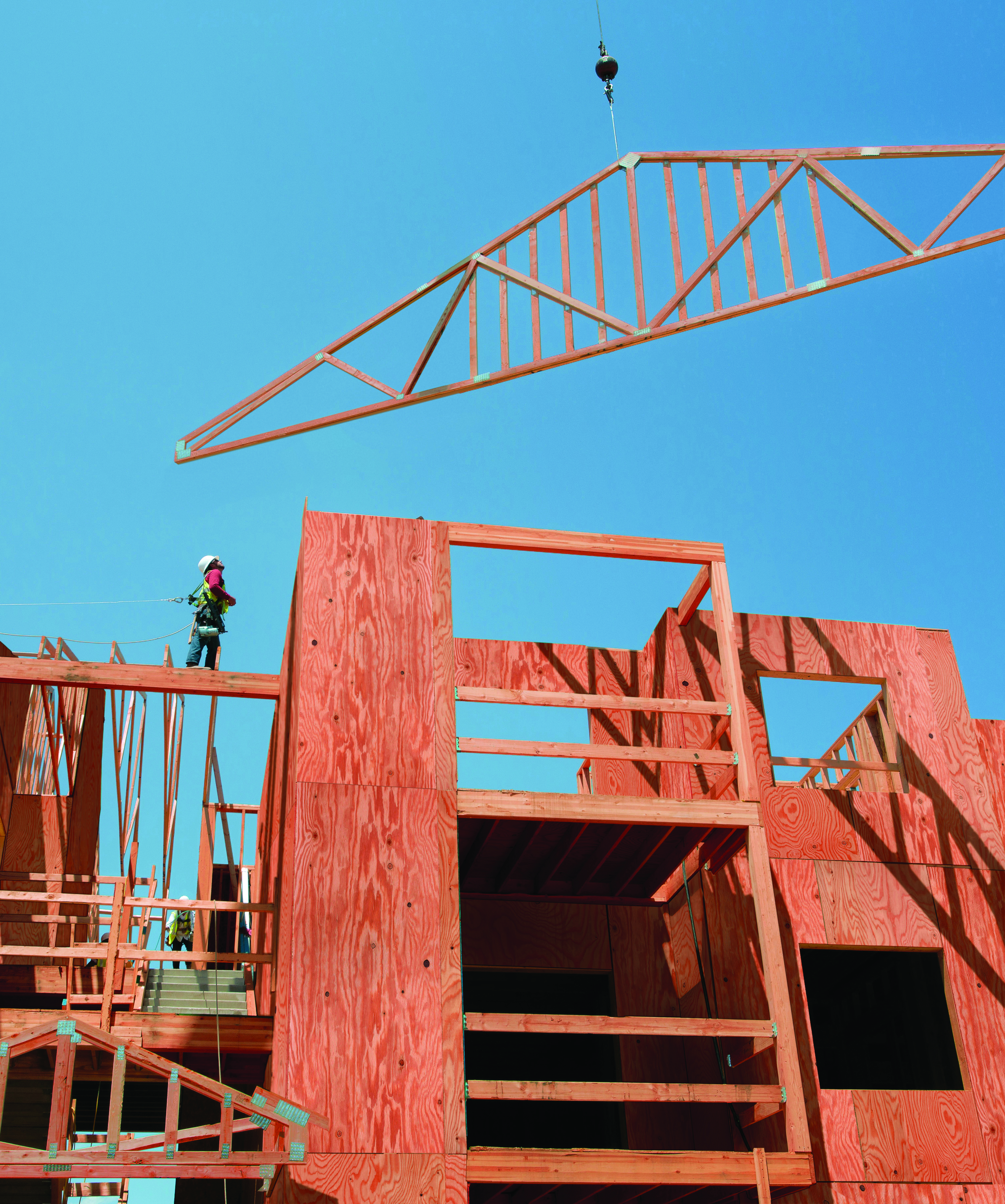
Photo courtesy of ProWood
Fire-Retardant Pressure-Treated Wood (FRTW) is recognized as a code-acceptable option for framing walls and roofs for many different types of buildings.
Fire safety is a concern in all buildings but so is ease of construction and budgetary requirements. Finding a way to balance these aspects can often be the difference between a successful building project and one that is less so. As a result, many architects and building owners consider different types of materials and construction techniques in order to balance all of the project requirements. For many low- to mid-rise commercial buildings, that includes taking a closer look at wood products for economy, sustainability, and design flexibility. In order to be code-compliant, fire-retardant-treated wood (FRTW) is often used with many tested and proven wall, floor, and roof assemblies that are readily constructible. In this course, we take a closer look at why fire resistance is so important in buildings and how FRTW is being used in several different ways to meet that need in well-designed buildings.
THE NEED FOR FIRE RESISTANCE
Protecting buildings from fire has been a common concern throughout history. While the things that may cause fires have changed over time, the impact of them on people and property is real and often dramatic. The nature of building fires can fall into two categories.
Property Fires
Property fires, the first category, continue to happen across all building types in the United States. The National Fire Protection Association (NFPA) tracks the number of fire calls and events in the U.S. on an annual basis. According to a report in October of 2023 on their website, the following relevant key findings of their work were identified:
- “In 2022, local fire departments responded to an estimated 1.5 million fires in the United States. These fires caused 3,790 civilian fire deaths and 13,250 reported civilian fire injuries. The property damage caused by these fires was estimated at $18 billion.
- More than one-third of the fires (522,500–or 35 percent) occurred in or on structures. Most of the fire losses were caused by these building structure fires, including $15 billion for direct property damage (83 percent).
- Vehicle fires accounted for only 13 percent of fires, 16 percent of civilian deaths, and 5 percent of civilian injuries.
- Data suggests that less progress has been made in preventing deaths and injuries associated with reported fires. For overall home fires, the 2022 rate of 7.5 deaths per 1,000 reported home fires was higher than the rate of 7.1 in 1980. The death rate for one- or two-family home fires was 14 percent higher than in 1980, while the rate for apartment fires was 18 percent lower.”
They also point out that “most of the reduction in reported fires and fire losses occurred more than a decade ago. Thus, there is more work to be done to reduce fire incidence and improve life safety.” Architects and others involved in public safety play a key role in this regard.
Wildfires
This is the second category of fires. It’s no secret that wildfires are increasing in the U.S. and many communities across the country have experienced their effects on buildings, people, and the environment. The NFPA report cited above noted their significance, stating “Neither structures nor vehicles were involved in half of the fires reported in 2022 (51 percent). These fires included brush, grass, or wildland fires (22 percent); outside rubbish fires (16 percent); outside fires involving property of value (crops, timber, and other properties of value–6 percent); and other fires (6 percent).” Clearly, this is a significant concern and a disturbing trend.
In response, some jurisdictions are implementing Wildland-Urban Interface (WUI) building codes to address fire safety concerns. These WUI codes typically require greater fire resistance in the construction of all types of buildings in order to provide a larger time frame for people to escape wildfires. In these cases, the choice of materials used to achieve adequate or required fire resistance in building exteriors and structures becomes a significant point of design and specifications.
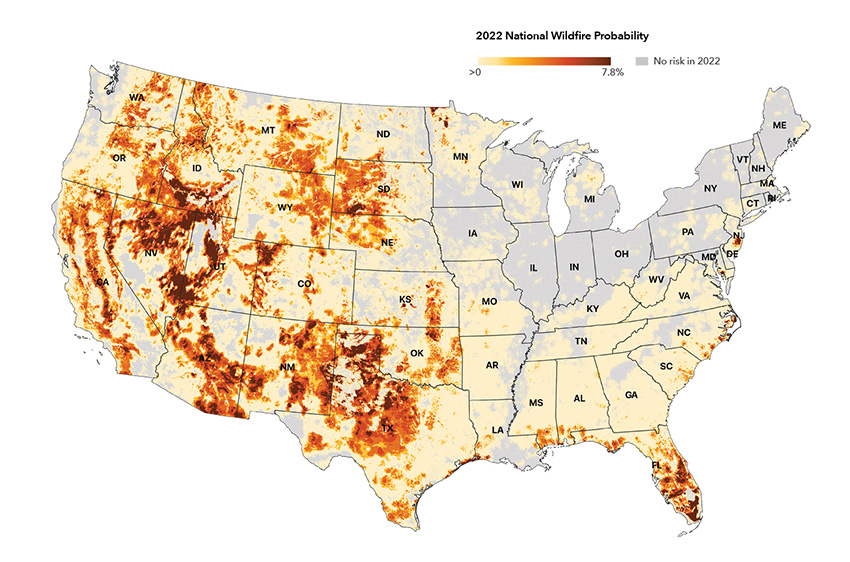
Image courtesy of ProWood – Source: First Street Foundation
Wildfires have become more probable in many locations across the United States and are as significant a concern to safety in buildings as fires that start within buildings.
BUILDING CODES AND FIRE
A major motivation for building codes has always been fire protection. For the past 20 years or so, the standardized model codes have been developed and regularly updated by The International Code Council (ICC). This is a very comprehensive, ongoing process that involves thousands of code officials, design professionals, construction specialists, and others around the country. Once vetted, voted on, and published, it is then up to the local authorities having jurisdiction (AHJs) to adopt the version of the codes they choose to enforce. While the ICC publishes and coordinates a “family” of more than a dozen different codes, several are relevant to our discussion here.
- The International Building Code (IBC) is the basis of all commercial building design and construction and is the foundational document of most of the other building related codes.
- The International Residential Code (IRC) applies specifically to one-and-two-family detached and attached homes. Multifamily residential properties are covered by the IBC.
- The International Existing Buildings Code (IEBC) applies to alterations, additions, or change of occupancy of existing buildings pointing out the things that either apply or may be exempt from the IBC based on project size or scope.
- Related codes such as the International Fire Code (IFC) and the International Energy Conservation Construction Code (IECC) apply to all building projects with more detailed requirements for fire- or energy-related issues, all coordinated with the IBC and the IRC.
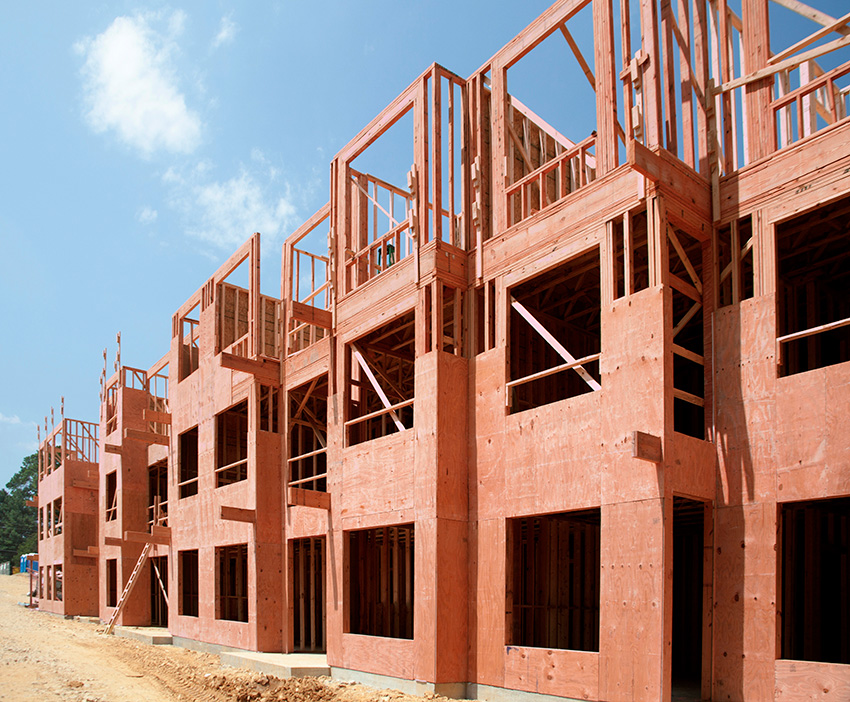
Photo courtesy of ProWood
The International Building Code (IBC) identifies the required fire resistance for exterior walls, interior walls, floors, and roofs along with the acceptable uses of fire-retardant-treated wood all based on the five defined Types of Construction.
All of the codes rely on independent, third-party standards as the basis for materials or building assemblies to demonstrate code compliance. For example, the American Society of Testing Materials (ASTM) and Underwriters Laboratory (UL) each maintain their own well-recognized library of testing protocols. These standards apply to many different building situations and establish the accepted means for evaluating things like fire-resistance ratings among many others. Using these testing standards, manufacturers can have their products tested by independent labs and have the results reported. The codes identify the testing results required to show compliance.
Relatedly, manufacturers can submit their tested products for review to the ICC Evaluation Service (ICC-ES, a subsidiary of the International Code Council). Once reviewed and evaluated, an ICC-ES Evaluation Report can be generated which describes the details and conditions in which a particular product is found to be code-compliant and therefore consistent with safety standards.
Types of Construction
When designing any building, one of the first things that needs to be identified is the type of construction to be used as defined by the codes. Architects can choose which type to design and construct, but each choice comes with some requirements and restrictions. In some cases, the size (area) or height of the building will determine which Type(s) are acceptable for fire safety, particularly in site locations with local fire zone requirements. Chapter 6 of the 2021 IBC defines the Types, summarized as follows:
- Type I construction requires noncombustible materials for the primary building elements with two levels of fire resistance identified:
- Type IA – The primary structural frame and exterior and interior bearing walls must be noncombustible with 3 hours of tested fire resistance, which usually means masonry and concrete are used. Floor construction only requires 2 hours of fire-resistance rating, and roof construction requires only 1-1/2 hours of fire-resistance rating. If steel construction is used, it usually means that the steel structure is protected with spray-on fire protection products.
- Type IB – The difference between IA and IB is that IB allows slightly lower fire-resistance ratings of noncombustible assemblies with the primary structural frame and bearing walls rated at 2 hours, floor construction at 2 hours, and roof construction at 1 hour.
- Type II also needs to be constructed with noncombustible materials but they have lower fire resistance requirements than Type I.
- Type IIA includes the primary structural frame, bearing walls, and the floor and roof construction at only 1-hour rating.
- Type IIB does not require any fire-resistance rating for the structure, walls, floor, or roof; just noncombustible materials.
Exceptions to the above are identified in Section 603 of the IBC which addresses the use of permitted combustible products in Types I and II Construction, including the selective use of fire-retardant-treated wood for certain non-structural elements or secondary structural elements.
- Type III construction requires noncombustible materials only on the exterior walls while interior building elements can be of any code-permitted material, whether or not it is combustible. Fire-retardant-treated wood framing and sheathing are specifically identified and permitted within exterior wall assemblies with a 2-hour rating or less.
- Type IIIA includes a 2-hour rating for exterior walls, but only a 1-hour rating for the primary structural frame, interior bearing walls, and the floor and roof construction.
- Type IIIB only requires a 2-hour rating for exterior walls and no other fire rating for the structure, interior walls, floor, or roof.
- Type IIIB only requires a 2-hour rating for exterior walls and no other fire rating for the structure, interior walls, floor, or roof.
- Type IV construction includes mass timber elements combined with noncombustible materials based on the requirements of the sub-types. Note that the 2021 version of the IBC requires noncombustible material to be applied over exposed mass timber and some surfaces, “designed to increase the fire-resistance rating and delay the combustion of mass timber” in Types IV-A, IV-B, and IV-C construction, but not in Type IV-HT.
- Type IV-A – The primary structural frame and exterior and interior bearing walls must achieve 3 hours of tested fire resistance. That usually means masonry or concrete exterior walls and protected frame and interior bearing walls. The floor construction only requires 2 hours of fire-resistance rating, and the roof construction requires only 1-1/2 hours of fire-resistance rating.
- Type IV-B – The primary structural frame and all exterior and interior bearing walls need to be rated at 2 hours, floor construction at 2 hours, and roof construction at 1 hour.
- Type IV-C – has the same fire-resistance ratings as Type IV-B but has fewer requirements for noncombustible coverings or coatings.
- Type IV-HT construction calls for exterior walls to be of noncombustible materials while interior building elements are permitted to be of heavy timber construction including solid wood, laminated heavy timber, or structural composite lumber. Heavy timber must meet minimum size requirements such that it will char during a fire but retain its strength for at least the rated amount of time required. FRTW framing and sheathing assemblies are permitted in exterior walls with a 2-hour fire rating or less. Cross-laminated timber (CLT) is also permitted in exterior walls provided it is protected by FRTW sheathing, gypsum board, or a noncombustible material.
- Type V construction allows for the structural elements, exterior walls, and interior walls to be of any materials permitted by the code. Type V is commonly associated with conventional wood-framed residential construction.
- Type V-A requires buildings to have a 1-hour fire-resistance rating for the structural frame, exterior and interior bearing walls, floor construction, and roof construction, but not interior non-load bearing walls.
- Type V-B places no requirements for any fire ratings on any building elements.
The design professional of record can choose which construction type to use on any particular building provided that it is coordinated with the other requirements throughout the code for the selected type of construction. Those other requirements include building occupancy, fire protection requirements, size limitations, height restrictions, and other factors.
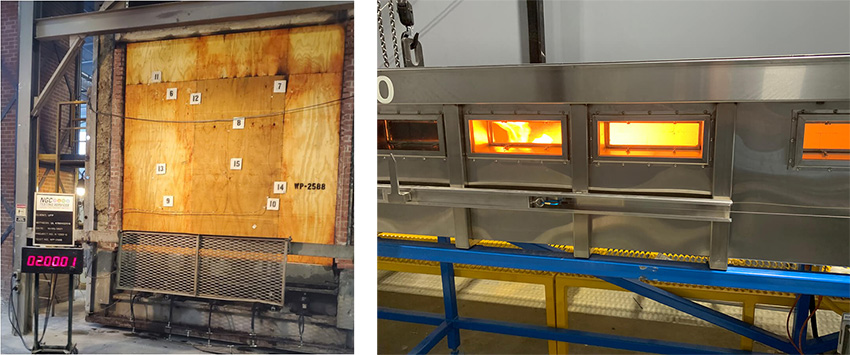
Photos courtesy of ProWood (left) and ICC (right)
A fire test using ASTM E-119/UL 263 at the end of 2 hours is reviewed against the test criteria to achieve a fire-resistance rating. For ASTM E84 testing, a Steiner Tunnel is used (shown on the right).
Construction Fire Ratings
In order to determine the fire-resistance ratings of materials and assemblies used in all construction types, independent fire testing is required based on accepted standards. There are two primary types of tests that the codes establish criteria for in order to be considered code-compliant.
- Materials or Assemblies: The most often cited test is ASTM E-119/UL 263, Standard Test Methods for Fire Tests of Building Construction and Materials. These test methods are intended to evaluate the duration that tested specimens contain a fire, retain their structural integrity, or exhibit both properties during a predetermined test exposure. An independent testing laboratory uses a specified assembly or component (i.e. wall, floor, ceiling, beam, column) and secures it to a testing furnace. A fire is started according to the testing protocols with a time clock recording the condition at the desired times (i.e., 1-hour, 2-hour, etc.). To pass the test, the wall cannot have burned through the tested surface, cannot exceed a specified increase in temperature (250 degrees F) on the exterior side, and cannot fail structurally due to the load being applied.
- Surface Effects: The codes are also concerned with the effects of fire on the surfaces of materials. ASTM E-84/ UL 723 Standard Test Method for Surface Burning Characteristics of Building Materials documents two fundamental things: First is to measure a flame spread index (FSI) using the required Steiner Tunnel test method. In order to meet code requirements, the product must be exposed to testing for 10 minutes with an FSI of 25 or less. Secondly, smoke development is measured at the 10-minute mark of the test. This uses a photometer to measure the concentration of smoke the sample emits as it burns. A smoke development index of 450 or less is required by the code for fire-retardant-treated wood.
Note that the test sample in this case is 2 feet wide x 24 feet long while the tunnel width is 17 inches so the edges of the sample sit on 3.5-inch-wide concrete. Metal batten strips are used perpendicular to the length on the top side of the sample to connect pieces of lumber or plywood that contain a 1/8-inch longitudinal gap down the center length of the sample. Each material and species combination is tested separately. In order to demonstrate a passing conformance, 2 of 3 tests must pass. The third test can be waived if the first two pass with consistent results.
- Extended Test: Flame Spread Index and Smoke Development are both first calculated at the initial 10-minute marks as noted above, but then the test needs to continue for an additional 20 minutes. In this extended 30-minute ASTM E84 test, the Flame Front is measured which is defined as the furthest distance the flame spreads across the surface of the sample. To comply with the code, the flame front cannot progress more than 10.5 feet at the 30-minute mark. The initial burner flame is 4.5 feet so that flame cannot extend more than an additional 6 feet at the 30-minute mark. (IBC 2303.2 Fire-Retardant-Treated Wood). The 30-minute E84 test is just one of many tests required in AC66 (Acceptance Criteria for Fire-Retardant-Treated Wood) in order to obtain an ICC-ES Code Compliant Report. Other testing evaluates strength properties and hygroscopicity.
Note that there is a new update in the 2021 version of the IBC related to ASTM E84/|UL 723 testing. It involves a change to the tests for plywood by requiring a horizontal rip cut that must be exposed during the test. For pressure-treated FRTW products, that should not be a problem since the treatment impregnates the wood. However, topical treatments are on the surface only and may not have the capability to meet this additional testing requirement–meaning it is not deemed as safe as the pressure-treated method.
In order to be code-compliant, construction materials, including FRTW, and assemblies must be tested and shown to meet minimum levels of performance. For example, UL has different category designations with the highest being FR-S, signifying minimal flame spread and smoke development. The tested products must then be labeled according to their level of performance. It is incumbent upon the manufacturer to ensure their products meet the testing requirements and then to label their products appropriately according to the requirements of IBC 2303.2.4 – Labeling.
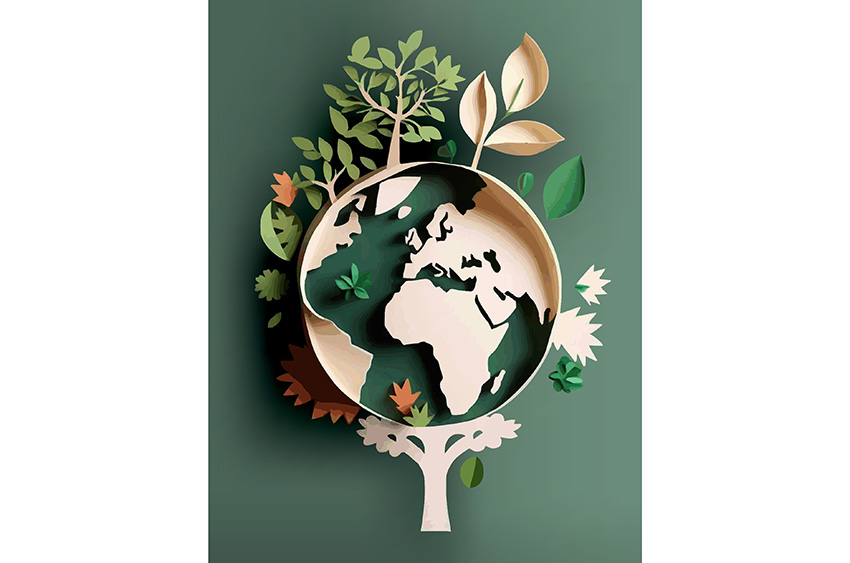
Image courtesy of ProWood
Wood building products are inherently more environmentally friendly than concrete or steel.
UNDERSTANDING FIRE-RETARDANT-TREATED WOOD
Low-rise construction is often based on wood framing and sheathing, including residential, light commercial, and mixed-use buildings. This is due to several factors. First, it is often the most economical choice that is easy to work with using well-known carpentry tools and methods. Second, wood is still one of the most environmentally friendly and energy/carbon-saving materials in construction. Finally, updates to the International Building Code (IBC) have recognized that wood members with larger mass or with fire-retardant treatment can be as safe or even safer than steel framing, which can lose its integrity during fires.
In light of all of the above, fire-retardant pressure-treated wood (FRTW) in the form of dimensional lumber and plywood or sheathing are now readily available which are code-compliant solutions for exterior and interior bearing walls, floor, and roofing assemblies. More specifically, FRTW is wood impregnated with chemicals during manufacture that has been tested under ASTM E-119/UL 263 and ASTM E84/UL 723 and meets the code required performance. While still considered a combustible material, code-acceptable FRTW can be used for 1-hour and 2-hour assemblies, does not support combustion, and its burning rate is appropriately limited when the flame is applied.
The greatest advantage of FRTW is its accepted use in a wide variety of building and construction types. It is permitted for use in types III, IV, and V construction for load-bearing walls, roofs, and floors within the specific parameters of the codes. It can also be used for non-structural items in Type I and II construction such as certain non-bearing partitions and walls plus most roof construction including girders, trusses, framing, decking, and some balconies, porches, decks, and exterior stairways.
Wood and the Environment
Wood is a natural, renewable resource that can be managed and harvested in a sustainable and responsible manner. That means it is a desirable and logical choice for construction whenever it can be used, particularly since it is often more economical than other alternatives such as steel and concrete. In the broader environmental sense, it has a much lower carbon footprint than steel or concrete construction. The natural process of photosynthesis while a tree is alive and growing is based on absorbing carbon dioxide from the atmosphere and storing (sequestering) it in the tree. As such, wood is considered by many to be the only truly carbon-neutral construction material in use. Steel and concrete require considerable amounts of fossil-fuel-based energy to extract, process, manufacture, and transport thus resulting in very high carbon footprints (i.e., very high levels of embodied carbon) for those building products. This has led to the growing popularity of wood construction in buildings.
Wood is also seen as a healthy and natural material, free from the concerns of other building materials that are synthetic or can contain harmful substances. In the case of FRTW, some manufacturers provide certifications related to green or sustainable standards, such as UL Greenguard Gold for low chemical emissions. Furthermore, wood does not conduct electricity, so it has no electrostatic charge associated with it. It also conducts less heat compared to concrete, steel, and aluminum, thus helping reduce energy consumption in buildings if designed into assemblies properly.
Producing FRTW
Fire-retardant treated wood is first and foremost a wood product with all the features and benefits of other wood construction products. Hence, the process of creating FRTW starts with obtaining untreated wood (dimensional lumber or plywood), typically made from a variety of Spruce, Pine, or Fir species. Note, however, that material and species cannot be mixed in a single treatment procedure. This wood then undergoes three primary steps, as follows.
- Treatment of Products: The untreated wood is impregnated with a blend of phosphate powder (the salt of phosphorus), boric acid powder, and water (for dilution). These are chosen because phosphorous is a common fire retardant used in other applications, too. When subjected to fire, the carbon dioxide reacts with these chemicals to create a char on the wood which insulates and suppresses the spread of fire and the development of smoke. When the treatment of the wood is done using a pressure process (Per IBC 2303.2.1), it must be performed in closed vessels under pressures not less than 50 pounds per square inch gauge (psig) (345 kPa). Remember that topical applications are also used by some manufacturers instead of the pressure treated process, but they don’t produce the same fire-retardant results. Therefore, such topical or coated products should be investigated for appropriateness and code compliance before specifying. Either way, fire-treated wood often contains a red/orange tinted dye for easy identification so it can be distinguished from non-treated wood on a construction jobsite. Certificates of Treatment are often issued for specific lots of material upon request or if specified.
It is typical for manufacturers of FRTW to incorporate a strict quality control process during all steps of the treatment. This can include a solution analysis of the mixed chemicals based on samples taken directly from mixing tanks and analyzed by a hydrometer. In some cases, chemicals to inhibit mold growth are added, so those are subjected to quality control as well. After treatment, lumber is drilled to verify the impregnation of the treatment based on 1/8-inch depth penetration and application of a two-part phosphorous indicator. Finally, documentation of quality control findings is recorded on a batch-by-batch basis for third-party inspection when requested.
- Kiln Drying After Treatment: The treated wood is moved from the pressure vessels to a kiln to be dried. It must be stickered to track each batch prior to entering the kiln and de-stickered after drying. Fire-retardant lumber must achieve a specified moisture content after treatment per the code. For lumber, this moisture content is not to exceed 19 percent, and for structural wood sheathing (plywood) not to exceed 15 percent. (IBC 2303.2.8) Spacers are placed between the wood to maximize airflow and proper drying. Fire-treated wood remains in the kiln until the specified moisture content is achieved.
- Protective Storage and Handling: In order to keep the fire-resistance treatment intact and to avoid any further absorption of moisture, the finished products are wrapped with protective wrappings. Stacks are separated by blocking for proper ventilation. The finished products are then stored and prepared for distribution to suppliers or project sites.
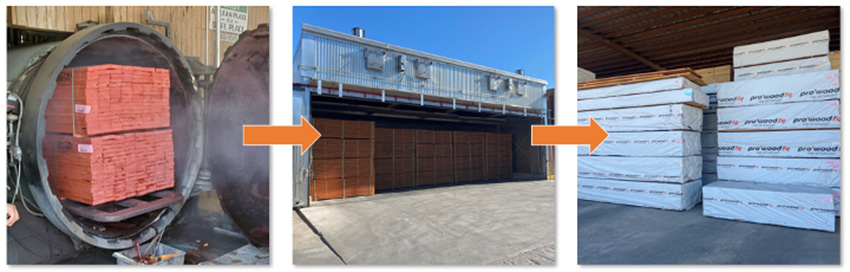
Photos courtesy of ProWood
The steps in the process of creating FRTW are 1.) pressure treatment 2.) kiln drying after treatment and 3.) protective (wrapped) storage and handling.
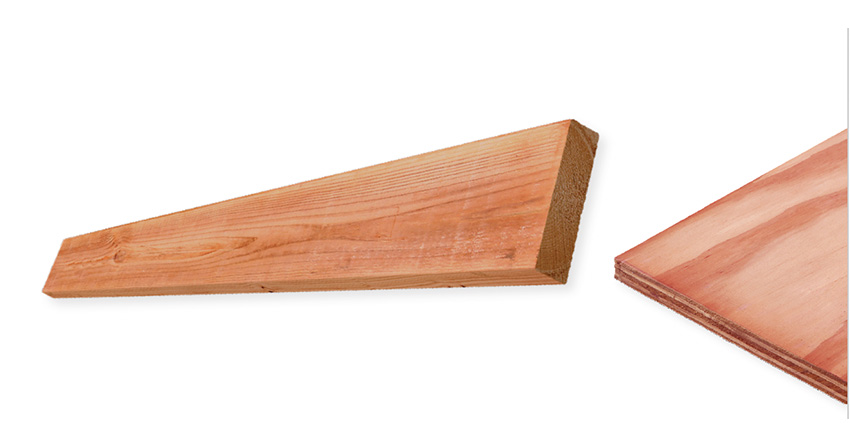
Photos courtesy of ProWood
The two primary FRTW products are dimensioned lumber and plywood.
Structural Considerations
It must be noted that the treatment process can affect the physical and structural properties of the wood. Depending on the wood species (spruce, pine, fir, etc.), the type of product (stud, joist, plywood, beam), and its application (wall, floor, roof), the structural strength originally associated with the untreated wood is reduced somewhat when subjected to the fire-retardant process described above. Therefore, the FRTW manufacturer is required to provide strength adjustments based on the intended use of the wood which must be factored into the structural design of the building.
The structural durability of FRT lumber and plywood is best verified according to the latest and most stringent versions of ASTM strength durability standards. FRTW is routinely tested by independent accredited laboratories, following two directly relevant industry standards: 1.) ASTM D5664 Standard Test Method for Evaluating the Effects of Fire-Retardant Treatments and Elevated Temperatures on Strength Properties of Fire-Retardant Treated Lumber and 2.) ASTM D5516 Standard Test Method for Evaluating the Flexural Properties of Fire-Retardant Treated Softwood Plywood Exposed to Elevated Temperatures. These tests are used to develop strength design factors of fire-retardant treated lumber and plywood, respectively, for various use conditions in buildings and elsewhere.
The National Design Specifications (NDS), Wood Handbook, and other publications have cautioned against the use of any wood product in environments exceeding 150˚F. Based on the strength data generated when tested per industry protocol at an accredited third-party laboratory, professional engineers have calculated design values and span adjustments to modify the untreated design values for lumber and span ratings for plywood. These design values are applicable at temperatures up to 150˚F for lumber and 170˚F for plywood.
Because of these considerations, it is appropriate to request the relevant structural data from manufacturers for their particular products. Commonly, FRT plywood needs to be slightly thicker (approximately 1/8”) than untreated plywood for the same structural application. Dimensional lumber may also have some minor span and strength limitations, although in most cases, it is not a significant design issue.
DESIGNING WITH FRTW IN BUILDINGS
As already noted, building codes allow FRTW to be used in multiple locations in buildings to satisfy structural and fire resistance needs. In particular, both FRT dimensional lumber and plywood can be considered for use by design professionals in some specific locations in buildings.
- Dimensional FRT lumber can be used for all stud framing in partitions and walls where permitted including studs, sill plates, sole plates, jack studs, and headers. It is also suitable for blocking and backers in wood or metal stud framed walls in all building types. It can also be used for roof systems including roof trusses, rafters and related framing and blocking. Floor systems can benefit with floor trusses, floor joists and framing all potential uses of treated lumber. Dimensional FRT lumber can also be used to create various other carpentry items, such as built-up beams, stairs, and millwork.
- FRT plywood can similarly be used for sheathing and enclosure of framed systems including exterior wall sheathing, roof sheathing over trusses or rafters, and floor sheathing/ subflooring. It can also be used on interior or exterior walls for non-structural sheathing or backer boards such as for mounting electrical or other equipment.
In short, FRT products can be used virtually anywhere that untreated wood products can be used, within the parameters of the applicable code requirements.
Typical Wall Assemblies Using FRTW
Like most construction assemblies that are tested for fire resistance, those using FRTW are specifically assembled per typical construction techniques and tested according to the relevant testing standards. Typical exterior wall assemblies are based on FRT 2x4 framing at 16” on center or FRT 2x6 framing at 24” on center plus FRT plywood used as exterior sheathing. Standard batt insulation is assumed between the framing members. The exterior may or may not include house wrap or other air and water membranes plus any common exterior facing. The interior is presumed to be finished with gypsum board (drywall) – 1 layer for a 1-hour fire-resistance rating and 2 layers for a 2-hour fire-resistance rating. Wall assemblies such as these have commonly been tested by UL labs and others and include the details of the parameters of the testing including fasteners, gypsum finish, etc. that need to be included. Copies of these tested assemblies are routinely available from manufacturers.
Sometimes, a question may arise regarding the intersection of a floor assembly with an exterior wall assembly. As we have seen, it is not uncommon for the code to require a 2-hour exterior wall, acceptably built using FRTW, but only requires a 1-hour rated floor or roof. The question then pertains to the intersection of the wall and the floor or roof and how to ensure the proper fire rating is maintained. Flooring and roof members need to rest on or be connected to the wall so it is that area of overlapping or intersecting construction that may be a design concern. If, for example, a 1-hour rated floor can be constructed without using FRTW, but a 2-hour rated exterior wall does need to be FRTW, does the intersecting portion of the floor also need to be FRTW? Those who have looked at this question closely rely on the intent of the code which, in this case, is to contain or compartmentalize fire within a space. The concern is with the interior spaces defined by either the wall sheathing or ceiling sheathing for the floor or roof. The conclusion is that as long as the wall and floor or roof assemblies each meet their independently required fire-resistance ratings, they comply with the code since the continuity of the interior surfaces is maintained.

images courtesy of ProWood
FRTW can be used as the basis for structural walls with either a 1-hour or 2-hour rated assembly as documented by accepted testing standards.
Specifying FRTW
Specifying FRTW is directly linked to its manufacturing process, codes, and testing standards. There are several considerations to address when writing specifications that include it.
- Quality Control: Documentation of a manufacturer’s quality control program for specified FRTW products should be available from manufacturers. Similarly, it is common for a 50-year Limited Warranty to be available against structural failure. Typically, such a warranty protects against a reduction in strength caused by the fire-retardant chemicals.
- Testing: A full range of product testing is recommended, beyond the fire rating tests already mentioned. In particular, hygroscopicity testing conducted by a third-party independent laboratory is the best way to confirm that, compared to untreated wood, fire-retardant-treated wood does not pick up excessive moisture under test conditions. A more complete list of testing includes the following:
- ASTM E84/ UL 723 Surface Burning Characteristics
- ASTM 2768 Extended 30-minute Test
- ASTM E119 Fire Tests of Building Construction
- ASTM D3201 Hygroscopic Properties
- ASTM D5516 Flexural Properties Plywood
- ASTMM D5664 Flexural Properties Lumber
- ASTM D6305 Strength Design
- ASTM D6841 Treatment Adjustment Factors
- AWPA E12 Determining Corrosion of Metal
- AWPA M4 Care of Treated Wood
- AWPA P50 Standard for Fire-retardants
- AWPA T1 Treatment Standard
- On-Site Storage and Handling: Exposure to precipitation or moisture during storage and installation must be avoided since FRTW is not intended for exterior exposure or applications. If any FRTW product becomes wet, it must be allowed to dry before enclosing it in construction. Finished products should be wrapped or bagged and stored 6 inches off the ground and under cover whenever possible. It is best practice to store all FRTW in a dry, covered space on a job site.
- Products: FRTW is available in a wide range of softwood species including Spruce-Pine-Fir, White Spruce, Red Spruce, Engelmann Spruce, Black Spruce; Southern Pine, Lodgepole Pine, Red Pine, Ponderosa Pine, Jack Pine; Douglas Fir, Alpine Fir, White Fir, Balsam Fir, Hem Fir, and Western Hemlock. Only fire-retardant-treated wood that is visibly clean and free of surface residue should be used.
- Labeling: FRT lumber and plywood products need to be clearly identified. Each piece shall be stamped with the critical information required by building code authorities including the UL FR-S designation and any ICC-ES report number. Additionally, all FRTW products should be color-tinted for easy identification on the job site.
- Installation: Structural systems, which include FRT treated lumber or plywood, should be designed and installed in accordance with the adopted building code using the appropriate lumber design adjustment factors and plywood spans from manufacturers’ structural testing information.
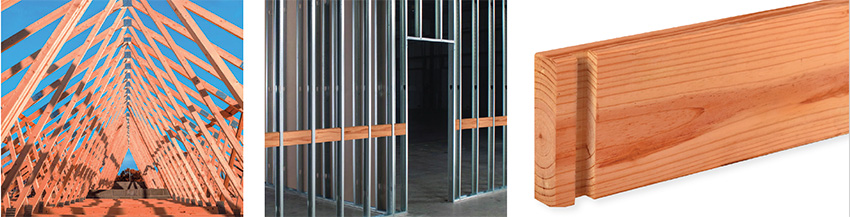
Photos courtesy of ProWood
Installing FRTW in buildings can take many forms in walls, floors, roofs, and even interior blocking and backing.
FRTW is not permitted for applications where the material may be exposed to precipitation, direct wetting, or regular condensation, and should never be used in contact with the ground. Ventilation should be provided in compliance with the applicable codes in force at the time of construction. If the wood is to be used in an interior application and becomes wet during construction, it should be allowed to dry before being covered or enclosed.
Typical joining cuts, end cuts, and drilled holes will not adversely affect the fire performance of FRTW, and no field treatment is required to maintain flame spread ratings. However, ripping or milling of FRT lumber is not permitted, as these operations could adversely affect the surface burning characteristics, however, end cuts are permitted. FRT plywood can be ripped as required. FRTW plywood can be cut along either dimension.
Fasteners: The fasteners used in FRTW must be selected to avoid corrosion or degradation from either the treatment chemicals or the installation conditions. Therefore, galvanized steel, stainless steel, silicon bronze or copper, in accordance with applicable sections of the IBC must be used. Even though the FR treatment may not increase corrosion of bare or galvanized steel, galvanizing provides an added level of protection with any treated wood product. The fasteners may also be subject to design value adjustments when specific products are evaluated using an ICC Evaluation Service (ICC-ES) report.
- Jobsite Safety: Some of the safety recommendations of manufacturers of FRTW include the following.
- Do not burn fire-retardant-treated wood.
- Wear NIOSH N95 dust mask and goggles when cutting or sanding wood.
- Wear gloves when working with wood. Some fire-retardant-treated wood chemicals may migrate from the treated wood into soil/water or may dislodge from the treated wood surface upon contact with skin - Wash exposed skin areas thoroughly.
- Wash work clothes separately from other household clothing before reuse.
- Fire-retardant-treated wood should not be used where it may come into direct or indirect contact with drinking water.
- Do not use fire-retardant-treated wood where it may become a component of food, animal feed, or beehives.
- Do not use fire-retardant-treated wood as mulch.
- Waste Disposal: All sawdust and construction debris should be cleaned up and disposed of after construction. Fire-retardant-treated wood may be disposed of in landfills or burned in commercial or industrial incinerators or boilers in accordance with federal, state, and local regulations.
- Finishing: FRTW that is visible in construction or otherwise in need of a finish can be covered using most conventional wood finishing methods. Under normal temperature and humidity conditions, latex, and oil-based paints, as well as water- and solvent-based stains, can be used with FRTW. If prolonged exposure to high humidity conditions is expected, special surface preparation procedures including the use of an appropriate primer are recommended. Before applying any finish, the wood surface should be lightly sanded, cleaned and dry. For the best results, always follow the coating manufacturer’s label instructions.
- Maintenance: Mold growth can and does occur on the surface of many products, including untreated and fire-retardant-treated wood, during prolonged surface exposure to excessive moisture. To remove mold from the treated wood surface, wood should be allowed to dry. Typically, mild soap and water can be used to remove the remaining surface mold.
CONCLUSION
Buildings of all types need to address fire safety. While different combinations of materials and structural systems are possible under the codes and widely used, FRTW is seen as a proven and often preferred material to achieve a readily constructible and fire-tested solution. The end result is that incorporating FRTW into wall and roof assemblies can help make the difference in providing greater safety and lowering the number of casualties due to fire in all types of buildings.
Peter J. Arsenault, FAIA, NCARB, LEED AP is a nationally known architect and a prolific author advancing safer buildings by design. www.pjaarch.com, www.linkedin.com/in/pjaarch