Finding new and innovative ways to protect the health and well-being of occupants during renovations in commercial construction is a persistent concern for architects, builders, and building owners. Today innovations and new products in roofing materials help facilitate a more toxin-free jobsite for occupants, neighbors, and contractors, helping as well with the health and sustainability of the planet.
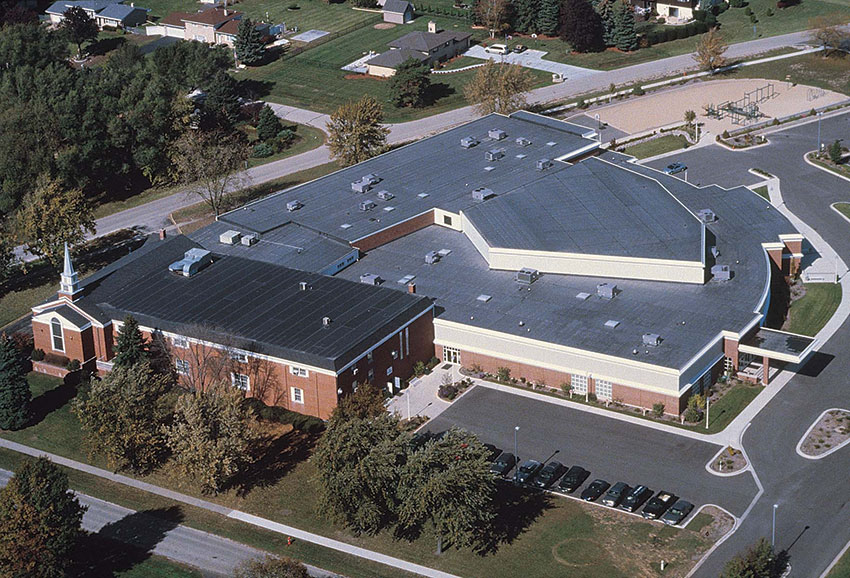
Photo courtesy of Versico Roofing Systems
Single-ply roofing remains the most popular choice for commercial buildings, however understanding the impact of VOCs and the health of the community should be of concern when specifying projects.
Of main concern in roofing materials are Volatile Organic Compounds (VOCs), a group of airborne chemicals often found in adhesives, sealants, and coatings. VOCs are of concern as both indoor air pollutants and outdoor air pollutants. However, the emphasis for problematic VOCs is particular to outdoor environments as opposed to indoors.
Indoor VOCs form in fumes from roof sealants and adhesives that can adversely impact the health of people who have been exposed. Prolonged exposure to VOCs can lead to respiratory problems, aggravate existing conditions such as asthma, and cause long-term lung damage.
Outside, VOCs contribute to localized air pollution forming ground-level ozone when they react with nitrogen. For this reason, the U.S. Environmental Protection Agency (EPA) regulates VOCs outdoors mainly because of their potential to lead to photochemical smog under certain conditions.
This article will provide an overview of common VOCs found in roofing materials and describe how these chemicals can negatively impact occupants, neighbors, and workers. It will also discuss how VOCs outside are differentiated by the EPA, how they are measured, and the negative impacts they can have on local air pollution and the environment. To help provide direction for architects and builders, the article will discuss low and no-VOC options in roofing materials and provide direction on jobsite management and scheduling to help reduce the risk of VOC exposure. Finally, the article will provide alternatives to traditional single-ply roofing systems that can help promote sustainability, such as bio-based roofing materials that increase the health and welfare of occupants and installers and also qualify for green building certification programs.
THE BASICS OF IAQ
Health, safety, indoor air quality, sustainability–all these terms have been drawn into the spotlight for builders over the past decade. Commercial building owners looking to improve productivity and employee morale are asking to incorporate biophilia and natural daylighting into office designs. Developers trying to attract more environmentally savvy clients are including onsite renewable energy options and high-performance homes, and legitimate concerns about climate change and the impact the built environment is having on the Earth have also contributed to the demand for a change in the way we design, build, and maintain structures.
While many of the elements that define a healthy and sustainable project like energy efficiency, durability, storm resiliency, and basic ventilation have been codified, other factors that impact the health and well-being of occupants, and the planet, are yet to be regulated. Embodied and operational carbon, for example, has yet to be clearly quantified but is likely to be regulated at some level in the not-so-distant future. To develop a positive reputation builders must keep abreast of the demands of the consumer, the interests of the market, and the requirements of basic building code.
A persistent driver in healthier homes and a sustainable planet is air quality, both indoor and out of doors. Many consumers are well-informed on the dangers of poorly ventilated homes, offices, and schools. From this group of educated consumers, most are familiar with the oft-quoted message from the U.S. Environmental Protection Agency (EPA) that studies of human exposure to air pollutants indicate that indoor levels of pollutants may be two to five times–and occasionally more than 100 times–higher than outdoor levels, and that the main concern is that most people spend about 90 percent of their time indoors.1
The laundry list of indoor toxins can be lengthy and usually includes pet dander, mold, dust, pollen and other allergens, carbon monoxide, tobacco smoke, radon, and pesticides. The potential health risks of poor IAQ can be minor, such as simple sniffles or mild headaches. However, the EPA warns the impact could be more threatening in vulnerable populations, for instance, occupants with existing health issues like asthma, or the young and the old with the potential for severe respiratory diseases and long-term disability.
When addressing issues related to poor IAQ, a common culprit–and one that consumers are increasingly aware of–is volatile organic compounds, or VOCs.
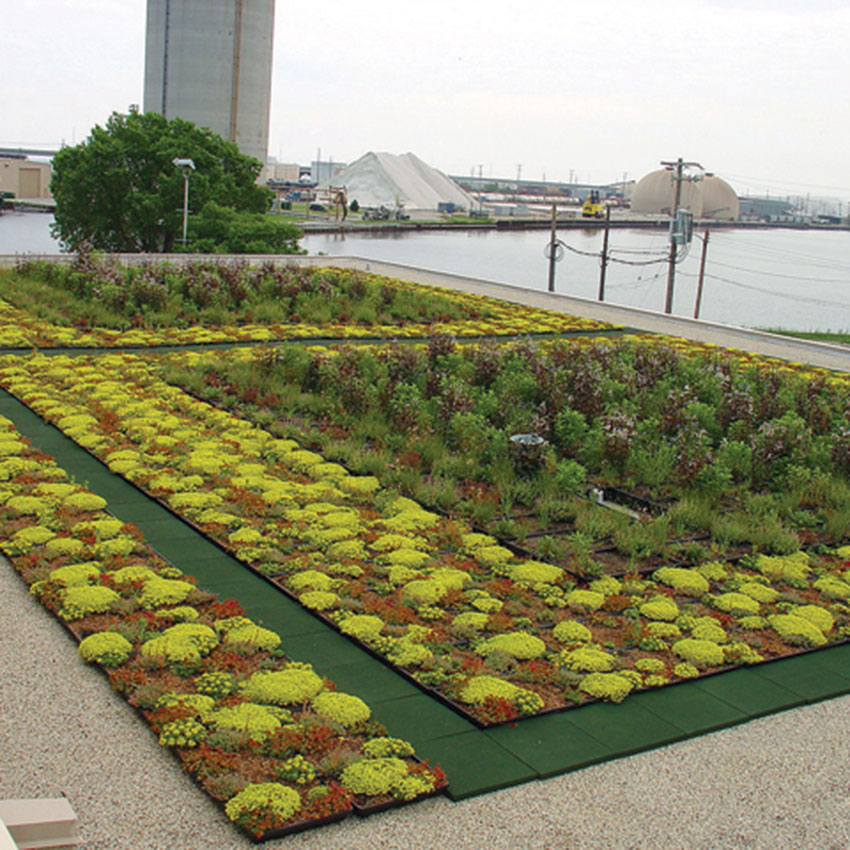
Photo courtesy of Versico Roofing Systems
Improving the sustainability aspects of a project can include everything from enhanced protection from the elements to rooftop gardens, however, the sealants and adhesives used should also be considered.
VOCS–THE BIG PICTURE
Without getting too pedantic, let’s break down the definition of VOCs, just to get a solid foundation on how they are defined, and why architects, builders, building owners, and occupants need to be aware of them.
The generally accepted scientific definition of what constitutes a material as a VOC is a chemical compound whose composition makes it possible for it to evaporate under normal indoor atmospheric conditions of temperature and pressure. When a material reaches the boiling point, it turns from liquid to gas, and all the molecules at the surface are released as vapor into the air. Water, for instance, has a boiling point at sea level of 212°F (100°C). The boiling point goes down as we climb in elevation due to less atmospheric pressure on the surface of the water. At 3,000 feet above sea level, water boils around 206°F; at 10,000 feet above sea level the boiling point is 194°F.
Water is inert and other than increasing the humidity in the room not likely to cause major harm to occupants as it evaporates. Formaldehyde, however, with a boiling point of -2.2°F (-19°C) is a known VOC and is often found in manufactured wood products like flooring and furniture, and is found in tobacco smoke. Exposure to formaldehyde can irritate the skin, throat, lungs, and eyes while repeated exposure can possibly lead to cancer. With a boiling point so low, formaldehyde will instantly begin to vaporize when exposed to air at room temperature. But boiling point is only part of the equation, the other factor that impacts the release of VOCs into the air is vapor pressure.
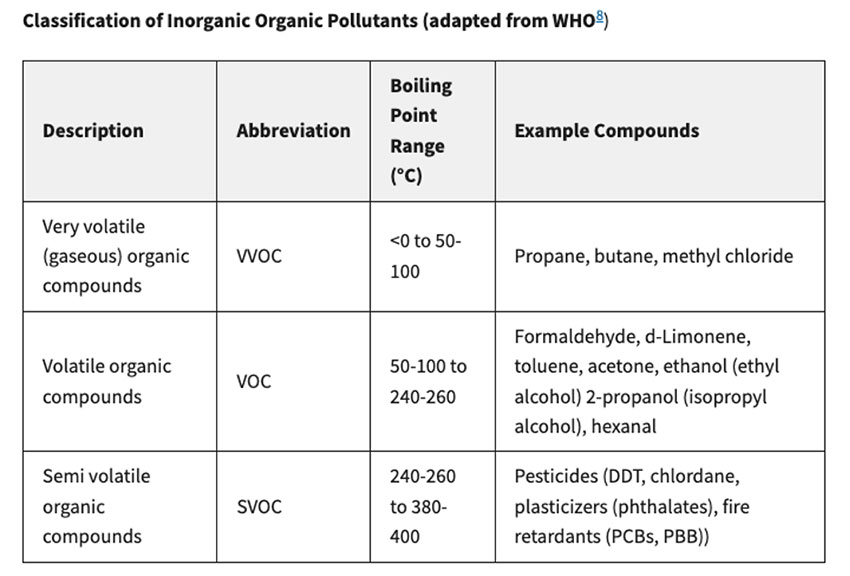
Image courtesy of the U.S. EPA
This chart shows how the World Health Organization defines VOCs based simply on boiling points.
Chemical compounds are always in a state of evaporating (vaporizing) and condensing, even below the boiling point.
This is true for both solids and liquids. Solids that are comprised of additives that were liquid chemicals when manufactured off-gas those chemicals. To understand how quickly and with what velocity these materials evaporate, we measure the vapor pressure.
Vapor pressure is a measure of the speed at which a substance vaporizes. Vapor pressure can be measured and quantified in millimeters of mercury (mmHb) as the pressure exerted by the vapor molecules above the surface of a liquid when the liquid and vapor are in equilibrium, meaning when they are evaporating and condensing at the same rate, within a closed container. This is the scientific definition, but in simple terms, vapor pressure measures how fast, or the force at which molecules will escape a chemical compound. The higher the vapor pressure, the faster the vapor will disperse into the surrounding area.
Using water as an example, we know when water boils it turns from liquid to vapor, but along the path to hitting the boiling point, the vapor pressure of water changes. The hotter the water, the faster the molecules escape. Imagine a tea kettle slowly beginning to whistle even before the water is at a full boil. At 32°F (0°C) the vapor pressure of water is 4.58 mmHg. At 77°F (25°C)2 vapor pressure is 23.76 mmHg. At the boiling point, 212°F (100°C) water’s vapor pressure is 760 mmHg.
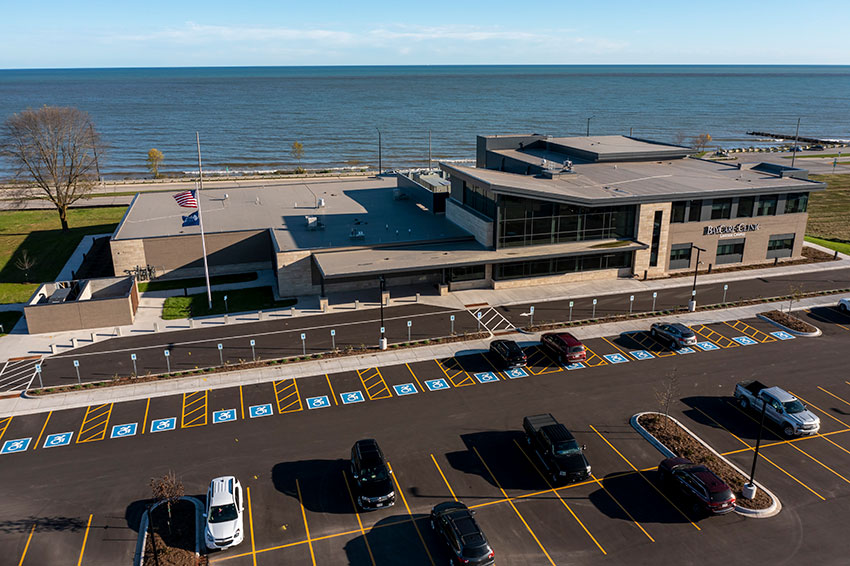
Photo courtesy of Versico Roofing Systems
Concerns of localized ground ozone and smog are the primary concerns for limiting VOCs in roofing materials. This is especially true in when the project is a school or medical facility, as featured in this image.
Why is this important? It all comes down to the “V” in VOCs. Volatile organic compounds, by definition, generally have low boiling points and high vapor pressure values. This means they are chemically prone to vaporize and disperse their molecules with high pressure in “normal” conditions, including the built environment. According to the Hazardous Substances Data Bank (HSDB), formaldehyde at 100 percent purity has a vapor pressure of 3,890 mmHg at 77°F (25°C)2. Again, compare that to the 23.27 mmHg of water at the same temperature and we can see why these VOCs are far more invasive.
Fortunately, most building products, paints, and finishes that incorporate formaldehyde in the manufacturing process use a diluted mix of the chemical, however, that simply reduces the overall volume of the VOC, not the ability to rapidly vaporize nor the vapor pressure.
Because boiling points and vapor pressure levels vary from compound to compound, VOCs are further defined by how readily they will emit vapors. The higher the volatility (lower boiling point), the more likely the compound will be emitted from a product or surface into the air.
This predisposition of a chemical to rapidly vaporize is what makes them volatile, and in fact often the low boiling point can be the demarcation line for identifying VOCs.
The World Health Organization (WHO) categorizes indoor organic pollutants as:
- Very volatile organic compounds (VVOCs)
- Volatile organic compounds (VOCs)
- Semi-volatile organic compounds (SVOCs)
From a health and safety standpoint, VVOCs are the most dangerous as they are toxic at very low levels of concentration. VVOCs are so volatile that they are difficult to measure and are found almost entirely as gasses in the air rather than in materials or on surfaces. However, of all three classifications, VOCs are far more common and can be as harmful as VVOCs. Most VOCs will be in solids or liquids that contain them, or on surfaces including dust, furnishings, and building materials. SVOCS, the least volatile compounds found in air, constitute a far smaller fraction of the total present indoors.3
Moving on to the “OC” in the VOC, an organic compound is any of a large class of chemical compounds whose molecules contain carbon. There are some carbonate compounds which contain carbon but are considered inorganic, but for the purposes of this article, the definition above will suffice.
VOCS INSIDE
The introduction of VOCs into the built environment is normally due to products that consumers bring into their buildings in the form of cleaners, pesticides, and solvents. However, during construction, builders can introduce many VOCs into a building with the products and materials specified for the project. This exposure can at once create risks for tradespeople and workers on the jobsite, and depending on how persistent the VOCs, eventually expose occupants.
Almost everything in the built environment including paints, caulks, sealants, adhesives, carpeting, flooring, insulation, cleaning products, and fuel contain VOCs unless they are specifically designed and manufactured without them. Here is a list of some of the most common VOCs found on the construction site.
Know Your VOCs
Formaldehyde (CH2O) found in glues, cast plastics, varnishes, insulating materials, pressed wood products such as plywood, particle board, laminate flooring, and varnishes.
Vinyl chloride (C2H3Cl) is used in the making of plastics (PVC), floor coverings, and consumer goods. It is also known as chloroethene, chloroethylene, or ethylene monochloride.
Toluene (C7H8) is an aromatic hydrocarbon and a colorless liquid that is water-insoluble with a smell associated with paint thinners, and it is predominantly used in some types of paint thinner, permanent markers, and certain types of glue. Toluene has the potential to cause severe neurological harm.
Isopropyl alcohol is a colorless liquid, flammable chemical compound, with the chemical formula CH3CHOHCH3 and having a strong odor. It is used in the making of cosmetics, pharmaceuticals, perfumes, dye solutions, antifreeze, soaps, cleaners, and disinfecting agents.
Carbon disulfide or carbon bisulfide (CS2) is a highly volatile compound and is present as a compound in varnishes, solvents, and insecticides.4
Building materials that contain VOCs can continue to off-gas after the installation is complete. The VOCs in paint, for instance, can continue to disperse for up to 72 hours, long after the coating is dry and our nose no longer detects an odor. Floors and pressboards can keep emitting low levels of VOC for years. The danger of VOCs to occupants comes from a combination of total volume of VOCs, type of VOCs, and exposure. This is why choosing low or no-VOC products for the interior is critical, especially for products such as carpet and flooring.
VOCs inside the house are one issue, while VOCs on the outside that are introduced during construction or remodeling present an almost completely different environmental challenge for the builder. As we will see, this is especially true when it comes to specifying roofing materials.
VOCS OUTSIDE
The term “VOC” is a universal label applied to this class of compounds, but the reasons these compounds are of concern are different outdoors. Whereas the main concern indoors is the risk to humans from directly inhaling, drinking, or absorbing the toxins in the VOC, outside VOCs pose less of a threat in this way. Natural ventilation helps disperse the chemicals quickly, diluting the concentration of the toxins so that under normal conditions they don’t pose a threat to human health.
The main concern with VOCs outdoors is how they serve as a main ingredient in creating the problem of photochemical smog.
On normal sunny days, the air can be clean and healthy, but when VOCs are introduced, a photochemical reaction starts. These VOCs can be from industrial facilities, electric utilities, motor vehicle exhaust, gasoline vapors, and, like the VOCs indoors, chemical solvents and adhesives. When these VOCs are mixed with oxides of nitrogen (an abundant and naturally occurring chemical in the air) or carbon monoxide (a byproduct of combustion engines plus the addition of heat from sunshine), ozone is created.
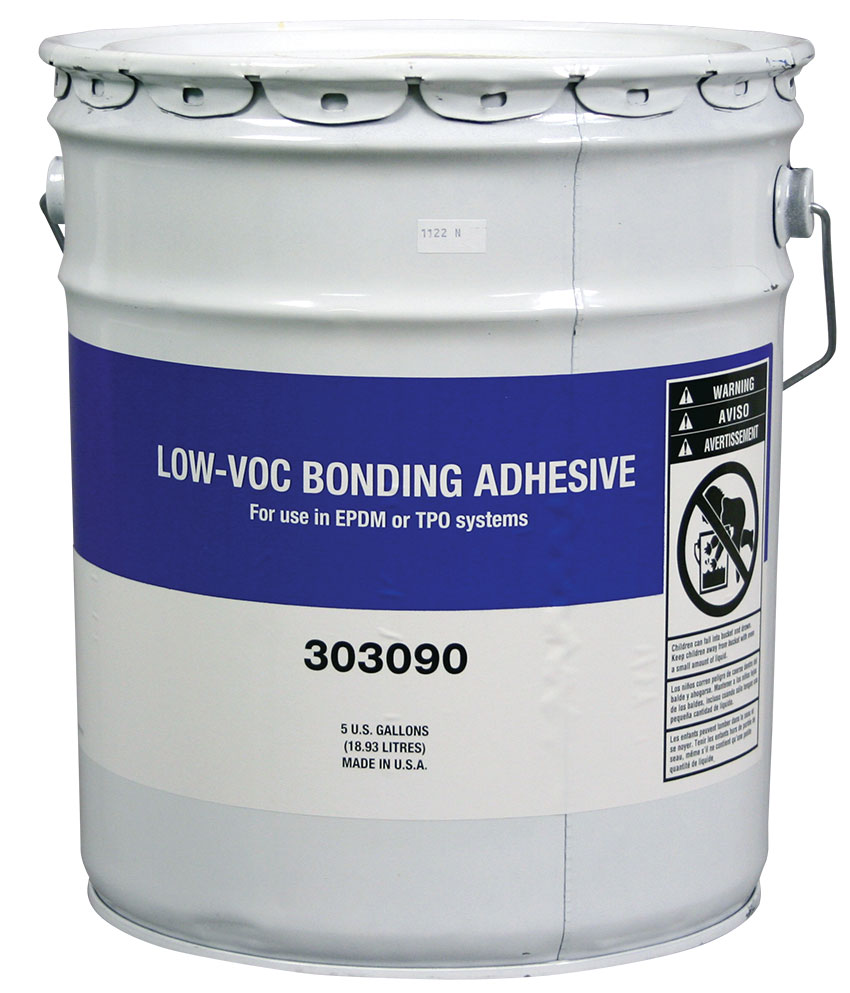
Photo courtesy of Versico Roofing Systems
Specifying low-VOC adhesives can help contribute to both a healthier environment and sustainability goals on the project.
There are two kinds of ozone. One called stratospheric ozone is beneficial for our planet and occurs naturally in the upper atmosphere. This “good” ozone forms a protective layer that shields us from the sun's harmful ultraviolet rays. The other type of ozone is ground-level or tropospheric ozone. This is considered “bad” ozone and proves the main ingredient in smog. Smog can be created by a mixture of other chemicals, but for this article, we can consider the terms photochemical smog and ozone to be interchangeable.
Ozone can create all sorts of health issues for humans, vegetation, and the environment. For humans─depending on the level of exposure─ozone can cause coughing and a sore or scratchy throat, make it more difficult to breathe, inflame and damage airways, and leave lungs more susceptible to infection. For people with existing conditions such as asthma, emphysema, and chronic bronchitis, the impact of ozone can be sudden, severe, and persistent. However, some of these effects have been found even in healthy people without these conditions.
For the environment, elevated exposures to ozone can affect sensitive vegetation and ecosystems, including forests, parks, wildlife refuges, and wilderness areas. Ozone can reduce photosynthesis, slow plant growth, increase plants' risk of disease, and make them more vulnerable to insects, drought, and harm from severe weather.
Also, tropospheric ozone is the third most important anthropogenic greenhouse gas after carbon dioxide and methane. It absorbs infrared radiation from the Earth's surface, reducing the amount of radiation that escapes to space.
Because of the negative impact that ozone can have on people, plants, and the planet, the EPA is heavily invested in reducing photochemical ozone, which means regulating VOCs. Roofing adhesives, sealants, and glues fall into this category of VOCs that potentially can create photochemical smog, and as we’ll see, there is frequently some confusion over exactly which chemicals are defined as VOCs, and which VOCs are regulated.
REGULATING VOCS OUTSIDE
Under the authority of the Clean Air Act (CAA), the EPA was directed to define and regulate outdoor air pollutants, including VOCs. In the 1970s the EPA started to list several chemical compounds that it deemed to be contributors to photochemical ozone. To do this, a threshold of reactivity, or volatility, was established to determine which compounds would be regulated, and those that would be exempt.
The list of VOCs on the EPAs list has grown and shrunk over the years as different chemical compounds have been evaluated, and the industry has challenged and petitioned for changes and exclusions to the list. Since 1977 there have been about 70 compounds that have been given exemptions because they have a negligible level of reactivity, meaning they fall below the threshold of presenting an actual threat to creating ozone. The intent of the exemptions was the belief that exempting such compounds creates an incentive for industry to use materials that won’t create photochemical ozone. Hence the creation of low or no-VOC labels on building materials.
The EPA originally defined the regulated organic compounds in outdoor air as “Reactive Organic Gases” (ROG). However, later changed that terminology to VOC, based on the relative nature and volatility of the compound. It is useful to note for background that while this change in terminology did clarify the focus of regulation to a more uniform and specific understanding of the compounds, using the term VOC rather than ROG has created some confusion in the industry.
The EPA has no authority to regulate household products when applied to indoor air quality, but the agency does regulate outdoor air quality. Although the same term “VOC” is used for both indoor and outdoor air quality, the term is defined differently to reflect its predominant concern in each context. Inside VOCs impact the health of the occupant, while outside VOCs contribute to the creation of ozone. The misunderstanding about this difference by some individuals and organizations, including manufacturers of building materials and products, is because the word VOC is used for both indoor and outdoor air quality purposes.5
Once the list of outdoor VOCs that contribute to photochemical ozone was established, the EPA then began monitoring levels nationwide to determine where and how to focus regulatory attention. The National Ambient Air Quality Standards (NAAQS) were defined and set limits on the concentrations of specific air pollutants in the outdoor air that are considered safe for public health and the environment. A region, usually a state, in which ground-level ozone is found to exceed the NAAQS, is said to be in nonattainment and required to develop a plan to reduce ozone levels. Individual states are required to develop State Implementation Plans (SIPs) outlining how they will achieve and maintain compliance with the standards.
For architects, builders, manufacturers, and suppliers, VOC regulation can vary depending on the jurisdiction and local codes. Because of high levels of ozone especially in areas of dense populations, heavy traffic corridors, or industry, some areas decide to go beyond NAAQS standards and enact even more stringent or specific guidelines for VOCs. In these regions, there can be regulatory groups developed that help set specific collective guides and standards for VOCs.
Regulatory Bodies Ozone:
- California Air Resources Board (CARB) is the regulatory body that oversees California’s statewide air quality initiatives and guides the regulatory activities of its 35 local air districts.
- Ozone Transport Commission (OTC) consists of 12 member states and the District of Columbia. The member states are Connecticut, Delaware, Maine, Maryland, Massachusetts, New Hampshire, New Jersey, New York, Pennsylvania, Rhode Island, Vermont, and Virginia. These states work together to develop and implement strategies to reduce ozone-forming pollutants.
- Lake Michigan Air Directors Consortium (LADCO) is another regional organization in the United States that focuses on air quality issues. Specifically, LADCO addresses air quality concerns in the states surrounding Lake Michigan.
- South Coast Air Quality Management District (SCAQMD) is a government agency responsible for air quality management in the South Coast Air Basin, which includes Los Angeles, Orange County, Riverside County, and San Bernardino County in Southern California. The VOC content limits and regulations in the SCAQMD are among the most extensive and sweeping in the country.
The key takeaway to understanding outdoor VOC regulations is that not all building materials and systems are allowable, even if the product is approved by the EPA. In California, for instance, one type of roofing adhesive may be acceptable and considered low-VOC in Sacramento, but this same material might not be allowed in Malibu. When specifying roofing types and systems, it is critical to do the extra legwork and focus on research to ensure that the system being specified will comply with all federal, state, and local VOC regulations. A good tip for structuring the process to do this is to select a manufacturing partner who understands what is and is not allowed and also understands some of the limitations of installing low-VOC, no-VOC roofing materials.
Craig Tyler, Specification Manager for Versico Roofing Systems, states “Many manufacturers of Roofing will specifically label a SCAQMD compliant or Rule 1168 compliant adhesive for use in those counties, which not only have a limit on VOCs, but a list of chemicals not allowed in the SCAQMD area. Also, keep in mind, there are also many adhesives that will meet the VOC limit threshold (200 g/l) or will contain no VOCs (0 g/l) for the other areas of the country with VOC limit requirements”.
SPECIFICATION FOR SUSTAINABILITY
Incorporating low and no-VOC roofing systems into the overall design of a project can help bolster sustainability, while also looking out for the health and well-being of the environment. As regulations and standards have increased the scrutiny of outdoor VOCs and the creation of photochemical ozone, manufacturers have responded by providing more earth-friendly products.
For commercial roofing, single-ply systems are the most popular, but they also often encounter regulations regarding VOCs. The three consistently specified styles of single-ply roofing are EPDM (Ethylene Propylene Diene Monomer), TPO (Thermoplastic Olefin), and PVC (Polyvinyl Chloride).
Single-ply roofing membranes can be attached to roofing substrates in several ways including mechanical fasteners, loose-laid with gravel (ballasted), or through a variety of adhesive products. These adhesives are typically marketed for use with either PVC, EPDM, or TPO roofing membranes, or for use with both TPO and EPDM roofing membranes.
Most roofing adhesives for EPDM and TPO are site-applied, single-component, and solvent-based. Craig Tyler, with Versico, says “most manufacturers have a water-based membrane adhesive which acts as the solvent, but the installation then has cold weather limitations, meaning it cannot be installed below 40°F (4.4°C) and tends to need more time for the water to “flash-off” than a conventional solvent”. The adhesive is generally applied using a roller or sprayed onto both the roofing substrate and the back-side of the roofing membrane and allowed to dry, or flash-off, until it becomes tacky. The membrane is then applied to the roofing substrate, and pressure is applied until a permanent bond is created.
Fully adhered membranes can provide a more durable roof when compared to mechanical fasteners because the fully adhered membranes tend to distribute uplift pressure more evenly across the membrane. Another benefit from both durability and ease of installation standpoint is that larger sheet sizes and rolls reduce the number of splices to complete the job while leaving fewer seams to seal.
Many of the chemicals used in solvent-based adhesives that single-ply roofing systems utilize contain VOCs, and navigating the path to compliance isn’t always easy. Most manufacturers of adhesives, sealants, and roofing systems provide low-VOC formulations, but that simple label may not mean the product is right for the project. For instance, the EPA sets limits on how much VOC a product can contain at a range of 30 to 250g/L (grams per liter). Under 250g/L, a product could be considered “low-VOC.” But as of 2023, SCAQMD Rule 1168 limits VOC emissions from adhesives and sealants commonly used in EPDM and TPO roofing systems to 200 g/L. Specifically, SCAQMD Rule 102 considers t-butyl acetate, a common additive used in sealants, to be a VOC, whereas it is considered exempt by the EPA. This is where research, documentation, and technical data sheets together become critical when specifying a roofing system in a particular area.
Also, when looking to achieve sustainable and healthy building status, it is important to note that under either definition, many exempt VOCs–those under 250g/L–still have health or environmental hazards associated with them. Just because the material is technically under the exempt limit does not mean it won’t contribute to ozone creation.
BIO-BASED ROOFING SEALANTS
One solution developed by manufacturers to reduce VOCs in roofing adhesives is to create a water-based formula. This kind of adhesive is generally only designed for PVC and certain TPO fleece-backed membranes, but it can significantly reduce the number of VOCs on the job site. Some available formulas of water-based adhesives contain less than 125g/L of VOCs.
Typical installation for water-based adhesives is designed as a one-sided, wet lay-in with no flash-off time. The adhesive must not dry during the application, or the roofing material will not adhere to the substrate. There are also limits to installation in cold weather, including it can’t be installed at less than 40°F and should not be used if the temperature is expected to fall below 32°F during the first 72-hour curing period.
Due diligence is critical when specifying water-based sealants for single-ply roofing systems. There are some products in the marketplace that tout a low-VOC water-based formula, and promote the product as applicable for PVC, TPO, and EPDM systems. Careful examination of the contents may show that though it is water-based and is technically low-VOC, it still contains 250m/L of VOCs.
GETTING CREDIT FOR LOW-VOC ROOFING
As part of the sustainability and durability pursuit, green building programs can provide guidance, direction, and justification for specifying materials and systems that promote a healthy interior, and exterior environment. While there are many programs available that provide certification on indoor air quality specifically VOCs, there are fewer programs that look at photochemical ozone potential. Fortunately, though, LEED v4 does.
LEED, which stands for Leadership in Energy and Environmental Design, is the world’s most widely used green building rating system. LEED is a points-based rating system. With LEED, projects can earn credits across eight categories: carbon, energy, water, waste, transportation, materials, health, and indoor environmental quality.
In LEED v4, the credits related to volatile organic compounds (VOCs) are primarily found in the Indoor Environmental Quality (IEQ) category and the Building Product Disclosure and Optimization section of the Materials and Resources (MR) category. However, these credits apply to VOC only on the interior of the building.
For roofing materials, there are a few options for which specifying low-VOC roofing sealants and adhesives can contribute to earn credits.
MATERIALS AND RESOURCES
Option 1: Environmental Product Declaration (EPD)
Intent: To encourage the use of products and materials for which life-cycle information is available and that have environmentally, economically, and socially preferable life-cycle impacts.
Requirement: Use at least 20 different products that have EPDs, which have been third-party verified and are in accordance with ISO 14025, ISO 14040, ISO 14044, or ISO 15927-1.
However, if the project falls within the LEED BD+C: Schools Category, then low-VOC adhesives and sealants can help earn a possible 3 points.
Low-Emitting Materials–Indoor Environmental Quality
Possible 3 Points
Intent: To reduce concentrations of chemical contaminants that can damage air quality, human health, productivity, and the environment.
Requirements: This credit includes requirements for product manufacturing as well as project teams. It covers volatile organic compound (VOC) emissions in the indoor air and the VOC content of materials, as well as the testing methods by which indoor VOC emissions are determined. Different materials must meet different requirements to be considered compliant for this credit. The building interior and exterior are organized in seven categories, each with different thresholds of compliance. The building interior is defined as everything within the waterproofing membrane. The building exterior is defined as everything outside and inclusive of the primary and secondary weatherproofing system, such as waterproofing membranes and air- and water-resistive barrier materials.
In the threshold of compliance for emissions and content standards, additional VOC content requirements for wet-applied products state that in addition to meeting the general requirements for VOC emissions, on-site wet-applied products must not contain excessive levels of VOCs. This is to protect the health of installers and other trade workers who would be exposed to these products. In order to demonstrate compliance, a product or layer must meet the following requirements, as applicable. Disclosure of VOC content must be made by the manufacturer.
Any testing must follow the test method specified in the applicable regulation.
- All paints and coatings wet-applied on site must meet the applicable VOC limits of the California Air Resources Board (CARB) 2007, Suggested Control Measure (SCM) for Architectural Coatings, or the South Coast Air Quality Management District (SCAQMD) Rule 1113, effective June 3, 2011.
- All adhesives and sealants wet-applied on site must meet the applicable chemical content requirements of SCAQMD Rule 1168, July 1, 2005, Adhesive and Sealant Applications, as analyzed by the methods specified in Rule 1168. The provisions of SCAQMD Rule 1168 do not apply to adhesives and sealants subject to state or federal consumer product VOC regulations.
- For projects outside the U.S., all paints, coatings, adhesives, and sealants wet-applied on site must either meet the technical requirements of the above regulations, or comply with applicable national VOC control regulations, such as the European Decopaint Directive (2004/42/EC), the Canadian VOC Concentration Limits for Architectural Coatings, or the Hong Kong Air Pollution Control (VOC) Regulation.
CONCLUSION
VOCs both inside and outside of the building envelope can create health issues for occupants and thus are both heavily scrutinized by building owners and regulated. Understanding the nature of VOCs in how they are measured, quantified, and categorized is critically important to help create a healthy indoor environment. Equally fundamental is to understand the distinction between indoor and outdoor VOCs, how they are defined, and what impact outdoor VOCs have on the environment. Unlike indoor VOCs, outdoor VOCs react with natural elements to create tropospheric ozone, or, smog.
This relationship between VOCs and ground-level ozone is increasingly becoming a concern as the EPA, states, and regulatory boards, such as CARB, work to create more stringent rules around the level of ozone in our communities.
For architects seeking to address VOCs when specifying roofing systems, materials, and adhesives, there are several important factors to consider. These include partnering with manufacturers who readily provide documentation in the form of data sheets and product documentation and certifications to verify VOC content and emissions levels.
In addition, it is important to rely on these partners to help identify low-VOC adhesive and sealant options that will comply with federal, state, and local building codes. This is especially relevant when specifying projects that fall within the purview of the California Air Resources Board (CARB), the Ozone Transport Commission (OTC), Lake Michigan Air Directors Consortium (LADCO), or the South Coast Air Quality Management District (SCAQMD).
Finally, as more clients seek sustainable building projects, it is important to understand how low-VOC roofing options can play a part in contributing to LEED credits, especially when designing for schools and health facilities.
Understanding how to discern between low-VOC products and collecting enough information to help choose which roofing system, style, and type is most appropriate for a project can be confusing given the varying restrictions on VOC-laden materials these days. However, a thoughtful and accountable specification process guided by a solid knowledge of VOCs and their prevalence in the building industry will go a long way to helping a project pass muster.
END NOTES
1 https://www.epa.gov/iaq-schools/why-indoor-air-quality-important-schools
2 https://pubchem.ncbi.nlm.nih.gov/compound/712#section=Vapor-Pressure
3 https://www.epa.gov/indoor-air-quality-iaq/technical-overview-volatile-organic-compounds
4 https://www.ncbi.nlm.nih.gov/pmc/articles/PMC8700805/
5 https://www.federalregister.gov/documents/2023/02/08/2023-02384/air-quality-revision-to-the-regulatory-definition-of-volatile-organic-compounds-exclusion-of
Andrew A. Hunt is Vice President of Confluence Communications and specializes in writing, design, and production of articles and presentations related to sustainable design in the built environment. In addition to instructional design, writing, and project management, Andrew is an accomplished musician and voice over actor, providing score and narration for in both the entertainment and education arena. www.confluencec.com