This CE Center article is no longer eligible for receiving credits.
Without a doubt, the United States likes to go big. We are the home of Mount Rushmore, Disneyland, and the Whopper. We are the birthplace of Apple, Google, Facebook, and Amazon. The movie industry grew up here. We are an economic and military powerhouse. The rate of entrepreneurship is staggering. We have big vehicles, big houses, and big dreams.
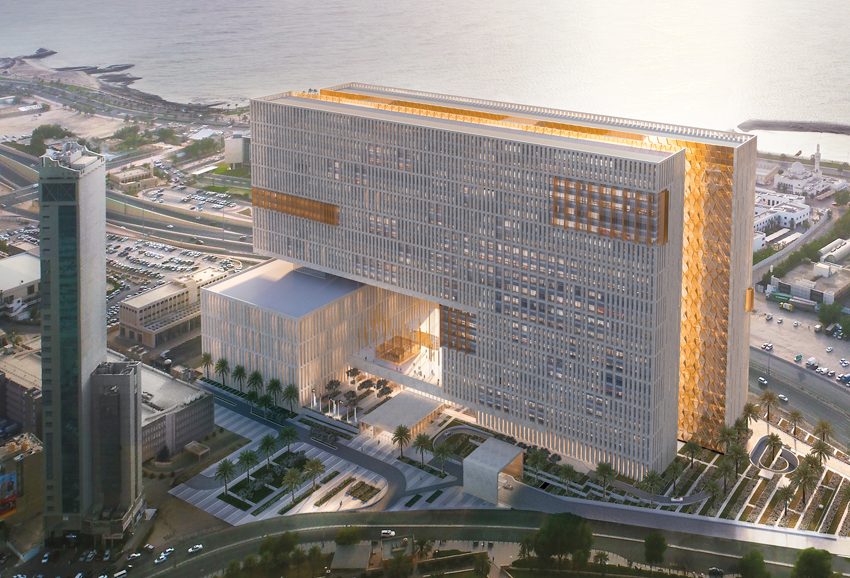
All images courtesy of Robotic Parking Systems, Inc.
When it is completed, the New Palace of Justice located in Kuwait City, Kuwait, will contain the largest robotic parking system in the world with 2,433 spaces.
But with some emerging trends, we lag. This is the case when it comes to automated parking systems, which are robotic or automatic systems that park cars without human intervention using precisely calibrated machinery and software. These innovative parking systems save valuable urban space, create the highest use for land, increase ROI for developers, improve the environment, delight drivers, and are primed to mesh with future technologies. Research and Markets research firm estimated that the global market for automated parking in 2019 was $1.3 billion and forecasts the global market to grow to $3.6 billion by 2027.1
While automated parking technology and hardware are viable and readily available today in the United States, the biggest systems are located in other countries.
The current honor of the Guinness World Record for the largest automated parking system with 2,314 spaces belongs to the Al Jahra Court Complex in Kuwait. Prior to this verified designation in 2018, the biggest automated parking system was Emirates Financial Towers (EFT) in Dubai with 1,191 parking spaces, which earned its standing in 2010. And soon, a new record holder is expected to be announced when the 2,433 spaces of robotic parking open in Kuwait at the New Palace of Justice.
Ironically, all of these record-breaking systems are made by an American company and manufactured here.
A History of Technology Advancing Architecture
Automated parking is gaining traction in the United States, though not nearly on the scale with which it is being embraced by architects and developers in other parts of the world. While having one’s vehicle automatically transported and stored within a massive steel grid is unfamiliar to most U.S. citizens, other now-common technologies were once faced with the same unfamiliarity and resistance. Elevators, for instance, were suspect for many decades after they were introduced. Only a stunt by Elisha Graves Otis at the 1854 World’s Fair in New York City, where he dramatically cut the cable of an elevator display, finally demonstrated to skeptics that an emergency brake system would prevent widespread death from elevator mishaps. Acceptance of the Otis elevator system is said to have made skyscrapers themselves possible.
When the developable space needed for parking cars is fully calculated, the acceptance of a system that can cut in half or thirds the space needed for parked cars could be revolutionary in terms of land use and even traffic issues. For architects, developers, and drivers unfamiliar with the innovation of robotic parking systems, it is helpful to take note of the largest of these installations and then examine the factors that led to their specifications.
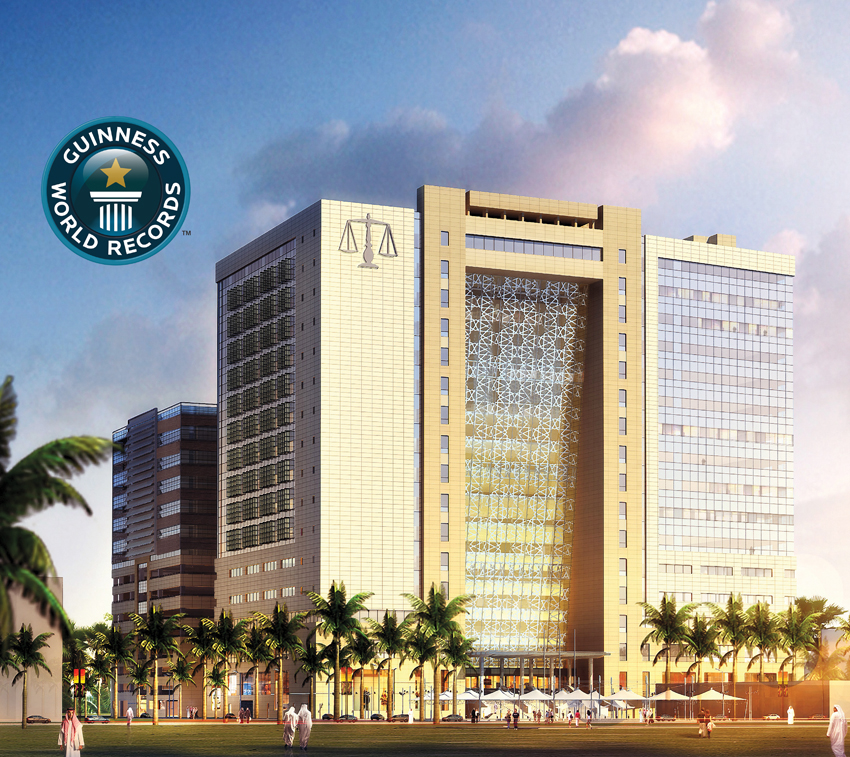
The Al Jahra Court Complex in Kuwait contains the world’s largest automated parking system with 2,314 spaces.
Al Jahra Court Complex in Kuwait
For the Al Jahra Court Complex in Kuwait—the current Guinness World Record holder for largest automated parking system—a U.S. company based in Florida with more than 100,000 square feet of manufacturing space was contracted for the project design, manufacture of the machinery, automation design, installation, startup of operations, and maintenance for the facility.
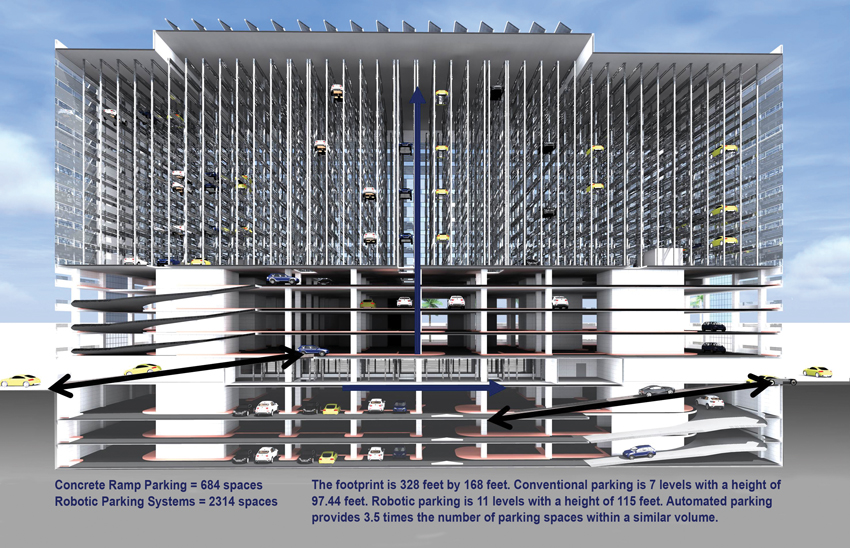
The structure is a combination of conventional and automated parking.
The parking facility was designed as a combination of conventional concrete ramp parking on the basement and podium levels, with the automated levels above the podium levels. The entire structure has a footprint of 325 feet by 168 feet, and both sections—conventional and automated—have approximately the same vertical height of 115 feet. However, while the conventional parking garage with ramps from floor to floor provides 684 parking spaces, the robotic parking system provides 2,314 spaces, or almost 3.5 times the number of parking spaces in approximately the same volume. This built project provides the starkest contrast of the space needed for each type of parking, and thus the advantageous ROI for developers who choose automated parking systems over conventional parking systems.
The automated parking structure is accessed by 12 grade-level entry/exit terminals. Peak traffic throughput (vehicles entering and exiting the terminals) is 425 cars per hour. That equals approximately seven cars per minute.
The performance of the facility exceeded the contractual requirements of 400 cars per hour throughput, and an average of 177 seconds exceeded the contractual retrieval time of 220 seconds.
The general manager of the project, engineer Mohammed Al Kholy, shared his satisfaction with the installation in a letter to the automated parking vendor: “I am writing this letter to express my gratitude and appreciation for the high-quality service being provided to us. They have executed the design, manufacturing, and delivery of over 1,293 tons of machinery, electronics, and automation equipment within a remarkably short time to meet the project schedule demanded by Amiri Diwan (the office of the Amir of Kuwait).”
Visit bit.ly/30rrIvh to watch a video of this parking garage in action.
Emirates Financial Towers in Dubai
The Emirates Financial Towers (EFT) in Dubai previously held the Guinness World Record for largest automated parking facility at 1,191 spaces. The machinery and automation were designed and manufactured by the same U.S. company that designed and built the next record holder.
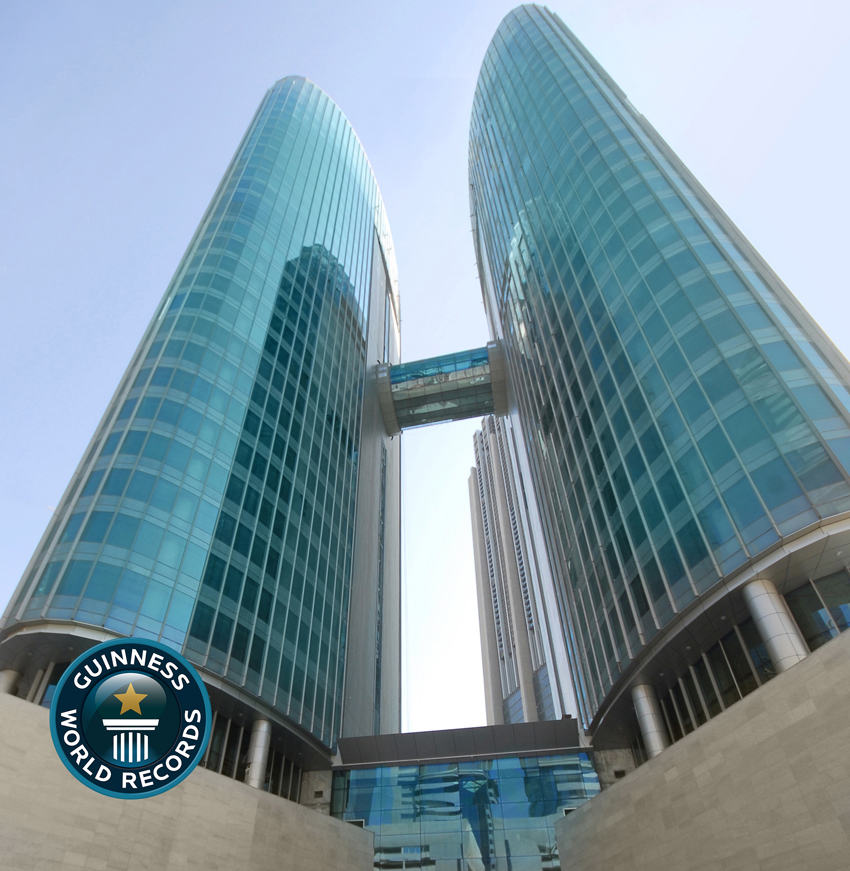
The previous world-record holder for largest automated parking system with 1,191 spaces is the Emirates Financial Towers in Dubai.
IBN Battuta Gate Complex in Dubai
The first automated parking garage in the Middle East was the Ibn Battuta Gate Complex in Dubai. Built in 2009, it has 765 spaces in a footprint of 276 feet by 98 feet, with a height of 57 feet. Performance tests showed peak traffic handling of more than 250 cars per hour with the capability of 32 cars in motion at any one time. As of 2020, this facility has a continuous operations track record of 11 years. The World’s Luxury Guide awarded the robotic parking system at Ibn Battuta Gate the status of the most luxurious automated garage in the world.
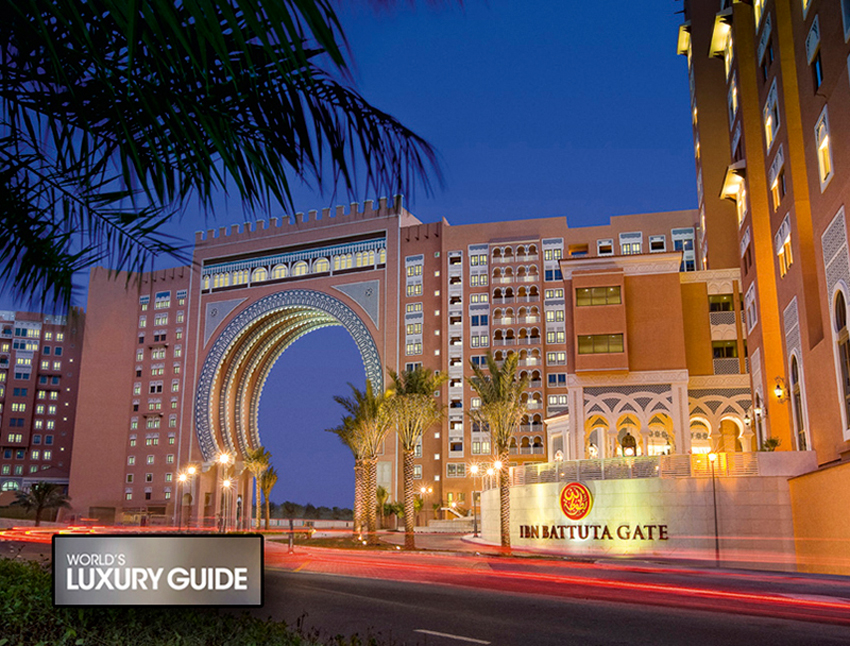
The parking system at the Ibn Battuta Gate Complex in Dubai was named the most luxurious automated garage in the world.
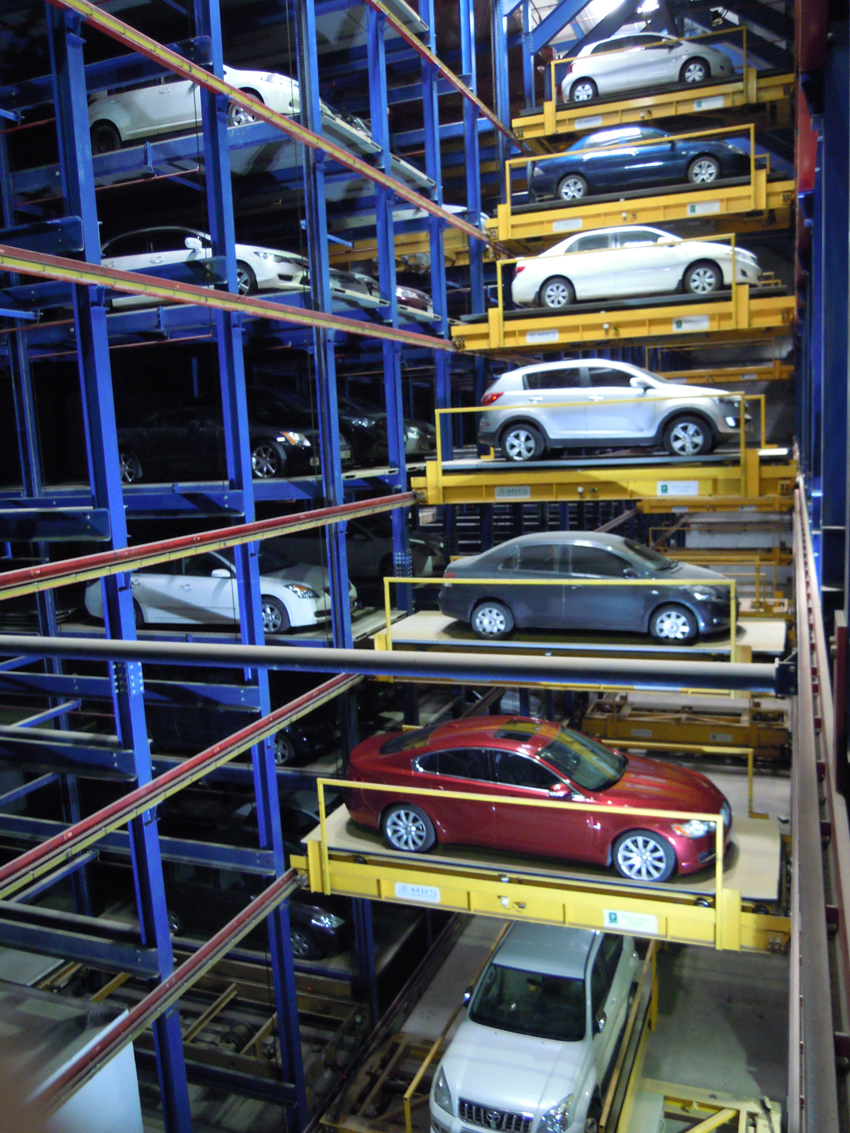
Shown is the interior of the robotic parking garage at the Ibn Battuta Gate Complex.
Upcoming: New Palace of Justice in Kuwait
The New Palace of Justice in Kuwait with its luminescent cubist design will be the world’s tallest and largest judicial building. The U.S. company that built the other Guinness World Record holders for largest automated parking systems is building 2,433 automated parking spaces for the facility. This iconic garage features 18 terminals with a throughput of 720 cars per hour. That is a capacity to deliver approximately 12 cars each minute. Previous third-party certification shows an average single retrieval time of 177 seconds. It is expected to take over the Guinness World Record title when completed.
How Robotic Parking Systems Work
The process happens in five steps. The user drives the car into a terminal, parks on a steel pallet, collects his or her belongings, and then exits the terminal. The doors to the terminal close. The computer-activated machinery pulls the pallet and car into the facility, and rotates them by 180 degrees. That way, the car is facing forward when it is retrieved. Then, an elevator lifts the pallet and car to an upper level. The pallet is transferred to another carrier that moves it laterally to an open parking spot. The car and pallet are moved into the designated parking spot. When the user returns for the vehicle, the process is reversed.
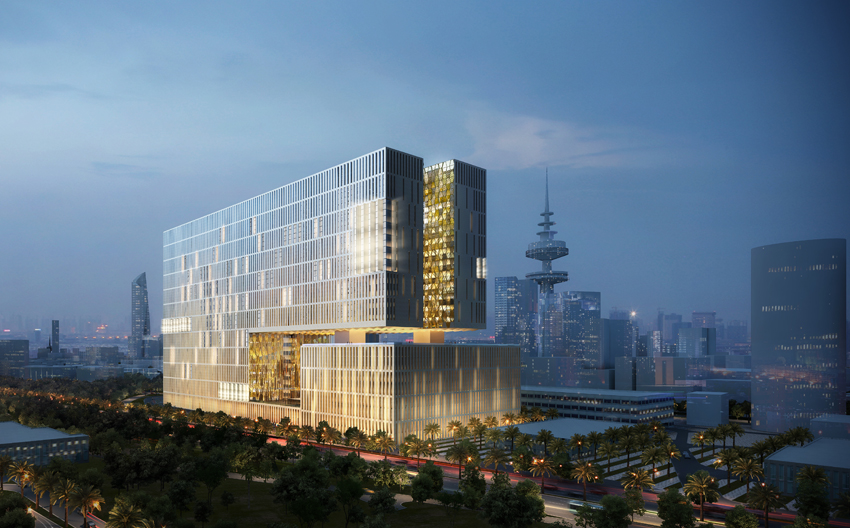
When the New Palace of Justice in Kuwait is complete, the 2,433-space automated parking system is expected to take the title as the largest automated parking system in the world.
Benefits of Pallet-Based Systems versus Dolly-Based Systems
Pallets are steel plates with grooves on which the vehicle is transported. Grooves in the pallets help drivers easily position their cars. Pallets are about 20 feet long and 7.5 feet wide. Pallets prevent the dripping of oil, acids, air-conditioning condensation, saltwater, snow and ice, or sand onto cars from the parking system machinery or the cars stored inside the facility.
Pallets eliminate all direct contact with the car and guarantee that no machinery ever touches the vehicle. This design feature ensures one of the highest standards of product liability protection for automated parking facilities. Some companies offer a pallet-cleaning mechanism for garages in locations that regularly have snow and ice. This system can remove water, sediments, and salt from pallets.
Several automatic parking systems do not use pallets. These systems use dollies that move under a vehicle and clamp onto its tires to transport it. Dollies used in these systems feature a major technical design flaw that can cause serious damage to low-ground-clearance cars or a chassis that was altered by the owner. The garage owner cannot defend such a damage claim.
With a dolly system, vehicles with a close-to-the-ground base can be scratched, dented, or have their bottom components ripped off altogether as the dollies travel under the vehicle. Electric vehicles have a low clearance from the floor to accommodate a battery pack. For these reasons, non-pallet systems may not accept certain vehicles.
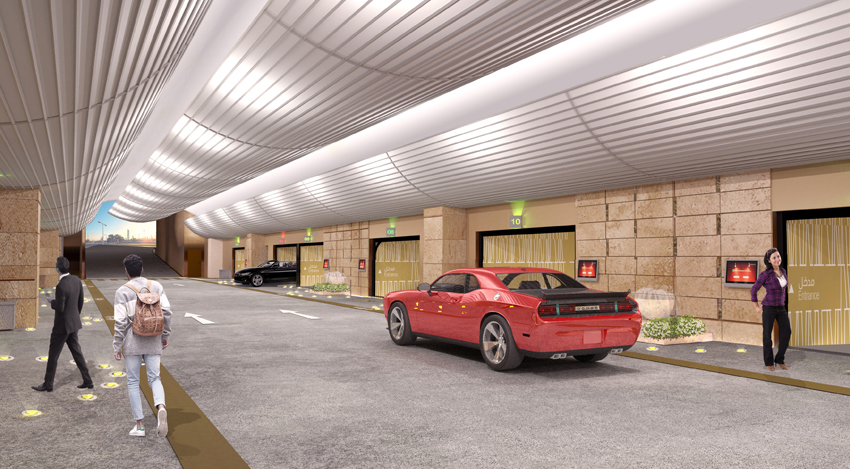
Shown is a rendering of the automated parking garage at the New Palace of Justice in Kuwait.
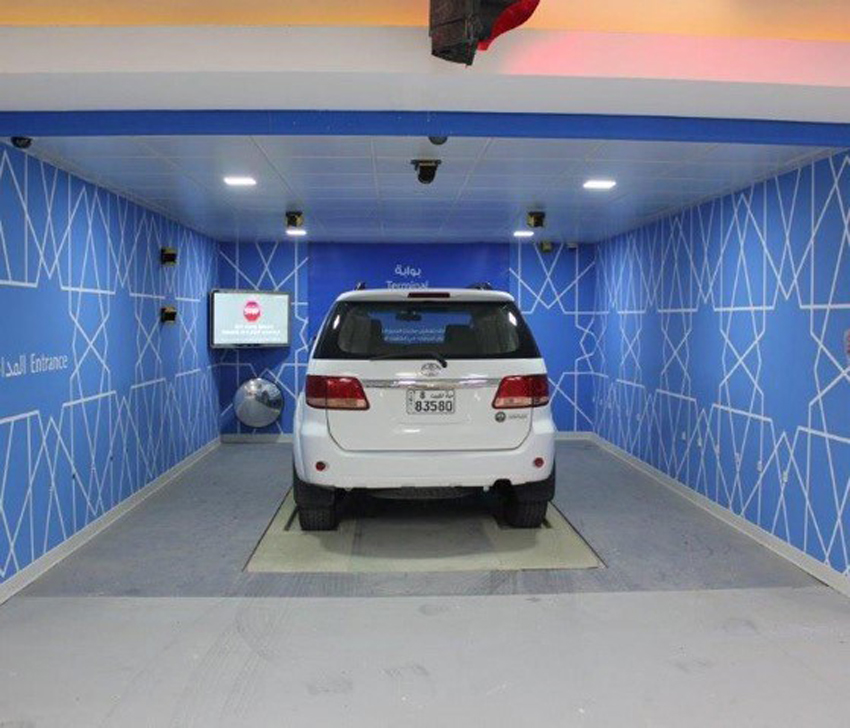
A pallet system on which a vehicle is transported, as opposed to a dolly system that grabs the wheels, ensures that no machinery ever touches the vehicle.
Throughput Capacity Verification
The big question that arises about automated parking is: How quickly can cars be retrieved? For an accurate assessment, third-party test certification and verification is critical to garage efficiency. Peak traffic throughput capacity equals the total cars per hour in a combination of inbound and outbound traffic. Throughput capacity is more critical than single retrieval time in day-to-day operations.
Reliability and Redundancy
For an automated parking system to work, it must be reliable with redundancies built in. Developers are naturally resistant to include any unproven technologies that might fail. Manufacturers of these systems understand the importance of this fact, and they invest in systems, machinery, and software to prevent outages.
Consider the, the 760-space garage at the Ibn Battuta Gate Complex in Dubai. The system consists of machines built to support independent motions on all three axis: vertically between floors, horizontally in a row, and in and out to move cars into and out of racks in the shelving system (made of steel, concrete, or a mix of precast concrete and steel). Independent machines are a key factor in the system’s reliability.
At least two of each type of machine are installed per area in the automated parking facility for redundancy. Both of the machines can perform the same tasks at the same time. Therefore, if one machine needs maintenance or repair, there is always a backup machine to keep the cars moving into and out of the garage.
No single failure will ever result in the system being inoperable. Performance for the robotic parking systems used in these largest of installations, based on operational and maintenance data over the past 16 years, is 99.9 percent uptime.
Forty robotic machines are used at the 765-space Ibn Battuta Gate Complex garage, for example. If one machine fails or needs maintenance, that is only 2.5 percent of the total robots in the garage. In this scenario, the only consequence of a robot failure is that a few cars take about 200 seconds for retrieval instead of 160 seconds.
Machine redundancy is complemented by other fail-safe features, such as true redundant computer servers, universal power supply, and a backup power generator to ensure continual operation.
Anne Marie Shein, then senior property manager for Ibn Battuta Gate, states that after more than three years of operation, “The automated car park is well-maintained and running flawlessly.”
A Healthier, Safer, and Stress-free Experience for Users
Conventional parking garages sound innocuous, but they are in fact dangerous and unhealthy. A study by the U.S. Department of Justice found that one out of 12 rapes occur in parking garages and more than 40 percent of sexual assaults by strangers occur in garages.2 Additionally, upper decks of parking garages frequently become sites for suicide.
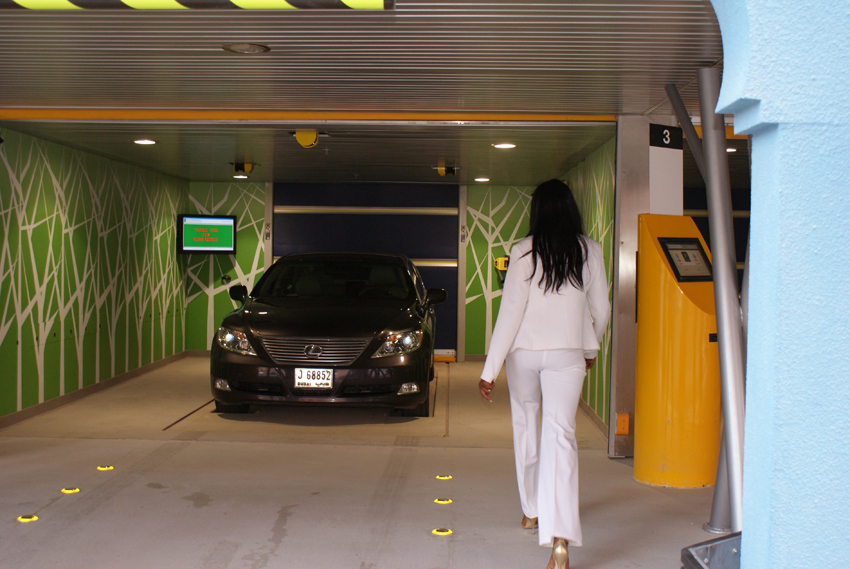
The user experience with an automated parking system, marked with a terminal to drop off and retrieve a vehicle, is vastly different from the experience of walking through a conventional parking structure to find a parking spot or find one’s vehicle, dodging other cars, breathing fumes, and possibly encountering an assailant.
Every day, there are numerous news stories about accidents, theft, and violence in conventional parking garages and parking lots. People are hit by cars or drive off parking decks. Others are assaulted, knifed, or shot. Vehicles are vandalized and stolen.
Architects, parking designers, developers, and owners can greatly increase parking safety and security for both individuals and cars by specifying an automated parking system. The inherent safety features of the system can help significantly reduce potential lawsuits and lower insurance rates as well.
These factors make automated systems beneficial for the health and safety of users:
Less stress: While driving around searching for a parking space may seem like a necessary evil of city life, it does not have to be. Imagine giving up circling the block or the parking garage looking for a parking spot. Imagine the simplicity of driving into a terminal, locking and leaving your car, and letting the machinery and software take over. And imagine the reverse, with no stress to recalling where you parked your car.
It is the equivalent of a premium valet service without the tipping.
Safety from other drivers: Dodging other cars in a parking facility is another aspect of city life that seems unavoidable. While conventional garages and lots make room for cars, virtually no consideration is made for the drivers exiting and retrieving those cars. Where do they walk safely? The automated parking system eliminates the car-versus-person dodge to which we are accustomed.
Personal safety: Most women will be familiar with a feeling of unease in conventional parking garages. With an automated system, there is no need to walk to and from the car through rows of vehicles or levels of parking decks. With an automated parking system, the driver pulls into a terminal located next to the street and leaves the car to be picked up by computerized machinery. The car is safe and protected on its own pallet, and never touched by machines or humans. When leaving, the driver returns to a lobby where the car is quickly delivered to a ground-floor terminal.
Fewer fumes: While breathing fumes from cars idling in a parking garage is yet another hazard we take for granted, an automated system completely eliminates this threat to human health. When vehicles are driven into the entry terminal of an automated system, the engine is immediately shut off and will not be started again until the driver has returned to retrieve the vehicle.
No access for thieves or vandals: Automated parking garages eliminate theft and vandalism. Vehicles are stored in a fully enclosed building and are 100 percent secure from access by others. This is a good example of a practice known as Crime Prevention Through Environmental Design (CPTED), a specialty of Randy Atlas, Ph.D., FAIA, CPP (Certified Protection Professional), who is both a criminologist and an architect. Atlas argues that buildings need to be designed for safety against crime, lest owners and operators risk liability for crimes committed.
A research brief by the U.S. Department of Justice titled “Crime Prevention Through Environmental Design in Parking Facilities” states, “Because parking facilities comprise a large volume of space with relatively low levels of activity, violent crime is more likely to occur in a parking facility than in other commercial facilities. Many parking facilities lack CPTED design features because most property owners and architects are not familiar with basic principles of design concepts for crime prevention.”3 Automated parking systems eliminate not only the fear and occurrences of crimes, but also the liability for those crimes.
No nicks or dings: Regularly parking in a conventional lot or garage almost always results in dings and dents in a car. Parking spaces are often small, and distracted people smash their door into the sides of vehicles, etc. In an automated parking system, no one touches the car after it is placed on the parking pallet. In fact, the automated parking facility itself contains only machinery and vehicles. No humans are allowed.
Touchless System in a Pandemic World
Another bonus of automated parking is the premium valet experience, which offers a contactless parking process to accommodate for pandemic needs. When the driver and the passengers have left the entry area (terminal), in higher-quality systems, the driver initiates the parking process with a touchless near-field communication (NFC) card, FOB, or mobile application. Instead of passing the keys to a valet and having a virtual stranger enter the vehicle, patrons simply use an app and keep their keys, with no other persons involved.
In simple terms, automated parking enhances the vehicle parking and retrieving experience—elevating it above the level of valet parking.
Environmental Benefits of Robotic Parking
Automated parking systems help conserve fuel while reducing pollution. No cars are driven in the garage, creating a greener garage experience. The electrical power required to run an automated parking system is low, meaning the net reduction of its carbon footprint remains significant.
EEA Consultants Inc., an environmental engineering firm, conducted a study comparing pollution and energy characteristics of a conventional 350-car garage to those of an automated garage of the same capacity.4
Data suggests that, overall, automated parking systems are better suited for the environment, reducing the amount of volatile organic compounds (VOCs) by 68 percent, carbon monoxide by 77 percent, nitrogen dioxides by 81 percent, and carbon dioxide by 83 percent. It also finds a reduction of fuel consumption by 83 percent.
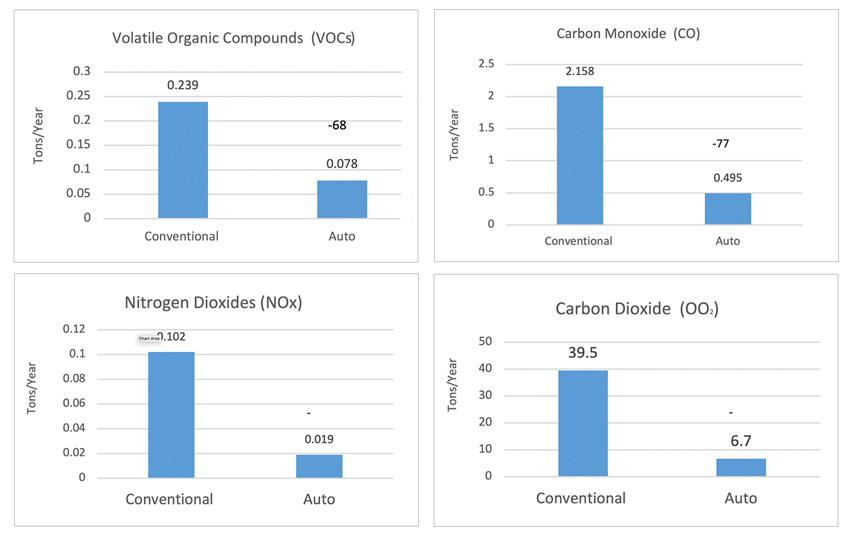
Shown are the statistics on pollutant reduction for automated parking systems based on a study conducted by EEA Consultants Inc., an environmental consultancy firm.
LEED Points and Carbon Credits
An automated parking system could potentially help contribute up to 12 points or more toward LEED certification.
The areas where automated parking can help earn points include:
- Maximizing open space in site development;
- Lighting;
- Reducing chemicals and pollutants;
- Air quality;
- Energy consumption (gas saved);
- Optimizing energy performance; and
- Preferred 5 percent parking (for low-emitting and fuel-efficient vehicles) and shared vehicle storage.
Codes
As with any emerging technology, the codes change and adapt with time. Automated parking is considered an automatic storage system, unoccupied, rather than the common understanding of garages as people driving vehicles through a building structure used for parking.
International Building Code (IBC): In terms of automated parking garages, look to the Occupancy per Section 311: Group Storage S2, Section 503.1.1: Special Industrial Occupancies, and as further detailed in Section 2208: Steel Storage Racks.
Also, if the parking system is based on an open rack structure, a building is considered a one-story construction. Some jurisdictions classify automated parking systems as “equipment” and issue appropriate requirements for certain fire ratings of the surrounding supporting building elements.
International Fire Code: Chapter 23, Section 2309: Automated Storage states that: Due to the high content of plastic as well as the existence of fuel tanks in automobiles, the storage should be considered to be a “high hazard commodity,” and, in accordance with Section 2309 and Table 2306.2, require an in-rack sprinkler system per the National Fire Protection Association (NFPA) 13 as well as a building access point placed every 100 feet. These and similar requirements are also in accordance with NFPA 88A, which details such as well in its Chapter 9. Also described there are ventilation requirements of two air changes per hour, which can be satisfied, where possible, using natural ventilation.
Additional Codes
There are various codes that are available for automated parking. The following are highly common:
- National Parking Association (NPA): Guide to the Design and Operation of Automated Parking Facilities;
- American Society of Mechanical Engineers (ASME) B30.13: Storage/Retrieval (S/R) Machine and Associated Equipment; and
- All electrical equipment should be ETL or UL listed and approved.
Standard for Care
In the Standard for Care directive, a design professional has the responsibility or duty that anything that is designed needs to “fit for the intended purpose of use.” This is a very general and broad definition. However, it has become more and more important and implemented by the courts during the past 10–15 years. In the automated parking industry, it means that if an architect, engineer, or automated parking engineer knows that 400 parking spaces, for example, are needed for a residential development, he or she then has the obligation to make sure that the associated required peak traffic capacity is designed in accordance with industry standards.
According to the National Parking Association, “The most important factor for designing the access requirements for any parking facility is to determine the peak hour arrival and departure traffic volume.” This in turn determines the size and design of the automated parking structure. If a design professional does not adhere to this industry standard, he or she can be held liable by the developer or owner.
In addition, it is extremely important at the very beginning of the planning process to determine the support system grid layout of an automatic parking facility. This affects the efficiency of any facility layout and will optimize the footprint. This is exactly how planners start the layout of any building with a conventional concrete ramp parking structure. First, the column layout is determined for the parking facility. Then, the upper floors of the building are based on this column layout. This process also should be followed with an automatic parking facility.
Significant Land-Use Benefits and Positive ROI of Automated Parking
While parking may seem like an afterthought to some, providing an automated parking system could be the centerpiece of a project and if done well may provide the ROI that allows a project to go forward, or not. To assess the real cost of parking options, Samuel I. Schwartz, PE, a former transportation commissioner of New York City, compared the operating and capital costs of an 892-space conventional garage versus those of an automated parking facility. Schwartz concluded that, when all factors are considered, the cost of operating an automated garage is less than half (a 55 percent savings) than that of a conventional garage.
In his paper titled “The Garage of the Future Must Be Green,” Schwartz states, “An owner can save over $1.1 million per year with automated parking. In the current real estate climate, this is equivalent to capital cost savings of over $15 million.”5 Schwartz also stated that the useful life of a conventional concrete parking garage is about 20 years. The earliest European mechanical/automated systems show little to no wear after more than 50 years of usage. An example is the parking system of Deutsche Bank in Musnich, Germany, which was installed in 1956 by the Krupp Corporation.
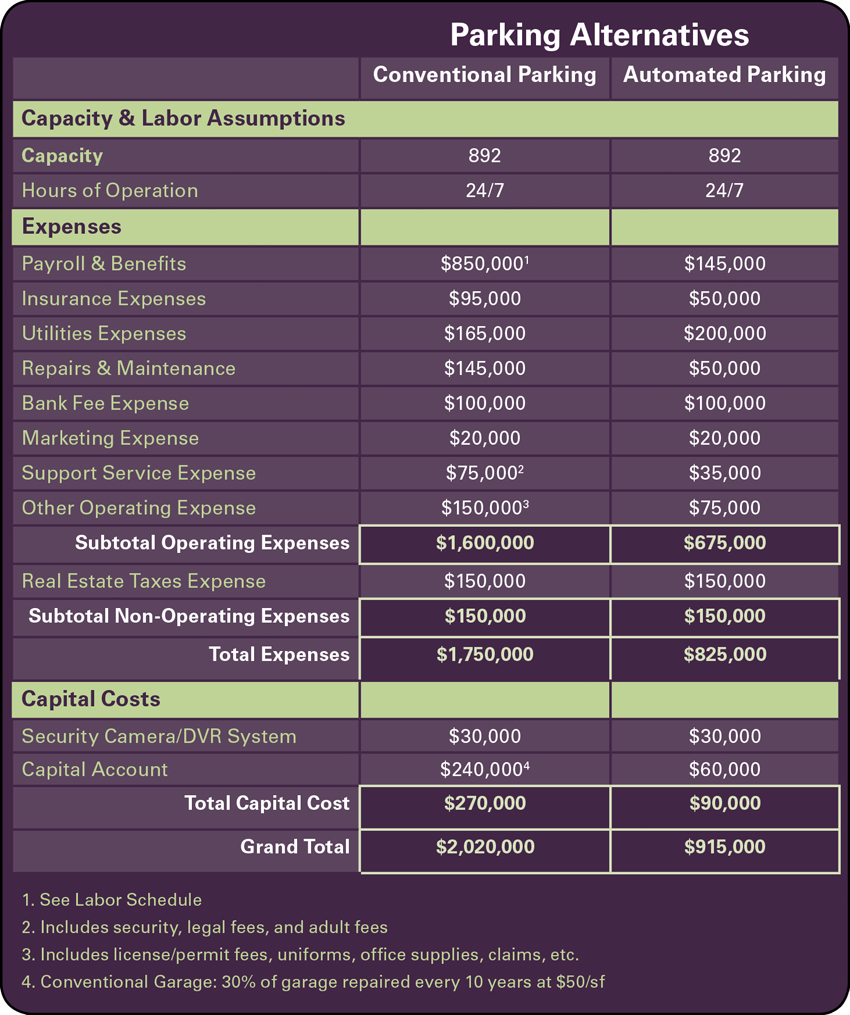
Shown are comparisons of expenses and capital costs for a case study in Upper Manhattan, New York City.
All Spaces ADA Compliant
Depending on the robotic parking manufacturer, all entry/exit terminals should not only be compliant with the American With Disabilities Act (ADA), but they also tend to be extra large and comfortable.
For a quality installation, the minimum width of each standard terminal will be larger than 15 feet, which means each walkway has 4 feet of equal clearance on the left and right of the parked car. The minimum width of the ADA entry/exit terminals is 12 feet of car slot and 5 feet minimum on one side for the walkway for wheelchair access. This is 17 feet width in total.
Considering the Number of Stories
Besides attention to the local zoning code requirements, there are other limitations for conventional parking garages. For example, users generally avoid driving more than 6 levels of ramps. Automated parking can reach higher than 15 levels.
There may also be local zoning benefits derived from automated parking because an automated parking system can be considered a 1-story building. This is because systems can be designed using a rack system with concrete only on the floor and ceiling of the entire space. In a rack system, the levels are constructed from removable steel structure and inserted machinery.
Capacity and Scalability
In 2001, a leading automated parking manufacturer made a major development in the automated parking industry with the development of “lift-and-run” technology. To understand why this technology is revolutionary, it is necessary to understand how it was done previously (and is still being done by many).
Above are images that demonstrate an older and widely used technology. This type of system relies on one machine to transport each vehicle from the entry terminal up to its final parking space. This means that the machine goes up to the final parking destination with a car and returns to the entry terminal empty to pick up another car in morning rush hour (for example). This is inefficient.

Shown is an example of older technology that relies on one machine.
The new patented lift-and-run technology, shown below, uses the principle of “passing” the load from one machine to another: It lifts the vehicle, runs with it for a certain distance on one of the X, Y, or Z coordinates (directions), and then passes it to another machine that is operating on another coordinate. This is much more efficient than having one machine do the entire transportation cycle along all three axis and increases the overall speed of the system.
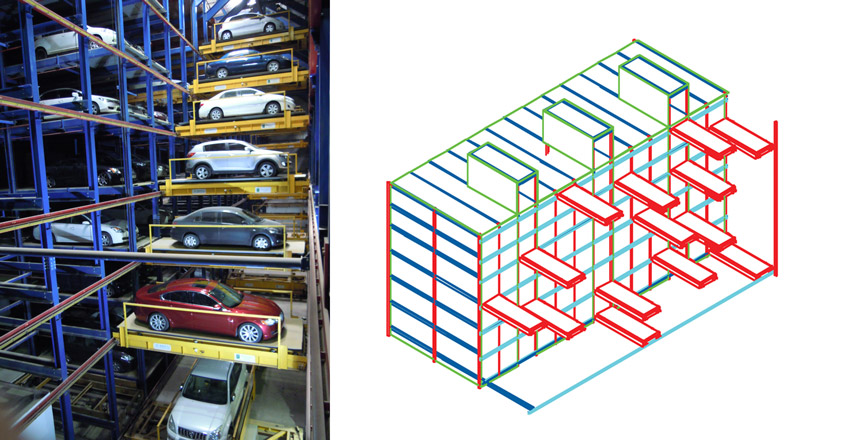
Advanced technology, known as “lift and run,” passes the load from one machine to another.
A major benefit of lift-and-run technology is its scalability. These systems are built like a layered cake. A layered cake alternates between cake and frosting. In order to have a bigger cake, one only needs to add another lay of cake and frosting to the top.
Lift-and-run parking is constructed in the same way, except its layers go from side to side. Each layer consists of machines that “lift” vehicles vertically (the cake) and machines that “run” cars horizontally (the frosting). To increase the size of the parking structure, one needs only to add a “layer” of lift-and-run machinery to one side.
Repeating instances of lift-and-run machinery create a system that is scalable in a way that a system that depends on “bookend lifts” cannot be.
Adaptive Reuse for Floor Space
In some automated parking systems, space can be reconfigured for future uses, including storage use by introducing containers (also for cold-storage use or nitrogen use). Much depends on the structure of the facility. Is it comprised of steel racks or concrete decks? Facilities with steel racks can be more easily adapted than traditional concrete parking garages and automated parking garages that rely on concrete for each level.
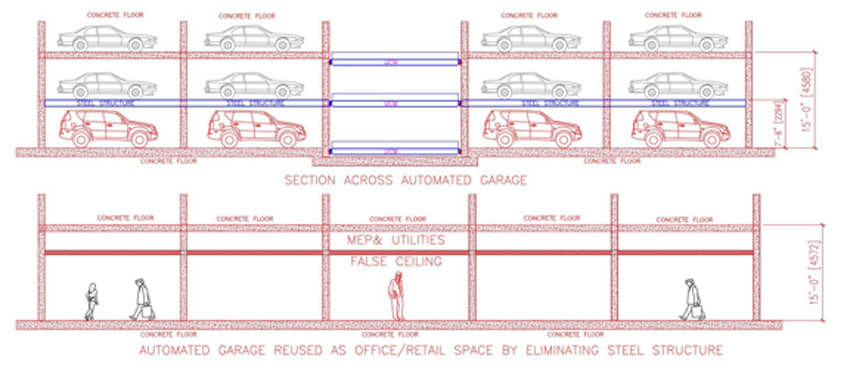
This illustration shows how an automated parking structure could be retrofitted for future needs.
As the illustration above shows, the system can be taken out and the space reallocated for other uses by providing ample heights. The system, partially or entirely, can be relocated to another location, allowing developers to convert the parking slot into other usable space. All or a portion of the parking spaces can be reused as storage spaces by providing container-like covering on top of the pallet.
Changing the Dynamics of Land Use
Automated parking frees up massive amounts of downtown property. Every 500-car concrete garage replaced with an automated robotic garage can generate up to half an acre of available land. These acres can now be used for green spaces, additional residential units, office spaces, amenity areas around the city, or additional parking.
Not enough parking is actually considered to be the primary cause of congestion. Therefore, parking moratoriums and the thinking that additional parking adds to congestion is the opposite of what in-depth U.S. Department of Transportation (DOT) and other research conclusively shows. Don H. Pickrell, chief economist at the U.S. DOT ’s Volpe National Transportation Systems Center, located at the Massachusetts Institute of Technology in Cambridge, states that “research in diverse urban settings estimates that as many as half of all automobiles on the street are simply cruising in search of vacant off-street spaces.”6 Additional studies have also reported that an average of 30 percent of traffic in city centers is generated by drivers’ search for a parking spaces.7
How Robotic Parking Fits into Emerging Driving Technologies
For higher levels of technology integration, automatic parking system companies would do well to orient their systems around the acronym CASE, as defined by Mercedes-Benz at the Paris Automobile Show. CASE is an acronym for: connected, autonomous, shared, and electric.
Connectivity: Through use of software from existing, known, and reliable companies, an automated parking company can be connected and receive and share information on an open network.
Autonomous driving: A parking company should develop a partnership with big players in the industry to facilitate the parking of autonomous driving cars.
Sharing: Communications exist to handle car sharing, fleets, and servicing cars.
Electrification: Automatic parking systems are designed to include automatic electric car charging stations. The owner just plugs the cable in the entry terminal to the car.
Electric Cars
With recent proclamations on electric vehicles from the largest U.S. and global automobile manufacturers, providing adequate numbers of charging stations for an anticipated influx of electric cars will become an issue. Fully automated parking systems can be equipped with these stations, and there is no limit on the number of charging stations the planner can select. More can be added at a later point as needed.
Once the car is charged in an automated parking garage, machines move the car to an ordinary parking slot and can bring in the next car in the queue for charging. Patrons can thus avoid receiving fines for blocking the charger after a car is fully charged. With this feature in an automatic system, the actual number of charging stations can be reduced, and respective cost savings can be gained.
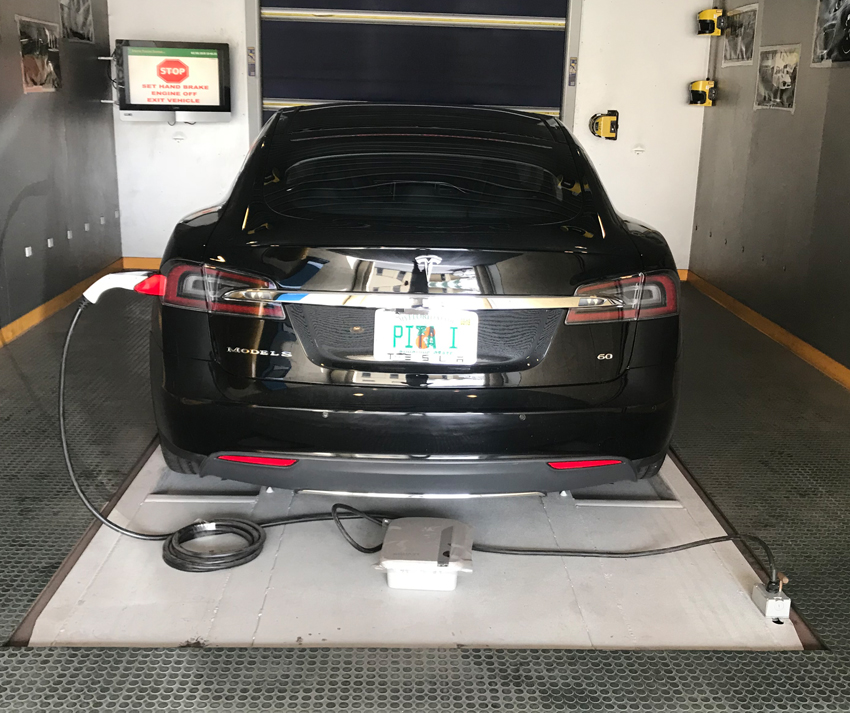
Electric cars can be changed in a charging spot and then automatically moved to another spot when fully charged, allowing another electric vehicle to be moved to that spot.
Autonomous Vehicle Parking
Going forward, conventional concrete parking garages will struggle to cater to the needs of self-driving or autonomous cars without large investments for sensors, software, and other guidance equipment. This increases the cost of investing in conventional garage construction. Automated parking systems, however, already have a built-in automation platform that can relatively easily accommodate self-driving cars.
Conclusion
While the United States cannot claim the largest automated parking systems in the world at this time, there is no doubt that this could eventually change. The acceptance of automated parking will likely be driven by architects working in the best interest of developers to achieve the highest and best use for any new or retrofitted project. While U.S. residents have become accustomed to the fumes, danger, and inconvenience of conventional parking garages, there is every likelihood that they will one day embrace this technology as thoroughly as they have embraced the push-button ease of elevators. For the best ROI for land development, it is incumbent on architects and developers to give robotic parking systems serious consideration, changing the dynamics of land use.
End notes
1“$3.6 Billion Automated Parking System Market – Global Forecast to 2027.” Research and Markets. 3 September 2019. Web. 25 February 2021.
2Schwartz, Samuel. “The Garage of the Future Must be Green.” Parking Magazine. March 2009. Web. 25 February 2021.
3Smith, Mary S. “Crime Prevention Through Environmental Design in Parking Facilities.” National Institute of Justice Research in Brief. April 1996. Web. 25 February 2021.
4“Automated Parking Systems Offer Air Quality and Fuel Consumption Benefits.” Environmental Consulting Insights. EEA Environmental Consulting Activities. Summer 2009. Web. 25 February 2021.
5Schwartz, Samuel. “The Garage of the Future Must be Green.” Parking Magazine. March 2009. Web. 25 February 2021.
6ULI on the Future: Smart Growth – Economy, Community, Environment.
Urban Land Institute. 1998.
7Arnott, Richard and Inci, Eren. “An Integrated Model of Downtown Parking and Traffic Congestion.” Journal of Urban Economics. November 2006.