This CE Center article is no longer eligible for receiving credits.
Largely driven by a desire to deliver that next iconic building, corporations, higher-education institutions, and even private-sector clients are actively engaging architects to design sleek curtain-wall facades that stand out from the crowd.
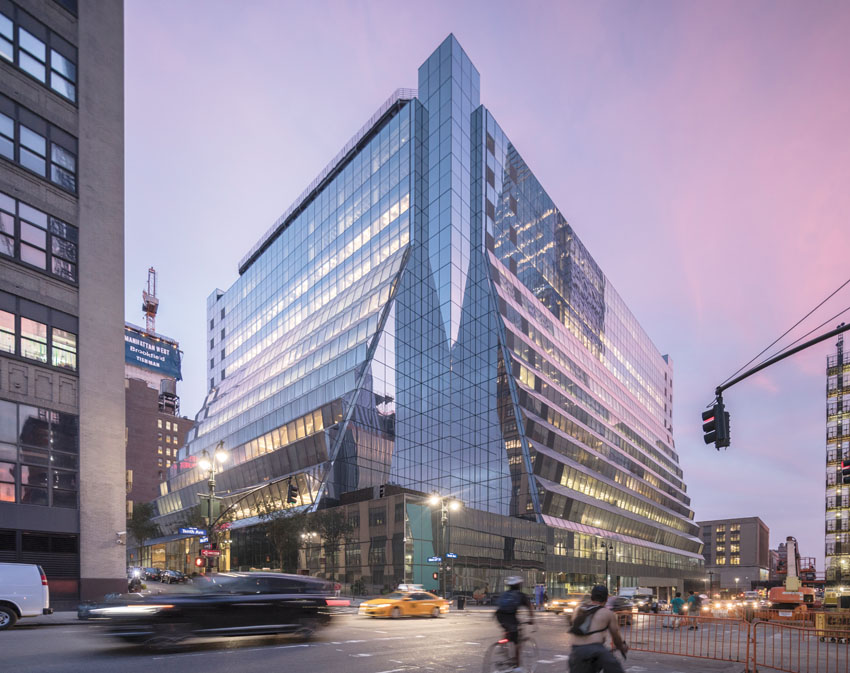
Photo courtesy of REX/© Laurian Ghinitoiu
REX and Front’s redesign of the 5 Manhattan West angled curtain wall was successfully achieved with a well-managed design-assist project approach, closely involving the full project team.
“Brand and user experience is huge, and clients want inspirational, high-performance spaces that walk the walk in terms of environment and sustainability,” says MIT School of Architecture Associate Professor of Practice Marc Simmons, founding principle of the New York-based facade systems design firm Front.
“As the face of the building, we feel a responsibility to deliver a thoughtful, dynamic skin that will contribute to the residents’ and public’s experience of the home and the city fabric,” adds Marci Clark, Ph.D., development director, architectural historian, JDS Development Group, New York.
From large high-tech companies to public courthouses to universities, cutting-edge curtain-wall designs, particularly in urban areas where mid-sized and tall buildings are on the rise, are filling an important niche.
“Curtain walls offer the best combination of single-source, high-performance, customized enclosures, and are often the most desirable alternative to meet the complex demands of modern large projects like quality, speed, and lower risk,” says Sameer Kumar, AIA, LEED AP, director of enclosure design, SHoP, New York.
Another driving factor enabling the design and execution of complex curtain-wall designs is the latest technological advancements. Perhaps most significant has been the transition from 2-D AutoCAD to 3-D drawing platforms, such as Rhino, Revit, Inventor, Softworks, and Cotia.
In addition, Jeff Heymann, vice president, Benson Industries, Portland, says the application of CNC, BIM, and robotics to the manufacturing process has enhanced the capabilities of glass fabrication. Consequently, the fabrication, coating, insulation, lamination, and production of larger glass lites and bent glass—both hot and cold formed—is more predictable and readily available.
“Glass sizing is being pushed larger and larger, and companies are developing ways to curve, laminate and use glass in ways that were previously unthinkable,” adds Anthony Kantzas, facade consultant, Front, New York.
And new techniques with frits and screen printing, digital printing, and new interlayers have made glass a greater part of the facade’s shading scheme, decorative features, and overall aesthetic.
Heymann adds that improvements in CNC and equipment intelligence have increased the ability to fabricate aluminum extrusions and panels with a high degree of complexity to keep pace with building geometry and form. He is also seeing more interest in adopting different materials into aluminum-framed curtain walls, be it terracotta, other metals, cementitious products, or photovoltaic panels.
While the results of these enhanced technological capabilities are often remarkable, complex facade projects require a close-knit building team, optimized leveraging of expertise, and a well-sequenced operation from design to fabrication to construction, in order to optimally mitigate risk and efficiently deliver projects.
“The best practice by far when dealing with a novel, innovative, or complex facade design is to engage all key players involved in the implementation of the facade program as early in the process as possible,” says Mic Patterson Ph.D. LEED AP, ambassador of innovation and collaboration, founder, immediate past president, Facade Tectonics Institute, Los Angeles.
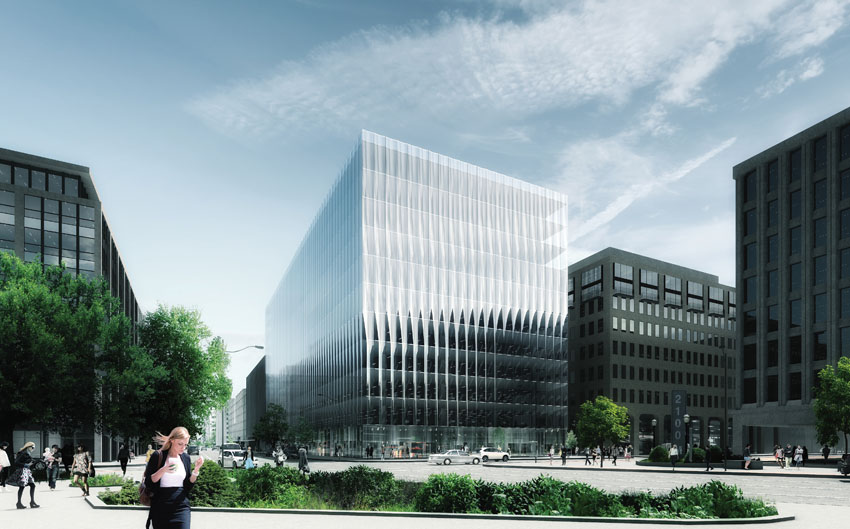
Photo courtesy of Samson Properties
2050 M Street’s striking Washington, D.C., facade, delivered via design-assist, creates a kaleidoscopic effect with hundreds of identical, subtly curved insulated glass panels with no mullions for a full all-glass aesthetic.
SELECTING THE RIGHT PROJECT-DELIVERY APPROACH
In selecting a project-delivery method, the decision should be dictated by the individual needs of each project.
“The geographical location, the overall project schedule, and the specific mix of materials on a project are some of the key variables that contribute to the procurement strategy,” Kumar explains.
For example, if building performance is the main goal, a design-build approach might be a good way to go. Similarly, more simplified designs are usually suited for a traditional project-delivery model.
However, with more complex designs, experts advocate for design-assist, despite the fact that building owners may be hesitant to depart from the traditional way of doing things. Design-assist is the procurement method by which, prior to completion of design, a construction contract may be awarded on a best-value basis pursuant to which a contractor provides design assistance to the architect or engineer of record through a design professional separately retained by the contractor. It is a collaborative, team-oriented process that capitalizes on the benefits of early engagement of all parties.
“The facade contractor does not define the project-delivery strategy, but when asked, we always encourage a design-assist approach,” confirms Jeffrey Vaglio, Ph.D., PE, AIA, vice president of Advanced Technology Studio, Enclos, St. Louis. “The preference toward design-assist is because it aligns with our in-house technical strengths, and embracing of prototyping technology allows us to add value and advance critical decisions that are all in the best interest of a project schedule.”
As a contractor, Heymann agrees, “In our experience, the best project-delivery strategy for major projects is to engage us in a design-assist usually 20 to 24 months before curtain wall is to be ready to install on-site.”
This way, the contractor can most optimally work along with the design team as a true partner to help develop the facade to a point where the scope of work can be locked in by the curtain-wall fabricator with a lump-sum price. “We can then manage a schedule that works within the overall construction schedule,” he concludes.
While this looks great on paper, one of the challenges is that fact that the AECO industry is notoriously risk averse and therefore wary of innovation, explains Patterson. So the process of embracing of truly collaborative project-delivery processes has been frustratingly slow.
Patterson believes that the problem is fundamental: The industry is founded on deeply instilled competitive practices and has yet to gain adequate experience in true collaboration.
“This is why attempts at embracing collaborative delivery strategies often stall out or are largely abandoned before a project’s completion,” he laments.
Unfortunately, advanced facade designs are almost impossible to execute without a fully team-integrated process.
“It is critical that a complex or novel facade design, or one involving any form of innovative product or material, utilize some form of collaborative delivery strategy,” he says.
In cases where the project stakeholders are willing to go with a design-assist process, Matt O’Malley, DPR Construction, Reston, Virginia, offers some best-practice advice from the perspective of the general contractor (GC).
- Be collaborative but also proactive about managing the design-assist process. Do not leave it to the design team and to the curtain-wall subcontractor. The GC has to drive the process to ensure the right results.
- The GC needs to maintain relationships with all players in the supply chain, not just the prime subcontractor.
- The GC also needs to understand where the materials are coming from. This includes visiting the various shops and facilities along with the prime subcontractor in order to ensure production schedule and quality.
- While most of the supply-chain management will be the responsibility of the prime subcontractor, the GC needs to take an active role in helping to ensure performance.
Adding some additional insights on the design-assist process, O’Malley observes that most of the major curtain-wall subcontractors prefer working this way, and that most of the major vendors have large backlogs and need to be engaged early enough to ensure capacity.
Largely driven by a desire to deliver that next iconic building, corporations, higher-education institutions, and even private-sector clients are actively engaging architects to design sleek curtain-wall facades that stand out from the crowd.
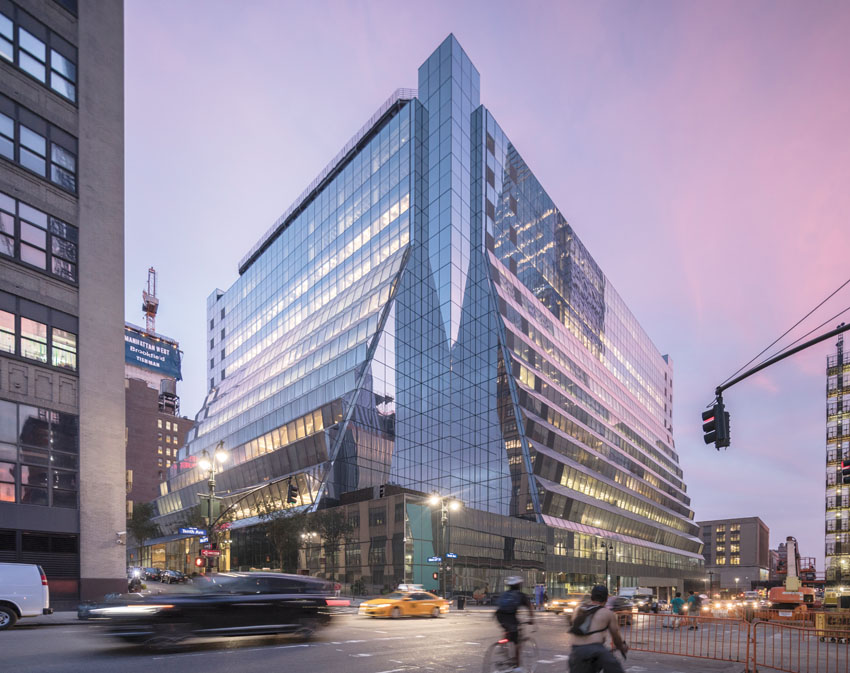
Photo courtesy of REX/© Laurian Ghinitoiu
REX and Front’s redesign of the 5 Manhattan West angled curtain wall was successfully achieved with a well-managed design-assist project approach, closely involving the full project team.
“Brand and user experience is huge, and clients want inspirational, high-performance spaces that walk the walk in terms of environment and sustainability,” says MIT School of Architecture Associate Professor of Practice Marc Simmons, founding principle of the New York-based facade systems design firm Front.
“As the face of the building, we feel a responsibility to deliver a thoughtful, dynamic skin that will contribute to the residents’ and public’s experience of the home and the city fabric,” adds Marci Clark, Ph.D., development director, architectural historian, JDS Development Group, New York.
From large high-tech companies to public courthouses to universities, cutting-edge curtain-wall designs, particularly in urban areas where mid-sized and tall buildings are on the rise, are filling an important niche.
“Curtain walls offer the best combination of single-source, high-performance, customized enclosures, and are often the most desirable alternative to meet the complex demands of modern large projects like quality, speed, and lower risk,” says Sameer Kumar, AIA, LEED AP, director of enclosure design, SHoP, New York.
Another driving factor enabling the design and execution of complex curtain-wall designs is the latest technological advancements. Perhaps most significant has been the transition from 2-D AutoCAD to 3-D drawing platforms, such as Rhino, Revit, Inventor, Softworks, and Cotia.
In addition, Jeff Heymann, vice president, Benson Industries, Portland, says the application of CNC, BIM, and robotics to the manufacturing process has enhanced the capabilities of glass fabrication. Consequently, the fabrication, coating, insulation, lamination, and production of larger glass lites and bent glass—both hot and cold formed—is more predictable and readily available.
“Glass sizing is being pushed larger and larger, and companies are developing ways to curve, laminate and use glass in ways that were previously unthinkable,” adds Anthony Kantzas, facade consultant, Front, New York.
And new techniques with frits and screen printing, digital printing, and new interlayers have made glass a greater part of the facade’s shading scheme, decorative features, and overall aesthetic.
Heymann adds that improvements in CNC and equipment intelligence have increased the ability to fabricate aluminum extrusions and panels with a high degree of complexity to keep pace with building geometry and form. He is also seeing more interest in adopting different materials into aluminum-framed curtain walls, be it terracotta, other metals, cementitious products, or photovoltaic panels.
While the results of these enhanced technological capabilities are often remarkable, complex facade projects require a close-knit building team, optimized leveraging of expertise, and a well-sequenced operation from design to fabrication to construction, in order to optimally mitigate risk and efficiently deliver projects.
“The best practice by far when dealing with a novel, innovative, or complex facade design is to engage all key players involved in the implementation of the facade program as early in the process as possible,” says Mic Patterson Ph.D. LEED AP, ambassador of innovation and collaboration, founder, immediate past president, Facade Tectonics Institute, Los Angeles.
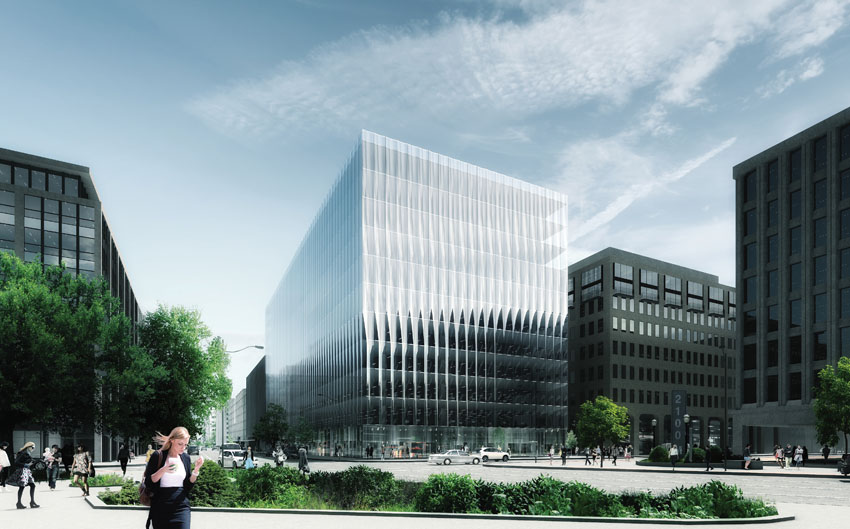
Photo courtesy of Samson Properties
2050 M Street’s striking Washington, D.C., facade, delivered via design-assist, creates a kaleidoscopic effect with hundreds of identical, subtly curved insulated glass panels with no mullions for a full all-glass aesthetic.
SELECTING THE RIGHT PROJECT-DELIVERY APPROACH
In selecting a project-delivery method, the decision should be dictated by the individual needs of each project.
“The geographical location, the overall project schedule, and the specific mix of materials on a project are some of the key variables that contribute to the procurement strategy,” Kumar explains.
For example, if building performance is the main goal, a design-build approach might be a good way to go. Similarly, more simplified designs are usually suited for a traditional project-delivery model.
However, with more complex designs, experts advocate for design-assist, despite the fact that building owners may be hesitant to depart from the traditional way of doing things. Design-assist is the procurement method by which, prior to completion of design, a construction contract may be awarded on a best-value basis pursuant to which a contractor provides design assistance to the architect or engineer of record through a design professional separately retained by the contractor. It is a collaborative, team-oriented process that capitalizes on the benefits of early engagement of all parties.
“The facade contractor does not define the project-delivery strategy, but when asked, we always encourage a design-assist approach,” confirms Jeffrey Vaglio, Ph.D., PE, AIA, vice president of Advanced Technology Studio, Enclos, St. Louis. “The preference toward design-assist is because it aligns with our in-house technical strengths, and embracing of prototyping technology allows us to add value and advance critical decisions that are all in the best interest of a project schedule.”
As a contractor, Heymann agrees, “In our experience, the best project-delivery strategy for major projects is to engage us in a design-assist usually 20 to 24 months before curtain wall is to be ready to install on-site.”
This way, the contractor can most optimally work along with the design team as a true partner to help develop the facade to a point where the scope of work can be locked in by the curtain-wall fabricator with a lump-sum price. “We can then manage a schedule that works within the overall construction schedule,” he concludes.
While this looks great on paper, one of the challenges is that fact that the AECO industry is notoriously risk averse and therefore wary of innovation, explains Patterson. So the process of embracing of truly collaborative project-delivery processes has been frustratingly slow.
Patterson believes that the problem is fundamental: The industry is founded on deeply instilled competitive practices and has yet to gain adequate experience in true collaboration.
“This is why attempts at embracing collaborative delivery strategies often stall out or are largely abandoned before a project’s completion,” he laments.
Unfortunately, advanced facade designs are almost impossible to execute without a fully team-integrated process.
“It is critical that a complex or novel facade design, or one involving any form of innovative product or material, utilize some form of collaborative delivery strategy,” he says.
In cases where the project stakeholders are willing to go with a design-assist process, Matt O’Malley, DPR Construction, Reston, Virginia, offers some best-practice advice from the perspective of the general contractor (GC).
- Be collaborative but also proactive about managing the design-assist process. Do not leave it to the design team and to the curtain-wall subcontractor. The GC has to drive the process to ensure the right results.
- The GC needs to maintain relationships with all players in the supply chain, not just the prime subcontractor.
- The GC also needs to understand where the materials are coming from. This includes visiting the various shops and facilities along with the prime subcontractor in order to ensure production schedule and quality.
- While most of the supply-chain management will be the responsibility of the prime subcontractor, the GC needs to take an active role in helping to ensure performance.
Adding some additional insights on the design-assist process, O’Malley observes that most of the major curtain-wall subcontractors prefer working this way, and that most of the major vendors have large backlogs and need to be engaged early enough to ensure capacity.
DESIGN PHASE
A curtain-wall facade project’s design phase frequently employs many of the aforementioned advanced digital design tools. Where complex geometries are involved, architects and facade designers turn to parametric modeling like Grasshopper for Rhino3-D to study the extent of variation in a skin’s panelization, determine governing dimensions, and conceptualize system details that are applicable across a range of unique instances, explains Vaglio.
“Early phases also rely on Revit to set up estimating models, AutoCAD for detailing, as well as structural and thermal analysis software,” he adds.
At Front, experts will take programs like Grasshopper and write their own customized scripts to better analyze geometry and generate design options. Furthermore, the facade consulting group will program their own plugins when there are no commercially available tools suitable for the task.
One example is a tool that Front created called Elefront, accessible at www.food4rhino.com/app/elefront. “It enables us to embed and manage complex building information in the 3-D model and streamline the process from design to fabrication,” says Kantzas. “Due to the complexity of certain projects, we also invented a workflow that divides a building into different systems, components, and stages, allowing team members to work collaboratively and concurrently on a large-scale complex project.”
Overall, Simmons explains that this initial design process involves applying iterative forms of analysis performed again and again and again to ultimately arrive at the efficiencies and characteristics that the project team is seeking.
From a performance standpoint, Yalin Uluaydin, RA, Eckersley O’Callaghan & Partners, New York, points out that the facade design must be verified first and foremost. Many times, structural modifications are needed before moving on to the detailing and design phases, where issues of constructability are dealt with.
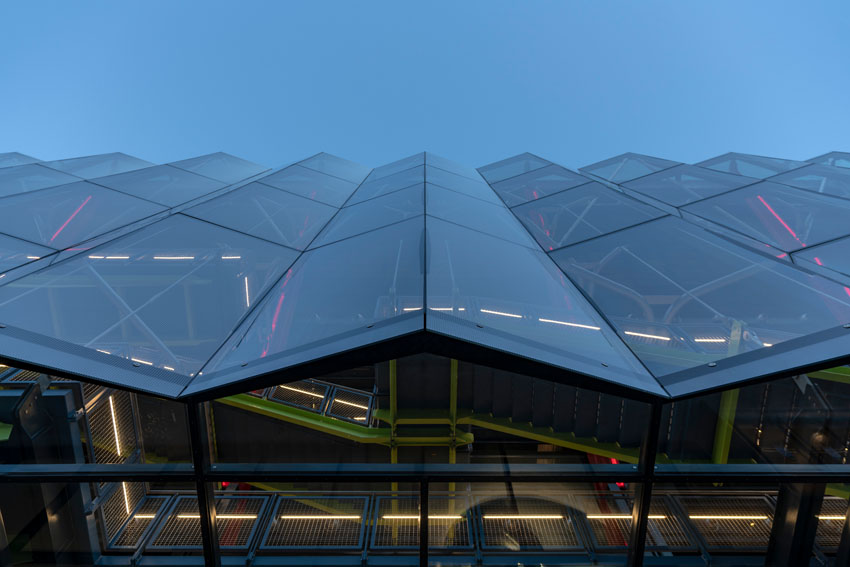
Photo courtesy of Eckersley O’Callaghan & Partners
At the International Spy Museum in Washington, D.C., the final design features a folded structural glass veil suspended in front of the “black box” exhibition space.
Simultaneously, as the facade is being designed, an integrative process will pool the expertise of fabricators and contractors, thereby benefitting from their valuable input.
Along these lines, SHoP’s process involves tapping into various design and communication technologies like 3-D modeling, 3-D printing, AR, virtual reality, and physical prototyping to develop their concepts into buildable designs. “At the same time, we interface with the client team and contractors to draw interest from the facade industry stalwarts and get early input on general detailing strategies and feasibility, as well as project scheduling and procurement strategies,” says Kumar.
In terms of ways in which contractors offer advice on feasibility, one example is metrics developed by Benson that help determine the relative complexity of one project as compared to the next, and to ascertain the level of risk and potential resource requirements. Ultimately, Heymann says that a lot of the decision-making comes down to lessons learned from past projects, so it is in the best interest of project teams to draw in experienced contractors.
DESIGN-ASSIST
By working in a design-assist process, the design team can work with the contractor toward a dedicated guaranteed maximum price, and this usually helps accelerate the project schedule.
From the perspective of risk management, Patterson points out that a risk-averse building industry—with the owner on one end and the vendor/fabricator on the other—will typically work to push the risk down or upstream, respectively. “Often the risk concentrates on the facade contractor who is left to figure out how to best implement the facade program,” he explains. “But the remarkable thing is that these attempts to deflect risk are seldom successful, and if a challenging facade application goes awry, everyone involved in the project suffers.”
Consequently, the best practice by far when dealing with an innovative or complex facade design is to engage all key players involved in the implementation of the facade program as early in the process as possible. “Schematic design is not too early to bring these entities onboard,” Patterson says.
When the facade contractor is engaged as a paid member of the design team and tasked with sitting shoulder-to-shoulder with the architect’s facade designer, it can then provide real-time budget, schedule, and constructability input throughout the design process, explains Patterson. In a true design-assist setting, the team has the opportunity to work through the details of the design, eliminating surprises at bid time.
In facade contractor Enclos’ experience, it finds its input being requested earlier and earlier. For example, being invited to bid on a product based on only 50 percent of design development documents is not unusual. Furthermore, the bid to build the facade is accompanied by a fee for design-assist services for a period of time to collaborate with the architect and facade consultants to arrive at a constructible solution, by 100 percent design development, that aligns with the project’s target budget, explains Vaglio. “Arriving at a buildable system that sets up the manufacturing and construction phase is essential to ensure the schedule goals can be achieved,” he adds.
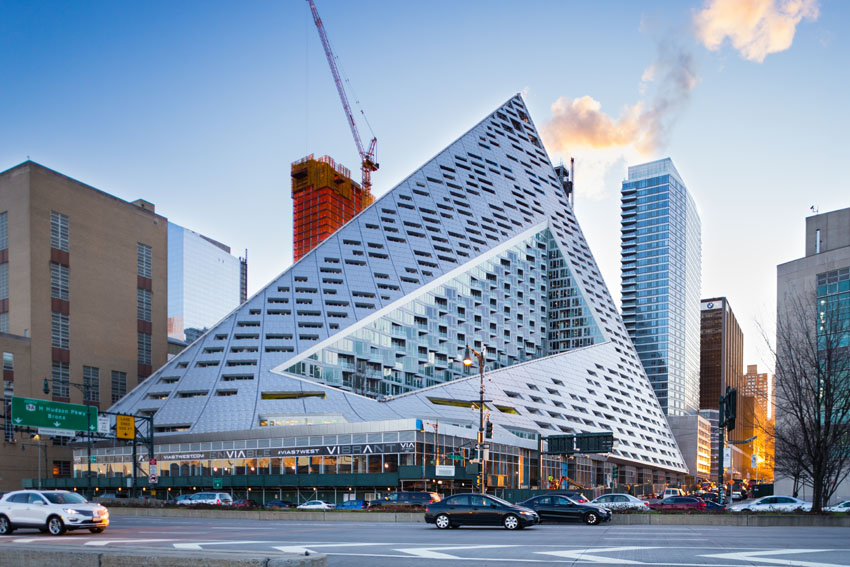
Photo courtesy of Enclos
The facade contractor should be brought in early on for collaborating with the architect and facade consultants in or to arrive at a constructible solution. This was the case for VIA 57 West in Manhattan.
In cases where the facade contract is only awarded at the end of construction documents, this can create a situation where architects might be brow-beaten into decisions contrary to the design intent due to downward pressure of the construction schedule, costs associated with maintaining the original design, unforeseen conditions, etc.
On the other hand, with design-assist, the facade contractor can work on the performance mockups and project shop drawings prior to groundbreaking, which can also take the facade off the critical path in some cases. “This whole process brings advantages to everyone in the AEC team, as issues can be resolved in an agreeable manner,” Uluaydin says.
While this is an ideal scenario, Patterson is afraid that the industry has failed to converge on a definition for design-assist. “For many in the industry, it remains the practice of inviting a facade contractor in at some point during design development and learning as much as can be learned for free, which is not design-assist, but rather business as usual,” he says.
Similarly, O’Malley observes that some designers are reluctant to engage the contractor too early because they feel that it might stifle their ability to design the project the way they want, and some owners still feel that the best way to get the lowest price is to finish the drawings and have a competitive bid.
Curtain-wall companies can contribute in several ways to the early stages of a project: they can provide valuable advice and guidance, including options on how to configure the system; material and product sourcing options; cost estimates; input on logistics, site constraints and erection options; and feedback on lead times and market capacity.
While a general best practice for bringing in the curtain-wall company is also “the earlier, the better,” O’Malley points out that the design team needs to first spend some time exploring concepts, massing, and material types with the building owner in order to hone in on a general concept for the design. Furthermore, the industry is very busy, and curtain-wall contractors have plenty of projects from which to choose. Consequently, the design team has the best chance of hiring the right curtain-wall company for the job if it has already defined some of the major parameters of the project.
The glass supplier can also provide critical information on the performance attributes of various architectural glass products, and attributes that affect the sizing of mechanical systems and the ultimate comfort of the building occupants.
As decisions continue to be made, Enclos often creates project-specific animations of the construction sequence and full-scale 3-D printed prototypes of key performance details. “The 3-D prints help educate our customers on where the performance is occurring within their facade system, while the animations clearly showcase a site logistics plan, revealing early on any coordination items with the general contractor,” Vaglio says.
“When design development has concluded and a project moves into production engineering, teams use Inventor to develop detailed models of each unit,” he continues. “A lot of energy is invested in precision at this stage, and the primary beneficiary is the manufacturing shop. Leveraging the data from the Inventor models, we have developed a proprietary workflow that links this information to CNC machines and inventory tracking. This provides a level of quality control at each step in fabrication and assembly.”
Giving a sense of timeline, Uluaydin says that for most small- to mid-size projects with a performance and visual mockup, contractors need about 12 to 16 months for mockups, submittals, engineering, fabrication drawings, procurement, and fabrication. He adds that complex facade systems may involve the use of new materials or technologies, which require quite a lot of testing before implementation.
Heymann advises that a project’s performance mockup capture as many details as possible: “The knowledge gained while working on the performance mockups helps progress the shop drawing details, fabrication, and assembly plan, and our field installation crew can better understand the nuances inherent with any custom design.”
This is especially the case with complex geometries, because the facade contractor must understand the tolerances inherent in materials, fabrication, installation, and how those relate to building structure tolerances and movements. These factors combined ensure that expectations for quality and aesthetics can be successfully achieved, he adds.
Design features such as oversize curtain-wall and glass units, sunshades, and crown and roof screen walls and claddings can become very ornate. “This creates complexities that need to be studied and planned well in advance so those requirements can be built into the design, cost, and schedule of the project,” Hemann says.
Depending upon site conditions, executing the logistics of facade installation may be yet another hurdle to overcome, particularly in the absence of a tower crane, as contractors will need to get creative to transport the materials into the building to be able to set from the floor slabs.
“Getting the unitized panels into the hoist for distribution on floors can be a critical plan to assure the installation goes as efficiently as possible,” says Michael Haber, managing partner, W&W Glass, Nanuet, N.J.
In some cases, a custom lifting/rigging systems is needed to install complex geometry or deal with otherwise inaccessible conditions. “These solutions require a great deal of upfront planning and design technologies to prove the efficacy,” he adds.
Additional logistical challenges may include the size of ocean containers, over-the-road shipments, building site access and unloading, opportunities for vertical transportation on-site, hoisting and installation equipment capacity and capabilities, trade personnel access to work points, and construction sequencing within the system and with other trades, relates Heymann.
MANAGING THE SUPPLY CHAIN
As a project’s facade begins to take shape out in the field, the entire sequencing process is most complex, requiring a high level of management.
One of the ways that Enclos deals with this challenge is by tapping into extensive network of preferred partners who offer many of the common materials utilized in a facade. “With early communication to key material suppliers and a timely commitment to work with them, they can be setup for success to be productive,” Vaglio explains.
Of course, there can always be anomalies and/or schedule changes, driving the team to adapt and supplement with additional internal resources or external partners.
“Any hiccup in the supply chain is a potential disaster,” Patterson says. “Delays to the installation of the facade system leave the building open to the elements and prevent the following trades that require building enclosure before they can proceed. Successful facade contractors have learned to be experts in supply chain management.”
In trying to avoid a situation where a particular material has yet to arrive on-site at installation time, Clark Construction Group spends time vetting their partners. “This includes researching subcontractor supply chains and making visits to verify that they can perform to standards that we believe are necessary to achieve the required results,” reports Joseph Conover, vice president, Clark Construction Group, Los Angeles.
“Lead times are also critical path items and must be considered when selecting the right vendors,” agrees Haber. “We have to know that the vendors have the capacity to produce products within the scheduled delivery window when we need it. Otherwise you will fall behind and slow the process of other trades putting the project schedule in jeopardy.”
Heymann also agrees that the building team members need to be active participants in understanding the capabilities, core competencies, and lead times of the key material suppliers for the facade. His firm has a close relationship with key aluminum and glass suppliers, and will hire them based on their ability to manufacture to the quality required in the specifications, their manufacturing capacity, and their ability to respond when there are hiccups.
In reality, Uluaydin says it is rare that the contractors will not have materials on-site or labor to perform the installation, “Materials not delivered on time or excess labor pool is a financial and schedule burden for contractors, so they manage this as part of their responsibilities,” he explains. “This causes a delay and has serious implications for subs and contractors and is something they try and avoid.”
What can come up are issues surrounding the visual quality of materials and a lack of specification that can quantitatively be used to judge quality, and this can delay material delivery. In order to mitigate this, a preconstruction process is generally applied to work out these types of issues.
In addition to having the capacity to provide the required volume of fabricated material, selected vendors need to have the technical knowledge to engineer and competently fabricate solutions that will work for the exact project requirements, Haber adds. “If either of these requirements are lacking, there will be potential for poor quality, material not fitting on-site, requiring re-engineering or remakes, or material not being delivered. This will ultimately cause project delays which all can lead to lost revenues,” he explains.
To best avoid these types of situations, factory visits should be made to review quality during fabrication. “If not managed, an undesirable distortion or visual defect may end up on the building due to schedule constraints,” Uluaydin warns. “This is where tight specs and tangible review criteria are needed to judge materials for compliance. Otherwise it is subjective and just leads to disputes.”
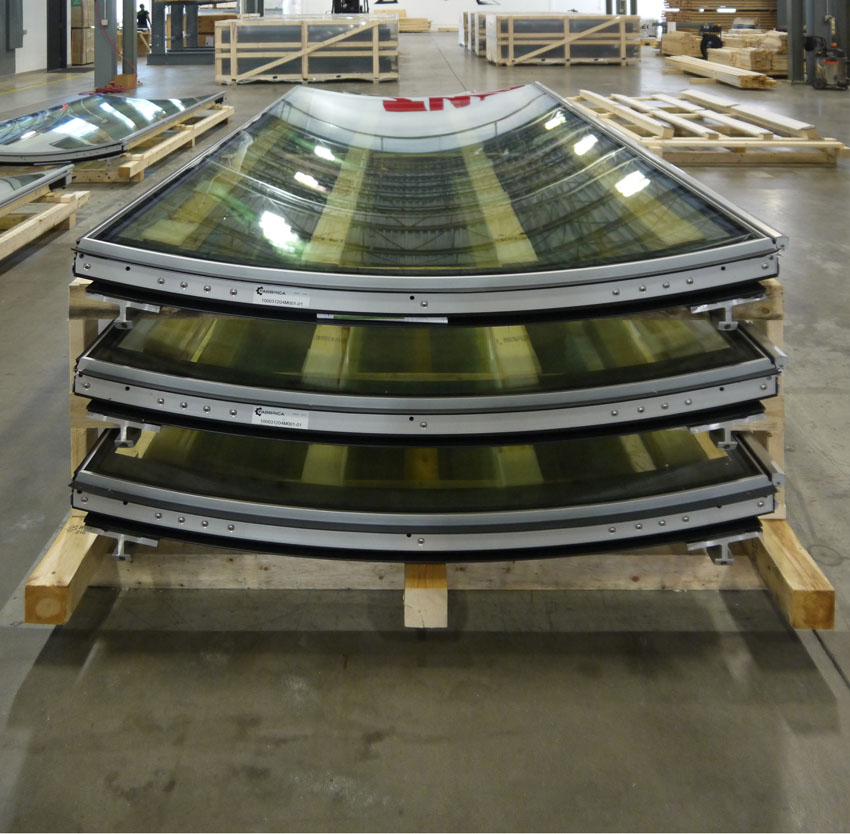
Photo courtesy of REX/© Luxigon
The curved panels for 2050 M Street are inspected in Fabrica’s shop in Enfield, Connecticut, before shipment to the site.
Another issue surrounding risk mitigation is having the right labor on hand at the right time. In order to address this, as a union company, Benson has access to glaziers and iron workers in whatever locale they work. “We are also mindful not to take on too much work in any one region so we can recruit, manage, and maintain a quality workforce,” Heymann explains.
Offering a big-picture perspective on this process, Simmons compares it to a spiral circling upward. Travelling along the spiral, the design team collects data points for all aspects of the project, and builds confidence and awareness for best system design and technical detailing. As the process cycles up, things start coming into focus.
“There is a fear of things coming undone along the way, and we are constantly trying to assess and control risk as it appears,” he explains.
EXCEPTIONAL FACADE PROJECTS
A great project example of successfully managing the supply chain is Bjarke Ingels Group’s VIA 57 West pyramidal-shaped condominium complex built around a sprawling, European-inspired interior courtyard.
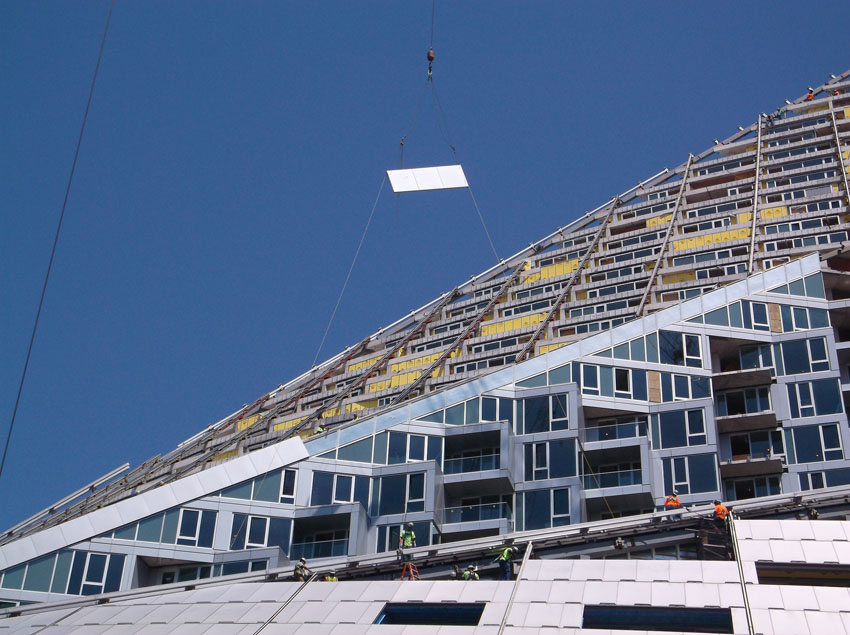
Photos courtesy of Enclos
Simulations and parametric modeling helped the design team fine tune, fabricate, and deliver a unique pyramidal-shaped facade enclosing a large interior courtyard for VIA 57 West.
With four distinct elevations and a sloping, hyperbolic-shaped roof, the sizing of the gutters to support optimal distribution of rainfall had to be studied early on in the design. This was accomplished with Enclos’ Advanced Technology Studio, using a combination of RealFlow simulations and parametric Grasshopper models to analyze the water flow distribution for every panel.
Creating a continuous, smooth, double-curved surface along the south elevation was also challenging.
“In order to achieve the tight tolerance of the design intent, our team developed detailed fabrication-ready 3-D models for each of the more than 1,200 unique mega-panels creating the sloped facade and fed this information into our CNC machines,” explains Alessandro Ronfini, senior designer, Advanced Technology Studio, Enclos. “During and after the fabrication and assembly process, each panel went through a rigorous quality-controlled process that included a laser metrology scanner, which verified that each double-curved geometry was an exact match of the master 3-D model.”
Once analyzed and approved, each panel was transported to the site for installation. Here, laser scanning and constant verification of the built condition with the master 3-D model were essential to confirming that the physical location of each panel matched the ideal location of its digital twin, he explains.
To accommodate the concrete and steel tolerance, Enclos built the anchors securing the facade to the main structure with a tolerance of 2 inches in all directions. “This gave us enough room to adjust each panel as necessary to achieve the shiny, smooth surface you can admire along the Hudson River today,” relates Ronfini.
About 10 miles up the river, at Columbia University’s Manhattanville campus, a 12-story and nine-story building, separated by a large plaza, will become the new home of Columbia’s Business School.
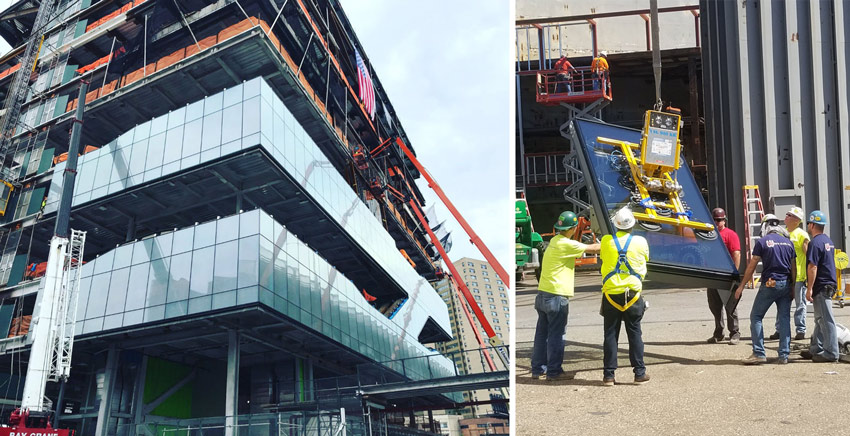
Photos courtesy of W&W Glass
With five different wall systems, the design, fabrication, and installation of two new buildings at Columbia University’s Manhattanville campus required large mockups to test for air, water, thermal, and acoustic performance to verify the system’s integrity.
The facades consist of GFRC panels, aluminum single-span, multistory unitized curtain walls, and a tall span structurally-glazed glass fin all coming together across multiple levels. Consequently, coordinating all the materials and ensuring a seamless, weathertight system was a big challenge.
“Projects like this require a high degree of R&D to develop systems then prove them out by building mockups for each wall type with specific conditions to put them through a battery of tests at a lab,” explains Haber.
In order to accomplish this, the project team collaborated early on with vendors to get their input. “This project had five different wall types and two large performance mockups that were fully tested for air, water, thermal, and acoustic performance to verify the integrity of the system as the different wall types came together. In addition, there were multitude of visual mockups used to illustrate visual concepts, fit, and finish.”
Ultimately, by working through bugs during the mockup phase, a certain level of risk was mitigated.
For another W&W project, the curtain-wall installer was challenged with ensuring that 47-story unitized curtain wall system at 30 East 29th Street could integrate custom chevron-shaped insulated metal panels into the facade in a weathertight manner.
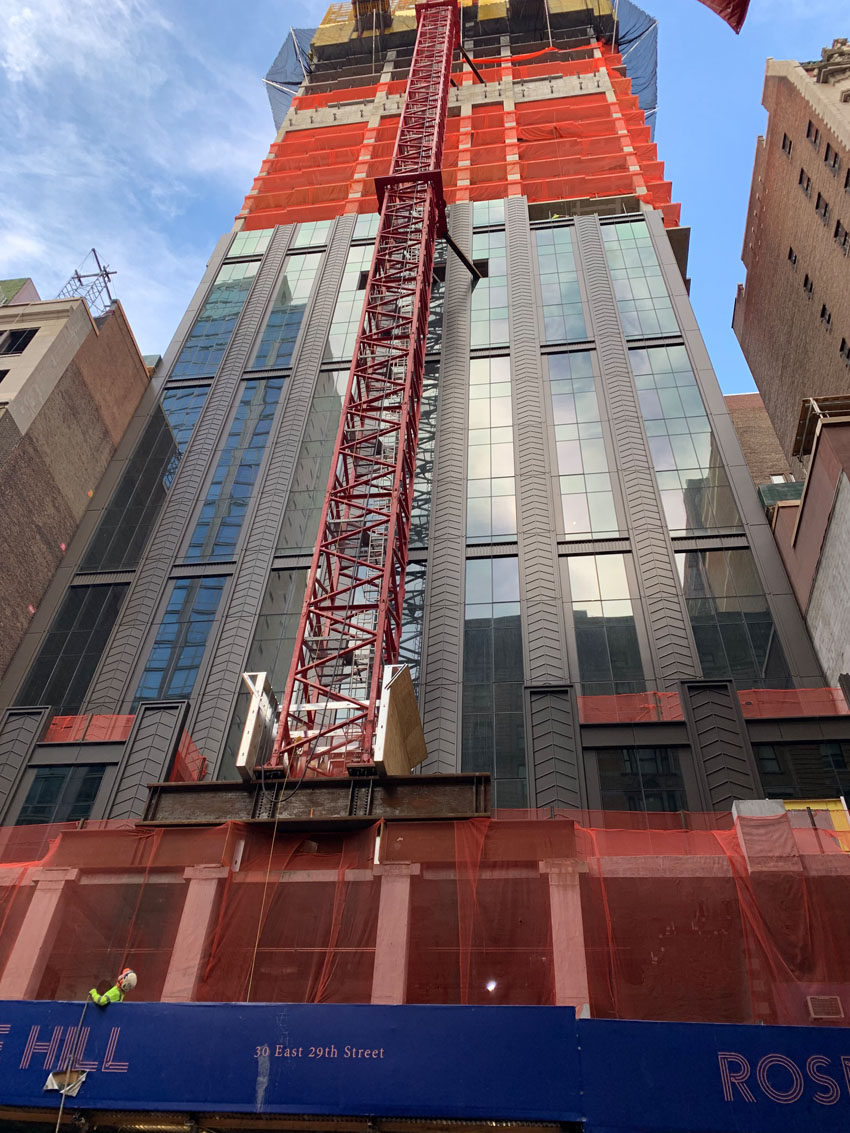
Photo courtesy of W&W Glass
For the 47-story 30 East 29th Street facade, an intensive R&D process was engaged in order arrive at alternate fabrication methods for curtain-wall panels so that they could be incorporated with a complex shape and profile.
“There was intensive R&D into alternate fabrication methods for the panels so that they could be incorporated with this complex shape and profile,” Haber says. “Custom vertical extrusions were also added next to the panels to add banding to the chevrons and windows.”
While bar stock receivers, used on typical aluminum metal panel systems to engage into traditional curtain wall pockets, were considered, they did not turn out to be a viable option.
“The design ultimately used a custom profile at the edge of the panel to achieve the aesthetics the architect desired with feasibility from a technology perspective to assure it could be efficiently fabricated and sealed on a shop assembly line,” says Haber.
By doing this additional design work upfront, the team mitigated risk, and the final result was a clean, tight transition between insulated metal panel, extrusion profile, and the structurally glazed curtain wall mullion.
The iconic New York Times Building provides another example of how additional work performed early on can pay off in the long run. In this case, Forest City Ratner paid Benson a stipend before the project was even awarded to develop details and best means and methods to help understand the facade design’s ceramic brise soleil and come up with manufacturing methodology that would be consistent throughout the project.
“By working on a visual mockup early in the process, we were able to demystify the sunscreen design. It gave us confidence that our ideas and the use of materials and vendors —like the aluminum extrusion fabrication and ceramic baguette supplier—would meet the tolerances required and assemble relatively easily,” Heymann says.
Just south of VIA 57 West, at 5 Manhattan West, REX designed a scheme to reclad the building with a contemporary, pleated facade design. Analysis showed that due to the additional weight, the existing slabs were insufficient to support the weight of the new structural system.
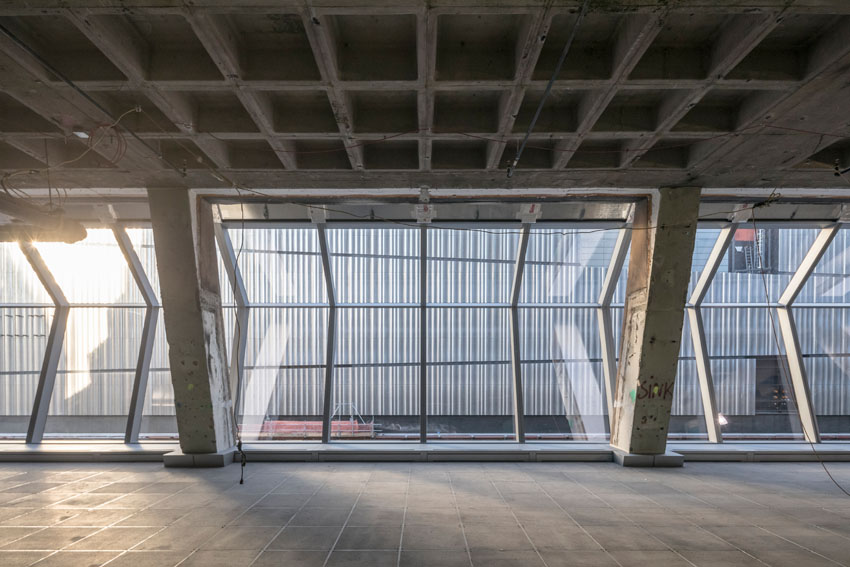
Photo courtesy of REX/© Laurian Ghinitoiu
Pleated curtain-wall panels were specially designed for 5 Manhattan West to simultaneously sit and hang so that the heavy pieces would not rotate during lifting and placement.
“We decided to span new steel called spreader bars, supported between columns to support the new facade system,” explains Kantzas. “This means that all of the loading from the facade goes directly into the columns and no load is imparted onto the slabs.”
However, drilling expansion anchors into the side of the fully reinforced columns was a challenge, so columns were X-ray scanned in order to locate reinforcement.
Furthermore, the facade’s stepped design made hoisting and setting the panels very difficult challenge. Custom lifting rigs were developed to adequately lift the panels so they would not rotate. However, the panels were very heavy, and with the pleat/kink in the panel, it was difficult to get it to dead load at one slab level, according to Kantzas. “We had to design the panels so they sat and hung at the same time,” he explains.
NYC TO DC
More recently, REX and Front collaborated on facade design for 2050 M Street in Washington, D.C. REX’s vision was to create a kaleidoscopic effect with hundreds of identical, subtly curved insulated glass panels with no mullions for a full all-glass aesthetic.
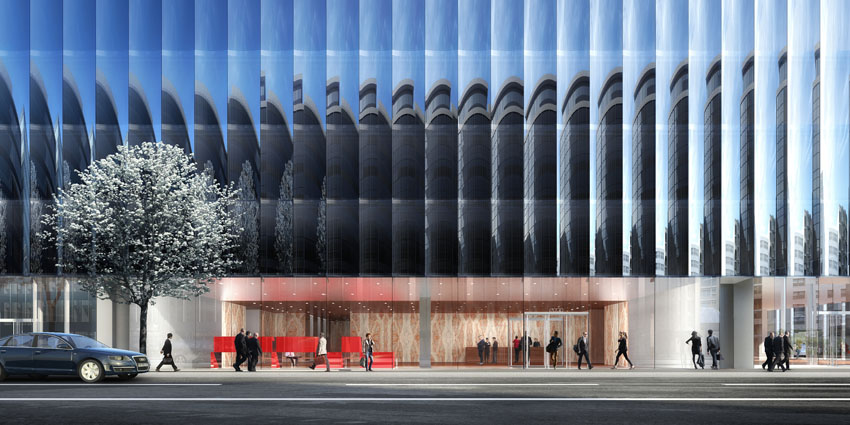
Photo courtesy REX/© Luxigon
The unique glass at 2050 M Street creates a new Washington, D.C., office type, one which combines the advantages of an all-glass building with the modulation of a high-relief facade befitting its context.
However, when working with curved, laminated panels, Simmons points out that a higher variation in the fabricated geometrical dimensions of the panels is common, thereby compromising a clean aesthetic post-installation.
Fortunately, the team decided that a tight-tolerance aluminum frame could absorb the looser glass, drawing the observer’s eye away from any imperfections in the glass geometry. “The tight-tolerance frames are installed just like a regular unitized curtain-wall unit, so you still get those economic efficiencies,” Simmons explains.
But perhaps even more impressive was the design team’s ability to deliver a prefabricated unitized curved glass facade without mullions, which is really unprecedented.
As part of the project process, Front engineered the glass design on a prescriptive basis and took the specification to five glass fabricators globally, who then built accurate project specimens of the curved geometry, incorporating all fabrication details and tolerances. The preferred glass supplier was determined by owner, general contractor, and design team, and that company was assigned as the supplier to curtain wall contractors who were bidding the project.
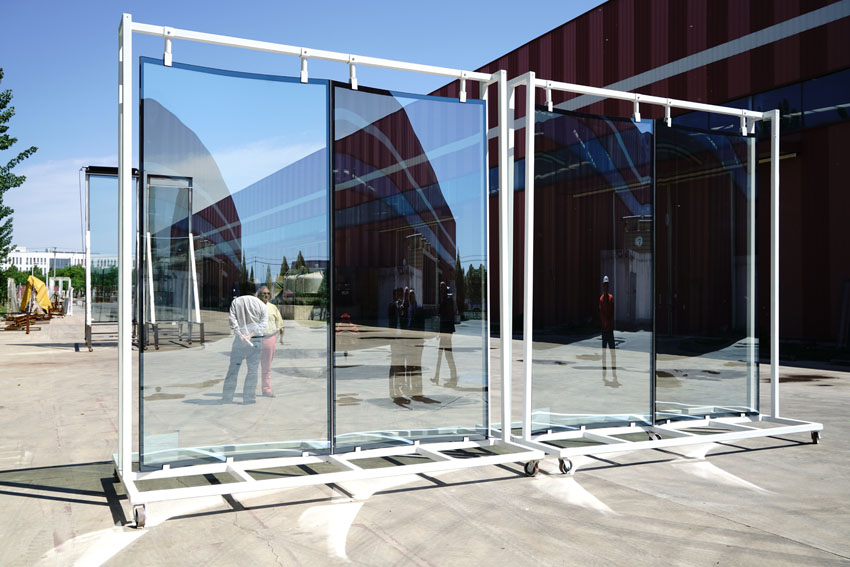
Photo courtesy REX/© Luxigon
This glass mockup for 2050 M Street demonstrates the design’s intention for transparency, crystalline reflectivity, and lack of distortion.
The curtain wall contractors took the glass supplier on board and offered a turnkey engineer and supply contract. Ultimately, the curtain-wall contractor was able to collaborate with a local installer with both contracts held separately under the general contractor.
“Once they knew how much the glass-supply aspect of the job would cost while securing the expected quality, there was greater confidence by the team that other aspects of the curtain-wall procurement could be delivered within budget,” relates Simmons.
Overall, Simmons explains that unlocking and having some control over the pricing of components is key to mitigating risk, but one really has to “get under the hood” in order to unlock that value.
Another interesting facade project in the Capital City is the new 140,000-square-foot International Spy Museum. Described as folded structural glass veil, suspended in front of the “black box” exhibition space, Eckersley O’Callaghan was challenged with delivering the complex facade design in a short time frame with a tight budget.
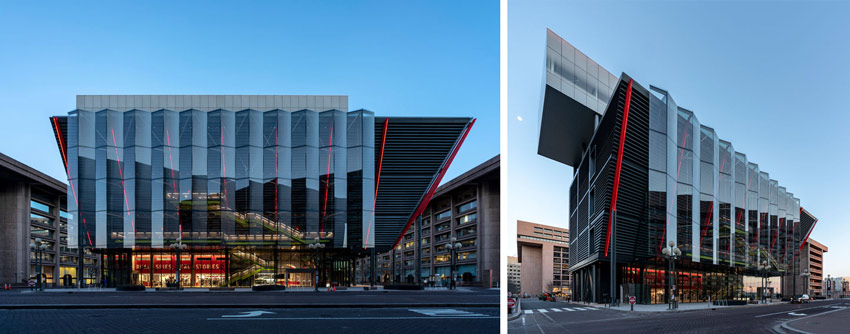
Photos courtesy of Eckersley O’Callaghan & Partners
The steel fabrication of the International Spy Museum’s exposed architectural elements required much craft and labor to achieve an exposed finish.
Regarding the latter, Uluaydin’s team rationalized the original curved glass design into 17-foot-high folded panels. A lightweight stainless-steel structure then stitched together the geometric folds, which ultimately delivered a thinner build-up of glass at a lower cost.
Adding even more complexity to the project was the fact that the facade is steel as opposed to aluminum. Whereas aluminum fabrication is an automated CNC process, the steel fabrication of exposed architectural elements required much more craft and labor to achieve an exposed finish.
Furthermore, the facade was designed with a tension-rod hanging system and was therefore very sensitive to movement during glass and framing installation caused by elongation of the rods due to weight, explains Uluaydin. And being that the rods were stainless steel, they were more prone to what is called thread galling (i.e., freezing up), thus not allowing field adjustments to the rods.
In order to address this head on, the facade contractor considered and designed the length of rods to maintain plan dimensions and make adjustments to the tension rods where necessary as they were installed. “The tolerances and connection points were all surveyed and monitored during the installation to maintain tolerances and appropriate clearances,” Uluaydin adds.
A little less than 10 miles north is SHoP’s 14-story mixed-use Midtown Center complex surrounding a large public plaza in Washington, D.C. A unique glass-and-copper facade was designed and built with 10 different unit types with varying angles of copper to create a gradient pattern. Unit depths range from 9 inches to 33 inches and are optimized at a typical 5-foot width for efficient office layout.
“The copper panels are clipped onto the facade with pre-attached formed stainless-steel pop rivets to allow for thermal expansion, concealed fasteners, and replacement if needed,” Kumar says.
In addition to aesthetics, the innovative facade design optimizes solar shading. As compared to an all-glass facade, the glass and copper design delivers a 6 percent peak reduction of overlit area, a 50 percent decrease in glare, and an 18 percent reduction of direct solar gains. “Because the sawtooth facade’s solid copper portion faces south, the lighting in the building is more indirect,” Kumar explains. “Furthermore, the copper portion of the facade acts not only as a louver but also a solid envelope with thermal insulating properties.”
One other recent innovative facade project of note is the San Francisco Museum of Modern Art, which involved the largest architectural application of fiber-reinforced polymer (FRP) in the United States.
Enclos worked closely with the design team early on to arrive at a tight pressure-equalized aluminum curtain wall that could also achieve the rippled surface with a rainscreen of FRP.
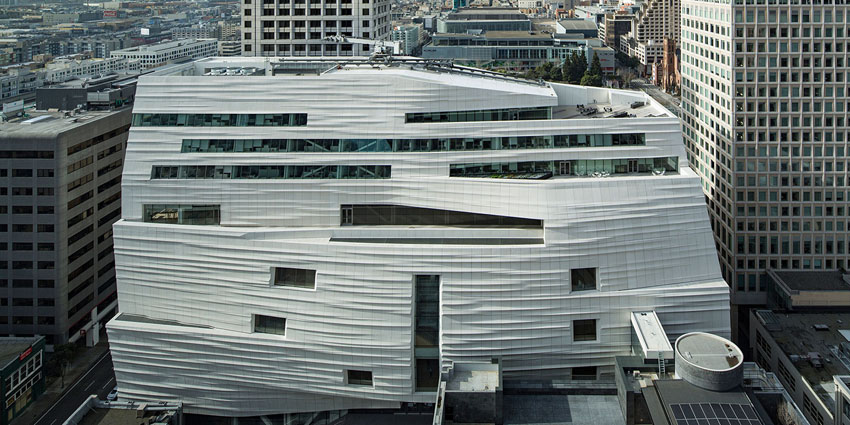
Photo courtesy of Enclos/© Henrick Kam
San Francisco Museum of Modern Art is the largest architectural application of fiber-reinforced polymer (FRP) in the United States. Working closely with the design team, a tight pressure-equalized aluminum curtain wall was installed to achieve the rippled surface with a rainscreen of FRP.
“The CNC capabilities of Kreysler Associates—a composite materials in construction expert—their efforts in getting fire-testing approvals, and proximity to both Enclos’ assembly shop and the project site made this a unique opportunity with many local synergies,” Vaglio says.
“The FRP panels were shipped 10 miles to be attached to the insulated curtain wall frames and sent another 30 miles to site,” he continues. “The result is a facade of 700-plus unique panels, approximately 5 feet by 4 inches by 26 feet tall. With early development of the contoured facade, including iterations of 3-D and parametric model exchanges amongst the design team, this is one of our proudest examples of a design-assist collaboration.”
BEST PRACTICES
Returning to the overall topic of mitigating risk down the supply chain, Patterson recommends keeping the chain as simple and local to the building site as possible.
As noted, some projects produce the curtain-wall system overseas, ship it to the United States for coating, send it back across the ocean for curtain-wall assembly, and then deliver it for a third time across the ocean, where it is then trucked cross-country for installation on a New York City skyscraper.
Not only does this this around-the-world-and-back-again transport significantly increase the risk of something failing, but the embodied carbon footprint is also off the charts.
“Economies of cost drove this decision, not considerations of risk or the economies of carbon emissions. This must and will change,” Patterson says.
Another critical consideration is site logistics, particularly in dense urban areas with no storage and the absolute minimum in the way of staging area. In these cases, prefabricated curtain-wall units have to arrive at the site just in time to be lifted from the transport vehicle and set on the building, he explains. Alternatively, racks of units must be carefully positioned within the building for access by installation crews.
With facade installation often running 25 percent or more of the total system cost, facade contractors must be strategic in the way they manage this.
Offering some overall advice, Vaglio emphasizes the importance of being open minded to new materials, sources, and solutions, and where appropriate, vetting new supply chain partners, establishing project expectations, and building trust.
Another important point is not hesitating to turn down a project. “We would rather let a customer know upfront that the project is not a good fit with our operational capacity than jeopardize our reputation by committing to a project we may not be able to perform at our highest level on,” he says.
As fabricators and contractors evaluate these opportunities, a number of key questions must be asked, including:
- Who will make the glass units?
- Can we verify the thickness?
- Can this be competitively bid?
- How will it be transported to site?
- How will it be installed?
- How does the cost compare to a traditional system?
“We get answers to each one of these questions to prove viability of the approach in terms of both possibility and budget constraints,” Kantzas says. “We follow a similar process for each facade component.”
Ultimately, supply-chain management comes down to trust. Of course, there are always extenuating circumstances that cannot be fully controlled. But by being honest about their capabilities, actively pooling their expertise, keeping the lines of communication open, and working together toward the same goal, building team members can greatly increase the odds of a successful curtain-wall project.