Durability From a Timeless Product
Learning Objectives:
- Describe the history, basic chemistry, and attributes of low-slope asphaltic roof systems.
- Differentiate among BUR, APP, and SBS systems, including raw materials, criteria used by manufacturers in the selection process of modified bitumen systems, and performance implications.
- Analyze the benefits and types of installation methods and surfacing options for modified bitumen systems.
- Examine the properties and advantages of modern hybrid roof assemblies.
Credits:
Asphaltic-based low-slope roofing is one of the oldest low-slope roofing technologies; appropriately, it remains a leader in construction segments such as healthcare, education, hospitality, and mixed use. Asphaltic-based roof systems are durable, have a long history of proven performance, and their redundancy provides owners peace of mind. The benefits of asphaltic-based roof systems include durability and redundancy. When used in hybrid systems that combine modified plies with a single-ply cap sheet, the result is a roof system that offers the best of both technologies.
A Short History of Low-Slope Asphaltic Roofing
All asphaltic roof systems start with the same base raw material. The terms bitumen and asphalt are often used interchangeably within the construction industry: asphalt is the most common reference in the U.S., while bitumen is the preferred term internationally. Bitumen is an immensely viscous material that, depending on its exact composition, can be a sticky, black liquid or an apparently solid mass. Bitumen can be found naturally or it can be a by-product from refining crude oil. Pitch Lake in Trinidad has the world’s largest known deposit of natural bitumen, estimated to contain at least 10 million tons of material.
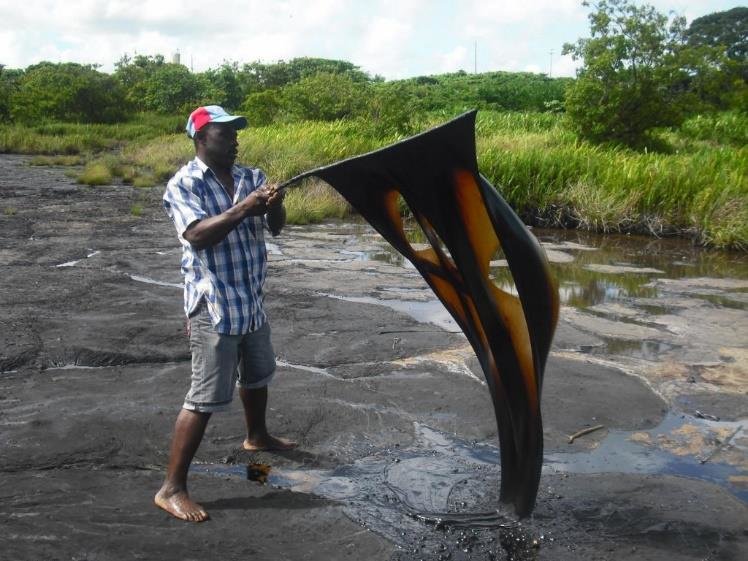
Photo courtesy GAF/Siplast
Natural bitumen at Pitch Lake in Trinidad.
The long history of people and bitumen
The qualities of bitumen have been known and used for human construction projects since ancient times. The earliest estimated use of bitumen dates back 40,000 years to the paleolithic period, where bitumen was used to adhere handles onto primitive stone tools.1 The use of natural bitumen for waterproofing, as well as an adhesive, dates at least to the fifth millennium BC, where it was used in crop storage baskets discovered in Mehrgarh, from the Indus Valley civilization.2 By the third millennium BC, refined rock asphalt was in use throughout the region of present-day India and was used to waterproof the Great Bath in Mohenjo-daro.3 In the ancient Near East, the Sumerians used natural bitumen deposits for mortar between bricks and stones, to adhere parts of carvings into place, and for ship caulking and waterproofing.4
Bitumen in modern times
Documentation of modern low-slope roofs using layers of bitumen and ply sheets to provide waterproofing goes back to at least the 1890s. Multi-layer asphaltic or bitumen roof systems remained the dominant roof assembly of choice until the 1970s and they have continued to endure due to their exceptional hardiness and multiple layers of protection. However, by 2022, asphaltic systems had fallen in popularity: making up about 20 percent of the commercial roofing market. Despite this decline, bitumen or asphaltic roofs are still relied upon today for projects due to their remarkable durability. The redundancy achieved by multiple layers of bitumen provides resilient protection from damage due to heavy foot traffic and during storms and wind events. Bitumen systems can be elastomeric, have built-in puncture resistance, and are compatible with a variety of substrates and conditions. Additionally, bitumen roof systems create an effective, simple, and practical water control system. If the top layer is damaged, the layers below will continue to protect the building from water intrusion.
Not only is a bitumen roof system a time-tested technology with proven performance and redundancy, but modern advances have increased installation options, surfacing variety, and detailing and repair advantages.
Meet the Family – Types of Low-Slope Asphaltic Roofing
BUR
The original asphaltic roof system for low-slope roofs is referred to as a built-up roof (BUR) system. BUR roof systems have been used for more than one hundred years in the U.S. BUR roof systems are made up of multiple, alternating layers of reinforcing ply sheets and asphalt, providing multiple layers of protection. BUR systems remain in use today because of the excellent protection they provide.
The core of the BUR system is assembled using a shingling system of alternating layers of plies and liquid oxidized asphalt, embedding each ply into a layer of asphalt and ensuring substantial overlap with the previous ply. Historically, rags, paper, or asbestos were used as the reinforcing plies. Thanks to technology advancements, the plies are generally asphalt-impregnated fiberglass felts, fabrics or mats. Fiberglass felt plies or glass plies contribute to the fire-resistance of the roof system.
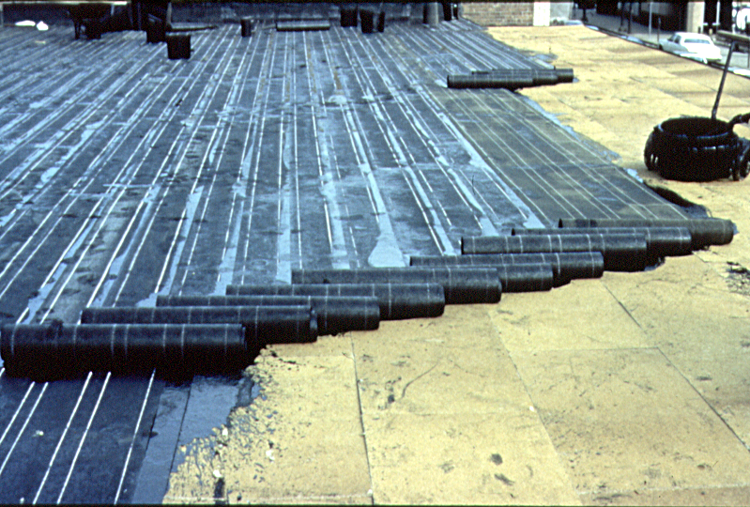
Photo courtesy GAF/Siplast
Installation of a BUR roof system.
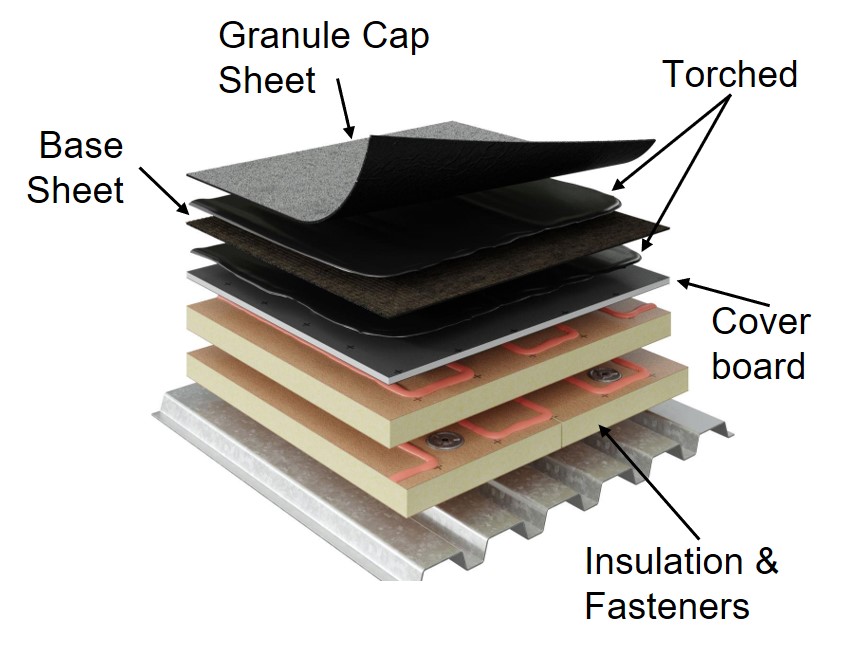
Image courtesy GAF/Siplast
Figure 3. Diagram of layers in a BUR roof system.
Installers traditionally rely on hot mopping of the asphalt requiring kettles, either placed on the roof or on the ground onsite. Advances in manufacturing have created alternative options such as cold-applied adhesive solutions instead of hot mopping asphalt and kettles. Cold-applied adhesives have temperature installation limits, but they can reduce the challenge of keeping an asphalt kettle hot enough during cooler weather.
The layering process is repeated on the roof with the application of asphalt or cold-applied adhesive, followed by the installation of additional plies until the desired number of plies is achieved. The multiple plies, when saturated in asphalt or cold-applied adhesive, create a barrier that provides additional resistance to water intrusion. The complete roof assembly typically ranges from 2 to 5 plies. This installation method can be labor intensive and requires quality workmanship to be successful. The system is then surfaced with either a mineral-surfaced cap sheet or with a flood coat of asphalt and mineral aggregate or gravel, a liquid applied coating, or, historically, slag.
Benefits of BUR
Built up roofing owes its popularity to the number of benefits it provides. It is a time-tested technology, with more than 100 years of history. These roofs provide many layers of protection, so that if the top layer becomes damaged, the additional layers below will continue to protect the building from water intrusion. BUR is, by design, redundant. BUR system materials remain relatively inexpensive and offer excellent fire resistance. However, BUR installation is more labor intensive than other low-slope roofing choices.
Because of its proven performance and resilience, BUR systems may be eligible for guarantees or warranties exceeding 20 years, depending on the materials used and the system installed. Modern BUR manufacturers also offer reflective cap sheets or granules. These cap sheets are available to help reflect the sun's rays away from the building, which can assist in maintaining internal temperatures.
Developments in roofing after World War II
Roofing, and the construction industry in general, experienced dramatic shifts in materials after World War II. This shift in both technology and availability changed how buildings were built. Roofs became noticeably flatter as lightweight steel construction supplanted the use of concrete and wood framing. As roofs became flatter, more equipment moved to the roof and the amount of foot traffic on the roof increased. The greater use of steel created buildings that flexed and moved more, requiring materials capable of accommodating the movement without failures. Additionally, the efforts from the war produced new types of polymers that were used in automotive and aeronautic applications that also found their way into roofing.
At the same time, the quality of BUR materials dropped dramatically. As a result, the industry developed a “new” bitumen that utilized polymers added to a bituminous base. These modified bitumen blends were used to create new membranes with the redundancy and durability of traditional BUR, but with additional properties from the rubber or plastic modifiers. The new formulas were able to accommodate the movement and have increased durability as the modified bitumen had a higher softening point and more elongation.
Creating modified bitumen blends
Modified bitumen used in roof materials is produced by blending together raw bitumen, filler, and polymer which are then layered with reinforcement to create a modified bitumen roll. Not all bitumen blends are the same. The quality of the final material is highly dependent on the quality of raw materials used, the manufacturer’s formulation, and the blending process. It is critical to be aware that there are different asphalt sources of varying quality and different types and quantities of polymer and fillers that can alter the final properties and durability of a material.