Improving Energy Efficiency in Single-Ply Roofing
There are numerous methods to attach roof assemblies to the roof deck: the method depends on deck type, wind uplift required, and budget. Deck types vary from wood, to steel, to concrete, where steel decks are the most common. Roof assemblies are typically adhered to concrete decks and even when fasteners are used, they do not penetrate through the entire deck, so thermal bridging is of little concern. In wood and steel decks, however, fasteners are commonly used to attach roof assemblies, and they must penetrate through the deck in order to ensure adequate attachment of the roof system above. The location of the fastener head and plate within the roof assembly has a large impact on the effect of thermal bridging in an assembly. In a typical mechanically attached system, such as in the graphic below, fasteners are installed through all of the layers of insulation and cover board and into the structural deck. This allows for heat transfer from the interior through the fasteners. Fasteners that span from the roof deck through the insulation and cover board can result in a loss of up to 17 percent in R-value. A way to reduce the effect of thermal bridging is to bury the fasteners in the system and install them down as close to the deck as possible, and then adhere subsequent layers of insulation on top. Mechanically attaching the first layer of insulation and adhering the second layer reduces the potential impact to only a 4 percent loss in R-value.
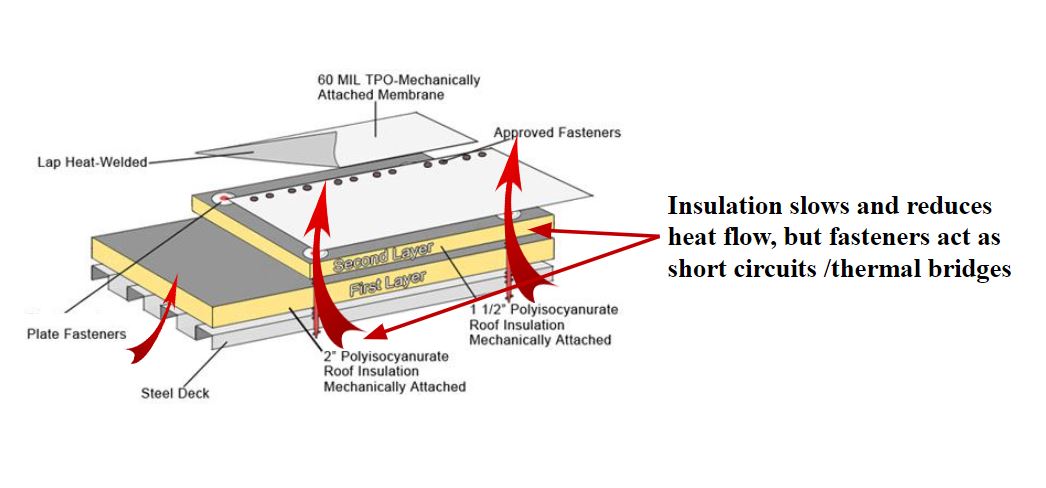
Ultimately, improved energy efficiency at the roof can begin with enhancing solar reflectivity. But if this is not founded on solid specifications that protect the roof against water, air and vapor, and thermal loss, those gains are lost. Cool roof performance needs to be supported by prevention of uncontrolled air movement, proper insulation, and with mitigation of thermal bridging.
Selecting the Best Actor: Contributions of Single-Ply Roofing to Energy Efficiency
Single-ply membrane types include EPDM, TPO, and PVC. The primary differences between the membrane types is their chemical composition, their performance when exposed to chemicals at the roof surface, and treatment of the seams during installation. Since the chemical make-up of each of the membranes is different, certain membrane types are more suitable for different applications.
Single-ply membranes are, as their name implies, a single layer of membrane roof material and are produced in rolls. Single-ply membranes are the most popular roofing membrane today due to their ease of installation and relatively low cost. Due to the nature of a single-ply roof, it can generally be installed more quickly than a multi-layer modified bitumen or built-up asphaltic roof system.
Essential Elements of All Single-Ply Membrane Roofing
Single-ply roofing use in North America traces its origins back to the early 1960s. Since then, single-ply roofing has grown in popularity due to its long service life, dependability, and ease of installation.
Modern single-ply sheets utilize a composite made up comprised of:
- The cap layer, associated with the membrane’s performance relative to the elements,
- The reinforcing scrim in the middle, and
- The core layer that forms the bottom of the sheet.
The cap, or top layer of a single-ply membrane, provides most of the weather protection. It features higher content of both heat and UV stabilizers.
Early thermoplastic single-ply membranes were unreinforced which led to premature failures for certain membranes. In today's single-ply roofing sheets, reinforcement provides dimensional stability, puncture resistance, and limits thermal expansion.
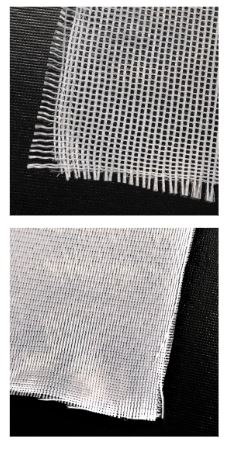
Image shows a low wicking 9 x 9 weft polyester scrim, coated to improve ply adhesion. Windows allow top and bottom layers to fuse together. Bottom reinforcement fabric, must be “primed” before coating during manufacturing.
Reinforcing scrim may be polyester or fiberglass. Polyester scrim is the most common scrim used in the industry and is compatible in mechanically attached, induction welded systems, and adhered methods. Polyester scrim offers a higher point load resistance. Fiberglass reinforcement is not as common and can only be used in adhered systems. However, fiberglass scrim offers more dimensional stability and lower thermal expansion.
The importance of the core, or bottom element of the single-ply membrane, is to facilitate welding to the cap of the adjacent sheet. The core contains an almost identical formula to the cap. The material differs in that it has less heat and UV stabilizers. For cool roof single-ply membranes, no white pigment is needed in the core. Balanced sheets have an equal size cap and core.
Types of Single-Ply Membranes
EPDM (Ethylene Propylene Diene Monomer)
EPDM was first introduced to the automotive industry in the 1960’s and is often referred to as a rubber roof. EPDM quickly gained popularity due to its ease and speed of installation as it is manufactured in rolls that are shipped to the site and installed onto the roof as a single layer. Currently, EPDM roof installations account for approximately 15 percent of the commercial roofing market. EPDM is typically black in color due to its key ingredient of carbon black. However, white EPDM can be manufactured with a different formulation and is available often at an increased price and decreased UV resistance when compared to black EPDM.
EPDM is available in large sheets, which are flexible and bend easily at transitions making it easy to install. Because EPDM is a thermoset material, seams between sheets must be glued or taped, which can lose adhesion over time, especially if not prepared properly during installation. Additionally, EPDM is prone to shrinkage over time, which can put stress on the glued or taped seams if not detailed properly. EPDM has poor resistance to acids, greases, oils, and is incompatible with asphaltic products. Compatibility for any potential chemicals on the roof should always be confirmed with the manufacturer.
EPDM is typically manufactured in thicknesses ranging from 45 to 90 mils and is versatile in its attachment method as it can be mechanically attached, ballasted or adhered, which makes it ideal for a wide range of applications.
Performance highlights:
- Available in very large sheets.
- Very flexible and easy to bend at transitions.
- White EPDM is available but with added cost.