Designing Outside the Box
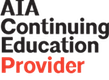
Learning Objectives:
- Define embodied carbon and its effects in the built world.
- Using a matrix of environmental impacts, make sustainable material selections from both traditional and alternative building products.
- Delineate between sustainable certifications, including LEED, LBC, and WELL, to secure a best fit for project goals and outcomes.
- Define material health and transparency, LCAs, and EPDs, in order generate a responsive and sustainable material selection framework.
- Evaluate materials by quantifying embodied carbon impacts through LCA tools such as EC3.
This course is part of the Metal Architecture Academy
What They Are
Future-oriented buildings require future-oriented products. Insulated Metal Panels (IMPs) are a
lightweight system of exterior wall and roof panels with metal skins and an insulating foam core. First
developed by the National Aeronautics and Space Administration (NASA), these panels have superior insulating
properties, and their outstanding spanning capabilities and one-pass installation makes them quick to
install, providing unit cost savings when compared to other wall assemblies.
To deliver their high-performance insulation, foam is injected, or poured in place, between two metal
sheets, where it then undergoes a chemical reaction, causing it to expand and bond to the metal skins,
thereby completely filling the interior cavity between the metal skins. The result is a solid panel
composite system that provides superior thermal value and resists moisture, insect, and rodent infiltration.
IMPs are available in a wide variety of colors, widths, profiles, and finishes, enabling the realization of
virtually any desired aesthetic for walls and roofs. IMPs can also be curved and formed and come in a
variety of high-performance coatings.
Expanding upon the various profiled options, designers can choose walls that are ribbed, fluted, or planked.
For flat walls, finishes can be flat, textured, or striated.
Additional design features include joint reveal widths, formed corner panels, end folds and treatments,
heavier gauge flat facings, and integrated windows and louver systems. Another available finish feature is
embossing, which creates surface texture on metal coils. This process flattens wavy coils and eliminates the
"mirror” effect of smooth finishes. It is also a useful way to mask minor blemishes such as paint scratches
and surface variations. Nondirectional embossing can be applied to create a uniform pattern, whereas
directional embossing produces linear lines along the length of the coil.
Typically, the most used metal substrates for IMP faces are G90 galvanized steel or aluminum-zinc coated
steel, while some custom panels are made from stainless steel or aluminum.
For the interior, a typical finish is a standard polyester 0.8 mm—including the primer—in a light-reflective
and easy-to-maintain color. United States Department of Agriculture (USDA)-compliant finishes and stainless
steel also are available for required applications, such as food processing and storage.
Performance-wise, architects can specify various panel insulation values, span lengths, and load/span
capabilities.
In the field, IMPs are not only considered the primary exterior finish, but now also are being designed as
the primary building envelope, and can be clad with various exterior cladding systems, such as brick veneer.
Where They’re Found
Commercial and Industrial: IMPs are ideal for all types of commercial and industrial buildings
including institutional, recreational, government buildings, and manufacturing facilities. Projects from
schools to retail centers to power plants benefit from the unique energy efficient insulation, lightweight
construction, durability, and cost-effective, timely installation of single component Insulated Metal
Panels. IMPs also provide solutions for a variety of climate considerations, including temperature,
humidity, airborne particles, and air movement, among others.
Architectural: Architectural IMPs not only have the normal attributes of those used in commercial and
industrial builds, such as high insulation values, speed of build, vertical and horizontal applications, but
also incorporate options such as custom shapes and widths, special custom colors and finishes, and custom
fabrication, including, but not limited to, factory bent corners, curved panels, and trimless ends.
Architectural IMPs offer options that can incorporate panels that coalesce with windows, louvers, sunshades,
or other integrated products to offer total building envelope solutions. Their flexibility provides
architects freedom to create unique building designs.
Cold Storage: Insulated metal panels are considered the ultimate solution for climate-controlled
facilities. Whether the need is for manufacturing, processing, storage, or distribution of perishable food
or other materials, an IMP wall can meet the demands. Available in panel thicknesses from 2-6 inches, a wall
can be designed to meet specific thermal performance requirements. Additional features include the panel’s
long spanning capability, flat and ribbed shaped panels, high performance coatings, and special joint
designs and details to meet safe hygiene and contamination requirements.
Insulated Roof: IMPs are the roofing solution that provides greatest insulation, simplest maintenance
and longest life coupled with quickest installation for low- and high-rise commercial and industrial roofing
applications. The essentially two-step installation process limits exposure to accidents, reduces the number
of installation steps and materials required, increasing the speed of installation, and reducing down time,
while providing a roof with superior insulation properties that can last more than four decades.
Sustainable Certifications And Programs
Recognizing the importance of comprehensive life-cycle analysis studies for roofing and cladding systems, the metal industry has invested substantial resources and effort to provide building teams with key product information to help design and build truly sustainable buildings and meet certification goals. Using natural metal materials creates a product portfolio that is well placed to tackle many of today’s biggest sustainability and development challenges. It also offers carefully designed, innovative and sustainable solutions for occupant comfort, safety, and for the benefit of the environment.
IMPs support resilient, high-performance, cost-effective project outcomes. Predictive energy modeling analysis of envelope and thermal solutions and hydrothermal performance can assist in making more informed decisions for an optimized high performance, low carbon envelope first strategy to reduce demand side energy.
LEED, or Leadership in Energy and Environmental Design, is the most widely used and recognized green building certification standard. It is administered by the U.S. Green Building Council (USGBC). LEED provides a framework to create healthy, energy efficient, cost-effective buildings for varying building and purpose types. The LEED process is designed to inspire innovative solutions that support healthy, highly efficient, and cost-efficient green buildings during the design, construction, operation and maintenance of these high-performance structures. There are four levels of LEED certification: LEED Certified, Silver, Gold, and Platinum. All prerequisites achieved attain a LEED certified building and the number of optional credits pursued and achieved can then earn a project a higher certification level. The LEED v4 Green Building Rating System includes revised performance criteria for certifying the design and construction of commercial, institutional, and residential buildings. LEED works for all buildings, regardless of where they are in their life cycle, and in any geographic location. IMPs can generate LEED points within the categories of Sustainable Sites; Energy and Atmosphere; Materials and Resources; Building Product Disclosure and Optimization: Environmental Product Declarations, Sourcing of Raw Materials, Material Ingredients, and Construction Demolition and Waste Management; Indoor Environmental Quality; and Off-Site Construction. Additionally, IMPs participate in LEED® pilot credits for Design for Enhanced Resilience, Tornado/High Wind, and Passive Survivability and Functionality During Emergencies.
The WELL Building Standard, administered by International WELL Building Institute, is the only green building standard to solely promote optimal human health and performance within the built environment. The new WELL v2 standard sets performance requirements in 10 categories relevant to occupant health in the built environment─Air, Water, Nourishment, Light, Movement, Thermal Comfort, Sound, Materials, Mind, and Community. These 10 categories, or concepts, are comprised of universal preconditions and flexible optimizations for a building to achieve a range of certifications. The Materials concept contains preconditions that include restricting lead and asbestos, limiting mercury, abating hazardous materials like asbestos and PCBs, and providing an assessment of outdoor structures for harmful ingredients. Points can be earned for higher certification in the Materials concept when controlling emissions from indoor building materials, reducing hazardous materials in products, and purchasing and installing products with ingredient disclosures via the Declare Label, EPDs, HPDs, or other foreign equivalents.
The Living Building Challenge (LBC) is administered by the International Living Future Institute. The program focuses on seven categories, or petals, across four project types. The seven categories of emphasis are place, water, energy, health and happiness, materials, equity, and beauty. Under these seven categories there are twenty program imperatives. Living Building Challenge compliance is based on actual, rather than modeled or anticipated, performance. Therefore, projects must be operational for at least twelve consecutive months prior to audit in order to verify Imperative compliance. The most recent version, LBC 4.0, was developed based on two goals, to simplify the program and to fill the gap between mainstream green building certifications and the entry point to the Living Building Challenge.