott Boston Watertown is the first hotel built in the area in 50 years, Dana Forsythe of the Wicked Local Watertown explains. The hotel is a joint venture between developers Boylston Properties of Boston and Stonebridge Companies in Denver. Boylston is known for its recent projects in developing areas of Boston, such as the recently completed LINX and the $60 million corporate development in Watertown.
The Residence Inn Marriott is located in Watertown’s East End. William McQuillan, Principal of Boylston Properties, said, “We built a contemporary building on purpose that has a 24/7 life to it. It’s about the future of Watertown, and it’s one of a number of projects going on in the East End that are all about the future of Watertown.”
Stantec Architecture designed the hotel, which sits in the location of the former Charles River Saab, the oldest Saab dealership in the United States. The 108,000-square-foot hotel features abundant, sustainable amenities contributing to its LEED ranking, including energy-saving HVAC, lighting, and groundwater systems. Additionally, a range of sustainable construction processes was also adopted.
According to the general contractors at PROCON, “The building’s exterior was a combination of color reflective masonry and panels with lighter toned upper floors highlighted by recessed faux wood accents.”
Using a drained, rear-ventilated rainscreen system, CEI Materials fabricated the metal composite and aluminum plate components of the facade. This system offers rainscreen technology with varying joint widths and color versatility. “With ten different colors on the project, joint colors and color layout of the panels required special attention in the final design and fabrication and installation,” said CEI Materials Project Manager Nick Sodt.
CEI fabricated 45,000 square feet of metal components for the project, which saw a few challenges, such as the site access on Arsenal Street due to existing power line layouts. Additionally, the company fabricated large 14-foot by 16-foot panels for the exterior, which created some challenges in terms of shipping and installation that were overcome.
The six-story hotel was a welcomed addition to the area, offering 150 spacious accommodations ranging from studios to two-bedroom suites with fully equipped kitchens. Guests can enjoy an array of modern conveniences, including an indoor saltwater pool. Watertown in Greater Boston is becoming highly popular with new sustainable developments that breathe new life into the area.
LEED Project: Metal Fins Reflect Water Movement and Reduce Glare in an Energy-Efficient Riverfront Office Building
The Chicago flagship operation of logistics provider C.H. Robinson, which aimed to achieve LEED Gold status, opened its doors to employees in August 2018 as the first anchor tenant in the new Lincoln Yards revitalization development near Chicago’s Lincoln Park neighborhood. Designed by the Chicago office of architecture and engineering firm Skidmore, Owings & Merrill LLP (SOM), the new four-story office building in 207,000 square feet accommodates more than 1,000 employees of C.H. Robinson, a leading global third-party logistics provider. This modern office building reflects its riverfront location with a design that emulates the flow of water with undulating fins fabricated from aluminum composite material.
To help achieve a LEED certification, the building incorporates low-cost, high-efficiency materials to achieve significant performance improvements, according to an architect’s statement. It is clad in heat-reducing glass shaded by the MCM fins, designed to mitigate solar gain, reduce glare in workspaces, and increase daylight in communal areas.
The recyclable MCM—manufactured with post-manufacturing and post-consumer content—contributes LEED credits to building projects. The undulating fins were fabricated with approximately 28,240 square feet of 4mm MCM in a custom silver mica color.
“SterlingBay presented us with a challenging and exciting opportunity that we tried to resolve with a sophisticated but simple design concept,” said Jorge Rovira, AIA, associate, SOM architects. “They asked us to create a design that would integrate the building with the river and that could be built efficiently,” Rovira said. “We investigated a mix of high-performance building materials to achieve LEED certification. When we looked at the big picture for this design, we knew we wanted to bring light deep inside the space while maximizing sustainability by controlling daylight to create a better workplace. We introduced the idea of large ‘fins’ that would be shaped to reduce glare inside and offer an opportunity to reduce the window-to-wall ratio and incorporate more surface for insulation. Behind the fins, a well-proven unitized curtain wall would provide the enclosure.” These fins would be designed with profiles that would move in and out from the building to meet changing glare control requirements, according to Rovira, who said the fins would also create the perception of long waves and reflect the movement of the river.
SOM engaged the engineering expertise of Sobotec Ltd. (www.sobotec.com), of Hamilton, Ontario, Canada, to work together to turn the vision for the facade fins into reality. “When we were thinking about a metallic surface, we thought (MCM) would be cost-effective and easy to handle and could be formed into different shapes. We were able to introduce a unique central atrium to bring more daylight into the building and yet remain within the project’s budget because we saved building material costs by selecting (the MCM). We were quite comfortable using aluminum composite material because we knew it could be twisted and that the corners would be sharper than those created with metal panels,” said Rovira. “We wanted the brightness of silver and its reflection,” he continued. “When light hits the silver (panels), it looks even brighter and almost gleams in the sun. As light hits the Chicago River, it bounces back so that you can see the river reflected on all floors of the building. The sparkling reflections and water movement are very beautiful.”
Sobotec engineered and fabricated approximately 300 different panel shapes to create the sunshade design on each of the building’s four floors, with one identical pattern repeating on the second and fourth floors and another on the third floor and roof. Each elevation features unique panels that create an angled facade and contour look for the fins.
Sobotec fabricated the panels and gussets and installed them in a unitized system in the controlled environment of the company’s shop rather than in the field. The units feature a custom aluminum frame and hook and pin system with locking bars. A total of 827 finished units measuring approximately 5 feet wide by 6 feet tall were shipped to the site for installation.
SOM architects spent approximately one year designing the project; construction was completed in one and a half years. Now that building construction is complete, “we all agree that it looks fantastic,” according to Rovira. “It’s a simple yet elegant design.”
CONCLUSION
In summary, let us review the potential for LEED credits and creative flexibility with the specification of metal composite materials. In the LEED v4.1 rating system, MCM excels in two categories: Materials & Resources and Innovation. Points earned with MCM focus on building materials that reduce a building’s environmental impact. LEED also rewards manufacturers who minimize energy and water use during manufacturing. The overall effect is a lessening of carbon emissions through the entire production life cycle. MCM specification often leads to Innovation points because of the material’s formability, flexibility, and high-tech finishes. These characteristics enhance creative potential, as illustrated in several highly regarded and visible projects where MCM added to the project’s aesthetics and helped achieve LEED certifications. The section on the manufacturing process of MCM helps explain the product’s lightness, durability, and resistance to oil canning. All these factors make MCM a logical and desirable cladding choice for architects and designers seeking an innovative material that helps achieve a LEED certification.
Kathy Price-Robinson writes about building and design. Her “Pardon Our Dust” remodeling series ran for 12 years in the Los Angeles Times. She specializes in writing about buildings that are durable and resilient to climate disruption and products and designs that provide shade in hot climates. www.www.kathyprice.com