Concrete Innovations
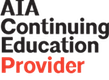
Learning Objectives:
- Describe new technologies used in concrete manufacturing that utilize recycling of materials.
- List ways in which these innovative concrete products can improve project performance.
- Explain how to implement the latest concrete innovations in building and infrastructure projects.
- Discuss the importance of incorporating new technologies to enhance resilience and sustainability in the built environment.
This course is part of the Concrete Academy
Cutting-edge building projects must use durable materials that also help reduce carbon footprint. Concrete is the material of choice for the tallest buildings in the world and infrastructure designed to last centuries. This article explores how new products using pozzolans, calcined clay, biochar, and other innovations enhance a product that is nearly 5,000 years in development and provides another pathway for meeting future challenges in the built environment. The article includes the histories, compositions, and environmental impacts of these technologies and offers case studies to show how innovation is being put into action.
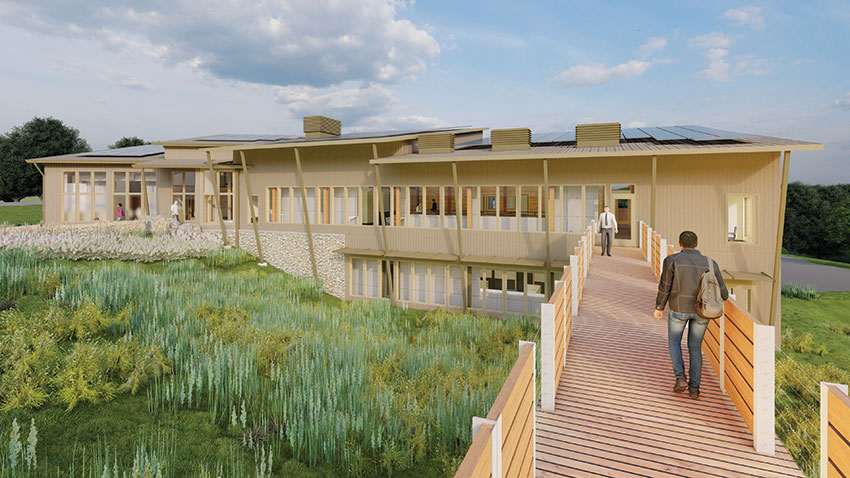
Photo courtesy of TLB Architecture, LLC
The Connecticut Department of Energy and Environmental Protection (DEEP) is poised to complete its new Western District Headquarters at Black Rock State Park in Watertown in fall 2023. The new building will utilize innovative concrete technologies and will be the first net-zero and LEED Platinum building built by the state.
CONCRETE INNOVATIONS OVERVIEW
In recent years, there has been a push in architecture to design and construct buildings that have a lower carbon footprint. This trend is driven by the real need to address the global challenge of climate change and the recognition that buildings are significant contributors to greenhouse gas emissions. There are several strategies for constructing buildings that help with mitigation. Designing energy efficient buildings that are resistant to natural disasters can significantly reduce life-cycle carbon emissions of a building. But another key strategy involves choosing sustainable building materials that have a lower carbon footprint. With new innovations and technologies, concrete is one material that is proving it has the potential to support these reduction goals.
In Connecticut, one state agency is embracing the challenge of climate change mitigation in full force—and aptly so. The Connecticut Department of Energy and Environmental Protection (DEEP) is tasked with mitigating negative energy and environmental impacts, and so it makes perfect sense that the agency should demonstrate its own mission. DEEP’s new Western District Headquarters at Black Rock State Park, located in Watertown, is poised for completion in fall 2023, and will be the first net-zero and LEED Platinum building built by the state.
The building will be the result of several years of planning. It will allow the agency to consolidate staff from nine outdated buildings that have been, until now, located in five separate towns. Combining them into one building will save energy and money, and it will increase efficiency. The new main building will be designed to achieve LEED Platinum certification and net-zero energy standards. A fully integrated approach to building systems and assemblies was required to maximize efficiency even more and minimize environmental impacts. It became clear to the building’s designers that a thermal mass wall would optimize the site’s solar orientation to reduce overall energy consumption. A Trombe wall was designed to provide passive heating during the winter months, passive cooling during the summer, and improved natural ventilation.
With the combination of earth sheltering, photovoltaics, a geothermal system, radiant polished concrete slabs, and a carefully designed building envelope, the building’s energy consumption will be significantly lower than a comparably sized traditional building. It will result in a 30-40% reduction in energy consumption when compared to a building designed to current building and energy codes. The building will be finished with wood grown from Connecticut State Forests and milled at DEEP’s sawmill.
The use of innovative concrete in this project is key to reducing the carbon footprint. Concrete is a durable building material that provides environmental benefits due to its longevity. But its environmental impact can be reduced with new technologies. Traditional cement used in concrete accounts for roughly 88% of its emissions, which means replacing traditional portland cement with alternative materials can have a big impact.
To reduce the carbon footprint of the DEEP facility, the plans call for 40% cement replacement in the structural concrete mixes with a high-quality ground-glass pozzolan—a supplementary cementitious material (SCM) made from 100% recycled post-consumer glass. For this project, the pozzolan was evaluated to determine its effectiveness, availability, and carbon reduction potential. A variety of mixes were evaluated to make up the 40%. The ground-glass pozzolan product for this project is considered a safe, sustainable, and high-performing pozzolan that dramatically reduces embodied CO2 emissions in concrete.
This ground-glass pozzolan was manufactured with 100% post-consumer glass sourced within a 50-mile radius and manufactured in Connecticut, just 16 miles from the site. The local sourcing and manufacturing also help reduce embodied carbon by way of reducing transportation. This pozzolan contains no crystalline silica, heavy metals, or known carcinogens, making it a non-toxic material. Independent testing of the product shows it at 56kg 2e in comparison to the average GWP for portland cement of 1,040 kg CO2e, resulting in 95% less impact.
The new headquarters aligns with the state’s goals to mitigate the climate crisis with an effort by state government to lead by example and identify opportunities for savings and ways to make government operations more sustainable.
The concrete sector is continually seeking new sources of SCMs to help make durable, sustainable, and cutting-edge designs, such as the DEEP headquarters. As a result, the industry is exploring new innovations and old technologies made new again. In this article, we will dig deeper into the history, composition, and benefits of SCMs such as ground-glass pozzolans, natural pozzolans, and limestone calcined clay cement. We will also discuss the benefits of biochar concrete and explore technologies that expand the supply of fly ash. In the process, we will provide greater context for how innovation of a 5,000-year-old technology can help achieve green building goals for architects.
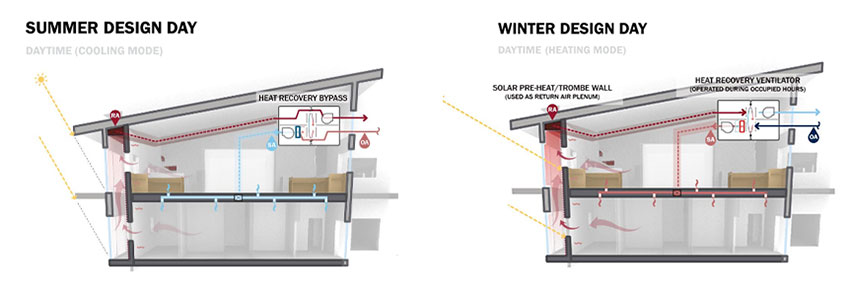
Images courtesy of Atelier Ten (diagrams) and TLB Architecture, LLC
The designers for the DEEP project designed a thermal mass wall utilizing concrete made with post-consumer ground-glass pozzolan cement to optimize the site’s solar orientation all year round. The Trombe wall provides passive heating and cooling and improves natural ventilation.
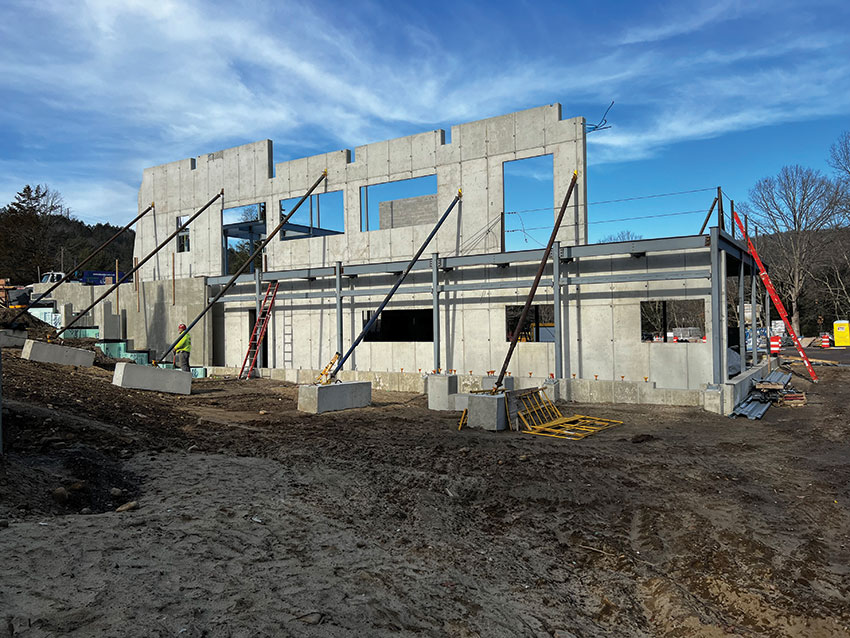
THE WORLD OF POZZOLANS
Pozzolans are materials used as a partial replacement for cement in concrete mixtures to improve its properties, such as strength, durability, and workability. The use of pozzolans in concrete dates to ancient times when volcanic ash was used as a binder in construction.
Modern pozzolans are typically made from natural or industrial waste materials, such as fly ash, silica fume, ground-glass, and calcined clay. They are commonly used in concrete mixtures as a replacement for a portion of the cement content, typically 10-50% by weight. The exact amount used depends on the specific properties of the pozzolan and the desired properties of the concrete mix. Pozzolans are finely ground and added to the concrete mix, where they react with the calcium hydroxide in the cement to form additional cementitious compounds, such as calcium silicate hydrate (C-S-H) and calcium aluminate hydrate (C-A-H). The additional compounds help to fill the gaps between cement particles, resulting in a denser and more durable concrete.
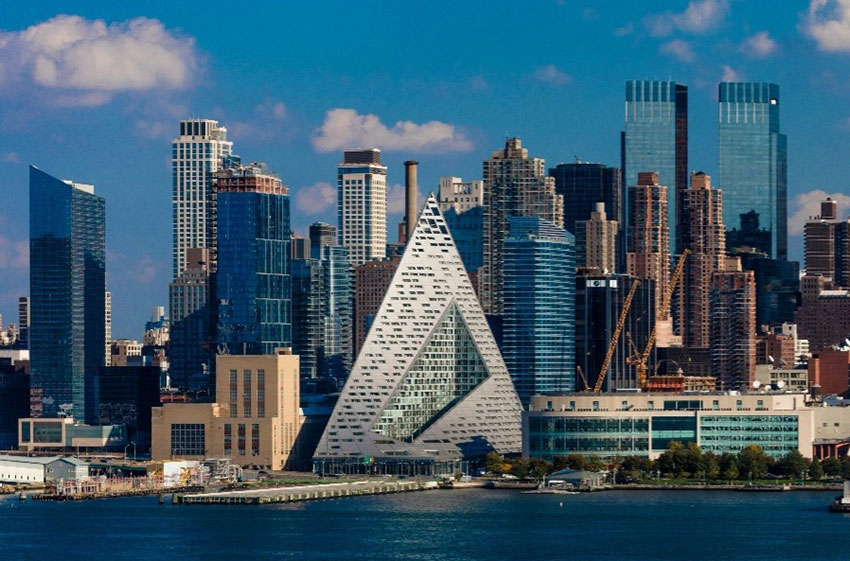
Photo courtesy of spiritofamerica/Adobe Stock
Via 57 West in New York City: This ultra-modern, innovative residential complex was built using structural concrete block, cast-in-place concrete flooring, and precast concrete stairs made with ground-glass pozzolan to help meet sustainability goals.
The use of pozzolans in concrete is a sustainable practice because it reduces the amount of required cement, which is a significant contributor to greenhouse gas emissions during its production. Pozzolans also have other benefits, such as reducing the heat of hydration during the curing process, which can reduce the risk of cracking, and improving the workability of the concrete mixture, making it easier to pour and place. Still, pozzolans vary in how they mix and react with cement, and, ultimately, how they impact the concrete’s durability and carbon footprint reduction. It’s important to have a basic understanding of how these pozzolans work so that they can be highly optimized for an effectively healthy and sustainable built environment.
Ground-Glass Pozzolan
Ground glass pozzolan (GGP) is a pozzolanic material that is made by grinding glass into a fine powder. The glass used in GGP is typically waste glass, such as recycled bottles or window glass, and is generally cleaned and processed to remove any contaminants.
The use of pozzolanic materials, such as volcanic ash, dates to ancient Roman times when the ash was mixed with lime to create a type of concrete that could harden underwater. Researchers began to study GGP potential as a cement replacement in the early 1960s. One of the earliest documented uses of ground-glass pozzolan in modern concrete was in a study conducted by the U.S. Army Corps of Engineers in 1963.
Since those early studies, research on GGP in concrete has continued to grow, with numerous studies conducted to evaluate its effects on concrete properties. These days, the use of GGP in concrete is gaining popularity, with several companies producing it as a commercial product for construction projects. Over the past 10 years, high-performance GGP has been utilized in a range of high-profile applications such as the United Nations Plaza pavers, sidewalks, and subway stations in New York City, the Google Headquarters in Mountain View, Calif., and in the nation’s first high-rise use of GGP.