Specifying Aluminum High-Performance Windows and Doors
Aluminum is 100% recyclable and retains all of its properties indefinitely. It takes just 8% of the energy required to produce products from raw aluminum to recycle aluminum, and it creates just 8% of the emissions of primary production. A 10% increase in recycling rates decreases primary energy demand and greenhouse gas emissions by 15%.
Aluminum is one of the only materials in the consumer disposal stream that more than pays for the cost of its own collection. A 2004 study by Delft University of Technology in the Netherlands concluded that roughly 95% of the aluminum collected from buildings is recycled.
Energy Usage
Energy demand for primary metal production has been reduced by 17%, and greenhouse gas (GHG) emissions have been reduced 42% in the previous two decades. For secondary metal production, energy demand has been reduced 58% and GHGs have been reduced 65%. Today’s electric power consumption per ton is about 50% of what it was 50 years ago and 7% lower than 20 years ago.
A life-cycle assessment (LCA) study by the Aluminum Association reviewed the 2010 production year of 25 companies representing 95% of U.S. production; the study found that primary production energy demand had decreased 11% since 2005 and 25% since 1995. The industry’s carbon footprint has dropped 19% since 2005 and nearly 40% since 1995, and it now uses more renewable hydropower
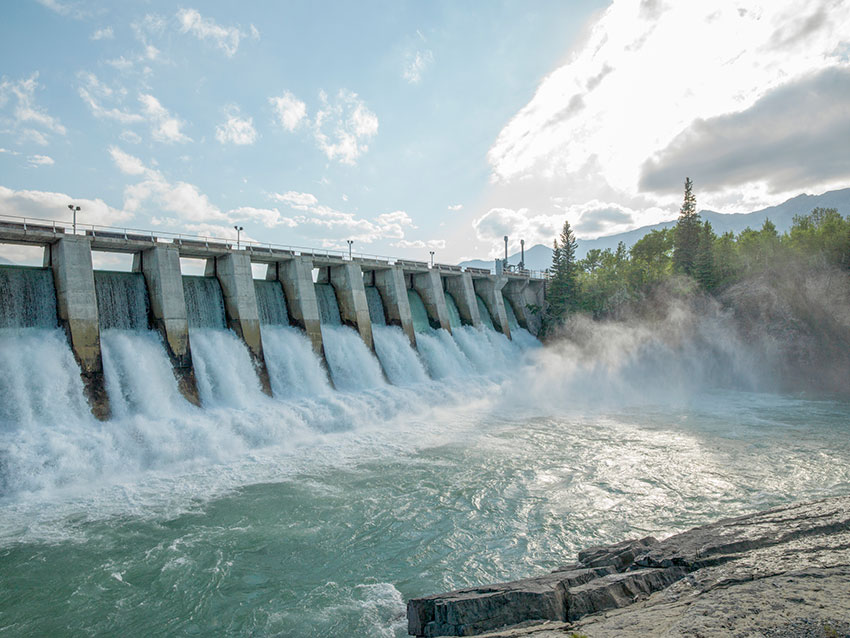
Photo courtesy of AscentXmedia; Getty Images
The aluminum industry’s carbon footprint uses renewable hydropower.
Window And Door Performance Considerations
Even before the pandemic hit, the architectural world was responding to the need for more holistic and healthier designs. Sustainability had been a driving force in new construction for many years, especially in terms of green materials and indoor air quality (IAQ). But a new focus on indoor environmental quality (IEQ) has brought about an awareness of the built environment as much more vital to the health, safety, and well-being of the occupant. Products and designs that could enhance daylighting, better acoustics, aesthetic comfort, and promote positive behaviors around physical and mental well-being have become integral to the conversation.
Aluminum framing is growing in popularity in North America because it has the potential to support IEQ. Its aesthetic appeal and ability to combine with other products that enhance IEQ has increased its demand. And because the healthy building concept includes sustainability within its principles, aluminum meets those needs as well, because of its environmental advantages. Commercial building developers looking for better energy-efficiency can choose high-performance aluminum windows and doors with a range of profiles and colors, allowing for design capabilities that can support overall appeal and brand.
IEQ has become a leading principle since 2020, as people return to offices or create new home-office spaces. Education, health care, and retail building project designers have also begun to understand the healthy building movement as key to their design successes. Research has shown that, for owners, these healthy buildings generally lead to financial gains and expense reductions after they have been built, through improved productivity, reduced sick days, and generally happier occupants.
Thanks to the material being lightweight, workable, recyclable, and corrosion resistant, aluminum is a great choice for healthy and sustainable buildings. Recyclable materials are important in terms of potential demolition and reducing the amount of construction waste that cannot be reused.
Advanced window insulation technology, including the use of dense inert gases such as argon, krypton and xenon in glazing cavities, prevents heat loss and increases soundproofing.
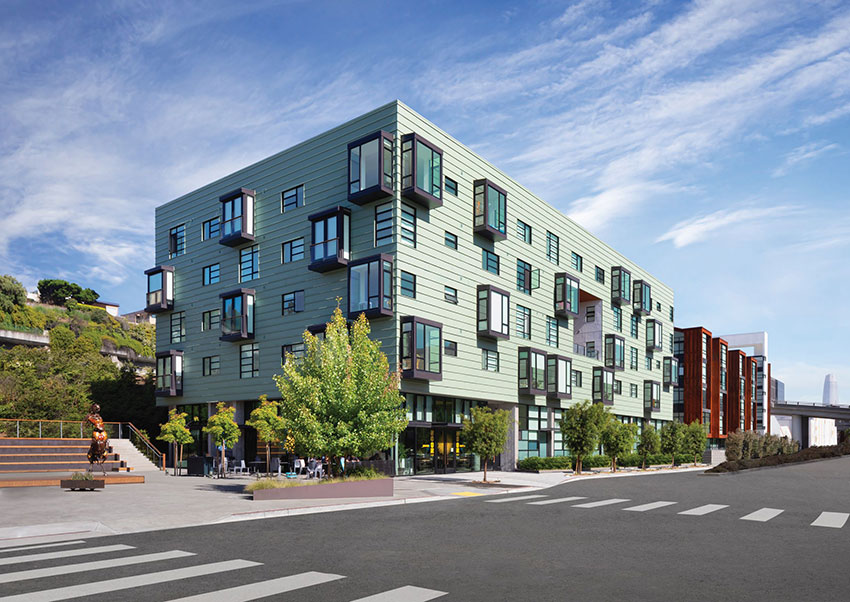
Photo courtesy of Chip Allen Photography
The O & M Indiana Street project in San Francisco is composed of two unique, mixed-use residential buildings set above a destination arts café and features high-performance aluminum windows and doors.
Thermal
When it comes to thermal comfort, aluminum windows and doors serve as part of a larger system. Because aluminum is a good conductor of heat, aluminum frames must be equipped with a thermal barrier that prevents heat from flowing inside to outside or vice versa depending on the climate, time of year, or time of day. Thermal barriers made from resins are incorporated into the aluminum profiles to allow the interior and exterior extrusions of a window or door to come together with minimum heat loss or gain.
Barriers can have thermal conductivities as much as 500 to 1,300 times lower than aluminum itself. The thermal performance of the entire window and door assembly is heavily influenced by that of the frame. Window and door design is intended to achieve the best possible daylight transmission while minimizing heat transmission. Window and door frame conductivity is a function of the frame material, geometry, and design (e.g., thermal barriers in metal frames). The thermal resistance of an aluminum frame is determined more by the surface area of the frame than by the thickness or projected area, as is the case with other frame materials.
A window or door frame profile with a simple, compact shape will perform better than a profile with fins and undulations. Aluminum can be extruded into very thin, very efficient frame profiles. The current technology with standard thermal barriers has improved aluminum frame U-factors from roughly 2.0 to about 1.0. Innovative thermal break designs combined with changes in frame design have also created high-performance frames that achieve U-factors even lower than 0.5. U-factors will be discussed later on in this course.
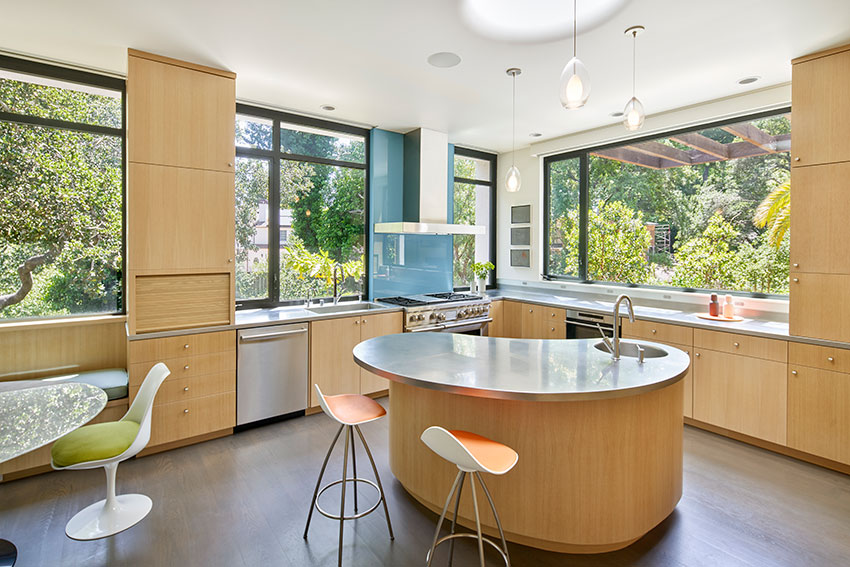
Photo courtesy of Bruce Damonte
Designed by Robert Nebolon Architects, the Hillsborough Residence features thermally strutted frames for increased energy efficiency.
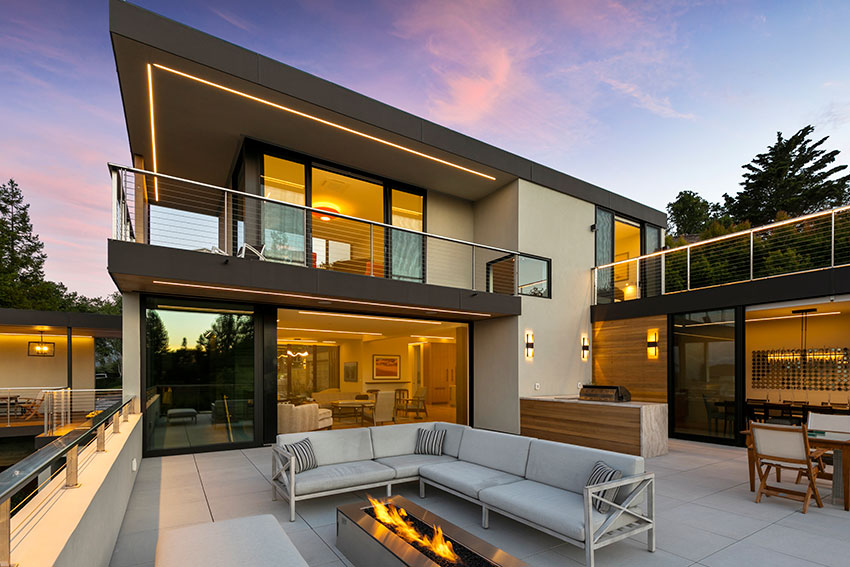
Photo courtesy of Tour Space
The Greenwood Residence windows and doors are made of 6063 extruded aluminum age-hardened to T-6 rating for strength and durability.
Moisture Resistance
Moisture resistance is key to supporting the health, safety, and well-being of occupants. Moisture resistance means better overall comfort and the ability to keep harmful molds from forming and affecting air quality. The glazing industry has made significant advances in moisture resistance and has established the basic detailing principles that should be considered when selecting and designing windows. It is important to select proven and more sustainable window design techniques, such as mitered corners stiffened by spline inserts, molded corner gaskets, vulcanized perimeter gaskets, and shop-applied perimeter collars as opposed to sealants, which can deteriorate over time.
Head Flashings
Use durable metal flashings. Window head flashings should slope to the exterior and be provided with an out-turned drip edge over the top of the window frame. They should extend several inches beyond the frame and be provided with watertight end dams. Head flashings should be sealed to both the inner face of the windows and the jamb flashings. Provide a (4 inch or 100 mm, minimum) upturned leg and counter flashing with wall waterproofing membrane adhered to the vertical leg of the metal flashing. For punched windows in openings that do not allow extension of the head flashing beyond the opening, use dual sealant joints in lieu of head flashing to capture water and direct it to the jamb flashings.
Sill Flashings
Provide sill flashings using durable metal (as opposed to flexible membranes) where they will be exposed. Slope flashings to the exterior and provide an out-turned drip edge over the face of the wall cladding. Provide an upturned leg (1 inch or 25 mm, minimum) on the interior and watertight end dams. Do not penetrate the horizontal portion of flashing with fasteners. Fasten sill frames with an inboard attachment angle through the upturned leg of the sill flashing and into the inboard leg of the sill frame. Membrane flashings may be appropriate for concealed sill flashings, which drain down into the wall cavity behind the cladding or onto sloped precast concrete or stone sills, but are less durable than metal.
Water Penetration
ASTM E1105 is the “Standard Test Method for Field Determination of Water Penetration of Installed Exterior Windows.” It is important to understand the difference between lab testing, which is to the point of failure, and field testing, which is intended to determine that the full assembly meets all ASTM and AAMA standards.
It is also important to understand whether the purpose of the test is to ensure the assembly will perform or whether it is to find the point of failure. Field testing is allowed at only two-thirds the lab test limits. When considering field testing, it is very important not to exceed the allowable stress design of the structure because it will introduce failure. If the structure is designed to withstand 110-mph wind loading, you would test at a pressure of approximately 3.5 psf.
If a window system can withstand two-thirds the lab test pressure in the field, and that equates to 5 or 6 psf, and if the building is only designed for 3.5 psf, then you would introduce failure into the structure or wall assembly. It is important that the expectations of the design team are considered prior to any field testing. Further information on this subject is available in an article entitled “A Discussion on Fenestrations Testing” by José Estrada.
Condensation Prevention
Excess condensation can support the growth of mold and mildew, which can lead to respiratory ailments and increase other health risks. In cold climates, condensation can also lead to ice buildup. Designers should check the required condensation resistance factor (CRF) based on anticipated interior humidity and local climate data and select a window with an appropriate CRF. Buildings with high interior humidity where condensation control is even more critical require project-specific thermal modeling. Thermally broken frames are the most effective means to resist or prevent condensation and ice accumulation.
Placing the thermal barrier in a position that avoids exposing the inboard aluminum frame portion to cold air prevents cold air “short circuiting.” AAMA provides guidance and testing protocols for these issues in AAMA 1503, “Thermal Transmittance and Condensation Resistance of Windows, Doors, and Glazed Wall Sections.”