Matching Design Aesthetic with Performance
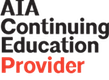
Learning Objectives:
- Explain the basic concept and design elements of louvers in commercial construction, and their primary purpose and function.
- Describe how louvers can help a building achieve thermal comfort and reduced water intrusion by being an integral part of the building envelope.
- Discuss the incorporation of “blank-offs” into louver design and how they add value to a project.
- List the important aspects of testing louver systems to ensure code compliance, durability, and performance expectations.
This course is part of the Mastering Movement™ Academy
BLANK-OFFS EXPLAINED
When it comes to louver design, one thing architects should know is something called a blank-off. It essentially refers to an accessory added to a louver system that does not have perforations or openings. A blank-off is a metal sheet or a system that consists of insulating material encompassed between two sheets, rendering the louver inactive.
Sean Carver, Senior Business Manager for Construction Specialties has a long tenure in working with architects and engineers to incorporate louvers into projects and believes blank-offs have a very unique and important role in a building design. It closes off unused areas of louvers, so if you have 100 square feet of louvers but only 50 are required for mechanical purposes, the quickest solution is to simply take the blank-off and block off the unused 50 square feet of louver.”
While louvers provide ventilation, incorporating blank-offs in the design can offer additional benefits. Blank-offs enhance privacy by restricting views from outside, ensuring confidentiality of more sensitive areas. They also act as a visual break, adding texture and depth to the building facade while complementing the perforated louvers.
There are two types of situations where the temporary application of blank-offs offer exceptional value and performance. One is for data centers that, by design, must provide exceptional security and protection for delicate equipment within. Blank-off panels are oftentimes used to close in a building and prevent some of the construction dirt and debris from coming through so that the servers and high tech equipment can be installed and protected.
Another situation for a blank-off is when a developer has an empty retail space that likely will be occupied at some point in the future. In such cases, an architect may specify a blank-off panel and then when the tenant comes in, they can take off the blank-off panels and use them just like a normal louver. This situation is temporary, but it could be utilized for a longer duration, as compared to the short-term needs of a data center. For the retail space, the blank-off, (when the unused louver area is closed off) is designed to remain in the fixed position indefinitely, until such a time that it can be removed to allow for an update to the building.
There are two methods for the application of blank-offs. Under a standard method, a simple compression gasket is installed on the back side of the louver framing and held in place with fasteners. In many cases, the fasteners penetrate through the gaskets or other wet areas of the louvers, which is particularly problematic. This is what’s known as an “80/20 principle” of blank-offs. In other words, the application will stop most of the water that it faces, but it absolutely will not stop all the water. If such an installation is problematic for a design, specifiers will need to have a backup plan to prevent any water that has penetrated the blank-off system from getting into the building or collecting behind the installation.
But there is another way to attach and seal blank-off panels–one that is not an 80/20 solution like gaskets. Rather, it’s almost 100 percent waterproof. It is called an enhanced method that uses a true weather silicone sealant. The method uses a butyl tape and silicone that’s applied around the edge. The result is a complete unbroken system that almost hermetically seals the louvers.
For the enhanced method to be effective, the sealant has to be tooled. It will not be enough to simply apply silicone sealant in a conventional way. The manufacturer will have to tool it into the joints appropriately or the effort is almost worthless. For the weather seal method to be truly effective and achieve a proper level of water resistance, the manufacturer has to be experienced and highly skilled.
SPECIFYING LOUVERS
The type of louvers architects specify varies from building to building and project need. A parking garage, for example, might require good airflow but not need protection from rain. On the other hand, a data center or mechanical room that contains sensitive electrical equipment may require louvers with strong protection from storms and high-performance airflow specs to ensure that the hardware is effectively cooled. When specifying a louver system, it’s essential that architects and designers have a clear understanding of the project requirements and which louver characteristics will meet those needs.
A common approach to specifying louvers is to have the performance needs dictate or drive the facade and envelope design. By first understanding the performance requirements of the project, the architect can then narrow down the available options in louver design. Paramount to this process is to understand the performance criteria for louvers, then consider security, airflow intake, and exhaust, then expected weather or storm durability, as tested and certified by a third party like AMCA. After the needs of the building and safety of the occupants have been determined, specification sheets from the manufacturer or supplier can be utilized to further narrow down louver options. Depth, free area, static pressure, rain defense, and hurricane preparedness should all be included in manufacturers’ documentation on their louver products.
One thing that is important for architects to remember is how louver size affects airflow. The size of louvers directly affects the amount of airflow they allow. Essentially, larger louvers allow more air to flow into the building, facilitating better ventilation.
Choosing the right size louvers will result in an installation that is much more effective, enabling a steady flow of fresh air and reducing the buildup of pollutants; enhancing the energy efficiency of spaces; and maintaining optimal temperature and humidity levels throughout the year.
But there are other things to consider in relation to louver size. For example, it’s important to be familiar with local building codes and regulations, as some areas have specific requirements for minimum ventilation rates, which must be adhered to for safety and compliance. Architects should know the purpose of the commercial space and the number of people occupying it—for example, high-occupancy areas, such as healthcare facilities, where indoor air quality is critical. Also data centers that need a consistent indoor temperature to protect equipment may require larger louvers to accommodate higher airflow demands.
The physical nature of the site confers other important and related considerations for louver specification, like environmental factors and building orientation. Where the building is located plays a significant role in determining the ideal louver size because areas with extreme weather conditions, such as hot summers or cold winters, may require larger louvers to facilitate efficient heating, ventilation, and HVAC systems. These considerations are especially important in modern society where air changes per hour and general fresh air transfer rates are considered in relation to COVID transmission.
Similarly, how the building sits on the site is an important factor. The orientation of a commercial building, window placement, and other factors can impact the amount of sunlight and airflow throughout the day. Properly sized louvers can help regulate solar heat gain, reducing the need for artificial cooling and optimizing energy consumption.
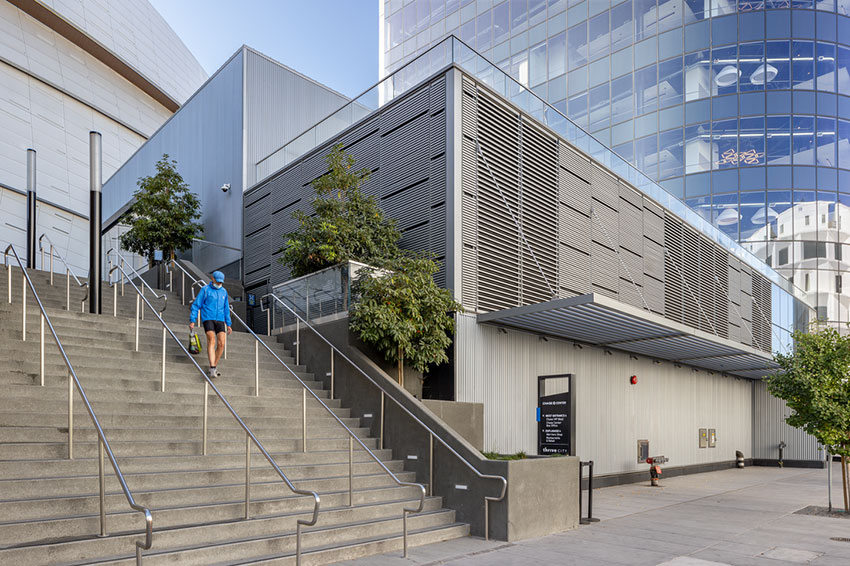
Photo courtesy of Lester Ali Photography
The Uber Offices in San Francisco (Pfau Long Architects) use storm-resistant louvers with strategically placed alternate blade depths to incorporate a dynamic and textured feel to the entrance.
LOUVER STANDARDS
When architects or engineers are deciding on a louver, one of the first things they are likely to do is review a product’s specifications and product performance details. But how do they know if the performance numbers are accurate? That’s an important question because an essential part of selecting louvers for a project is the confidence that the potential product or system meets appropriate performance standards. Knowing how a louver is expected to perform is critical to ensuring that it will stand up to real-life conditions on the job.
The Air Movement and Control Association (AMCA) and other industry standards provide guidelines for testing louvers. Specific tests include static pressure water penetration, wind-driven rain resistance, sand resistance, and acoustical performance. By adhering to these standards, architects and builders can have confidence in the performance and reliability of the chosen louver systems.
AMCA conducts the tests at one of their accredited laboratories where a manufacturer has its louvers tested. With the results of these lab tests, the manufacturer is allowed to post the results on its louver submittal page, along with an image of the AMCA Certified Ratings Program, or CRP, seal. Some louvers can be certified for multiple performance factors and may display the appropriate seals accordingly. These seals help architects identify tested products and then can obtain technical data sheets from the manufacturer.
ANSI/AMCA Standard 500-L helps specifiers understand what testing in accordance with this AMCA standard proves and does not prove about the louvers they are considering for a project.