SBS-Modified Bitumen Membrane Composition
Now that we have covered a bit of the history of roofing and specifically SBS-modified bitumen, it is important to understand more about SBS membrane composition and what makes the material work well in roofing applications.
Why Modify Asphalt? (Bitumen)
SBS-modified bitumen is essentially asphalt that has been enhanced to provide better long-term performance as a protective roofing material. There are three main components involved in modifying asphalt for roofing usage: the asphalt itself, the SBS synthetic rubber modifier, and the filler used in the bitumen blend. First, let’s review asphalt and where it comes from.
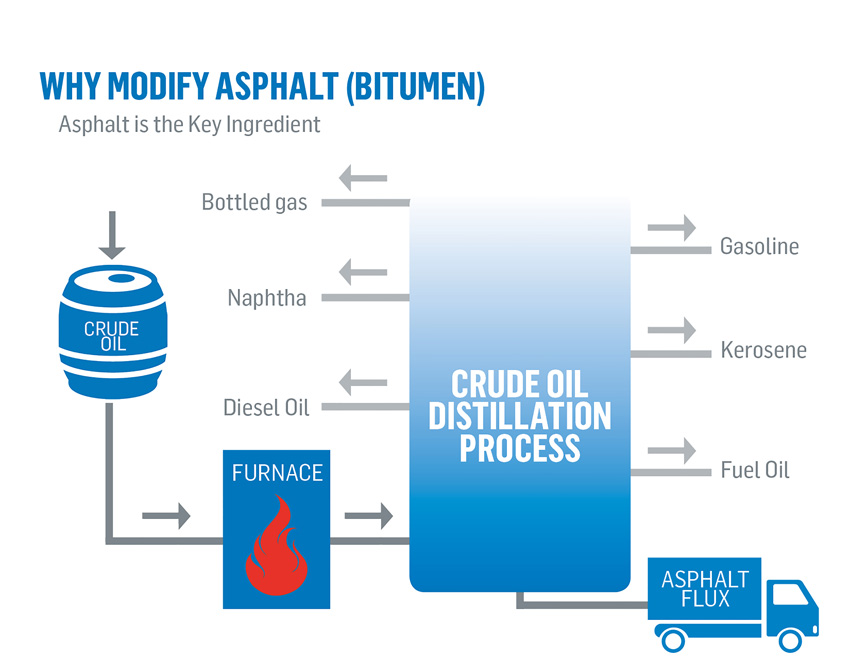
When crude oil is refined and distilled, there are a large number of byproducts that result. The one we are most interested in from a roofing perspective is asphalt flux.
During refining, crude oil is put through a process called fractionation where it is separated into its different components that serve a wide variety of practical purposes. One of these byproducts is asphalt flux, a thick bituminous material used in roofing construction. The resulting asphalt flux must then be modified for three main reasons:
- To increase its softening point.
- To lower its cold temperature flexibility.
- To increase its elongation/recovery properties.
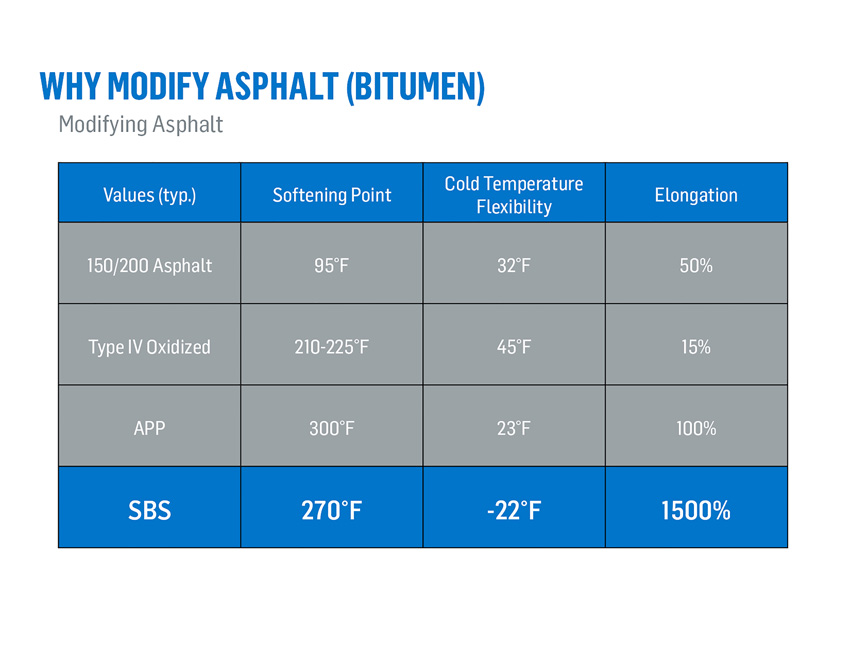
Here you can see the properties of various types of asphalt, both modified and unmodified, to give you a better understanding of how they perform in roofing applications.
As with any material, there are notable differences in the types of asphalt available.
- Penetration grade, or “pen grade” 150/200 asphalt is the base asphalt that has yet to be modified. As you can see in the chart above, it has a relatively low softening point and low-elongation properties.
- Type IV oxidized asphalt, commonly used in BUR roofing, has a much higher softening point, but the process of oxidation results in a less flexible asphalt with lower elongation properties.
- Due to its plastic nature (by addition of polypropylene) APP-modified asphalt has a higher softening point and flexibility at lower temperatures, though in temperatures below 23F (-5C) the material becomes brittle.
- With SBS-modified bitumen, the softening point is more than adequate for roofing purposes, and the cold temperature flexibility dips below -20F(-28C). The elongation and recovery (elasticity) properties of SBS-modified bitumen are far better than other bituminous materials, as the modified bitumen acts more like the SBS rubber modifier. As a result, SBS-modified bitumen is well suited to withstand climatic conditions around the world, and it can accommodate the movement of modern building and roof deck construction.
SBS-Modified Bitumen Performance
When you modify asphalt with the SBS copolymer, a number of benefits emerge, including:
- Higher elongation: This makes the membrane “more stretchy” and allows it to move with the natural expansion of the roof components.
- Increased elasticity: This gives the membrane the ability to move with the roof, i.e., expand and contract with the roof components.
- Excellent low-temperature flexibility: When oxidized asphalt gets cold, it gets brittle, and when you modify flux asphalt with SBS, it allows the asphalt to flex in cold weather without cracking or breaking.
- Enhanced high-temperature-resistance: The ability to stand up to elevated temperatures is also important due to the heat resistance needed because of modern insulation practices.
- More adhesive properties: SBS polymers are also used in many adhesive products, and when added to asphalt, they yield better adhesion properties for the asphalt.
- Better UV-resistance/improved durability: Properly formulated SBS-modified bitumen withstands heat and UV weathering better than oxidized asphalt, providing better durability.
Blending
When you modify bitumen with SBS, the bitumen begins to act more like rubber and less like bitumen. Through a process called phase inversion, the SBS polymer begins to swell and absorbs oils in the bitumen, giving it more rubber-like characteristics. This is all done at approximately 400F (204C) with very precise mixing times and speeds; too long in the mixing process or too much heat will begin to break down the compound.
The other components of the SBS bitumen blend are the fillers. The filler type and quantity can vary from blend to blend, but any fillers used in SBS-bitumen blends must be compatible and inert. These fillers must not have any adverse chemical effects in the bitumen blend.
Fillers can serve many functions, such as stabilizing the SBS blend (by absorbing excess oils that do not react with the SBS polymer) or increasing the fire-resistance of the SBS sheet. If filler is used as a fire retardant, the amount added to the blend must be considered. Too much filler begins to reduce the elastic properties of the material. High-quality SBS materials will incorporate some filler in conjunction with a chemical fire retardant to keep the filler percentage below deleterious levels.
If you take away only one thing from this section, remember this: as with any product, no two manufacturers create the same blend of SBS-modified bitumen. There are many different factors that go into developing a blend—from the asphalt sourcing and the type of SBS polymer to the quantities of fillers and the blending time and temperature. As a result, it is important to not only choose your materials carefully, but your suppliers as well.
Reinforcement
Now that you have a grasp on the formulation behind SBS-modified bitumen products, it’s also important to understand the membrane construction and application of the product, starting with reinforcement of SBS-modified products.
There are many variations to consider for reinforcing SBS-modified products, including fiberglass, polyester and virtually any combination of the two. One of the most important properties for roof membranes is dimensional stability—the reinforcement’s resistance to expanding or shrinking due to moisture, temperature or physical forces. Roof membranes should always be stable to provide maximum protection.
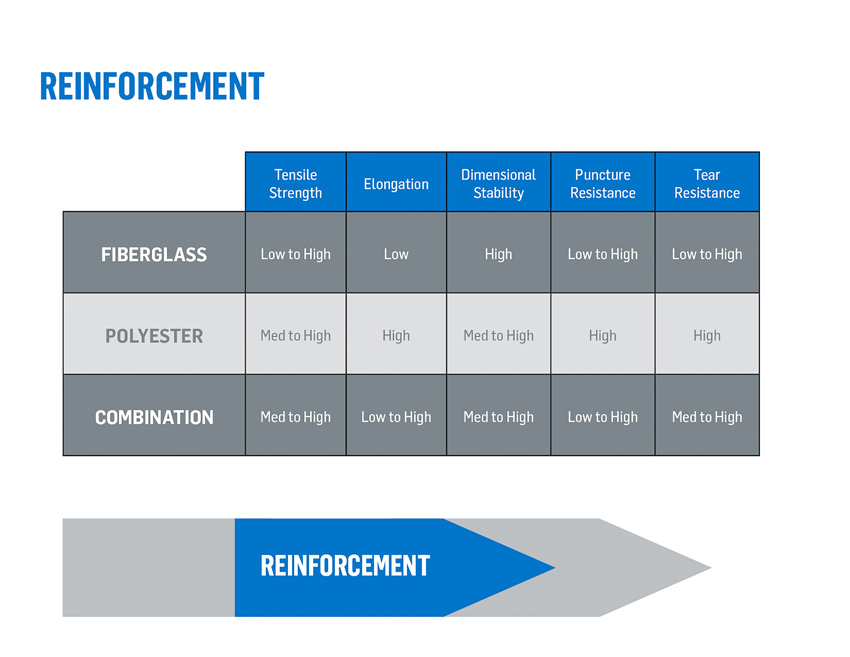
This chart shows the properties of various reinforcement materials. The right choice will depend largely on the needs of your application.
Reinforcement is important, but not the most important component in a roofing system—that accolade is reserved for the portion of the membrane that protects the roof from water and other elemental forces: the bitumen blend. One can use the highest tensile strength reinforcement in the industry, but if it is used with a substandard SBS-bitumen blend, over time the roof membrane will leak just the same as a low tensile strength material. Unlike traditional BUR constructed with oxidized asphalt and felts, the tensile strength required for SBS-modified bitumen membranes is a secondary factor.
Surfacing
The purpose of the roof membrane’s surface is protection and aesthetics. SBS-modified bitumen “base” plies are typically surfaced with silica (sand) or other minerals, polyolefin burnoff film, or release film in the case of self-adhesive materials. So-called “cap sheets” may utilize various surfacing options.
- Ceramic coated granules come in a variety of colors and are available with high Solar Reflectance Index (SRI) ratings.
- Ceramic coated granules can be designed to be environmentally friendly by reducing airborne nitrogen oxides (NOx) emission in the atmosphere.
- Uncoated mineral granules are also available that meet the most demanding SRI requirements for cool roofs.
- Metal-clad sheets were the original way to protect high-performance bituminous sheet materials, and are very effective at reflecting UV and heat energy, making metal foil especially compelling in high-slope or flashing applications.