Flooring for Laboratory Designs
Beneficial Characteristics for Laboratories
Vulcanized rubber flooring products offer a number characteristics that are beneficial for laboratory use. In terms of addressing physical requirements, they provide the following:
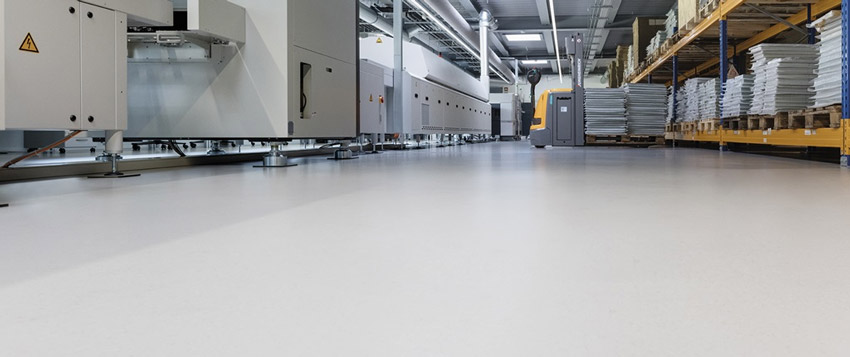
Photo: Dirk Wilhelmy
Rubber flooring can hold up against the physical demands of laboratory settings better than most other flooring options.
- Spill and chemical resistance: Chemicals, acids, oils, bacteria, and similar substances generally sit on top of the nonporous surface of rubber floor coverings. This means they can be cleaned up readily with little or no absorption into the flooring, thus avoiding stains or other deterioration of the flooring. Since the dense surface of the rubber does not readily react with many chemicals, it is not affected and the appearance is retained.
- Hygienic installations: Rubber flooring is typically installed with a seamless process using heat- or cold-welding techniques at junctions of flooring. This means that a liquid-tight environment can be created with no gaps that can leak fluids beneath the flooring or allow the growth of bacterial bioburden.
- Long-term durability: Laboratory and workplace floors are often exposed to equipment loading and foot traffic. Flooring made completely of rubber has superior elasticity and dimensional stability to enable it to withstand these loading and traffic conditions that can otherwise cause wear lines or tracks as they do in other types of flooring. The dimensional stability also means that it does not move under temperature extremes of either hot or cold. Movement or changes in the subfloor can cause cracks to form in other flooring such as epoxy or resin coatings, for example. With rubber floors, this risk does not exist since the elastic nature bridges any cracks to remain permanently intact and attractive. Further, impact effects from falling tools, metal parts, etc. may be lessened by the use of rubber flooring—even fragile objects (e.g., glass containers) are likely to sustain less damage and not break. In case there is any damage to the rubber flooring, either a tile can be replaced or the damaged area can be cut out of sheet flooring and a new piece cold welded into place. Either way, the repair process is quick and simple, making the flooring that much more durable over the long term.
- Flexibility for changes: In the event that rubber flooring needs to be changed to accommodate a change in the laboratory use, the process is pretty straightforward. If tiles are used, then they can be removed and new ones reinstalled. If sheet flooring is used, then it can be cut out and new material installed and heat or cold welded along the seams. Of course, in cases where potential changes are considered in advance, the type of rubber flooring can be selected to meet the most stringent anticipated needs to avoid the need for future replacement.
- Meeting regulatory requirements: The choice of different types of rubber flooring products means that selections can be made to accommodate specific requirements. Among other things, rubber flooring can be selected that qualifies for certification under cGMP regulations for bio-pharmaceutical facilities. This means the rubber flooring is shown to be effective at resisting a full range of chemicals, cleaners, disinfectants, abrasives, etc. in an acceptable manner. Separately, if there are code or other requirements for fire safety in the laboratory spaces, rubber flooring can help in this regard as well since products are available with high fire-retardant properties.
- Simplified cleaning and maintenance: Maintaining laboratory floors means that cleaning needs to be simple and effectively done with the flooring holding up to frequent, sometimes intense cleanings. Rubber flooring can provide these attributes, often reducing or eliminating the need for harsh cleaners in favor of mechanical cleaning approaches. This can include simply buffing out surface scuff marks, wheel marks, etc. to restore the surface to its original appearance. Further, there are no coatings or waxing required on the surface. That means less maintenance time spent adding or stripping wax and the cleaning products and processes related to that.
Based on the above, rubber flooring clearly meets the full range of physical demands for laboratories and similar intense indoor environments. Turning to the need to meet human considerations in laboratories, the following traits are also provided:
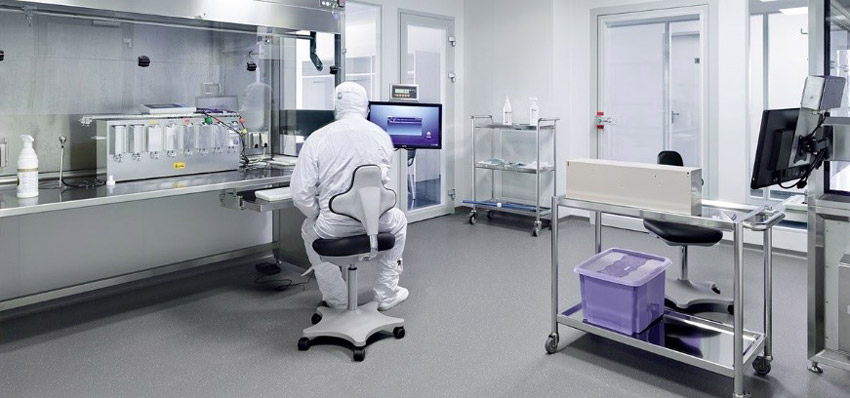
Photo: Oliver Heinemann
Rubber flooring meets many human needs for a positive workplace, including acoustics, comfort, and visual appeal.
- Slip resistance: Rubber flooring has been used in many high-foot-traffic areas for decades with an excellent record of slip resistance. There are several ASTM and ANSI standards used to determine how slip resistant a flooring product can be based on independent testing. There is also the European standard DIN 51130: Testing of Floor Coverings. Rubber flooring has commonly received very positive results for safety and slip resistance when subjected to these tests. Where appropriate, raised circles in the flooring can help with that slip resistance, particularly where water or other liquids may sometimes be present.
- Footfall sound absorption: The nature of the rubber flooring is to cushion impacts from people walking on it and in the process prevent noise from footsteps. It can also help with general sound deadening inside the laboratory compared to other flooring approaches that create echoes. Some rubber flooring has been tested for sound using standard measuring methods, and that information may help with selections where acoustics are a particular concern.
- Human comfort: Rubber flooring has been reported by many people in a number of different settings as being easier on their feet than other types of flooring. This can be attributed to the elastic nature of the rubber material and the inherent cushioning effect brought with it. The result is less discomfort or fatigue compared to standing or walking on hard surface floors.
- Visual variety: The options of rubber flooring types, colors, patterns, and textures allow for design creativity and visual alternatives to a single, uniform appearance everywhere. Tile patterns in geometric or other forms are possible, as are direct inlays in sheet flooring. All of these can be done without sacrificing any of the other attributes of the flooring or compromising on the performance in any way.
- ESD and electrical protection: Rubber flooring with electrostatic dissipative properties are available in the form of ESD flooring that is designed to dissipate the buildup of static electricity on people and equipment. Since rubber has a natural low propensity to charge compared to other flooring materials, it is an excellent choice here. Further, since rubber is also an insulator, it can help protect people and equipment from electrical current as well as static electricity.
While the discussion of all of these attributes has been about rubber flooring, keep in mind that these all apply to the accessory materials associated with it as well. Wall bases can be installed in a flash-cove manner that creates a seamless enclosure around the perimeter of a lab space. Alternatively, separate rubber wall-base products can be specified that can provide a more traditional appearance and installation process. Similarly, adhesives, stair treads, skirtings for floor penetrations, and any miscellaneous accessories can all be obtained. The advantage of getting all of these accessories from the same manufacturer is that they become a coordinated system that helps assure a complete, warrantable installation. It also allows the use of trained installers who are taught to use all of the products properly in accordance with the manufacturer’s instructions and recommendations for best results.
Josiah Woods is a former project manager at Janssen pharmaceutical company and has first-hand experience working in facilities both with resinous/epoxy flooring and rubber flooring. He comments, “What we really liked about the rubber flooring was its durability from blunt impact. In our environment, heavy hoses and metal clamps routinely hit the floor while disassembling equipment. The epoxy floors would chip, and the chips would spread like a pothole over time. The rubber flooring would withstand that impact considerably better with no breach of integrity to the floor.” This speaks directly to the durability and reduced maintenance that is inherent in the rubber flooring.
Nonetheless, in the cases where something did cause damage, he goes on to say, “Any repairs if needed, were cleaner and much easier than grinding down an epoxy floor. It was just a matter of replace the tile and go.” This speaks to less down time of the facility and a quicker, easier means to protect the appearance and cleanliness of the labs.