Causing the country more than a trillion dollars in damages each year, corrosion is a major issue to contend with. Occurring as a natural process, oxides develop over time, weakening materials and making them vulnerable to a variety of performance and protection issues.
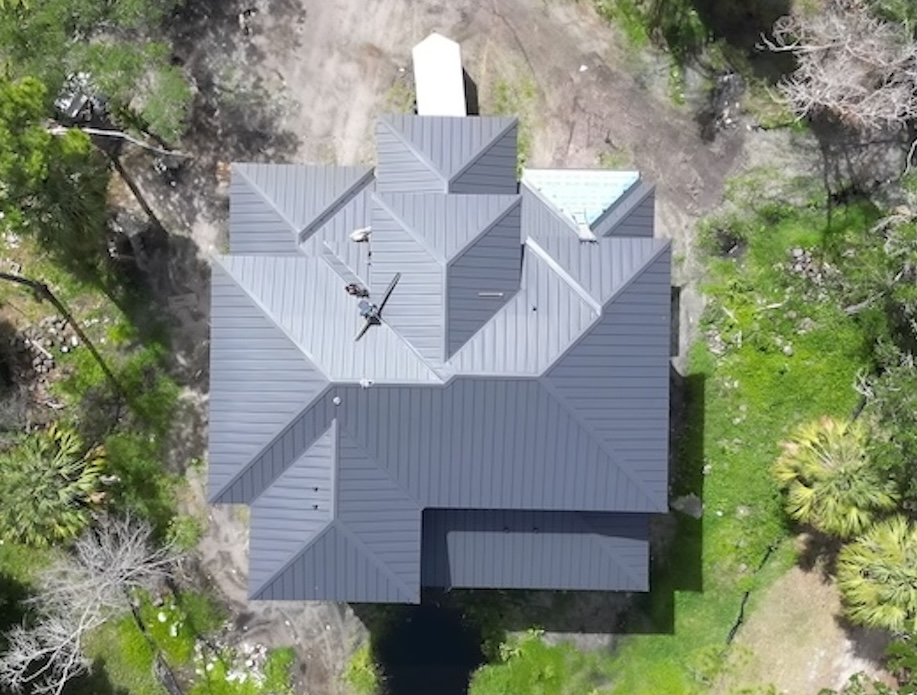
Photo courtesy of Fluorogistx and DuPont
A new steel roof, protected by highly durable PVF film, was installed on this multi-million dollar three-story home, 100 feet from the Tampa Bay. This roof was chosen specifically for its long maintenance-free warranty and excellent wind uplift in this corrosive and hurricane-prone environment.
Metal exteriors are particularly vulnerable, especially in corrosive environments such as areas of exposure to salt spray (coastal regions) or certain chemicals and off-gassing (manufacturing facilities, chemical plants), where this type of deterioration can occur ten times faster than in average environmental conditions.
Defined as a chemical or electrochemical reaction between a material and its environment, corrosion causes deterioration of building materials and its properties over time.
As the protective layer, typically a paint or coating, begins to exhibit cracks and peeling, the exterior is left exposed to reduced mechanical strength, structural damage, and potentially reduced seismic performance. If the structure is compromised, the resulting required repair work can be substantial, causing a significant financial expense to building owners, not to mention the environmental considerations of rebuilding and repair.
Fortunately, corrosion is preventable, as Joseph Crissinger, CSI, CCS, CCCA, ASQ, a Spartanburg, S.C., construction specifications, materials, and building systems consultant, explains, “Isolating the metal or substrate from unacceptable conditions will usually prevent corrosion. That is where the proper protective (corrosion-resistant) coating comes in.”
THE RIGHT COATING FOR CORROSIVE ENVIRONMENTS
While a number of exterior coating products offer a certain level of protection from these challenging environments, few are truly capable of shielding exteriors in these harsh settings. So, while some of the different paints and coatings may be sufficient under ordinary environments, when it comes to highly corrosive and coastal settings, a more robust solution is needed.
Polyvinyl fluoride (PVF) is a highly durable fluoropolymer used in films and coatings that provides an exceptionally long-lasting finish to a wide variety of surfaces exposed to harsh environments. PVF is a sustainable solution due to the longevity it enables, generating less waste over a building or structures lifetime due to reduced replacement. Furthermore, PVF is a non-PFAS material, nor is it manufactured with the use of any PFAS materials.
Not only do these protective films and coatings meet specifications for AAMA 2605, but the real proof of the pudding lies in the fact that this technology has been successfully protecting surfaces around the world for the past 60-plus years.
PVF polymer has been used in coatings that protect brake tubes and fuel lines in automotive applications due to its flexibility and resistance to rock spray and salt corrosion. PVF also has a long history of being made as a film, which has been specified into aircraft interiors since its invention due to its cleanability, durability, and excellent fire and smoke ratings.
Used for interior sidewall decorative panels, window shades, lavatories, bulkhead partitions, and more, the film offers a high level of interior design flexibility. PVF film can be embossed and printed on, supporting many flat and textured designs, and can be tailored to various gloss levels, thicknesses, and finishes.
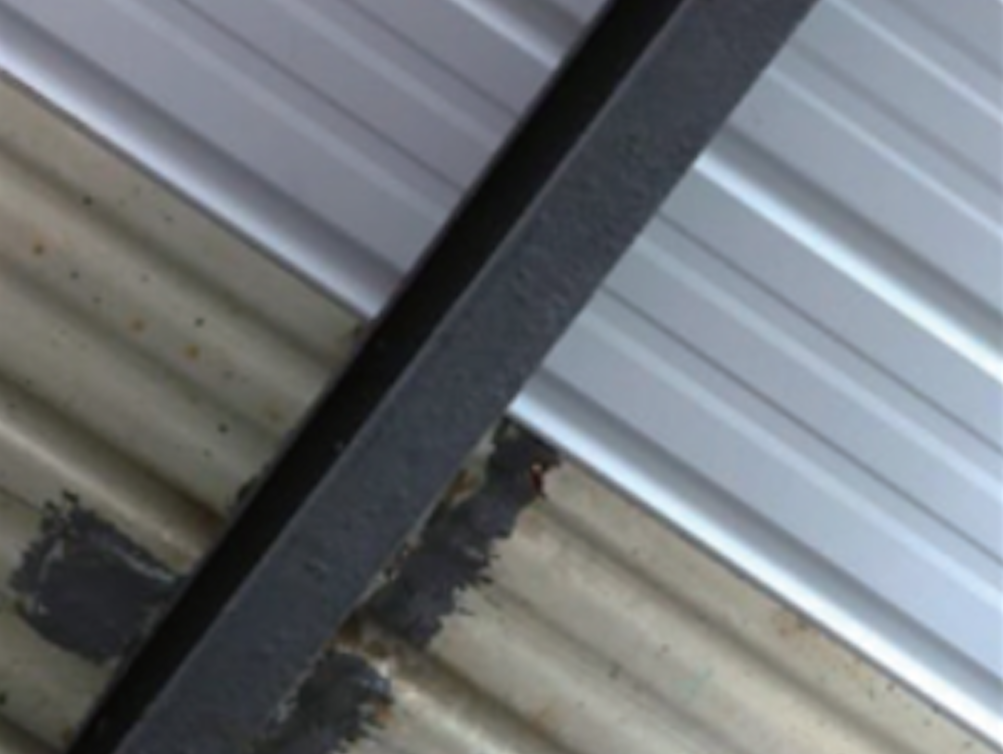
Photo courtesy of DuPont
Inside roof of chemical plant. PVDF paint on bottom left after ~2 years, PVF film at top right after ~8 years.
PVF film also has long-term track record protecting buildings. In fact, the film has demonstrated an unusually high level of long-term performance and durability in various highly corrosive environments.
Take the Okinawa power plant in Japan, for example. Situated less than 1,500 feet from the coastline in a high salt spray environment, and exposed to power plant smoke since 1986, the exteriors essentially look the same as they did upon installation 27 years ago. The PVF film-laminated walls and roof still deliver the same level of corrosion and protection. The plant has experienced practically no color fade as well, and has not required replacement of any panels.
The specification of such a long-term solution offers clear sustainability benefits. The extraction and manufacturing of steel or other metals occurs once and lasts for decades. The life-cycle embodied carbon, in turn, is significantly lessened, as the lifespan of each panel is increased, necessitating less material replacement over a building's lifetime.
Testing and other long-term case studies have also demonstrated an extremely high level of resistance to harsh weather, UV light, chemicals and pollution. PVF film is highly resistant to stains, and is easy to clean and disinfect. As a dirt-shedding material, it retains a new, fresh appearance and doesn't require freshwater rinses in warrantied exterior applications. Due to its hardiness and cleanability, PVF film is also a great solution for wallcoverings in high-traffic, sterile environments like hospitals and healthcare facilities, as well as restaurants, hotels, and airplanes.


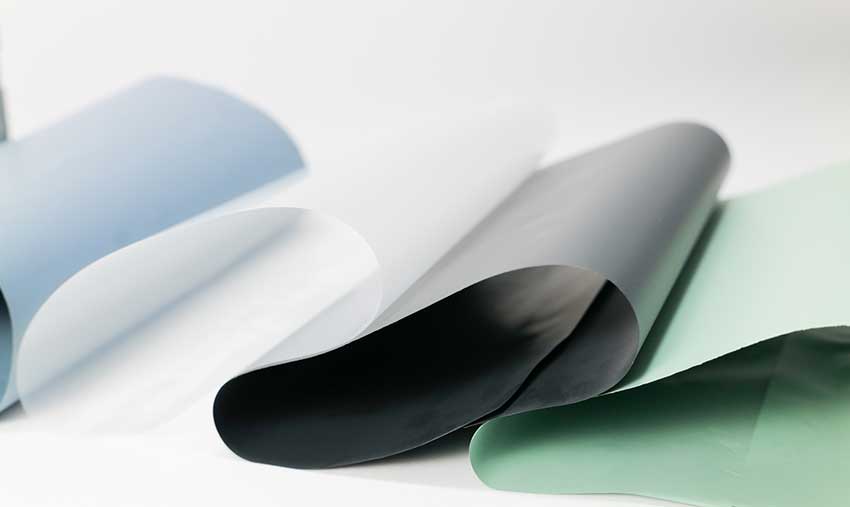
Photo courtesy of DuPont
PVF film offers a wide range of colors, matching popular coil coating colors, and transparent UV-resistant film.
METAL EXTERIORS
PVF film has distinguished itself as a superior solution for metal facades and roofs, particularly in harsh coastal environments with prolonged exposure to saltwater.
The polymer is highly inert, which makes it resistant to a wide variety of corrosive and chemical agents. It absorbs very little visible or UV light and is therefore highly resistant to photolytic degradation. Strong, flexible, and fatigue-resistant, the polymer is made without plasticizers and therefore does not promote growth of mold and mildew.
The material meets ASTM testing and performance standards including UV resistance, moisture absorption, strength, flexibility, clean ability, weathering, chemical and stain resistance. In addition, the film meets stringent smoke and fire codes.
Whereas paint requires a more involved application process, with a primer, topcoat, and often a third clear coat for extra protection, PVF film is applied via a single layer lamination process. The film, with adhesive, is laid down onto the metal coil and baked through an oven, setting the adhesive. The film is then part of the metal system, just as a coating would be, requiring no solvent drying time, or additional passes.
Since metal is particularly vulnerable to corrosion, building owners in coastal settings really have to consider the best level of protection for the roof and cladding. While some coil coatings can offer good protection, they are unable to meet the performance level of PVF film. Ultimately, corrosion will start to eat away at the integrity and appearance of the metal exteriors. The panels will need to be repainted, or more likely, replaced entirely. Not only will owners incur this expense, but the use of resources is an environmental strain. In addition, albeit temporary, the restoration process may disrupt the building’s regular operations and ability to run its business.
When PVF film is the protective layer of choice, the building is then set up for long-term protection, backed by up to 50-year warranties, with no coastal restrictions. In harsh operating environments such as steel mills or chemical plants, replacement of interior panels is expected and budgeted for every two years, sometimes less. Using PVF film, these interior panels can last upwards of eight years without damage, significantly reducing the time and cost of frequent replacements, as well as reduced waste over the buildings lifetime.
The composition of the PVF also lends a high level of flexibility and formability for enhanced adherence to the substrate. Cracking and corroding often happens on the bent part of formed panels. PVF is inherently extremely flexible, bending to 0T without any issue. This flexibility means the film does not crack or weaken when formed, so protection remains uniform across all bent edges and panel shapes.
Highly flexible, PVF film is available in a wide range of colors matched to popular coil coating colors, as well as transparent UV-resistant film. Ranging from cool colors like spruce green and sky blue; to neutral hues such as shell white, charcoal gray, dark bronze, and matte black; to warm colors like concord cream and sandstone, PVF film combines long-term durability with high quality aesthetics.
Leveraging its excellent color uniformity and fade resistance, PVF film-coated surfaces maintain their original appearance for decades.
RESILIENCE IN CHALLENGING CONDITIONS
Coastal counties of the U.S. are home to 129 million people, or almost 40 percent of the nation's total population, according to the NOAA Office for Coastal Management.
While steel is known for its durability as a roofing and siding product, it is not always recommended due to perceived vulnerabilities in coastal environments. However, a new roofing product has arrived, made specifically to withstand coastal weather challenges.
Beginning with a cold-rolled steel that is hot-dipped in aluminum and zinc alloys and combining this with a PVF film, which resists corrosion, UV damage, and cracking, steel roofing transforms into an exceptionally strong, corrosion-resistant, and resilient coastal construction solution.
The PVF-coated Galvalume steel product is warrantied at locations as close as 300 feet from breaking surf and 0 feet from bays, marshes, and saltwater and brackish water sources. The combination of technologies creates a revolutionary, maintenance-free, and highly sustainable roofing and siding solution.
The resultant standing seam roofing and wall systems provide strength and protection from extreme weather, reducing the potential for leaks and related water damage, and resistant to chalk, fade, mold, mildew, salt spray, and chemicals.
The product’s advantages also come to bear for hurricane-prone areas. The steel can withstand hurricane force winds, impact, and is also fire retardant. This coastal steel substrate is covered for 25 years, with up to 50 years finish warranty without any upkeep.
UNIQUE APPLICATIONS
Another metal application subjected to corrosive elements included metal pipes that transport LNG, fossil fuels, and other hot or cold liquids. The pipe jacketing is often coated in a PVDF or other paint to add functionality and aesthetics.
PVF films can be laminated to metal piping jackets to achieve excellent corrosion and chemical resistance and stable emissivity to maintain desired surface temperature. Frequent temperature changes can cause condensation; PVF film is also resistant to the growth of mold and mildew in moist or shady environments, maintaining a clean appearance for pipes.
PVF film is ideal for this application, meeting or exceeding ASTM standards C1423-21, C1729-21, C1767-21 for Pipe Jacketing applications and are a non-PFAS material that is both durable in outdoor exposure and highly flexible and formable.
Thanks to the film structure and PVF polymer properties, in decades of real-world applications, PVF remains looking brand new in applications in the most demanding environments, including the coast or chemical plants.
SEA CREST
Situated right on the Atlantic Ocean, Sea Crest Condo’s six-story roof in Hilton Head, S.C., had severally corroded over a period of 20 years.A post-tensioned slab condominium project, the apartments had been overbuilt with a stud frame, steel mansard structure that was open-framed, and the existing metal covering was a 24-gauge Galvalume standing seam metal roof with a PVDF paint finish.
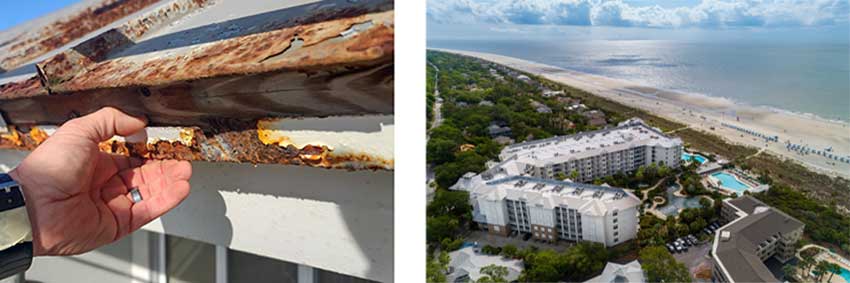
Photo courtesy of DuPont
Lending a high level of protection in this corrosive, salt water setting, 6,700 sq. ft. of roof area was replaced with a PV film-protected metal roof for the Sea Crest Condos in Hilton Head, S.C.
Having incurred significant damage from the saltwater environment, the roof had to be completely replaced. For the new aluminum roof, one option was applying three coats of PVDF finish, but that approach would have required a considerable amount of maintenance on a yearly basis.
Having experience with PVF film, the roofing contractor RPI Roofing presented the option as a longer-term, lower-maintenance alternative.
“We presented this to the [roofing] consultant. It seemed like a good fit for the owner’s long term, due to the PVF performance in color retention as well as corrosion resistance and dirt-shedding capability. And so they chose to go with the PVF film product,” explains Ted Deaton, vice president and estimator, RPI Roofing.
Negotiating around a pool that separated the building from the sand dunes, Deaton’s team scaffolded the area around the building and tore off the badly corroded steel roof.“We had to replace a lot of the hat channel, and did a lot of priming and rust inhibitive painting of the steel structure,” he relates. “Then, using aluminum clips, we installed a PVF-laminated aluminum, double-lock, mechanically-seamed, standing seam roof panel and the associated trim to match the aluminum and the PVF color.”
In installing the 6,700 square feet of roof area, the film’s high level of flexibility allowed it to bend to tight edges on the roofing panels without compromising the film’s integrity or adhesion.
RPI Roofing also liked the scratch resistance offered by the filmed roof panels. “Many times when you're double locking a standing seam panel, and you're on a steeper slope, you get some scratching of the PVDF painted panels from the installation and seaming process,” says Deaton. In fact, this is so commonplace that RPI often has to replace panels as the scratching goes all the way down to the bare metal and there’s no way to hide it. As a more durable and impact-resistant product, the PVF film was noted by installers to be much hardier during installation.
“This project is six stories up and it's not real visible up close like a one-story building would be, but, at the end of the day, there's somebody that's going to look at it and see it,” he says. Deaton also observes that with the humidity in the Southeast, PVDF paint finish can be susceptible to mold and mildew, whereas this is not the case with PVF film, which is unsupportive to the growth of organic matter.
Reflecting back on this successful project, the roofing installation posed very little intrusion for the condominium owner, as the contractors were able to stage the work without affecting their daily routines. In the end, the owners were very pleased with the finished mist gray roof.
J HOTEL
Owners of the new J Hotel in Dunedin, Florida, were seeking a roofing solution that could stand up to the unique challenges posed by the hotel's location right next to a bay in Florida's often harsh, coastal climate.
Working with Fluorogistx and Metal Roofing Systems, they determined a standing seam roof using an innovative blend, combining the strength of galvanized, domestic steel with the corrosion and fade performance of PVF film.
This system is a first-of-its-kind product that combines advanced materials to create a maintenance-free, highly sustainable roofing solution ideal for both residential and commercial uses. It is designed to withstand hurricane-force winds, resist hail and other impacts, and offers unparalleled resistance to
corrosion – ensuring that the roof will maintain its aesthetic appeal over time.
Additionally, the manufacturer offered extensive warranties, including 25 years on the steel substrate and up to 50 years on the finish, with no freshwater rinse required – a maintenance feature that was very appreciated with multiple story structures, as is the case with the J Hotel.
Overall, the owners are very happy with the beautiful final appearance of the roof. With a focus on sustainability, safety, and long-term performance, the J Hotel certainly sets a new standard for future developments in coastal regions.
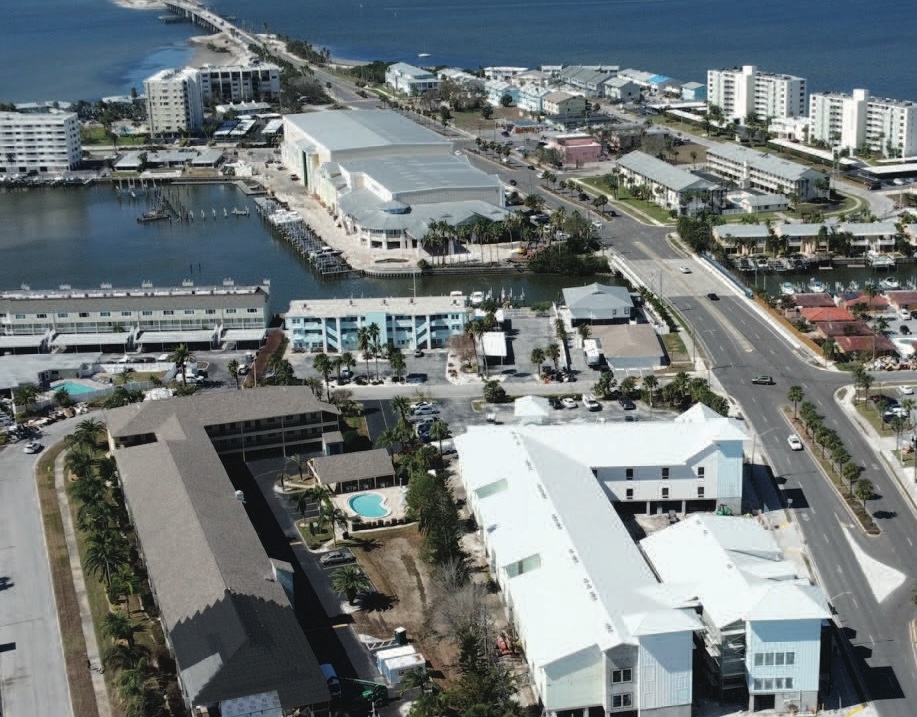
Photo courtesy of DuPont
J Hotel, Dunedin, FL
SPRING CREEK RANCH
For the recent construction of 15 new buildings at the Spring Creek Ranch Hotel & Spa in Jackson Hole, Wyoming, the owner was seeking a highly durable roofing finish to withstand the rigors of this varying climate, which includes many days of intense sunlight, as well as snow, hail, and extreme temperatures.
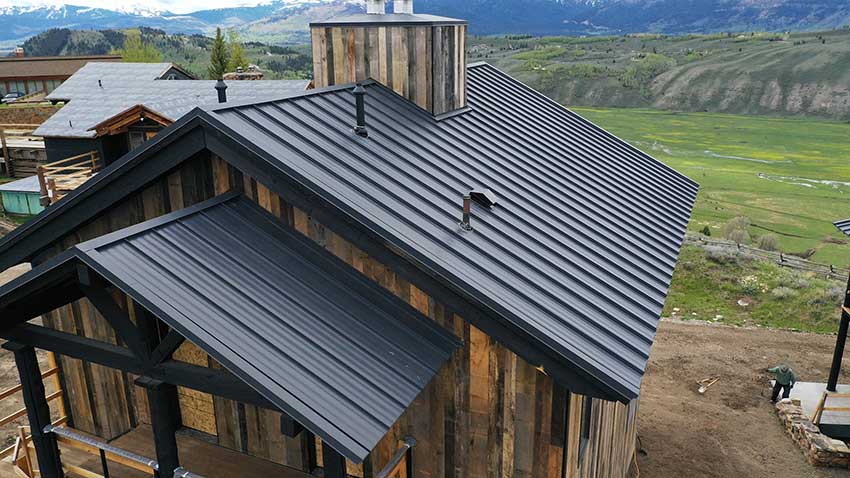
Photo courtesy of DuPont
Delivering aesthetics and a high level of protection, a matte black PVF film covers 15 new metal roofs at the Spring Creek Ranch Hotel & Spa in Jackson Hole, Wyo.
The sought-after ranch features amazing views of the Teton Mountain Range, including the world famous Grand Teton. Delivering aesthetics and a high level of protection, a matte black PVF film was selected for the resort’s rooftops.
With resistance to fading, chalking, cracking, blistering, and damage from UV exposure, harsh weather conditions, and varying temperatures; the PVF finish was selected for its high performance and durability. It's dirt-shedding properties ensure dust and dirt slide off, so the roof will look clean for decades.
PULLMAN HOTEL MONTPARNASSE
Drawing from some older PVF success story files, the Pullman Hotel Montparnasse (formely a Sheraton) in central Paris, built in 1974, has an 18,000-square-meter facade featuring steel cladding, laminated with white PVF film. Almost 50 years later, the metal exterior—with its vertical, angular lines—appears like new without any chalking, or corrosion whatsoever. The hotel remains a Parisian landmark with its iconic, extremely long-lasting exterior appearance.
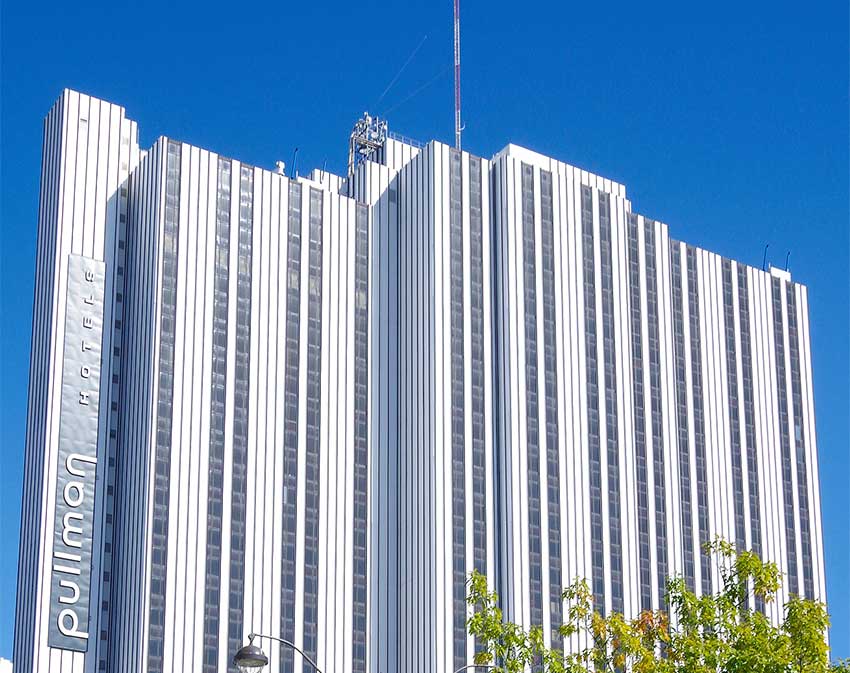
Photo courtesy of DuPont
The Pullman Hotel Montparnasse (formerly a Sheraton hotel) in central Paris was built in 1974. Almost 50 years later, the steel-cladded facade laminated with white PVF film looks like new, with no yellowing, chalking, or corrosion.
YOKOHAMA, JAPAN
Finished with a PVF film in 1983, is a commercial building in the coastal city of Yokohama, Japan. After 39 years of exposure to Tokyo Bay, the building appears untouched by the elements, dirt, and corrosion.When compared to a standard PVF film color chart showcasing fresh film samples, the exterior cladding of the tower displays no discernable difference in color after close to four decades of outside exposure.
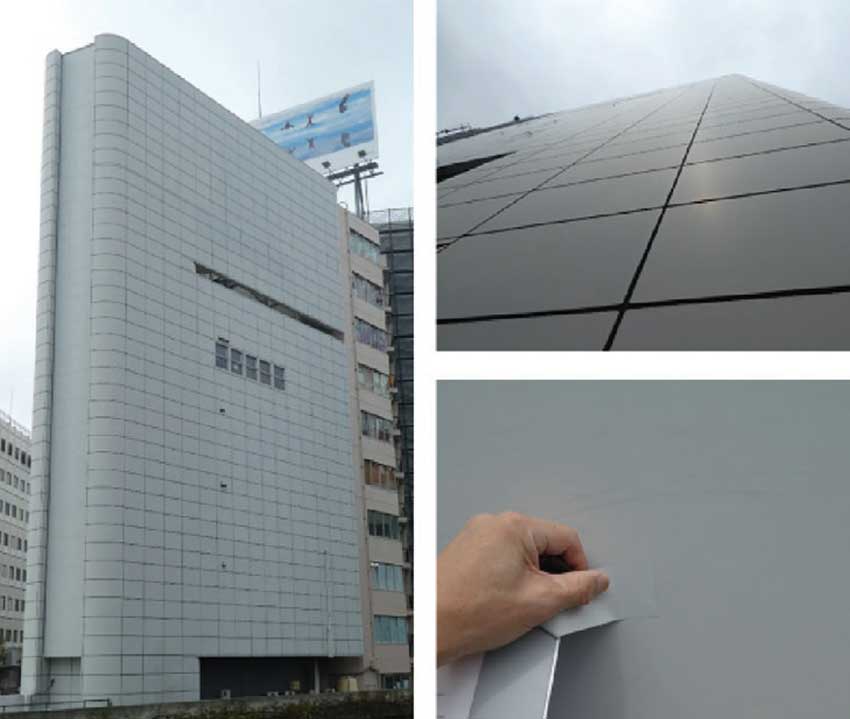
Photo courtesy of DuPont
After close to four decades of exposure to Tokyo Bay, this commercial building in the coastal city of Yokohama, Japan, appears untouched by the elements, dirt, and corrosion.
WEMBLEY STADIUM
In an application applied to windows versus metal, PVF film is lending the same level of protection and aesthetics more more than 15 years to 50,000 square feet of roof lights with a UV-blocking PVF film at London’s Wembley Stadium. Hosting England national football team home games and events such as the FA Cup Final, the film shields the roof from elements and provides chemical and pollution protection. The PVF-protected roof also brings in 70% daylight in a soft, diffused natural light. The roof lights cover and brighten a significant area of the stadium directly beneath its iconic arch. As demonstrated in this case study, PVF film can be made in a vast range of colors as well as varying levels of UV-blocking transparency, to achieve any desired look without sacrificing performance.
COMPARING ALTERNATIVES
As noted, coil coatings on the market today are available in a number of technologies, all offering a certain level of protection for metal exteriors. These include PVDF, FEVE, SMP, and polyester, all applied as liquid or powder via coil coating lines to steel or aluminum.
However, when dealing with coastal and demanding environments, these options don’t always provide adequate protection against corrosive elements.
PVF film distinguishes itself as much more robust, durable protection in a number of ways. The first reason being the inherent properties of the PVF polymer, the base material of the film. PVF has many beneficial properties, two of which are it's unparalleled resistance to chemical corrosion and it's excellent flexibility.
PVF film is made with a biaxially-oriented process, which means the film is stretched in two directions during its manufacture to optimize flexibility and check for quality. With this approach, if there are any holes or weaknesses in the film, this will be revealed. Through this stretching process, this makes the film stronger and tougher, ensuring it exhibits optimal mechanical properties in use.
When adhered to metal and fabricated, the film stretches and retains shape, ensuring a consistent level of protection on all areas. Conversely, with current coil coatings, during the coil coating process, as the solvent dries off, gas bubbles often form and pop under the paint surface, causing tiny pinholes. Over time, corrosive elements like saltwater can penetrate these weak areas in the coating and damage the metal beneath.
When applying these coatings to a metal surface, they require a primer, a top coat, and sometimes a clear third coat to achieve a desired level of metal protection. Each layer of additional materials requires time and heat for the solvent to dry off.
PVF film comes with adhesive applied to one side, which is directly applied to the metal coil on a coil coating line and baked through the oven. It is securely bonded to metal with these flexible adhesives, specially chosen to ensure an extremely long-lasting lamination.
Applied in an automated, continuous fashion, the film permanently becomes part of the metal substrate, allowing the film’s protective surface to expand and contract with the underlying substrate during temperature fluctuations and fabrication.
Even after extensive aging, PVF film shows no cracking, peeling, or chalking, ensuring a low- maintenance, durable structure with superior resistance to the wind, water, sunlight, hail, acid rain, chemical exposure, and pollution.
PVDF coatings are commonly used for exteriors in more demanding environments. However, PVDF often cracks when bent or aged. On the contrary, the elongation properties of PVF film allows for more flexible designs. As noted, PVF film can achieve 0T bend regardless of the metal or substrate it is applied to. The film naturally exhibits excellent formability and won’t crack on bent edges, either during fabrication or over the metal’s lifetime.
With PVDF coil coatings, they typically cannot achieve 0T and sometimes crack at lesser bends of 1,2T. When these coatings are bent into panel shapes, they risk cracking, exposing the metal to corrosion over time. Even when paint formulations are able to achieve greater flexibility, they typically do so at the expense of other attributes such as resistance to chemical corrosion.
PVF also exhibits chemical resistance superior to any coil coating currently used, thanks to the film structure and PVF polymer properties. Through decades of real-world applications, PVF remains looking brand new in applications by the coast or inside chemical plants. While some coatings offer good chemical resistance, they all exhibit blistering and cracking significantly faster than PVF in both lab tests and real applications. Highly corrosive environments require periodic recoating or panel replacement as the paint blisters and starts to leave the metal exposed.
For example, a chemical plant’s synthesis workshop replaced some of its interior steel roof with PVF-film-laminated steel sheets in 2016. These roofs have not been replaced since and still look as good as new. High temperature acid glass produced in the workshop causes severe corrosion, and previously had required regular replacement of the workshop’s painted steel roof panels, often every two to three years or less. This level of required maintenance not only impacts the plant’s regular operations, but it can pose a production safety hazard as well as adding additional material and labor cost to the plant’s budget.
Another benefit of PVF film is that the material is dirt-shedding and resists stains and discoloration, ensuring a lasting new look. Due to minimal color change over time, if a replacement is required, only the damaged panel needs to be replaced, as the aged film will match the new film due to excellent color retention, thus reducing labor and material cost.
Offering an additional tool for PVF applications, PVF repair tape can be used to protect exposed edges and repair scratches that occur during installation. This repair is undetectable with exact color matching and minimal thickness, yet provides excellent protection from corrosion.
In contrast, with current coil coatings, when a coating becomes dirty or damaged, or a panel needs replacement, the entire roof typically needs to be repainted to ensure color matching and consistency. Furthermore, many coastal building coating warranties require a fresh water rinse to remove salt buildup, whereas PVF does not require a rinse and typically needs less maintenance under warranty.
Offering an additional tool for PVF applications, PVF repair tape can be used to protect exposed edges and repair scratches that occur during installation. This repair is undetectable with exact color matching and minimal thickness, yet provides excellent protection from corrosion.
CHEMICAL PROPERTIES
To better understand what makes PVF extremely inert, its polymeric material chemically acts like polyethylene, but with one hydrogen atom substituted with a fluorine atom at each repeat unit. The high electronegativity of the fluorine atom, and its tendency to draw electrons and tighten the surrounding atomic bonds, lend remarkable strength to the carbon-fluorine bond.
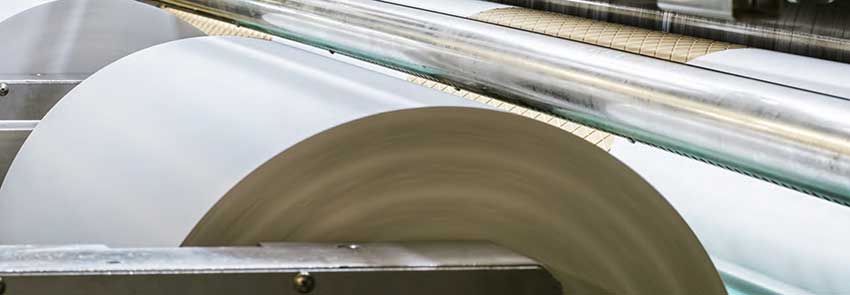
Photo courtesy of DuPont
PVF is laminated to metal by applying it with an adhesive directly to the metal coil on a coil coating line.
Among the different variations of fluoropolymer, PVF offers a unique property in that the benefits gained by the incorporation of fluorine do not come at the expense of mechanical performance. Further, the semi-crystalline nature of PVF films enables them to deliver a favorable combination of strength and ductility.
When laminated to a substrate such as metal, it is ideal for applications requiring either hot or cold forming post-lamination, such as roofing, since a PVF-based film can sustain strain and aggressive bends without cracking or compromising integrity on bent areas. For other fluorinated materials like PVDF to reach the same level of formability, additives are required to reduce crystallinity. Unfortunately, this then compromises the level of chemical resistance and outdoor performance levels.
PVF film does not rely on co-resins or plasticizers to enable a high degree of flexibility. It is a pure fluoropolymer with pigments to add color. The simplicty of this forumlation creates superior resistance to any chemicals transmitting through the polymer matrix, no catalysts for embrittlement or discoloration, and no ability to host mold or mildew.
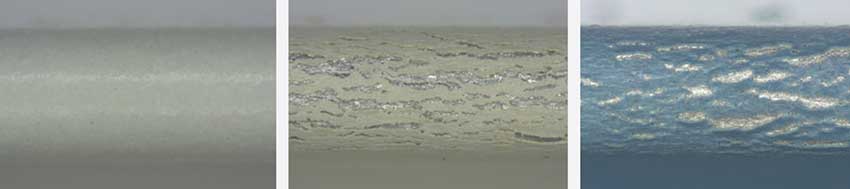
Photo courtesy of DuPont
PVF film over bent metal as seen under a microscope shows no cracking (left side), as compared to PVDF coating on bent metal in the middle and on the right, showing cracking and exposed metal.
PVF film does not rely on co-resins or plasticizers to enable a high degree of flexibility. It is a pure fluoropolymer with pigments to add color. The simplicty of this forumlation creates superior resistance to any chemicals transmitting through the polymer matrix, no catalysts for embrittlement or discoloration, and no ability to host mold or mildew.
Commonly based on polymethyl methacrylate-based (PMMA), an acrylic is added to PVDF coil coating paints, and this alters the crystallinity of the polymer. The crystalline PVDF domains decrease in concentration, enabling more plastic deformation before fracture. But, if too much acrylic is added, the formability of the materials is decreased due to the fundamentally brittle nature of PMMA. With PVF film, no acrylic is added, as it is not needed to achieve optimized performance.
As a key point regarding its composition and sustainability, PVF is excluded from all global definitions of PFAS and not included in any current regulatory restrictions. It contains no fully-flourinated carbons and is not included in the ECHA PFAS restriction list.
PUTTING PVF TO THE TEST
PUPVF film is highly inert, making it suitable for extremely high chemical resistance and compatibility with acids, bases, oxidizers, and a variety of solvents, including polar, non-polar, aromatic, aliphatic, hydrocarbon and chlorinated solvents, and other harsh chemicals. Even under extreme conditions with high concentrations, extended exposure times, and high temperatures, the PVF film retains all or most of its original properties and appearance.
In a series of accelerated and long-term lab tests, PVF was immersed for various periods of times between 77°F and boiling temperatures in acids, bases, solvents, and miscellaneous chemicals. Afterwards, there was no perceptible change in either appearance or mechanical properties to the film.

Image courtesy of DuPont
Over the course of 15 years, pigmented PVF films in south Florida were tested and displayed under five units of color change, essentially invisible to the naked eye.
In other lab tests, PVF proved itself to be impermeable to greases and oils. This makes the films easy to clean because the vast majority of staining agents remain on the surface of the films as opposed to seeping into the material.
Chemical resistance testing in the lab includes spot and submersion testing of various arch chemicals, including hydrogen chloride, sodium hydroxide, nitric acid, and more. Commercial PVDF, FEVE, and SMP paints all failed significantly faster than PVF film. Testing for PVF film ended at 2000 to 3000 hours without failure across all chemical tests. The tested PVDF paints failed long before the film testing ended, some in as little as under 100 hours and none more than 1,500 hours. Failing is defined as cracking, blistering, and an otherwise damaged coating film layer, displaying a ruined appearance and exposing the metal beneath to corrosive elements.
Over the course of 20+ years, pigmented PVF films in south Florida were tested and generally displayed well under five units of color change, essentially invisible to the naked eye.
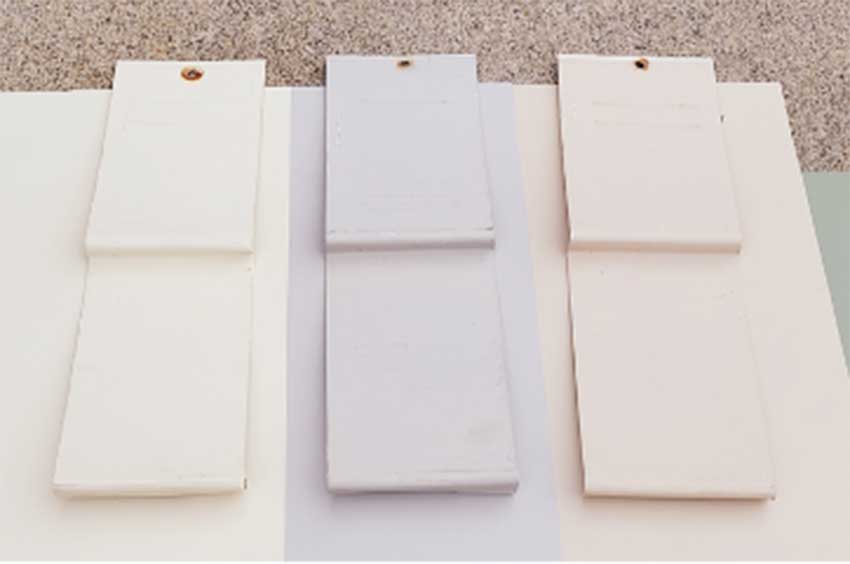
Photo courtesy of DuPont
This photo shows 20-year-old south Florida-tested metal with PVF-film-laminated samples installed over fresh film of the same color. No color change or cracking is visible, even under a microscope
Regarding the film surface, there is no cracking or chalking visible from a minimum distance of 6.5 feet with un-aided eye. The black glove test on 20-year aged film shows no chalking on the glove wipe. Further proving the film’s integrity, laminates with PVF film installed over 20 years ago in south Florida showed no surface cracking even under a microscope.
While the south Florida exposed PVF film test on metal surfaces exhibits low color change of ΔE < 4.5. In comparison, a polyester coating posts ΔE of more than 13, jumping up to a color change value of 12 in less than a year. A PVDF coating gradually changes, reaching more than four after 10 years, with a color change of at least seven units by 15 years.
Warranties range depending on application, but PVF offers upwards of 30 and 40 years for chalk and color for roofing and siding, and up to 50 years for the film's integrity.
When tested for corrosion resistance per ASTM B117, PVF demonstrates greater than 3,000 hours on aluminum whereas PVDF reaches 1,500 hours. For humidity resistance, per ASTM D2247, PVDF performs for 4,000 hours while PVF exceeds resistance of greater 4,000 hours.
Per ASTM G21 Standard Practice for Determining Resistance of Synthetic Polymeric Materials to Fungi, PVF is mold and mildew resistant. This means it does not support organic growth, which metal is very vulnerable to in moist and humid environments where mildew is common.
EXCELLENT STAIN RESISTANCE
Demonstrating PVF’s extremely high level of stain resistance, extensive testing was performed on all sorts of potentially stain-causing agents. Testing was done on a Type II vinyl wallcovering laminated with PVF film and stains were allowed to set for 24 hours. All of the following agents were successful removed with a dry cloth cleaning: acid solutions, acetone, butanone, ethylalcohol, gasoline, glycol, and tolene. The following agents were successful removed with a wet cloth cleaning: coffee, grape juice, mustard sauce, red wine, tea stains, Worcestershire sauce, chocolate syrup, brake fluid, iodine, and sodium hydroxide.
In addition, these substances were removed with detergent: ketchup, black crayons, brown shoe polish, lipstick, white board marker, oily pen, asphalt, and mercurochrome. With solvent, ballpoint pen and spray paint were successfully removed.
Of note, the test used a standardized cleaning methodology. PVF’s high level of performance proves its extremely high level of cleanability and stain resistance. In fact, one of PVF’s first applications was for outdoor graphic signage/billboards to protect the colors from fading and protect against yellowing, dirt, and graffiti.
When subjected to mold resistance performance testing, PVF film registered as highly resistant to mold growth. For the ISO 846 Part C: Resistance to Bacteria for a Type II Wallcovering, the film exhibited no growth or nutritive components on or around all samples. In addition to added value in the aforementioned humid environments, this is also highly valuable for highly sterile interior environments, like hospitals or food service.
PVF also scores high marks in the category of indoor air quality. When used in a wallcovering application, the specification of the film can contribute towards GREENGUARD Gold and LEED certifications through reducing Volatile Organic Compounds (VOCs).
And similar to its use on exteriors, PVF film offers a very high level of durability and protection for interiors, significantly reducing replacement and material waste. This significantly reduces the material’s footprint over the life of a building.
One other important performance category is fire and smoke resistance. Based on the Warrington Fire rating, which is a global standard, PVF-protected wallcoverings have a low flame spread and smoke development ratings, meeting EN 13501-1:2018 as part of EN 15102:201.
In fact, due to its very low smoke production and flame spread, PVF film has been specified into the inside of aircrafts since the 1960s. In addition, it’s commonly used for interiors on trains, in healthcare facilities, hotels, and more.
With decades of demonstrated outdoor performance in harsh environments, PVF film has stood the test of time. Superior flexibility and durability ensure stability of the finish, even during severe environmental stressors, from construction-related damage and wear during installation, and despite unpredictable weather.
Metal buildings provide some of the best possible longevity on the market, and the greatest protection against wind uplift, fire, and other challenges. Using PVF film ensures these strong structures retain their aesthetic and increase their endurance and performance.
PVF COATING
Another application of PVF technology is in the form of a coating. Manufactured based on the same base polymer as PVF, the polymer imparts the coating with very similar attributes as the film, including a high level of flexibility, resistance to cracking at bends, and chemical resistance. PVF coating lab testing proves the coating’s ability to resist corroding and blistering when exposed to harsh acids significantly longer than alternative coatings.
PVF coating is a relatively new application in building and construction, but early field testing, shows very low color change and excellent resistance to fading and chalking, and accelerated testing aligns with PVF film performance.
PVF coatings have a long history in the automotive industry, providing protection to brake tubing under the vehicle body, which is exposed to corrosive road salts, impact, and bending during installation. It is now being used in metal building applications, and for building exteriors and interiors in demanding environments. PVF coating is an excellent choice for end users who require a similar high level of performance to PVF film, but are more suited to a coating application.
In a more recent, high-profile application, PVF coating was used to update China’s third largest stadium - Shanghai Stadium. Playing host to many significant events including the football and soccer games of the 2008 Summer Olympics, the stadium was originally built in 1997. In 2021, prior to hosting the FIFA World Cup, PVF coating was chosen to replace the existing material on the aluminum siding and cladding on account of its durability and cleanability. The coating applied to the aluminum honeycomb panels is resistant to fading from UV rays and will preserve the stadium’s aesthetics for many years.
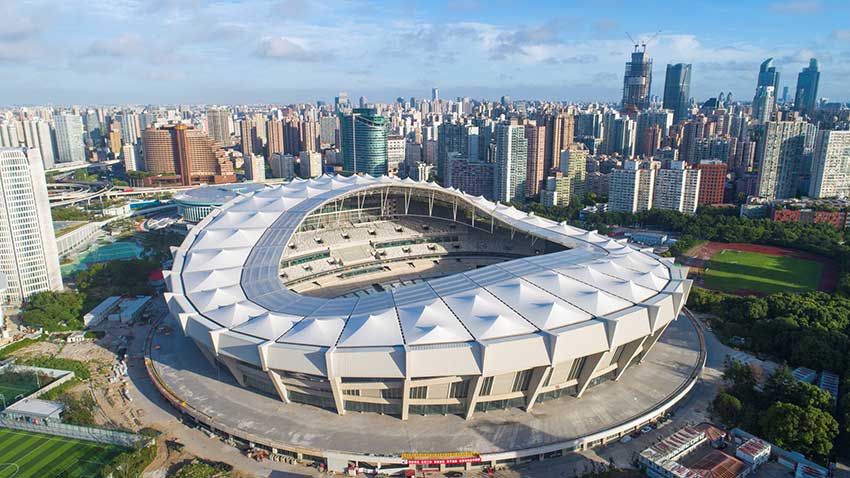
Photo courtesy of DuPont
The aluminum siding and cladding for China’s Shanghai Stadium was replaced with a PVF coating last year.
For another Shanghai project, World Laureates Forum in Lin’gang, a PVF coating was used on the aluminum in the cornice and entrance of the building. Every year scientists from around the world, who have won Nobel Peace or Wolf Prizes, are invited to a conference located in this building. PVF was an important choice for this application due to the site’s proximity to the sea. The technology protects surfaces from corrosion due to sea salt spray by creating an extremely chemically resistant and durable barrier over the metal. The dirt-shedding and UV-resistant properties lent by the PVF coating mean that the building will not fade over decades in the sun, and will look clean and new over its lifetime, despite the demanding environment.
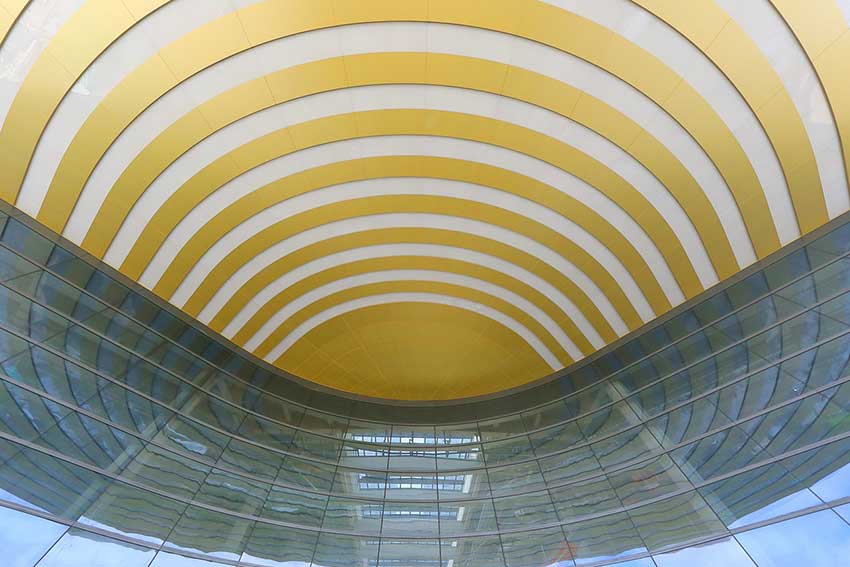
Photo courtesy of DuPont
Even though the Beijing Tennis Club constructed three different white air-inflated dome structures with PVF film in different years starting in 2006, each fabric has retained its original appearance. In comparison, there is a fourth tension architectural fabric structure with a PVDF top finish on the site that discolored significantly from its 2003 installation.
PROTECTING INTERIORS
As noted, another popular PVF film application is interiors, particularly higher use environments with greater cleanability and sanitary requirements like healthcare settings.
As a testimony to the long-term protection and durability the technology lends to these applications, Delaware’s Omega Medical Center installed PVF film-protected wall coverings in all high-use areas across the 14,500-square-foot facility over 30 years ago. While the painted sections of the medical occupational health and on-the-job Workers’ Compensation injury center have had to be repainted multiple times over the past three decades, the wallcoverings are as durable, easy to clean, and attractive as they were when the Center first opened back in 1985. While interior design is rarely required to last that long, choosing PVF film enables the designer and building owner to renovate and replace when they want to, not when they have to. This leads to greater design and budgetary freedom, as well as reduced material waste.
More recently, PVF film was selected as a protective material for the renovation of the largest women and children’s medical center in China. Completed this summer, this center in Guangzhou Zeng-cheng was chosen for its durability and cleanability, and applied in three different ways─for interior metal panels, wallcoverings, and wardrobe finishes.
Showcasing the wide range of substrates that the PVF film can be applied to, the material was thermo-formed to the doors of closets, cabinets, and wardrobes in patient rooms, and vacuum sealed to .35-meter-thick PVC, as well as composite wood panels. The film was laminated to a wallcovering patterned with wood, textured grass cloth, and other prints to create a colorful, yet healing atmosphere for this modern medical facility.
CONCLUSION
Rigorous testing and decades of real-world applications have established PVF as a highly robust, protective film well suited for metal exteriors in harsh and corrosive environments. The film is also popular as an architectural fabric, for interiors, and more. Its resistance to cracking, fading, and staining and its high level of color fastness and retention of the surface aesthetic make it ideal for metal siding, roofing, and facades; as a fabric membrane; and for wall coverings and other interior applications.
Compared to other coating technologies, which do not offer nearly the same level of protection on a number of accounts, PVF is ideal for these challenging environments, backed by a long warranty with no geographic limitations. Whether exposed to salt water, pollution, or chemicals, or for settings such as healthcare applications requiring a high level of durability and hygiene, PVF film is the clear choice.