Versatility of Design and LEED Certification with Metal Composite Materials
Learning Objectives:
- Explain the features, benefits, and advantages of metal composite materials (MCM).
- Describe the sustainability of metal composite materials.
- Discuss how MCM helps earn LEED credits in LEED v4.1.
- Identify five noteworthy projects where MCM helped achieve LEED certification.
Credits:
This course can be self-reported to the AANB, as per their CE Guidelines
Approved for structured learning
Approved for Core Learning
This course can be self-reported to the NLAA
Course may qualify for Learning Hours with NWTAA
Course eligible for OAA Learning Hours
This course is approved as a core course
This course can be self-reported for Learning Units to the Architectural Institute of British Columbia
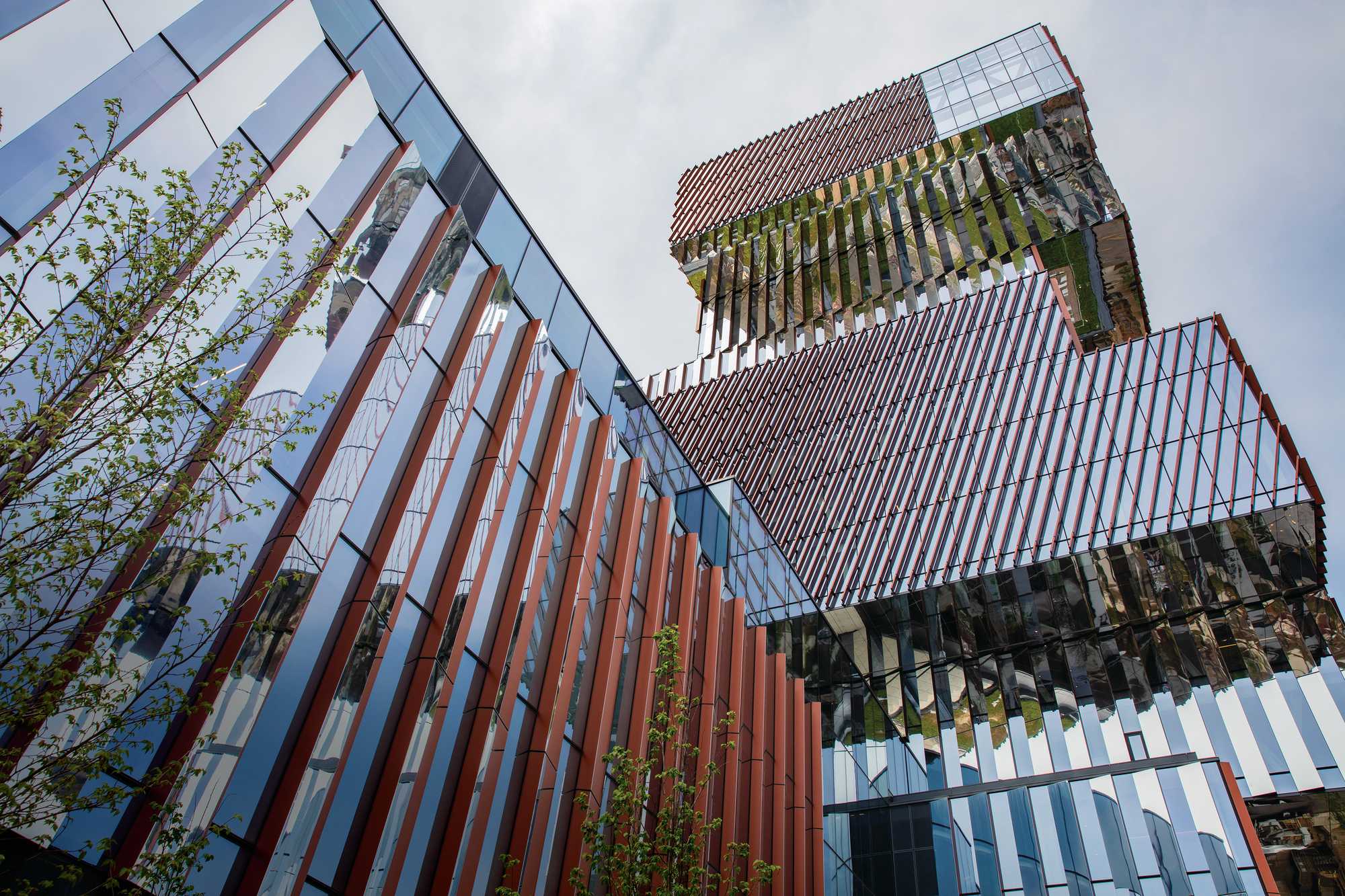
Image by Bob Perzel Photography
Boston University Center for Computing & Data Sciences, designed by Boston-based KPMB Architects.
Metal composite material (MCM) may be familiar to architects and designers for its versatility, durability, design flexibility, and dramatic beauty. However, the material’s sustainable characteristics and potential LEED credits—earned through the U.S. Green Building Council’s Leadership in Energy and Environmental Design rating system—should also be considered. LEED v4.1 prioritizes sustainable materials, helping manufacturers to design, produce, and deliver building materials that reduce a building’s environmental impact. LEED v4.1 also rewards manufacturers who reduce energy and water use during manufacturing, minimize their carbon footprint during distribution and transportation, and lessen overall carbon emissions through the entire production life cycle. LEED focuses on efficiency and leadership to deliver triple bottom line returns of people, planet, and profit. This course also discusses the history and manufacture of these leading-edge panels. It illustrates their features, benefits, and advantages, including an array of finishes that help MCM stand out from other cladding materials. This course emphasizes five significant projects targeted for LEED certification. The course begins by briefly reviewing potential LEED v4.1 points earned with MCM.
LEED V4.1 POINTS EARNED BY MCM
These are the main LEED v4.1 categories and credits that MCM products help to earn:
Category: Material & Resources
- Building life-cycle impact reduction: 5 points possible
MCM is recognized within the design and construction industries for its reduced life-cycle impacts. This credit intends to “encourage adaptive reuse and optimize the environmental performance of products and materials.” The two options are 1) building and material reuse for 1 to 5 points or 2) use of a whole-building life-cycle assessment for 1 to 4 points.
- Building product disclosure and optimization—environmental product declarations: 2 points possible.
With robust environmental product declarations, an MCM specification helps earn this credit. The intent here is “To encourage the use of products and materials for which life-cycle information is available and that have environmentally, economically, and socially preferable life-cycle impacts. To reward project teams for selecting products from manufacturers who have verified improved environmental life-cycle impacts.”
The two options include 1) environmental product declaration for 1 point or 2) a multi-attribute optimization.
- Building product disclosure and optimization - sourcing of raw materials: 2 points possible.
The documented sourcing of the raw materials used to create MCM is vital for earning this credit. The intent is “to encourage the use of products and materials for which life-cycle information is available and that have environmentally, economically, and socially preferable life cycle impacts. To reward project teams for selecting products verified to have been extracted or sourced in a responsible manner.”
The options include 1) raw material source and extraction reporting and/or 2) leadership extraction practices for 1 point.
- Building product disclosure and optimization - material ingredients: 2 points possible.
These LEED points are earned when specifiers select an MCM manufacturer with complete material documentation. The credit’s intent is “To encourage the use of products and materials for which life-cycle information is available and that have environmentally, economically, and socially preferable life-cycle impacts. To reward project teams for selecting products for which the chemical ingredients in the product are inventoried using an accepted methodology and for selecting products verified to minimize the use and generation of harmful substances. To reward raw material manufacturers who produce products verified to have improved life-cycle impacts.”
The two options include 1) material ingredient reporting for 1 point and/or 2) material ingredient optimization for 1 point, and/or 3) product manufacturer supply chain optimization for 1 point.
- Construction and demolition waste management: 2 points possible.
This credit intends to “reduce construction and demolition waste disposed of in landfills and incineration facilities by recovering, reusing, and recycling materials.” Options include 1) diversion for 1 to 2 points or 2) reduction of total waste material.
Category: Innovation
- Innovation: 5 points possible.
The innovation potential is a crucial benefit of MCM, as its unparalleled formability broadens creative design. The credit intends to “encourage projects to achieve exceptional or innovative performance to benefit human and environmental health and equity. To foster LEED expertise throughout building design, construction, and operation and collaboration toward project priorities.” Options include 1) innovation for 1 point, 2) pilot credit for 1 point, or 3) additional strategies that include innovation, pilot, and exemplary performance for up to 5 points.
HISTORY, FEATURES, BENEFITS, AND ADVANTAGES OF METAL COMPOSITE MATERIALS (MCM)
The International Building Code (IBC) defines a metal composite material (MCM) as:
A factory-manufactured panel consisting of metal skins bonded to both faces of a solid fire-retardant core. Section 1406 in the IBC focuses on the use of MCM in construction. The section contains considerable detail about physical and fire performance and the required testing to allow the use of MCM on various construction types.
History of MCM
While IBC Section 1406 has only been around since 2000, the use of MCM in North America dates back to the late 1970’s. The first aluminum composite material (ACM) was created in Europe in 1969. In 1979, the first ACM was produced in Benton, Kentucky. In the early 1980s, several global companies produced ACM and shipped it to North America for architectural projects. By the 1990s, three companies were manufacturing ACM in North America. Eventually, some manufacturers used alternative skin materials such as copper, zinc, stainless steel, and even titanium. This skin material change broadened the product name to metal composite material or MCM. Today, the number of manufacturers continues to grow worldwide, and the amount of variation in product offering and quality continues to expand.
One of the other significant variables seen in the industry over the years is the production process used to make the MCM. The typical method is to extrude or place a core material between two continuous skins of metal with a bonding technology to keep the components together, run the assembly through a series of heated rolls under considerable pressure, and end with the manufactured sheets cut to length. Continuous sheet production in a controlled factory environment has proven to be the most common practice to ensure the highest quality for MCM products.
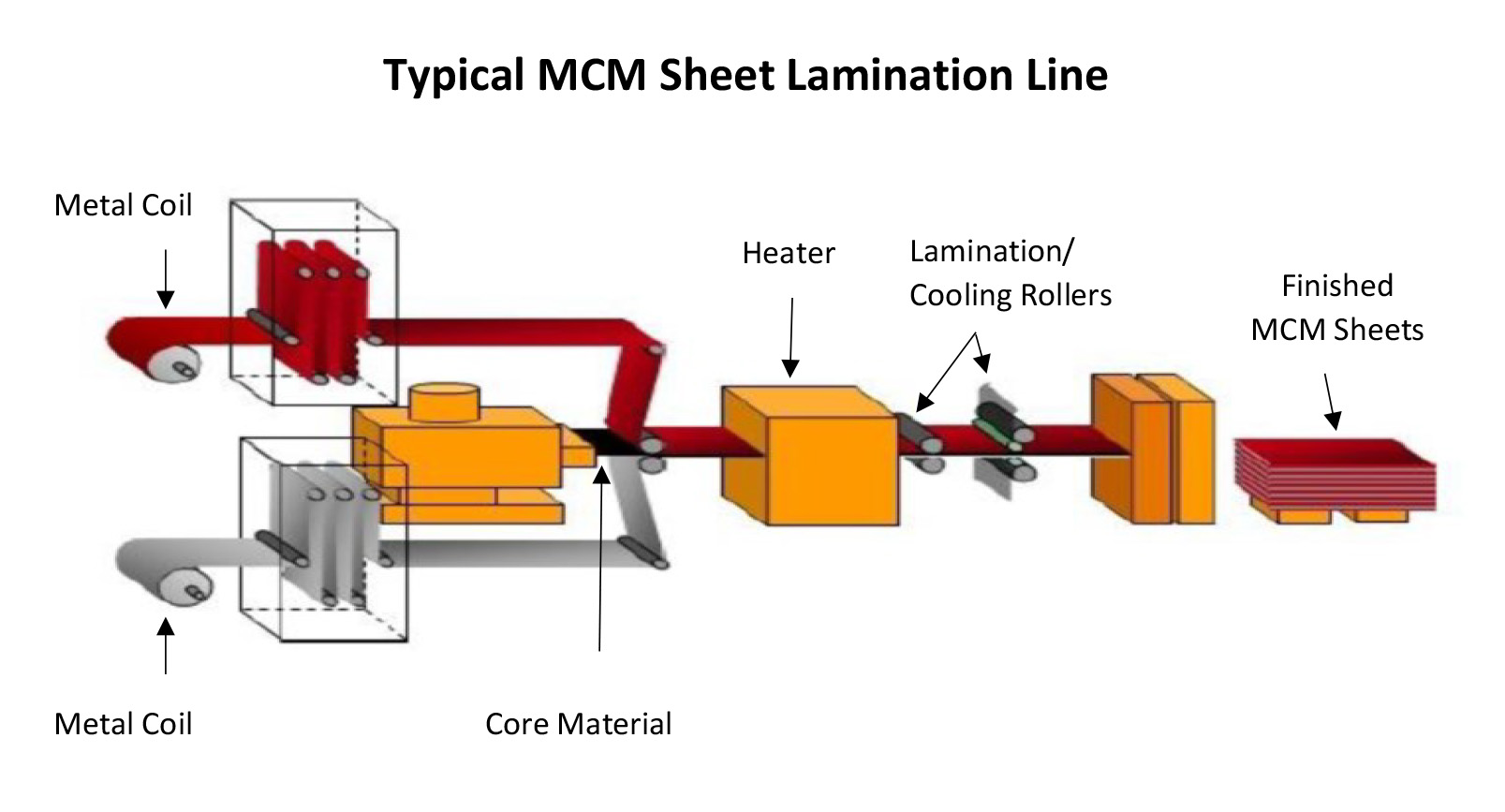
Graphic provided by the MCM Alliance of the Metal Construction Association
The MCM production process.
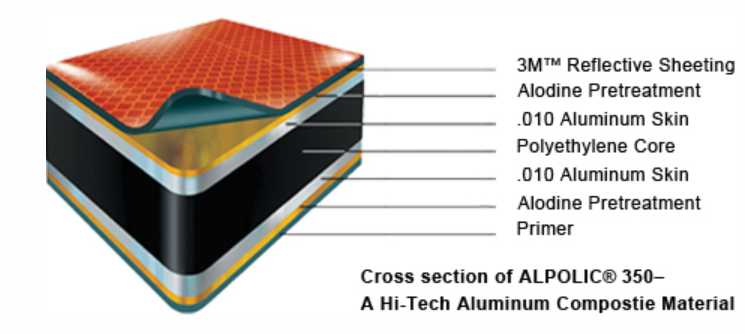
Provided by the MCM Alliance of the Metal Construction Association
Section diagram of MCM.
Metal Composite Material Production
The MCM production process is relatively straightforward. It starts with producing an extruded core material, then applying a material that bonds the elements, and then adding aluminum skins for structural stability. This results in a product ready to finish in a myriad of colors and types. This material stack is heated and passed through a roll laminator, providing significant pressure and tension for bonding all the individual elements. The bonded sheets must be cooled in a controlled process to maintain the bond integrity and the material’s flatness as it cools. The semi-soft, malleable core becomes more rigid as it cools between the two metal skins. The skins, generally aluminum, are also at a high temperature, cooling as the process continues. Metal contracts as it cools, making the entire assembly want to move, twist, and bow until the finished composite sheet reaches ambient temperature. The required bond strength to keep the sheet together is not attained without the controlled addition of heat, tension, and pressure. The controlled cooling maintains the product’s flatness.