Labor Shortage Solution Specifying a Factory-Made Roofing Membrane
CASE STUDY 1
A Revitalized Solar Roof for San Francisco’s Davies Symphony Hall
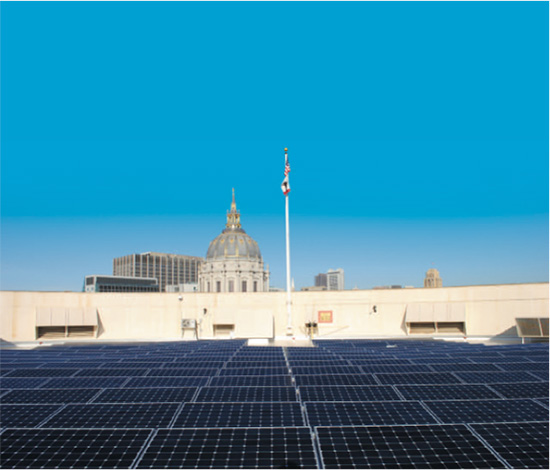
Photo courtesy of Duro-Last
The 25,000-square-foot roof of the Louise M. Davies Symphony Hall in San Francisco was slated for a photovoltaic solar system. However, a deteriorating roof had to be addressed first.ancisco was slated for a photovoltaic solar system. However, a deteriorating roof had to be addressed first.
San Francisco has long been known as a center for culture and the performing arts. Showcased by its War Memorial Opera House, considered the last Beaux Arts building constructed in the United States, this legacy continued with construction of the adjoining Louise M. Davies Symphony Hall. Opened in 1980 and renovated in 1992, its modern design was a collaboration of architects and acoustical engineers working in concert to create an intimate environment to enhance the music of the San Francisco Symphony and the beauty of the structure itself.
A few years ago, the San Francisco Public Utilities Commission (SFPUC) determined that installing a photovoltaic (PV) solar system on Davies Symphony Hall would benefit the people of San Francisco. The SFPUC retained engineering consultant AEPC of San Ramon, Calif., to design the PV solar system for the 25,000-square-foot roof.
The project team for the roof revitalization and PV solar system installation included Technical Roof Services (TRS) of Concord, Calif., and Fidelity Roof Company of Oakland, California.
Moisture Issues Emerged
Initially, the installation of a rooftop solar energy system seemed to be straightforward. However, significant moisture issues were discovered in the underlying roof insulation, contributing to deteriorating conditions in the 14-year-old tar-and-gravel roof.
“We knew the roof had some leaks and wanted to correct any problem areas before the solar panels were installed. Our goal was to ensure that the roof could last the life of the solar array, or a minimum of 25 years,” says Venk Mani of APEC.
“We were aware of leaks in the exterior concrete walls but there had to be another source of wetting,” adds Phillip Dregger of TRS. “The wet insulation on the roof just didn’t follow any typical patterns.”
After exhaustive testing, TRS and Dregger determined that there was substantial moisture leaking around the HVAC duct support posts that contributed to the saturation of the roof’s insulation. It was clear that extensive repairs were needed, including replacing the 4,000 square feet of wet insulation, to protect the longevity of the new roof system.
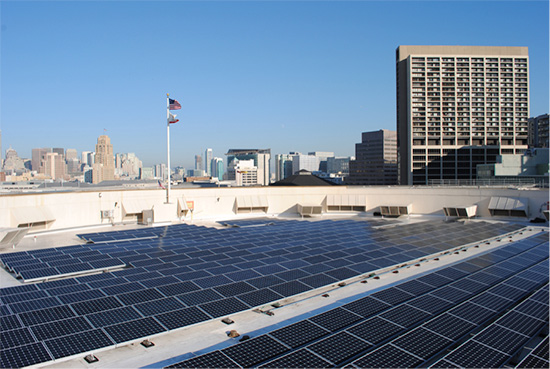
Photo courtesy of Duro-Last
Specifying a roof that would last as long as the overlaying solar array was the paramount concern.
The solar panel installation was the primary consideration.
“It’s relatively expensive to turn off and disconnect a solar array and to repair the roof,” Dregger explains. “Therefore, the owner required the roof life to match the service life of the PV system. In other words, they needed a new roof.”
Options for Roof Ready for PV Solar
The SFPUC was presented with two available options:
- Tear off the current roof and install a new one.
- Overlay the existing roof with a new membrane.
The SFPUC opted to re-cover the existing roof as replacing the old roof would take longer and interfere with the symphony’s rehearsal and performance schedule.
After evaluating the available membrane alternatives, Dregger recommended a white 60-mil-thick thermoplastic PVC roof system.
“Dealing with the dust, debris, odors, and noise would be important considerations on this project,“ he explains. “The PVC roof membrane would be quicker to install. Additionally, we needed to mechanically attach the cover board and new roof membrane through the existing roof down to the concrete deck.”
Material Prefabrication Expedited Installation
Prefabrication was another advantage of the roofing system selected. The membrane was prefabricated into rolls that were 22 feet wide, reducing the application time and on-site welding.
In addition, the penetration flashings, parapet wall membrane, membrane curbs, solar hold down boots, and other related roof materials were all custom fabricated at the factory. This not only assured installation accuracy at changes in plane on the roof, such as projections, curbs, drains, perimeters, and abutting walls, but of equal importance was the roofing company’s ability to expedite the installation process and meet critical deadlines.
Solar Ready
The first step in the roof overlay process was to remove the existing gravel from the built-up roof as well as the wet roof and insulation areas. Once cleared, the design called for half-inch, high-density gypsum cover board to be mechanically fastened through the existing roof and insulation, to the concrete deck, which provided a smooth surface for the adhered 60-mil overlay membrane. This process assured the roof met wind uplift as well as seismic design requirements.
Working Around Rehearsals and the Streets of San Francisco
Scheduling commitments at a busy location in the center of the city meant that the materials and equipment could only be delivered and crane-loaded onto the rooftop on weekends.
Work schedules were adjusted to meet the symphony’s pre-established rehearsal and performance requirements. This meant sometimes working late into the evenings and weekends to meet the scheduled completion. The on-site time and labor saved by the prefabricated roofing system helped keep the project on track.