Versatility of Design and LEED Certification with Metal Composite Materials
Once the butterfly shape was conceptualized, the challenge became how to make it fly─functionally, aesthetically, and monetarily. An aluminum composite material provided the solution. About 250,000 square feet of MCM in a custom bone-white color was installed as exterior wall cladding on the Tower Hospital. “Metal provided flexibility and affordability,” Moorhead said. “It was the perfect choice to give the crisp white look that Rush was interested in, and it was easily adaptable to the curvilinear shape of the building.”
The aluminum composite material used to clad the tower helped Rush realize those goals. The material is durable and can be bent into any shape. It was noted that the Rush Tower has a lot of bends and curves, and the MCM panels provided the vehicle for architects to employ.
Sobotec in Hamilton, Ontario, the metal fabricator on the project, designed a unitized curtain wall system to enclose the Tower as quickly as possible. Sobotec created AutoCAD computer-generated drawings to fabricate the MCM panels. ASI Ltd., in charge of the installation, then fit the panels into the prefabricated curtain wall with a framed support system for the metal panels and glass.
Like many academic medical centers, the Rush campus is a conglomeration of buildings constructed during different decades. The campus has several metal buildings, so an aluminum composite-clad tower would feel cohesive. The Rush leadership, Moorhead explained, “really wanted to project an image of fresh, clean, modern, and technically savvy.”
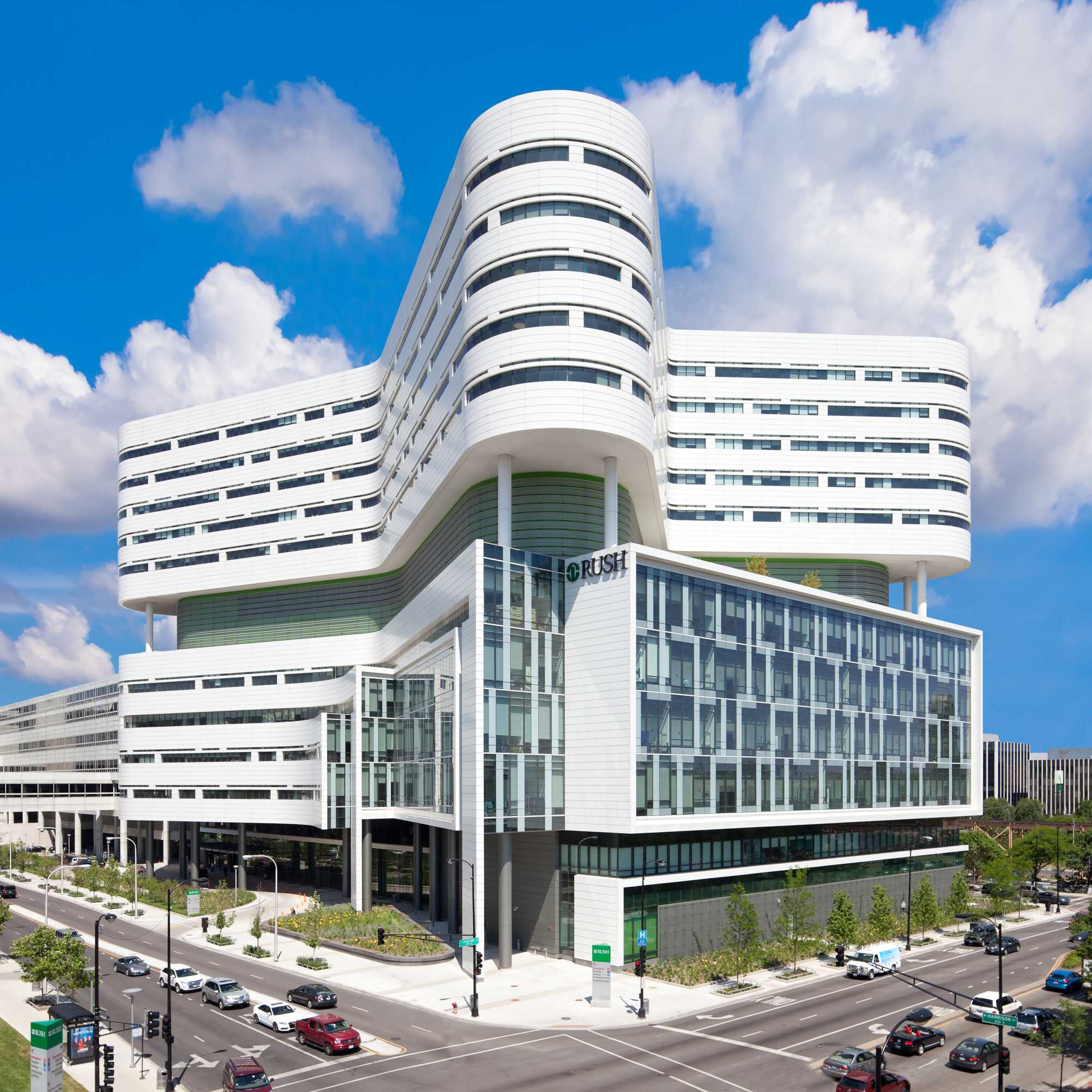
Robert R. Gigliotti; courtesy of 3A Composites USA, Inc.
LEED Gold-certified Tower Hospital at Rush University Medical Center, designed by Perkins+Will.
HIGH-TECH FINISHES PROVIDE A MODERN IMAGE
It is essential to specify the right finish for the project. Considering coastal or chemical influences, positioning of the sun, and desired appearance factor in determining the correct finish for the application and warranty considerations.
A Variety of Finish Options
- Polyvinylidene fluoride (PVDF): Due to its durability to withstand harsh climatic conditions, 70 percent PVDF resin-based coatings are used worldwide. Paint containing 70 percent PVDF can resist chalking and fading and withstand lengthy exposure to UV rays, temperature, humidity, water, and atmospheric pollutants like acid rain.
- Fluoroethylene Vinyl Ether (FEVE) clear coats: FEVE clear coats are often used on bare finishes (such as various brushing patterns). It offers protection from the elements to preserve the aesthetic of the bare finish. This clear coat provides transparency to observe the natural brush strokes applied to the coil. Various tints can broaden the color palette and improve the project’s aesthetics.
- Silicone-modified polyester (SMP) and highly-durable polyester (HDP): Highly-durable polyesters have improved formulation, resulting in significantly improved durability and color retention with greater UV degradation resistance. They are often used in exotic finishes, such as color shifting and textured finishes.
- Custom colors: Manufacturers typically have a color-match department specializing in color development to help guide architects/designers through the process. Suppliers can match most Pantone, RAL, NCS, or other paint manufacturers’ systems. This flexibility with paint manufacturers for brand identity custom colors is an added advantage.
- Patterns that mimic natural surfaces and metals These include stones, woodgrains, abstracts, graphite, stainless, zinc, mica, and metallic.
- Anodized: Anodizing is an electrochemical process that thickens and toughens the naturally occurring protective oxide on aluminum. The anodized finish becomes part of the metal, and its porous structure allows for coloring and sealing. Aluminum oxide is one of the hardest surfaces known, second only to the diamond.
- Brushed and mirror finish: A brushed finish provides warmth and richness and offers an alternative to a colored opaque finish. However, it may lack color consistency from batch to batch and is not recommended for coastal or harsh chemical applications. Reflective mirror sheets reflect the natural environment without the higher weight and breakability of glass.
- Color-shifting paints: Color-shifting materials, originally derived from the automotive industry, change color as different wavelengths of light are reflected back to the observer. Depending upon the viewing angle, the panels offer ever-changing color gradients with iridescent highlights. The color effects are enhanced as the individual surface layers break up and refract the light. Typically, two or three colors are selected with one opposing color from the color wheel selection.
An MCM representative can help determine which finish option is best for a project based on the location and application.
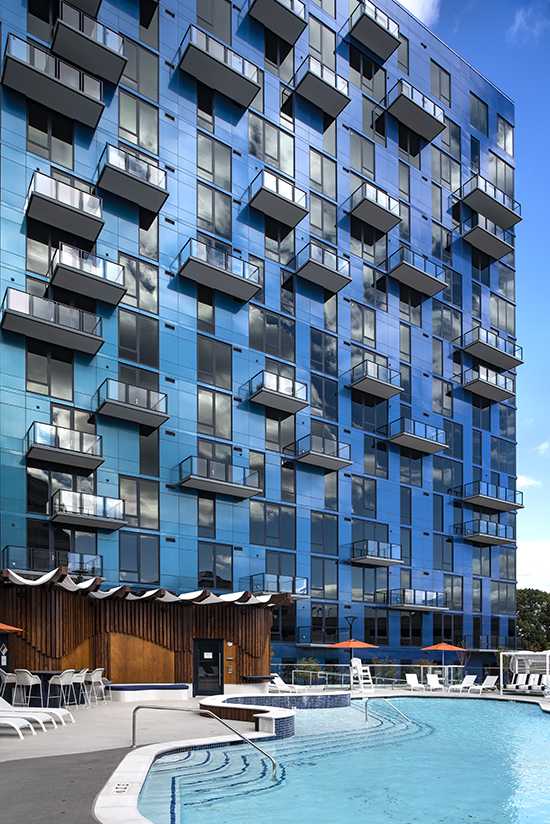
Mark Kempf Photography; courtesy of 3A Composites USA
Exo apartments in Reston, Virginia, designed by R2L: Architects in Washington, D.C.
LEED Project: Color-Shifting Aluminum Composite Panels Complement Dynamic Windows
Marketing materials for the Exo apartments—which feature a gleaming contemporary facade—encourage residents to “live in full color” in this 457-unit multifamily residential community that was targeted to achieve LEED Gold status. Located in Reston, Virginia, Exo residents live less than 25 miles from Washington, D.C.
The Exo aimed toward LEED status by including sustainable building materials and techniques, including smart glass technology. Recyclable MCM panels manufactured with post-manufacturing and post-consumer content contributed LEED credits.
The 530,000-square-foot Exo comprises two identical 16-floor towers connected with a single-story reception-area link building. It is clad in aluminum composite material in a color-shifting finish. The MCM product was selected as a complementary building material to Exo’s color-changing smart glass technology, which adjusts window tint to allow optimal natural light.
R2L: Architects was tasked with designing Exo for Greystar as the first multifamily residential community in the United States to feature a particular brand of dynamic glass. “Our design was driven by smart glass technology,” said Sacha Rosen, AIA, principal, R2L: Architects. “This was to be a world demonstration project, serving as the first all-residential building using (this brand of dynamic glass). Incorporating smart glass technology required an extensive design process.”
The pre-glazed windows use electrochromic technology, requiring wiring to each window for electrical control. Apartment residents can control the windows in their apartment through an app that lets in natural light while reducing glare, lowering energy costs, and eliminating the need for shades or curtains. Apartment managers also have access to overall building control for the windows.
To aid in this intricate window design, Custom Walls & Windows, Inc. of Jessup, Maryland, began work with general contractor John Moriarty & Associates of Virginia, LLC, based in Arlington, and R2L: Architects in early 2017. “It was Custom Walls & Windows’ suggestion to clad the building with (the aluminum composite) panels,” said Rosen. “The thought was: If the glass changes colors, why not use metal panels that change colors?”
The project features 150,000 square feet of MCM in an ocean-toned color-shifting finishing system. The colors are transitional finishes that celebrate the natural color shifts that occur in the world around us. From naturally occurring elements to the glowing luster and sheen found in modern metals and luxury goods, colors add biophilic fascination to the built world.
As the original aluminum composite material, this brand allows architects and designers to meet the fire performance requirements of today’s building standards. Consisting of two sheets of smooth 0.020” aluminum heat bonded to a solid, fire-retardant core in 4mm nominal thickness, the MCM system is one component of the wall assembly that meets the requirements of fire classifications while offering the proven product properties such as flatness, formability, durability and ease of fabrication.
“The color of the overall design was generated by the smart glass, so the cladding color had to look good with the glass,” according to Rosen, who said the smart-glass technology offers residents four tints ranging from clear to darkening shades of blue. “Custom Walls & Windows suggested the (ocean color). The color was perfect, so there was no need to pursue custom colors.”
The Exo’s twin 16-story towers rise above a landscaped parking plinth featuring 646 parking spaces and are connected by a link building designed completely in intelligent glass. According to an architect’s statement, the building facades are modularized and designed to leverage efficiencies in fabrication and construction, while scattered balconies punctuate the elevations.
The box-like design of the residential towers may be straightforward, but according to Rosen, the color-changing building materials make it stand out. “There are so many new developments on the market in the Washington, D.C., area, you have to differentiate your offering,” Rosen said. “The Exo is very contemporary and different from everything else out there. We used the building materials to make it striking.”
Approximately 16,000 panels were fabricated and installed with a male/female interlocking system. Custom Walls & Windows designed a three-piece panel system with glass and panels for easier installation. “The (aluminum composite panels) look fantastic,” Rosen said. “It’s even more intense than I had hoped. It’s very striking and contemporary. Often, you have a vision for a design and then have to figure out how to make it a reality. It’s very rewarding as an architect to have access to a unique and special material…and to work with a contractor who knows how to use it.”
SUSTAINABILITY AND HOW MCM HELPS EARN LEED CERTIFICATIONS
This section discusses how MCM is a sustainable product, beginning with its manufacturing process. After that, the discussion turns to a brief review of specific LEED points that pertain to MCM.
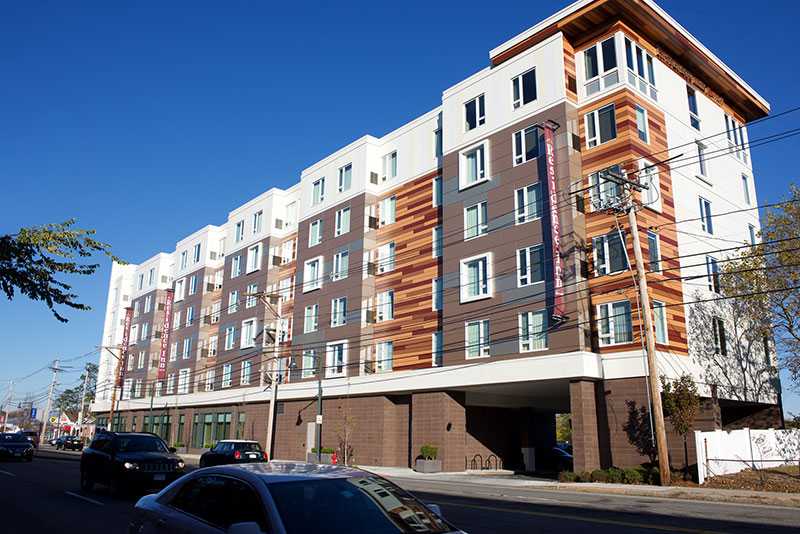
Photo courtesy of CEI Materials
Residence Inn Marriott Boston Watertown, designed by Stantec Architecture.
Manufacturing Environmental Impact
During the manufacturing, all excess material is recycled back into the process. Scrap aluminum goes back to aluminum processing plants for recycling, and the scrap core material gets recycled.
Composite Concept
The sandwich concept reduces energy input and consumption. Given that aluminum, the most common metal used in MCM, requires large amounts of energy to be produced, the portion of aluminum used to manufacture MCM is by far less than that of flat sheet aluminum. Typical MCM uses 70 percent less aluminum than 1/8-inch plate.
Coil Coating Environmental Impact
The continuous coil-coating process provides MCM with a protective coating that is available in a wide range of paint colors and finishes. During the coil-coating process, 99.9 percent of all volatile organic compounds (VOCs) are captured. Excess paint is recovered and used to cover the non-visible side of MCM, so no excess paint is burned as waste. Additionally, all solvents used to clean the machinery are collected and reused.
Seventy percent PVDF resin-based coatings are used around the world on the exteriors of numerous architectural projects because they can:
- Resist chalk and fade
- Withstand lengthy exposure to:
- UV rays
- Temperature
- Humidity
- Water
- Atmospheric pollutants, like smog