This CE Center article is no longer eligible for receiving credits.
Designing exterior walls in buildings is a complex process. Beyond the structural system that may be either independent from or integral to the wall system, multiple other criteria must be met. The International Building Code (IBC) requires that the wall include a water-resistant barrier (WRB) in the interest of durability and integrity of the wall. It also indicates the conditions where fire resistance is or is not required in exterior walls according to different aspects of life safety. The International Energy Conservation Code (IECC) requires an air barrier to reduce air infiltration as a mandatory provision. It also requires insulation in the wall with a prescriptive requirement for continuous insulation (ci) outside of the structure in many climate zones in order to address the issue of thermal bridging. There are also project design criteria for general appearance, budget, and reduced maintenance that may impact not only the cladding or outermost surface of the wall but the rest of the assembly too. Altogether, the various materials and products designed and specified into an exterior wall must be able to be constructed as a complete, integrated wall assembly that is functional, code compliant, durable, cost-effective, and meets the design intent of the building.
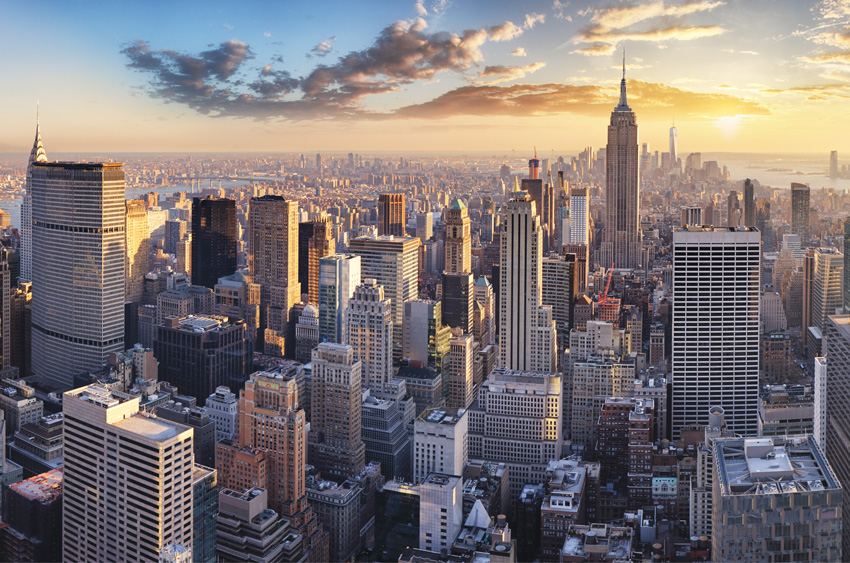
Photo courtesy of iStock.com/TomasSereda
Exterior walls can take many forms, but building codes require that they all meet minimum requirements for fire safety either by using noncombustible materials or by demonstrating safety through specific testing.
In light of all of the above, this course will look specifically at ways to solve one of the biggest challenges in many exterior wall designs, namely designing and demonstrating life safety performance during a fire. We will begin with a look at what the building codes require as well as one of the most cited, but often misunderstood, standards referred to in the code, namely NFPA 285. With an understanding of each of these, we will then look at several design approach options to create exterior walls that are safe, fire resistant, and readily able to be constructed.
IBC Requirements
The IBC is widely adopted across the United States by most authorities having jurisdiction (AHJ) as the basis for health, safety, and welfare in buildings. Other than one- or two-family homes and townhouses (which are covered by the International Residential Code), all other new construction or significant renovation of existing buildings need to comply with the relevant provisions of the IBC wherever it is adopted and in place. While there are different versions issued every three years (2012, 2015, and 2018 versions are currently in use around the country), there are some basic things that haven’t changed significantly, if at all, including the following.
Types of Construction
The IBC identifies five fundamental ways to characterize construction as a basis to subsequently refer to specific code requirements applicable (or not) to each type. Chapter 6 of the IBC identifies these five types (using Roman numerals) by listing specific “building elements,” such as primary structural frames, bearing and nonbearing exterior and interior walls, floor systems, and roof construction. In order to qualify as Type I or Type II construction, all of these primarily structural building elements listed in the code “are of noncombustible materials” except in a few cases where some specific exceptions may apply.
Moving on to Type III construction, the code defines this as “that type of construction in which the exterior walls are of noncombustible materials and the interior building elements are of any material permitted by this code.” There is a provision that allows for fire-retardant wood framing and sheathing here if certain criteria are met, but otherwise, combustible materials generally are not allowed on the exterior walls but are allowed on interior assemblies within the parameters of other sections of the code. Type IV construction is similar in that it also requires “the exterior walls are of noncombustible materials” but goes on to indicate more specifically that “the interior building elements are of solid wood, laminated wood, heavy timber (HT), or structural composite lumber (SCL) without concealed spaces.” Finally, Type V construction is “that type of construction in which the structural elements, exterior walls, and interior walls are of any materials permitted by this code.” This type typically means acceptable wood-framed construction that is not Type IV and does not have the same noncombustibility requirements for building elements.
It is significant to note for our purposes that Types I, II, III, and IV all require noncombustible exterior walls as part of their basic description. The clear intent, in the interest of life safety, is to limit the spread of fire whether one originates inside a building or somewhere outside. This the fundamental approach of fire safety in the code: contain a fire if it breaks out through various means, including the use of materials that don’t burn and contribute to growth of the fire. Nonetheless, there are some specific exceptions and variations for different types of exterior walls, and some of those exceptions can be different between different versions (years) of the IBC so it is always a good idea to check the prevailing code for a particular building location. Even so, the noncombustible requirement remains a key point for exterior walls.
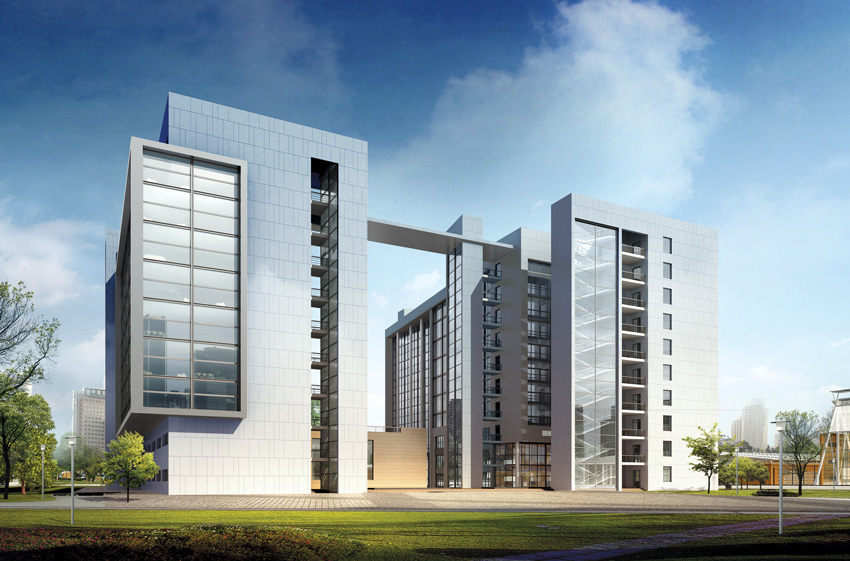
Photo courtesy of han871111/Shutterstock.com
Exterior walls are among the building elements that the International Building Code uses to define and classify different construction types.
Exterior Wall Requirements
In addition to the construction-type descriptions, there are other places in the code that bring additional requirements for exterior walls. For clarity, the code does define exterior walls in Chapter 2 as “a wall, bearing or nonbearing, that is used as an enclosing wall for a building, other than a fire wall, and that has a slope of 60 degrees or greater with the horizontal plane.” This comprehensive definition is the basis for Chapter 14 of the IBC, which is devoted entirely to multiple aspects of such exterior walls.
Beginning with Section 1402: Performance Requirements, the IBC identifies specific criteria for weather protection, including the need for a water-resistive barrier (WRB) behind the cladding or outermost surface. It also lists requirements for structure, fire resistance, flame propagation, and flood resistance. Since some of these things are interrelated, most notably in flame propagation that is directly influenced by the materials used in an exterior wall, it provides a specific clarification. Section 1402.5 indicates that “exterior walls on buildings of Type I, II, III, or IV construction that are greater than 40 feet in height above grade plane and contain a combustible water-resistive barrier shall be tested in accordance with and comply with the acceptance criteria of NFPA 285.”
More simply put, if the required water-resistive barrier is a combustible product (i.e., a plastic or composite membrane or similar) over a stated threshold and it is being used in a wall that is required to be noncombustible (Type I–IV), then there is a standard test required known as NFPA 285. We will delve deeper into that test later in this course, but for now, suffice to say that it is a nationally recognized and IBC-adopted test of the National Fire Protection Association (NFPA) that has been developed to determine the fire safety of entire exterior wall assemblies, not just individual products. Its purpose is to determine whether or not a combustible element is permissible (i.e., safe) for use in an exterior wall based on subjecting a test wall to direct flames and recording the results. There are a few exceptions to requiring this test, mostly involving masonry and concrete construction or low fire risk when the only combustible item in the wall is the water-resistive barrier.
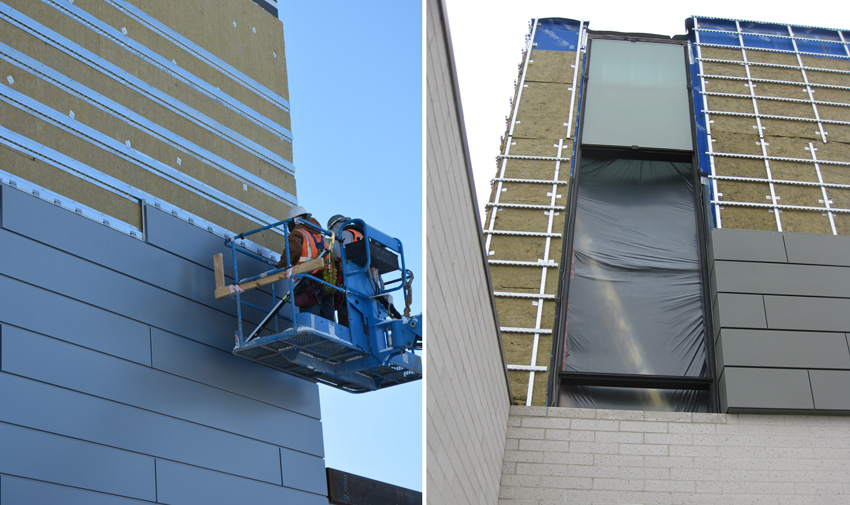
Photos courtesy of ROCKWOOL™
The International Building Code (IBC) addresses safety in buildings with many specific provisions directly applicable to exterior walls.
Chapter 14 continues to address other aspects of exterior walls, including criteria for wall materials, interior wall coverings, vapor retarders, veneers, and the use of combustible materials on the exterior side of exterior walls. For this last item, those combustible materials must be limited in size, location, type, or comply with other provisions of the code in order to be allowed in Type I–IV construction. There are some specific sections on particular cladding choices, such as metal composite material (MCM) panels, exterior insulation finish systems (EIFS), high-pressure decorative laminates (HPL), and plastic composite decking. In the case of MCM and HPL, there are conditions that can again require that the wall assembly be tested according to NFPA 285 similar to the water-resistive barrier testing requirement.
Designing exterior walls in buildings is a complex process. Beyond the structural system that may be either independent from or integral to the wall system, multiple other criteria must be met. The International Building Code (IBC) requires that the wall include a water-resistant barrier (WRB) in the interest of durability and integrity of the wall. It also indicates the conditions where fire resistance is or is not required in exterior walls according to different aspects of life safety. The International Energy Conservation Code (IECC) requires an air barrier to reduce air infiltration as a mandatory provision. It also requires insulation in the wall with a prescriptive requirement for continuous insulation (ci) outside of the structure in many climate zones in order to address the issue of thermal bridging. There are also project design criteria for general appearance, budget, and reduced maintenance that may impact not only the cladding or outermost surface of the wall but the rest of the assembly too. Altogether, the various materials and products designed and specified into an exterior wall must be able to be constructed as a complete, integrated wall assembly that is functional, code compliant, durable, cost-effective, and meets the design intent of the building.
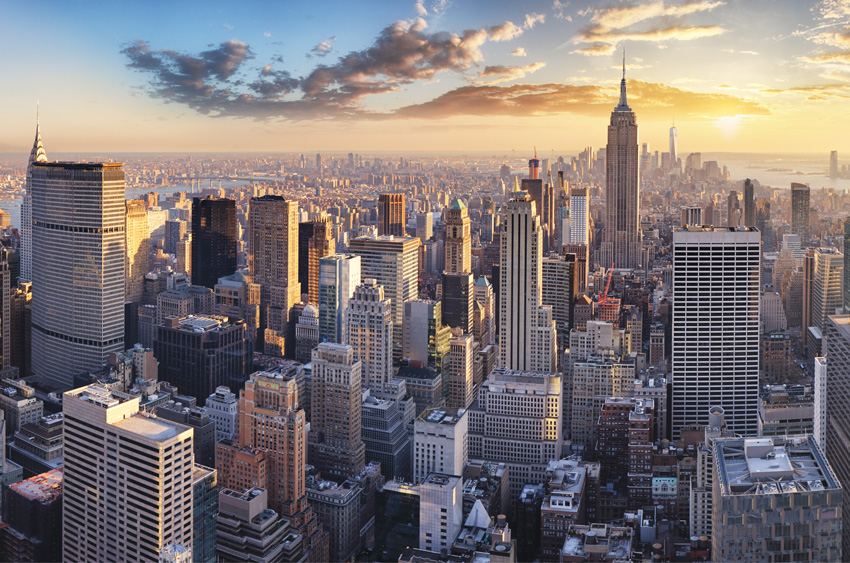
Photo courtesy of iStock.com/TomasSereda
Exterior walls can take many forms, but building codes require that they all meet minimum requirements for fire safety either by using noncombustible materials or by demonstrating safety through specific testing.
In light of all of the above, this course will look specifically at ways to solve one of the biggest challenges in many exterior wall designs, namely designing and demonstrating life safety performance during a fire. We will begin with a look at what the building codes require as well as one of the most cited, but often misunderstood, standards referred to in the code, namely NFPA 285. With an understanding of each of these, we will then look at several design approach options to create exterior walls that are safe, fire resistant, and readily able to be constructed.
IBC Requirements
The IBC is widely adopted across the United States by most authorities having jurisdiction (AHJ) as the basis for health, safety, and welfare in buildings. Other than one- or two-family homes and townhouses (which are covered by the International Residential Code), all other new construction or significant renovation of existing buildings need to comply with the relevant provisions of the IBC wherever it is adopted and in place. While there are different versions issued every three years (2012, 2015, and 2018 versions are currently in use around the country), there are some basic things that haven’t changed significantly, if at all, including the following.
Types of Construction
The IBC identifies five fundamental ways to characterize construction as a basis to subsequently refer to specific code requirements applicable (or not) to each type. Chapter 6 of the IBC identifies these five types (using Roman numerals) by listing specific “building elements,” such as primary structural frames, bearing and nonbearing exterior and interior walls, floor systems, and roof construction. In order to qualify as Type I or Type II construction, all of these primarily structural building elements listed in the code “are of noncombustible materials” except in a few cases where some specific exceptions may apply.
Moving on to Type III construction, the code defines this as “that type of construction in which the exterior walls are of noncombustible materials and the interior building elements are of any material permitted by this code.” There is a provision that allows for fire-retardant wood framing and sheathing here if certain criteria are met, but otherwise, combustible materials generally are not allowed on the exterior walls but are allowed on interior assemblies within the parameters of other sections of the code. Type IV construction is similar in that it also requires “the exterior walls are of noncombustible materials” but goes on to indicate more specifically that “the interior building elements are of solid wood, laminated wood, heavy timber (HT), or structural composite lumber (SCL) without concealed spaces.” Finally, Type V construction is “that type of construction in which the structural elements, exterior walls, and interior walls are of any materials permitted by this code.” This type typically means acceptable wood-framed construction that is not Type IV and does not have the same noncombustibility requirements for building elements.
It is significant to note for our purposes that Types I, II, III, and IV all require noncombustible exterior walls as part of their basic description. The clear intent, in the interest of life safety, is to limit the spread of fire whether one originates inside a building or somewhere outside. This the fundamental approach of fire safety in the code: contain a fire if it breaks out through various means, including the use of materials that don’t burn and contribute to growth of the fire. Nonetheless, there are some specific exceptions and variations for different types of exterior walls, and some of those exceptions can be different between different versions (years) of the IBC so it is always a good idea to check the prevailing code for a particular building location. Even so, the noncombustible requirement remains a key point for exterior walls.
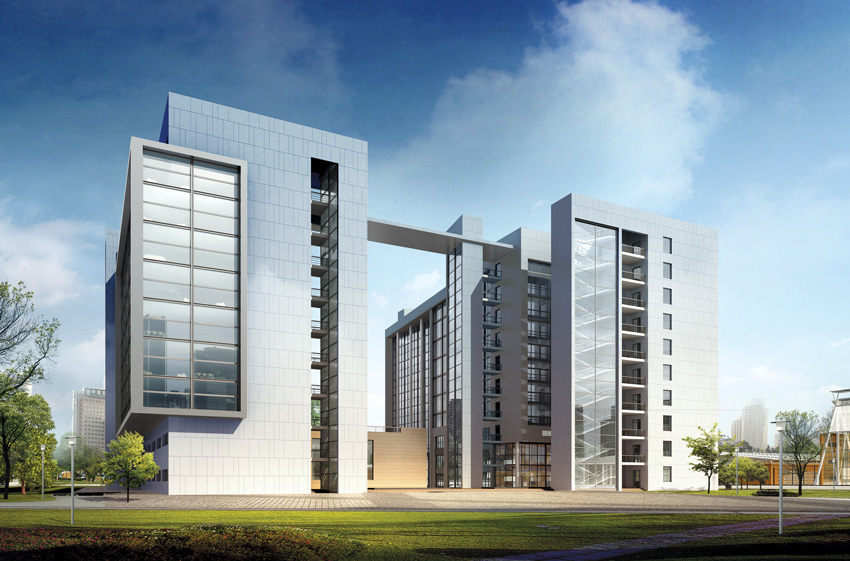
Photo courtesy of han871111/Shutterstock.com
Exterior walls are among the building elements that the International Building Code uses to define and classify different construction types.
Exterior Wall Requirements
In addition to the construction-type descriptions, there are other places in the code that bring additional requirements for exterior walls. For clarity, the code does define exterior walls in Chapter 2 as “a wall, bearing or nonbearing, that is used as an enclosing wall for a building, other than a fire wall, and that has a slope of 60 degrees or greater with the horizontal plane.” This comprehensive definition is the basis for Chapter 14 of the IBC, which is devoted entirely to multiple aspects of such exterior walls.
Beginning with Section 1402: Performance Requirements, the IBC identifies specific criteria for weather protection, including the need for a water-resistive barrier (WRB) behind the cladding or outermost surface. It also lists requirements for structure, fire resistance, flame propagation, and flood resistance. Since some of these things are interrelated, most notably in flame propagation that is directly influenced by the materials used in an exterior wall, it provides a specific clarification. Section 1402.5 indicates that “exterior walls on buildings of Type I, II, III, or IV construction that are greater than 40 feet in height above grade plane and contain a combustible water-resistive barrier shall be tested in accordance with and comply with the acceptance criteria of NFPA 285.”
More simply put, if the required water-resistive barrier is a combustible product (i.e., a plastic or composite membrane or similar) over a stated threshold and it is being used in a wall that is required to be noncombustible (Type I–IV), then there is a standard test required known as NFPA 285. We will delve deeper into that test later in this course, but for now, suffice to say that it is a nationally recognized and IBC-adopted test of the National Fire Protection Association (NFPA) that has been developed to determine the fire safety of entire exterior wall assemblies, not just individual products. Its purpose is to determine whether or not a combustible element is permissible (i.e., safe) for use in an exterior wall based on subjecting a test wall to direct flames and recording the results. There are a few exceptions to requiring this test, mostly involving masonry and concrete construction or low fire risk when the only combustible item in the wall is the water-resistive barrier.
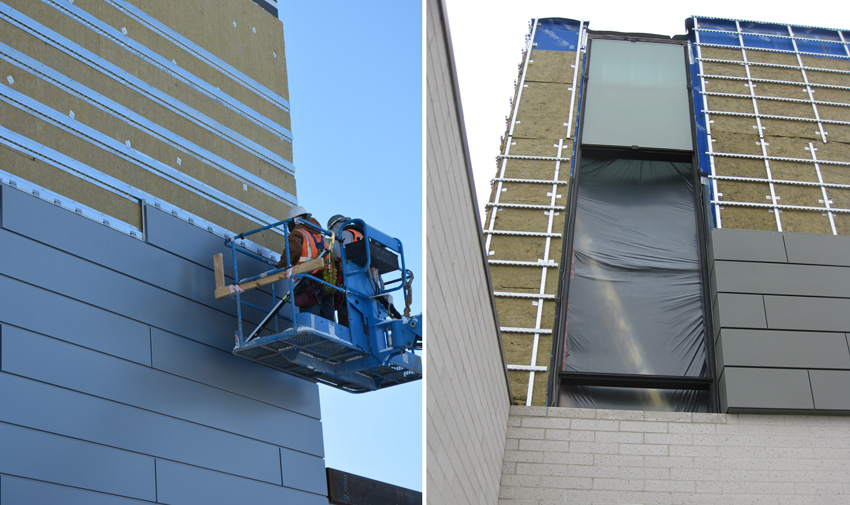
Photos courtesy of ROCKWOOL™
The International Building Code (IBC) addresses safety in buildings with many specific provisions directly applicable to exterior walls.
Chapter 14 continues to address other aspects of exterior walls, including criteria for wall materials, interior wall coverings, vapor retarders, veneers, and the use of combustible materials on the exterior side of exterior walls. For this last item, those combustible materials must be limited in size, location, type, or comply with other provisions of the code in order to be allowed in Type I–IV construction. There are some specific sections on particular cladding choices, such as metal composite material (MCM) panels, exterior insulation finish systems (EIFS), high-pressure decorative laminates (HPL), and plastic composite decking. In the case of MCM and HPL, there are conditions that can again require that the wall assembly be tested according to NFPA 285 similar to the water-resistive barrier testing requirement.
Energy-Efficiency Requirements
Chapter 13 of the IBC indicates that all buildings “shall be designed and constructed in accordance with the International Energy Conservation Code.” Therefore, all of the provisions of the IECC come into play. The intent of the IECC is to “regulate the design and construction of buildings for the effective use and conservation of energy.” Note that it doesn’t regulate energy; rather, it directly regulates design and construction with some very particular requirements for exterior walls and other parts of the building enclosure in the interest of energy conservation. Those requirements vary a bit for commercial (i.e., nonresidential) buildings based on defined climate zones (numbered 1 through 8 and ranked warmest to coldest) where the building is located. Nonetheless, the two biggest requirements are for air sealing to prevent energy losses due to unwanted air infiltration and insulation to prevent heat transfer through the exterior walls beyond established levels.

Photo courtesy of iStock.com/AntonioGuillem
In addition to energy conservation, buildings that address air infiltration and proper insulation levels are more comfortable to be in.
Air sealing of buildings has received notable attention in the recent updates of the IECC. This comes from the recognition that unwanted drafts can reduce energy performance as much as, if not more than, unwanted heat loss (or gain) due to low levels of insulation. Hence there are a series of mandatory (i.e., no options except to comply) requirements for air sealing in buildings. Related to exterior walls, that includes providing an air barrier much the same as a water-resistive barrier. Indeed, some products are on the market that provide both types of barrier in a single product. That is convenient, but the specifier needs to be sure they in fact are tested and certified for both—otherwise a separate air-sealing barrier or strategy is needed. Either way, if the air barrier is noncombustible, then there should be no issue using it in an exterior wall in Type I–IV construction. If it is in fact combustible, then it falls into the same category as a combustible water-resistive barrier and will need to be tested as part of a wall assembly using the NFPA 285 standard.
Moving to insulation, the IECC has called for its use in exterior walls for some time. However recent updates to the IECC have called for more of it and in different configurations. Specifically, the latest versions include tables that establish minimum levels of insulation (based on stated R-values of the insulation) both in terms of conventional framing cavity insulation (i.e., insulation installed between metal or wood framing studs) and continuous insulation (i.e., insulation installed outside of the framing and other structural members). The move toward requiring continuous insulation has been in the interest of improving energy performance since the framing studs cause significant breaks in the insulation creating “thermal bridges” between the two sides of the wall. In metal-stud walls in particular, where the surface area of the studs in the wall is typically on the order of 20 percent or more, the effectiveness of the insulation can be reduced significantly. In fact, the IECC provides a set of correction factors that identify “effective R-values” that are a half to a third of the stated R-value of insulation by itself. The use of continuous insulation over the outside of the framing addresses this problem and can be used either as the complete insulation approach or in combination with insulation in the framing cavities.

Images courtesy of ROCKWOOL™
The IECC prescribes the use of continuous insulation outside of the framed portion of an exterior wall, while the IBC requires testing per NFPA 285 if foam plastic insulation is used. Some examples of wall assemblies that have been tested and passed by using noncombustible stone wool insulation are shown here.
Note that the IECC doesn’t dictate what products to use or prescribe specific exterior wall designs—that is the role of the design professional. It does provide the minimum R-value performance requirements that need to be incorporated into that design, however. Note too that there is a provision within the IECC that allows an alternative to show code compliance based on the overall building performance. In this case, some trade-offs may be allowed such that a reduction in wall insulation levels may be acceptable if it can be demonstrated that the building performance is made up in some other manner, such as increased insulation in the roof or foundation level. Proving that claim to a code official involves a computer analysis that can be done using free software from the United States Department of Energy known as ComCheck or by doing a full-blown computerized energy model. In any of these scenarios, however, some level of insulation will still be required in the exterior walls under the IECC.
Of course, there are many types of insulation available on the market with their own sets of characteristics, including R-value ratings per inch of thickness, material makeup, and most significantly for our purposes, combustibility. If the buildings where the insulation is being installed in the exterior walls are Types I–IV, then those walls still need to be of noncombustible construction. If the insulation used is verifiably noncombustible, whether used as continuous insulation or between the stud framing, then there is no issue. However, if the insulation is in fact combustible, particularly if it is made from combustible plastics in the form of commonly used rigid boards or spray foam, then there are some very specific concerns.
Use of Plastics
Building products made out of plastic have become widespread so the IBC has included a variety of provisions to address their safe use, primarily since most plastics are petroleum based and very combustible. Chapter 26 of the IBC is devoted entirely to plastic and provides standards addressing foam plastics, light-transmitting plastics, fiber-reinforced polymers, and wood-plastic composites. We will focus here on Section 2603, which addresses foam plastic insulation.
Because of the prevalence of foam plastic insulation and its ability to provide favorable insulation values using common construction practices, the IBC allows its use as long particular conditions are satisfied based on safety and fire concerns. So minimum requirements are set for surface-burning characteristics to limit common things like flame spread and smoke development based on the very-often-cited ASTM E 84 test for building materials. There is also a requirement that plastic insulation is separated from the interior of a building by a thermal barrier like a half-inch layer of gypsum board or equivalent approved material such as stone wool insulation. There are some exceptions to this requirement in certain circumstances, but the goal is to delay ignition of the foam plastic in case of fire and thus reduce the effects on people and property.
Section 2603.5 of the IBC specifically addresses combustible foam plastic insulation used in “exterior walls of buildings of any height” in Type I–IV construction. The first thing to notice is that the 40-foot height threshold for combustible water-resistive barriers is gone once foam plastic insulation is used—it applies to buildings of all heights. This section then goes on to list some very specific requirements similar to the general ones for all plastics just described about the material and the way it is used. Most notable, however, are two conditions that trigger a requirement for independent testing of materials and even entire wall assemblies.
- Fire-resistance rating testing: The first testing requirement comes about if the exterior wall is required to carry a fire-resistance rating (i.e., 1 hour, 2 hour, etc.). In those cases, the code requires testing following two of the most common testing standards for fire resistance. The first, ASTM E119, was developed by the independent organization ASTM International. Test E119: Standard Test Methods for Fire Tests of Building Construction and Materials is likely familiar to anyone who has written specifications for any materials that need to show fire ratings, flame spread, or smoke developed requirements. This standard is “intended to evaluate the duration for which…building elements…contain a fire, retain their structural integrity, or exhibit both properties during a predetermined test exposure.” A very similar standard known as UL 263 has also been around for some time developed by Underwriters Laboratories (UL) who are the same people who test virtually everything electrical for fire safety. In this case, UL 263 is a Standard for Fire Tests of Building Construction and Materials. Since ASTM E119 and UL 263 are so similar, the code identifies and accepts either test as evidence of performance.
In order to carry out either test, an independent laboratory is engaged (i.e., hired and paid) to follow the stated test procedure and objectively report on the results. Essentially, the independent lab receives a material or a wall assembly (submitted by product manufacturers, construction professionals, or others) and exposes it to fire in a controlled test chamber. Following the testing protocols, the effects of the fire on the test specimen are then measured and documented. If the results fall within the limits prescribed by the code, then the associated rating can be applied and the assembly used where needed in buildings. If the testing results show a rating below what is required by code, then the assembly is not approved for use.
In the case of plastic insulation, the code basically says if a fire-rated exterior wall is required, it must demonstrate successful test results based on a tested wall assembly (not just the individual materials) that includes that plastic insulation. This is important because otherwise the fire-rated wall would be found acceptable simply by virtue of using a mix of standard noncombustible materials that have each already been tested independently. Hence, the addition of combustible plastic insulation must not change the fire rating of the wall. In some cases, a standard assembly that has already been tested and documented per the ASTM or UL standards could be used if that matches the design intent of the building. Either way, it is the use of the combustible plastic insulation that triggers the need for a constructed sample of the entire wall assembly to be tested and show that it still meets the fire-resistance rating where that is required.
- Fire-propagation testing: There is also a second requirement for testing when foam plastic insulation is used in exterior walls, still regardless of building height in Type I–IV construction. This second requirement applies whether the exterior wall is fire rated or not—in other words, to all exterior walls. It is based on a concern for fire spreading through the exterior wall construction itself, both vertically and horizontally. Unfortunately, there have been some well-publicized and very dramatic instances of tall buildings that did not address this issue and lives were lost when a fire broke out. In most of these cases, a fire starts in one area of one floor in a building and makes its way into the exterior wall construction, either by burning through the interior wall covering, extending outside through a broken window, and burning through the exterior side. Foam plastic continuous insulation in the exterior wall can thus catch on fire and spread quickly up the building vertically and then outward horizontally to the point that the entire building is engulfed in flames. This has caused loss of life and severe building damage as a result.

Photo courtesy of ROCKWOOL™
Exterior walls that are not designed and constructed according to IBC code requirements or tested in accordance with NFPA 285 can create serious consequences in a fire.
Recognizing the severe risk to life safety from this exterior wall condition, the very short but important foam plastic insulation Section 2603.5.5 of the IBC addresses Vertical and Lateral Fire Propagation. In a single sentence, it simply states, “The exterior wall assembly shall be tested in accordance with and comply with the acceptance criteria of NFPA 285.” Keep in mind that this requirement only comes into play if foam plastic insulation is part of the exterior wall, but note that this is a requirement for the entire wall assembly and not just the individual products used. Further, there are only two exceptions to this requirement. The first one applies if the building is only one story tall. In that case, the plastic foam must meet maximum flame and smoke requirements, be no more than 4 inches thick, be covered by an acceptable metal cladding, and the building must have an automatic fire-sprinkler system. The second exception applies if the plastic insulation is covered on each face (interior and exterior) with not less than 1 inch of concrete or masonry with no air space or up to 1 inch air space if the plastic meets certain criteria.
What does all of this mean for the design of exterior walls with foam plastic insulation? It means that unless the building meets one of the two exceptions noted, the entire wall assembly needs to be tested according the NFPA 285. Let’s take a closer look at what having that test done means.
The NFPA 285 Standard
As noted, the NFPA has developed NFPA 285: Standard Fire Test Method for Evaluation of Fire Propagation Characteristics of Exterior Non-Load-Bearing Wall Assemblies Containing Combustible Components. It is easy to see why it is referenced by the IBC since it is directly relevant to the use of combustible items in exterior walls as we have reviewed. Here are the details:
- What it is: NFPA 285 is a standardized fire test that provides a method of determining the flammability characteristics of exterior, non-load-bearing wall assemblies/panels. As summarized, it “is intended to evaluate the inclusion of combustible components within wall assemblies/panels of buildings that are required to be of noncombustible construction. It is intended to simulate the tested wall assemblies’ fire performance.”
- How it was developed: Model building codes in the 1980s and 1990s sought a means to determine fire safety in exterior walls that were required to be noncombustible but where combustible components might be required for other reasons (e.g., insulation). Accordingly, NFPA technical committees took on the task of developing a consensus-based testing standard for this purpose. The first version of NFPA 285 was released in 1998 with subsequent updates in 2006 and 2012. The updates included editorial and technical changes to clarify the intent and purpose of the standard as well as update the testing procedures, test equipment, and acceptance criteria.
- What it tests for: As stated in Section 1.1 of the standard, it’s scope is to provide “a test method for determining the fire-propagation characteristics of exterior non-load-bearing wall assemblies and panels used as components of curtain wall assemblies that are constructed using combustible materials or that incorporate combustible components and that are intended to be installed on buildings required to have exterior walls of noncombustible construction.” The focus is on fire propagation, meaning the spread of fire that the IBC is concerned about. It is also specifically applicable to the most common condition of exterior walls that are separate from the building structure (i.e., the walls are not carrying the building structural load) or the use of curtain wall panels that are attached to a separate structural system.
- What is needed for the test: An independent testing laboratory is responsible for providing the proper setting and conditions for the test to occur. Accordingly, it follows Chapter 4 of the standard that describes in great detail the dimensions, construction, and makeup for air requirements of the test facility (i.e., the building where the test is done) and similar requirement for the test apparatus (i.e., the default two story structure that an exterior wall assembly is to be placed upon and tested). There are similar detailed descriptions for natural-gas fired burners that need to be installed in specific locations to simulate a fire both inside and outside of the test apparatus. Next, the party that is requesting the test (i.e., construction professionals, product manufacturers, others) needs to provide a test specimen that complies with the detailed provisions of Chapter 5 of the standard. The test specimen must be at least 17.5 feet high and 13.3 feet wide, include a window, and be mounted or constructed onto the test apparatus all in strict accordance with all of the details of Chapter 5. As has been noted already, this test specimen must be of the entire wall assembly as designed and intended to be constructed in a building, not just individual products or materials. That means it includes everything such as framing or curtain wall panel systems, sheathing, air- and water-resistive barriers, cavity and/or continuous insulation, exterior cladding and any related support systems, windows with flashings, caulking and sealants, and the interior wall surface.
- How the test is conducted: The independent testing laboratory must follow specific protocols for instrumentation related to temperature measurements, gas flow meters, and thermocouples. It must also follow a multifaceted calibration procedure to help assure accuracy of results. Once everything is in place and verified (including even the ambient temperature in the facility), the actual test is conducted in several stages. First, the gas supply to the test room burner is turned on and ignited. After 5 minutes, a second burner at the window is turned on and ignited. After 30 minutes from when the test room burner was ignited, the gas supply to both burners is turned off. For at least 10 minutes after that, any residual burning of the test specimen needs to be allowed to continue unless it threatens safety within the facility. Throughout the entire test, video recording, data recording, and visual observations must be undertaken following specific instructions in Chapter 9 of the standard. Then the test specimen must be “dismantled and dissected to determine the extent and the depth of damage within the combustible components and the condition of the test specimen’s exterior wall panel facings.”
Video courtesy of ROCKWOOL™
Fire testing of a complete wall assembly takes place inside a testing facility with a test apparatus all in accordance with the criteria listed in NFPA 285.
- Conditions of acceptance: Among the data collected, the test is designed to identify two crucial items: what temperatures were reached in different places of the tested specimen and where the flames traveled. Generally speaking, the tested specimen must not heat above established temperatures (500–1,000 degrees above ambient temperature depending on specific location), and flames must not spread vertically into the second floor or horizontally past the side walls of the test apparatus.
- Report: Based on all of the above, the independent laboratory issues an objective and factual report following the format identified in Chapter 11 of the standard. If the report indicates that the tested wall assembly fell within the conditions of acceptance of the test, then the design and construction team can submit that to a code-enforcement official as evidence of meeting the NFPA 285 standard and complying with the IBC. In essence, the interpretation can be made that, even though there are combustible materials in a wall otherwise required to be noncombustible, the testing proves that this particular wall assembly prevents fire propagation and spreading similar to the way a noncombustible wall might. Therefore, there is no threat to public safety, and the tested wall can be allowed under the code. On the other hand, if the report indicates that the test specimen did not fall within the conditions of acceptance, then the wall assembly fails and cannot be accepted for use under the IBC. The party requesting the test can then redesign and reconstruct a new wall assembly/test specimen and engage the laboratory to conduct an additional test, repeating that process as needed until the conditions of acceptance are met.
The above summarily describes the NFPA 285 standard. The full text of the standard can be reviewed at
www.nfpa.org
Design Options
When designing exterior walls, it should now be clearer what the code requirements are regarding the use of combustible and noncombustible materials. It should also be clearer as to when wall assemblies need to be tested according to NFPA 285, what that test involves, and why. With all of this as the basis, the role of a design professional is to be sure that exterior walls are designed and specified to be either fully noncombustible or, if combustible foam insulation (and in certain cases if a combustible water-resistive barrier) is used, to assure that the entire wall assembly as designed has been properly and fully tested. Not doing so puts a project in jeopardy of not receiving a building permit from a local AHJ, thus causing time delays or potential liability. Recognizing all of this, there are several design strategies that can be considered as options.
Strategies Where NFPA 285 Testing Is Required
If the design decision is made that foam plastics or other relevant items are to be included in the exterior walls, then there are basically two options. The first, and probably least costly in terms of time and money is to select and use a standard assembly that has already been tested by someone else. Information and details about such tested assemblies, including the final test report, are sometimes obtainable from product manufacturers or others. The critical point in this option is that both the design, including the precise placement of vertical and horizontal cladding panel seams, and the construction must be identical to the tested conditions. That includes the specific materials and products used, even proprietary ones, if that was the basis of the test. If a designer wants to change anything, then a different tested assembly will need to be found that includes that change or an engineering judgement will need to be made to assess the change and its effect on the fire performance. Similarly, if a contractor wants to substitute a material or a product for something in a previously tested wall assembly, that can invalidate the use of that test as a basis for code compliance. Note too that if different exterior wall types are used on a building due to differing conditions (horizontally or vertically), each of those types will need to be matched with a previously tested wall assembly that is the same as each different wall type. Nonetheless, if everyone on the design and construction teams agree to match exactly the tested conditions, this is an option.
In cases where a previously tested (or listed) wall assembly is not available or appropriate, there are only a few other options. One would be to have a fire-protection engineer or testing laboratory assess the proposed assembly and provide an engineering judgement as to the anticipated fire-propagation performance based on testing done for similar assemblies. If that is not practical or possible, then the design and construction team always has the option of arranging for, submitting, and paying for an independent laboratory to conduct the test using NFPA 285. That will require some extra time and expense, obviously, and may or may not be justified or acceptable to the project owner. On large projects with only a few wall types, it may be worth considering, but on smaller projects or projects with many different wall types, it will likely become cost-prohibitive quickly—particularly if the tested assemblies don’t meet the acceptance criteria the first or even subsequent times.

Image courtesy of ROCKWOOL™
A typical decision tree is shown here to summarize when testing per NFPA 285 is called for in the IBC or not.
Strategies That Avoid NFPA 285 Testing
As noted earlier in our discussion, there are conditions that do not trigger the code requirement for testing per NFPA 285. The first are the exceptions noted, such as designing a single-story building that includes an automatic fire-sprinkler system and meets other criteria. The other is to provide concrete or masonry on either side of plastic foam insulation, essentially encasing the combustible insulation in noncombustible materials. Alternatively, if the building is small enough and all other related code conditions can be met, it could be designed and built using Type V construction. However, with no specific provisions for the fire protection of the facade in Type V construction, there are legitimate concerns for fire safety, particularly if combustible foam plastic insulation is used. While these three code-acceptable options are possible, they may not necessarily match the owner needs, design criteria, or cost budget for the project.
A preferred strategy that allows for the greatest flexibility in design and construction is to use all noncombustible materials in the exterior wall in the first place, particularly the insulation. Without the presence of foam plastic insulation and a combustible water-resistive barrier, the IBC no longer requires the exterior wall to be tested since there is no threat of fire propagation in the wall assembly. This approach would allow common wall assemblies of noncombustible materials, such as metal framing, gypsum sheathing, metal cladding, or curtain wall panels, to first be selected based on standard preferences and project conditions. The addition of noncombustible insulation could then be incorporated in the manner that best suits the project. By using all noncombustible materials, the requirements for Type I–IV construction are satisfied and testing is no longer an issue.
What type of insulation is noncombustible? Those made of noncombustible base materials. Perhaps the best example of that is stone wool insulation. This is a type of insulation that has been around for more than 80 years and has been used in a variety of residential, commercial, and industrial applications. Stone wool insulation does not use any foam plastics, flame retardants, or blowing agents. Rather, it is manufactured out of volcanic basalt rock mixed with some recycled slag in a furnace. The melted rock is then literally spun into wool with minor amounts of binder to create the desired density of the end product as either rigid board, semi-rigid board, or batt-type insulation. That means it can be used in framing cavities in batt form and as continuous insulation in the semi-rigid or rigid board form. The stone wool fibers are typically nondirectional, which is important for achieving the multiple performance characteristics of the final product. In terms of R-value, stone wool provides very good results (R-4 or better per inch), but most notably, that performance has been shown to remain constant over time. Since there are no blowing agents, there is nothing to off-gas, meaning that the thermal resistance does not change. It also has superior qualities in regard to dimensional stability, sound attenuation, water repellency, and vapor permeance.
Because of its makeup, stone wool insulation excels in terms of meeting code requirements for noncombustible insulation. It will not develop toxic smoke or promote flame spread, even when directly exposed to fire, as most other insulation materials do. When tested in accordance with ASTM E84, stone wool typically shows a flame spread of 0 and a smoke development of 0. By comparison, spray polyurethane foam (SPUF) tested to ASTM E84 typically achieves a flame spread of 25 and smoke developed in the 350 to 500 range.
Beyond these basic fire-resistance properties, stone wool insulation has an impressive ability to withstand temperatures up to its melting point of approximately 2,150 degrees Fahrenheit (1,177 degrees Celsius). As such, it can act to contain smoke and fire when used in conjunction with appropriate fire-sealant materials, thus protecting against the spread of fire. This is quite a contrast to most other insulation materials and even many other building materials.
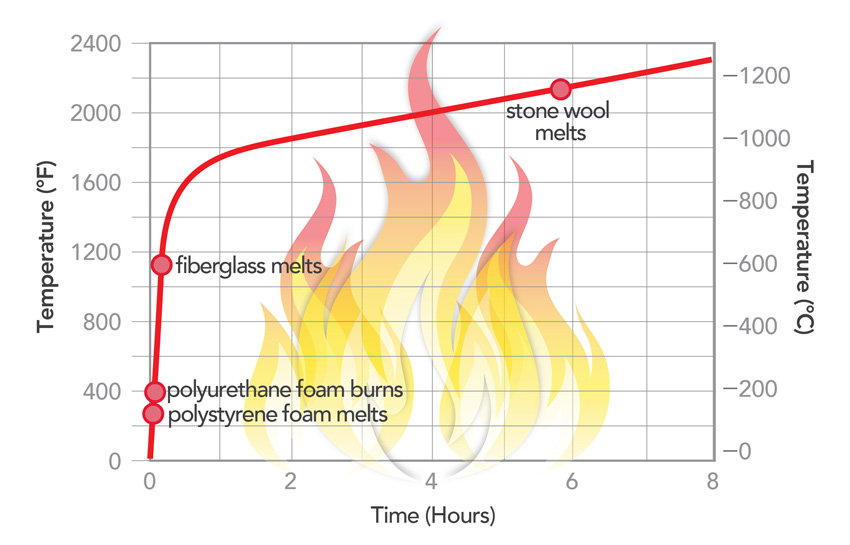
Image courtesy of ROCKWOOL™
A standard test procedure determines temperature development and melting points for different materials. As shown here, stone wool insulation has an extremely high melting point in comparison to other insulation materials
Since stone wool insulation does not contribute to fire, it can provide additional minutes of protection for occupants to reach safety. It can also provide fire-services personnel valuable time to both clear occupants and control the spread of fire while delaying the collapse of various structural members of the building. Again by contrast, foam plastic insulation must meet ASTM E84 ratings of a flame spread of 75 and smoke development of 450. Even at those levels, it must also be separated from the building interior by an approved thermal barrier, which does not apply to stone wool.
In short, taking the design approach to eliminate combustible materials from an exterior wall assembly can be the best option for many projects of all construction types, heights, and configurations. It provides great design flexibility, meets all code requirements, and eliminates the need for additional testing of wall assemblies.
Conclusion
The code requirements for fire safety in buildings do not need to be seen as in conflict with the energy-conservation requirements for insulating exterior walls. Having reviewed the relevant code sections of both the IBC and the IECC, it is clear that there are many design options and alternatives indicated in the codes to show compliance. Architects and other design professionals who understand the fundamental requirements and can discern the different options available have the best opportunity to achieve life safety, comfort, and energy conservation in building designs.
Peter J. Arsenault, FAIA, NCARB, LEED AP, is a nationally known architect, consultant, continuing education presenter, and prolific author advancing building performance through better design.
www.pjaarch.com, www.linkedin.com/in/pjaarch