Labor Shortage Solution Specifying a Factory-Made Roofing Membrane
Roofing Failure Consequences
Studies of roof failures show that many problems occur because of installation errors, particularly at changes in the plane on the roof, such as projections, curbs, drains, perimeters, and abutting walls.
It is often during forensic investigation of roofing failures that installation or compatibility errors are discovered. For single-ply membrane roofing, the errors can include open laps from improper on-site heat welding, loose flashings from improper on-site fabrication and installation, loose flashings from sealant failure, compromised flashings that are made of unreinforced membrane material, etc.
The consequences are immense. While exact statistics are difficult to come by because of out-of-court settlements, one industry source calculates that approximately 60 percent of litigation claims related to a building originate from the roof area. And that can be tough news for architects. High-profile litigation cases include:
- Architect Frank Gehry and a construction company were sued by the Massachusetts Institute of Technology for leaks, cracks, and drainage failure in MIT’s $300 million Stata Center.
- Santiago Calatrava, a world-famous Spanish architect, faced legal action in 2014 from his native city of Valencia after the roof fell off the opera house he designed. Calavera faced more legal action from the owner of a winery with a persistently leaky roof.
When considering the design of imaginative buildings, it’s hard to fault architects for their vision. As Frank Lloyd Wright famously declared, “If the roof doesn’t leak, the architect hasn’t been creative enough.”
In most commercial building design, however, the design program is fairly straightforward. Still, a typical roofing installation presents craftsmanship challenges for the installers: on-site seaming, flashings of projections, edge details, and so on. If these challenges are not skillfully met, leaking problems will likely develop.
For the health of the building, as well as the health of designer’s reputation and finances, specifications that remove potential problems are worth some consideration.
Factory Controls Bring Many Benefits
There are multiple benefits to fabricating components inside a controlled environment like a factory. The workers and materials are protected from weather, which means fewer lost days to snow, storms, or heat, and less damage to the materials because of weather.
The workers in a factory can be trained and supervised more easily. This means fewer construction defects, which means fewer building failures, lawsuits, and unhappy owners and tenants.
Recycling and reusing materials is more streamlined in a factory than on-site, where massive dumpsters filled with construction waste headed for a landfill are a common sight.
On the job-site, factory fabricated components, such as prefabricated roofing, means that the installation goes faster, and construction schedules get met. In the case of roofing, a custom prefabricated membrane means that workers spend less time on the roof itself, which translates to fewer jobsite accidents, and lower insurance premiums.
Factory-built components that were once cutting edge but have now become commonplace include:
- Structural Insulated Panels (SIPs)
- Precast concrete
- Steel framing
- Roofing trusses
- Membrane roofing
For building owners and managers, custom fabrication of single-ply membrane roofing systems offers several advantages:
- Prefabricated roofing systems are easier to install throughout the year, even during adverse weather conditions. Installation time is reduced so the contractor can get on and off the job quickly. The relatively small amount of roof membrane seaming done in the field is completed with hot-air welding methods, which are virtually unaffected by cold or damp weather conditions.
- Single-ply roofing prefabrication dramatically reduces waste, both during the manufacturing process and installation. The roofing contractor orders the exact amount of roof membrane necessary for roof coverage, rather than a collection of raw materials.
- Prefabrication also appeals to engineers and architects who would like to address a particular structural or aesthetic design problem. Panel sizes, shapes, and colors can be pre-planned and prefabricated to achieve desired visual results.
- Finally, prefabrication allows the roofing contractor to take control of a construction operation in a highly unstable environment. Roofing contractors must plan their roofing projects carefully, and prefabrication affords greater worker productivity, a higher-quality installation, and potentially more satisfied customers.
How a Roofing Membrane Is Prefabricated in a Factory-Controlled Setting
Typically, a membrane manufacturer that offers prefabrication has an engineering services department to provide technical support, including CAD services, to create a roof customized to each building’s specifications.
Membrane sheets are manufactured and inspected for quality control. According to the plans, membrane sheets are heat-welded together and prefabricated to dimensions as specified by the architect, specifier, or contractor. At least one manufacturer offers prefabricated panels up to 2,500 square feet.
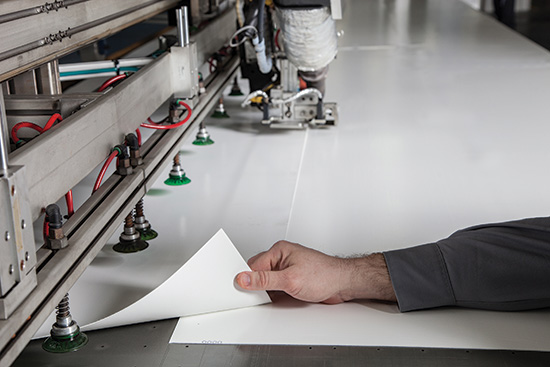
Photo courtesy of Duro-Last
In the factory, the membrane sheets are fitted with welded fastening tabs.