The Architect’s Guide to Specifying Sustainable Single-Ply Roofing Membranes: NSF/ANSI 347
Causing an Impact Upstream—Informed Selection of Suppliers
Just as a chain is only as strong as its weakest link, the sustainable quality of a roofing membrane manufacturer is dependent on the sustainable qualities of its key suppliers. Does the supplier comply with local, regional and national environmental requirements? Does it have an environmental management system in place? Does it use renewable energy and track greenhouse gas emissions? These factors, if in compliance, earn a point in NSF/ANSI 347.
If a supplier has a social accountability disclosure process—which includes compliance with local, regional and national labor requirements, as well as documentation of social accountability—the membrane manufacturer earns another point. If the percentage of supplier compliance reaches 33 percent of key suppliers, or 50 percent of key suppliers, more points are possible.
At the minimum, these thoughtful point categories cause the membrane manufacturer to examine its own choice of suppliers, and perhaps to make choices based on these criteria.
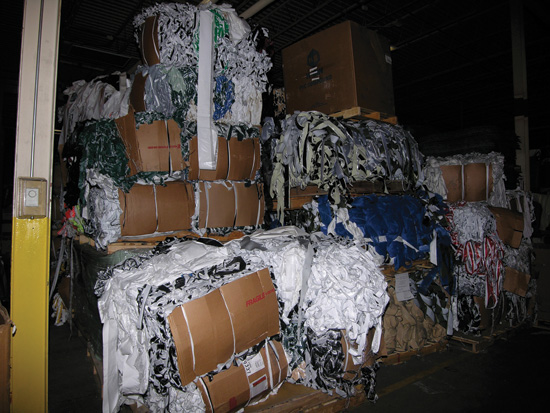
Photo courtesy of Duro-Last
Recycling and reclamation programs earn points in the standard.
Recycling and Reclaiming Roofing Membranes
For single-ply roofing membrane materials, unlike some other roofing products, there is potential for recyclability. The standard awards points for recycling post-consumer membranes into durable products with a documented 5-year or 10-year life expectancy. When a program for reclamation is in place—including chain of custody, tracking and a take-back process—points are awarded for achieving increasing annual performance targets. This encourages the membrane manufacturer to make a start on this process, with tens of thousands of pounds per year of reclaimed roofing membrane the first 2 years, twice that for the next 3 years, and four times that for years 6 and beyond.
In the Factory: The Roofing Membrane Manufacturing Process
Once the design, sourcing and recyclability factors are assessed, it's time to turn our attention to the actual manufacturing of the roofing membrane materials. Ideally, the items included here cause manufacturers to ask themselves: How do our manufacturing processes impact the environment, and how can we further improve on that?
As usual, improvements in procedures begin with policies and a formal Environmental Management System (EMS). To earn the maximum of 6 points, the membrane manufacturer should create a system that is specific to the manufacturing site, and have that audited annually. In addition, the EMS should be registered with a qualified third party. The intention is transparency and accountability.
In the development of NSF/ANSI 347, the stakeholders wanted to ensure that the environmental planning that was set into place during the design process would be carried through into manufacturing. Anyone familiar with the design and construction of buildings, and the disconnects that can happen between the designer and builders, will appreciate the importance of this effort. An extra point is available for a tracking system.
Conserving Energy and Considering Energy Sources
What would an environmental assessment be without attention to energy conservation? And of course, it is not only the direct energy metrics we worry about, but equally importantly the resultant greenhouse gas emissions from the production of the energy used. Save the energy, reduce the emissions. In the standard, membrane manufacturers earn points for both reduced energy consumption and for transitioning from energy from non-renewable sources to renewables such as wind, solar, biogas, and geothermal.
Also, the team that developed the standard had an awareness of the extra energy needed for operation of new pollution control equipment, recycling equipment and/or the increased energy needed for certain processes implemented for environmental benefits. Therefore, those increased usages will not be included in the calculations for the initial 5 years those processes are put in place.
Water and Waste Worries
Drought is still a significant issue in many parts of the Southwest United States, and along with growing awareness of the effects of global warming in general, has contributed to the inclusion of water conservation considerations in the single-ply roofing membrane standard. Manufacturers can earn points by an inventory of water used, and how it's used, along with reducing that consumption, and for using internal cooling loop processes to reduce water discharges. When the wastewater reaches drinking water quality standards, more points are awarded.
Further along the membrane manufacturing process, minimizing waste is important. Membrane manufacturers can reduce what goes to the landfill, minimize packaging materials, and document a recycling or reclamation program for used pallets.
Greenhouse Gas Emissions
Ideally, in the production of roofing membrane, there would be no release of greenhouse gasses (GHG). The manufacturer is encouraged to complete a baseline inventory of GHG emissions in accordance with ISO 14064, EPA standards, protocols established by the World Resources Institute (WRI) and World Business Council on Sustainable Development (WBCSD) or an equivalent standard.2
Looking past the initial assessment, the developers of this standard provided incentive for continued progress with increasing points for reductions of 2 percent, 4 percent and 6 percent.
Finally, a roofing membrane manufacturer is rewarded for participating in a GHG reporting program, where they annually inventory and report their emissions. Again, transparency of environmental impacts is stressed and incentivized.