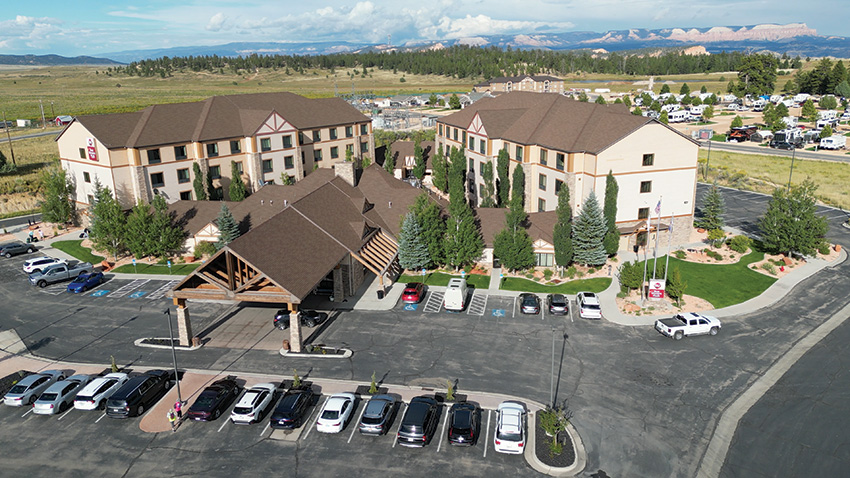
Photo courtesy of Propane Education & Research Council
While breakdowns in the hot water system once plagued Ruby’s Inn near Bryce Canyon in Utah, a tankless hot water system retrofit solved the problem.
A steady flow of hot water is like good health; you don't appreciate it until it's gone. Hot water is critically needed in commercial operations, where its absence can mean the difference between making a profit or not, keeping the doors open or closing up shop. How can a hotel, restaurant, fitness center, hospital, care center, school, or other facilities stay open without hot water? They can't. Still, threats to a steady supply of hot water plague establishments daily: aging storage tank systems, overloaded systems, broken systems, and more.
Considering the critical need for hot water in commercial operations, architects, designers, specifiers, and property managers should understand what can go wrong when the flow of hot water lessens or stops, and the potential for natural gas or propane tankless water heaters—which also save energy, money, and space—to solve the problem.
THE PROBLEM: LACK OF HOT WATER = DISGRUNTLED CUSTOMERS
Consider this situation at a historic, sprawling establishment in Utah. When up to six tour busses simultaneously roll up to the iconic Ruby's Inn complex on the edge of Bryce Canyon National Park, the travelers tumbling out of the busses usually want one thing above all: a hot shower. Upon arrival, the visitors would not be aware of the strain that dozens of concurrent showers put on the tanks of a conventional hot water system. The visitors would not know about the tons of laundry done by the staff every day. They wouldn’t realize that Ruby's Inn is 25 miles from the nearest natural gas line. The customers have likely been on a bus for hours. They simply want hot showers when they arrive. But if the massive complex with hundreds of hotel rooms and an RV park fails to deliver the required hot water, bad reviews and refund requests are sure to follow.
That is where the business found itself several years ago with a faulty and failing storage tank hot water system. The inn was founded in 1916, long before Bryce Canyon was a national park. Over the decades, the inn expanded and rebuilt to its current size of more than 700 hotel rooms and other amenities. That equals a massive demand for hot water and colossal repercussions when that hot water supply fails. The inn operators searched for a solution that would provide a more effective water heating system.
"Our goal was a reduction in the discounts we had to give," said Ron Harris, part of the management team at Ruby's Inn. "We had to completely refund a room and sometimes an entire building block because guests took a cold shower in the morning. We looked at about $60,000 a year in discounts and refunds." And with the refunds came less-than-favorable reviews. "Couldn't get water to a comfortable temperature," or "The water was barely warm," said reviewers on Trip Advisor in 2011.
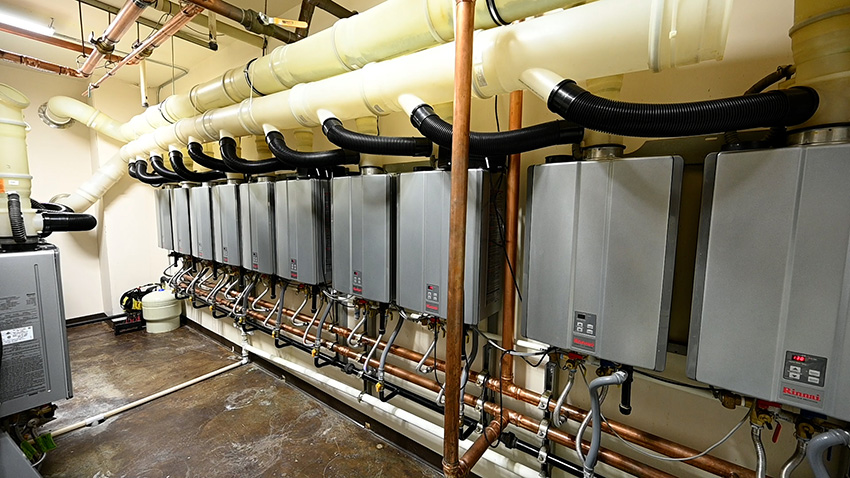
Photo courtesy of Propane Education & Research Council
An array of tankless water heaters at Ruby’s Inn saves energy and space and provides reliability to keep the establishment running smoothly.
The Solution: Propane Tankless Water Heating Retrofit
All those complaints stopped a few years ago when Ruby's Inn underwent a retrofit of its hot water delivery system. The solution ultimately included 175 new propane tankless water heaters with 35 tankless rack systems and four hybrid commercial water heating systems. With the more efficient tankless units in place, the resort has had no issues with hot-water supply or customer complaints, freeing staff time and money for other efforts at the resort. And perhaps just as importantly, Ruby's Inn saves about $6,000 per month on propane alone.
The online reviews of Ruby's Inn have certainly brightened in tone. "There was plenty of hot water," stated a reviewer on TripAdvisor in 2024, and "The water pressure in the shower was unbelievable and so hot that you hated to get out!" wrote another satisfied guest in 2023.
THE HISTORY OF HOT WATER
Hot water provides thermal comfort, a means of cooking, and cleanliness. To get these benefits, some ancient humans settled near hot springs, which naturally created and stored hot water. When Homo erectus learned to harness the power of fire around 1 million years ago, they heated water using skins on a stone-lined fire pit. Indigenous Americans heated stones in a fire pit and then transferred them to a container of water.
In ancient Greece, circa 5th century B.C., Homer and other Greek writers told us the Greeks, for whom athleticism was paramount, favored a variety of public baths for health and relaxation. During the Roman Empire, starting around the 1st Century BC, the Romans expanded the concept of public baths. According to historical studies, Roman baths were open to all citizens and allowed them to relax, mingle, and gossip, with separate baths for women and men. The baths consisted of heated rooms and pools, many sited to harness the sun's heat. Some systems, called hypocausts, employed water heated in fiery wood-burning furnaces beneath the raised floors of the baths. The resulting steam rose through chambers beneath the floors. Tiles and decorative mosaics lined the floors.
Public baths in the style of the Greeks and Romans did not catch on in the United States, partly because of taboos toward public nudity. Early American bathing focused on the "Saturday bath," a tin tub drawn into the kitchen and filled with water heated on the stove where family members took turns getting clean, presumably in preparation for Sunday church.
Invention of Tank-Style Gas Water Heater
In 1889, a Norwegian immigrant in Philadelphia named Edwin Ruud invented the first automatic tank-style gas water heater. Advertisements at the time touted that water heating was no longer tied to the kitchen stove but was done in the basement, and you didn't even have to light a match. It was called a "mechanical masterpiece." After that, heating and storing large amounts of water in tanks until it was needed became the norm. The sound of a water heater firing off and on during all hours to keep the water within 10 percent of the thermostat setting until needed became a familiar scenario and a virtually non-stop consumption of natural gas, propane, or electricity.
However, while large hot water tanks in home basements improved domestic life, the same strategy to heat and store massive amounts of water for commercial operations has become problematic regarding reliability, energy efficiency, and space required.
THREATS TO HOT WATER IN COMMERCIAL OPERATIONS
Try for a moment to imagine any of the following establishments operating without a steady flow of heated water:
- Hotels, resorts, and spas
- Restaurants and bars
- Commercial kitchens
- Retail restrooms
- Schools and dormitories
- Fitness centers
- Laundromats
- Long-term care facilities
- Hospitals and clinics
- Industrial facilities
Without this vital feature, these establishments would be unable to function. So, what causes problems with the critical delivery of hot water when it's needed? Most often, problems stem from issues with the old-style storage tank systems.
Unreliability: What happens when tank systems fail, or there is more demand than supply? In the service industry, customer complaints are expensive and harmful to the company's reputation. While a few family members in a home might wait for a water heater to recover before taking a shower or doing laundry, that is not an option in commercial operations. Imagine employees in a manufacturing facility waiting to wash their hands until the system renews itself.
Lack of Longevity: According to the U.S. Dept. of Energy, storage water heaters have a lifespan of 10 to 15 years.1 That can be as little as seven years if the tank is not maintained by flushing and replacing the sacrificial anode designed to counteract minerals that can eat away the inside wall of the tank. And commercial tank-style water heaters can fail even more often. Consider what happens in a hotel or restaurant when the hot water system goes out, and the operation grinds to a halt. Those affected include employees, suppliers, customers, and all ancillary operations. Huge impacts follow. Unfortunately, replacing a failing storage tank with a new one is no easy task. Large machinery might be needed to lift a large tank out. Scheduling that machinery and the crew required to make the switch complicates and potentially lengthens the outage.
Inefficiency: The U.S. Dept. of Energy (DOE) states that the energy usage of storage tank systems is up to 34 percent more than the energy used for tankless systems, with increased resulting in operational costs and higher emissions. According to the DOE: If all commercial water heaters sold in the U.S. were ENERGY STAR certified, the energy cost savings would grow to nearly $890 million, and more than 17 billion pounds of annual greenhouse gas emissions would be prevented.
In a commercial example, the Worldmark Anaheim, a 246-unit hotel close to Disneyland, reduced its natural gas consumption by 30 percent after switching to a tankless system." In another example, Ruby's Inn in Utah saves about 7,000 gallons of propane each month after upgrading from tank water storage units to tankless systems.
Square footage needed: Boilers and tank-style water heaters are bulky with a large footprint and take up a correspondingly large area, along with required clearances to provide space for repair and maintenance personnel. question3}
FEATURES AND BENEFITS OF TANKLESS HOT WATER SYSTEMS
Just as Ruby's Inn evolved with the times, so too has the reliable production of hot water. Over the past 10 to 15 years, commercial tankless water heaters have evolved from an obscure and novel option to emerge as a growing mainstream water-heating specification. Commercial tankless water heaters have the versatility to meet a wide range of load types while offering reliability, energy-efficient performance, and a space-saving footprint. They're available in various capacities and can be combined into larger arrays for water output rates of several hundred gallons per minute. And they don't waste energy or space by keeping a large water tank hot at all hours.
How Tankless Systems Boost Performance in Commercial Buildings
Instead of storing water, tankless systems use a heat exchanger to heat water as it's needed in a building. For example, when a guest turns on a shower in a hotel, a propane or natural gas burner in the tankless unit quickly heats the heat exchanger. In very high-efficiency condensing models, incoming cold water is preheated from the combustion exhaust. Then, the water continues to be heated as it passes through the unit's heat exchanger and exits from the tankless unit at the hot-water outlet pipe, where it then flows to the shower or sink to meet the hot-water demand.
These impacts are significantly reduced when tankless systems are used. Generally speaking, systems that last 20 years or more–such as tankless water heating systems–help prevent interruptions to the facility.
Types of Commercial Tankless Water Heaters
Commercial tankless water heaters can be divided into two types: natural gas and propane powered, and electric powered. Gas and propane powered units are typically more energy efficient and cost efficient to run. Less propane is needed than natural gas to heat water. Gas and propane powered units can continue to operate in a power outage. Gas and propane powered units can further be divided into condensing units and non-condensing units. Condensing tankless water heaters use advanced condensing technology to transfer energy from exhaust gases before they are vented to the water, which makes them more efficient than non-condensing tankless water heater.
Flexibility for Peaks and Dips
One of the most important benefits of using tankless technology in commercial buildings is its flexibility in meeting a wide range of load types. Whereas a storage tank system has to be designed for a building's peak load and keep a full tank constantly heated, a tankless system can rely on just a portion of the tankless units during off-peak times. The tankless water heater can increase its combustion rate as the hot-water demand increases. When demand gets even higher, the system controller will turn on another tankless unit and share the demand across both units.
That means a system could be designed for a large peak load that requires several hundred gallons per minute of hot-water output but still responds well when only a tiny portion of that hot water is needed. Hotels are a particularly common use case for this strategy, says Jamie Lyons, a senior consultant with Newport Partners.
"Even though the peak demand for hot water happens really infrequently, they still have to be ready for it, or else they have unhappy customers," Lyons said. "The value proposition for tankless there is really strong because you can use an array of tankless units that can ramp up to meet the peak when it happens, even if it only happens a really small percentage of the time. You're ready for it, but you're not storing hundreds or thousands of gallons of hot water all the time."
Advanced technology is part of the equation. Instead of simply keeping water hot in a large storage tank, tankless systems use sophisticated controls to modulate the heating capacity of an individual unit higher or lower to meet the demand for hot water. In addition to the system bringing on additional units to share the load and increase output, the controller also spreads the duty cycle out so that one unit won't wear out before the rest.
At the Residence Inn by Marriott in Anaheim, California, for instance, the 17-unit tankless array includes 12 units to supply hot water to the 130 guest rooms and five units for the hotel's dining and laundry operations. Each tankless unit has a capacity of just under 200,000 Btus per hour. Because each individual tankless unit can modulate as low as 11,000 Btus per hour, the overall system has a huge capacity range from over 3 million down to 11,000 Btus per hour.
Space Saving Flexibility
The days of giant boiler and water tank rooms are diminishing. Building owners and operators need to maximize space to provide key functions and services, whether a building is a hotel, restaurant, school, or brewery. Because they don't store water, tankless water heaters are by nature compact. Commercial tankless arrays can be free-standing, wall-mounted, installed in corner layouts, or even located outside the building. They can even be integrated with a storage tank for staged, planned replacements of old tank-style water heaters.
In commercial spaces, every square foot means income potential. Considering that tankless systems require up to 80 percent less space than storage tank units, this can substantially increase available square footage. Realizing these space savings can benefit a retrofit project, and that flexibility can also be helpful in new construction.
For example, the initial plans for a new student apartment complex for Utah Valley University in Orem called for multiple water heaters and 5,000-gallon storage tanks. However, after realizing the potential for saving space, the plans switched to tankless water heaters. Today, eight tankless units with a total capacity of 14,500,000 Btu per hour supply generous hot water for the 450-unit complex while taking up much less square footage. This smaller footprint allows the university to use the extra space for several priorities, including residential and office space, other amenities, and a place to store the snow-melting equipment.
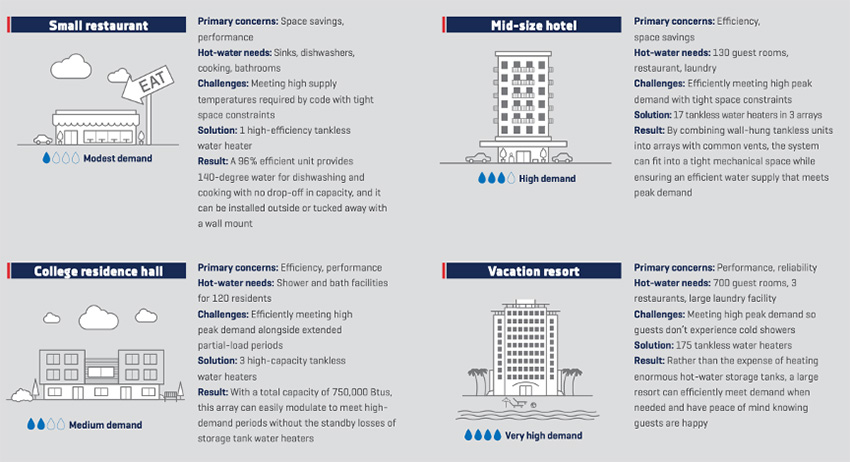
Graphic courtesy of Propane Education & Research Council
Tankless water heating's flexibility means arrays can be configured to provide reliable hot water to a small restaurant, a mid-size hotel, a college dorm, or a vacation resort. These are real-life examples.
Tankless Water Heater Arrays
In many commercial tankless systems, the capacity of an individual tankless unit is roughly 199,000 Btus. By combining these units in larger configurations, tankless arrays can provide hot-water output rates of several hundred gallons per minute. Tankless units can be arranged in self-supporting or wall-mounted racks, depending on the project's needs. Linking a system of multiple tankless water heaters together used to be a time-consuming process for contractors. But in recent years, manufacturers have simplified the process with tankless water heater arrays or racks: free-standing or wall-mounted multi-unit systems shipped to projects fully assembled, including gas and water manifolds. Depending on the application, manufacturers can customize these arrays to prioritize reliability, space savings, energy efficiency, or first-hour water delivery, including combining tankless units with storage tanks where appropriate. That's a vital service, as different types of commercial buildings have vastly different needs.
Venting Options
Propane and natural gas tankless water heaters require venting to exhaust combustion gases, and manufacturers offer a variety of venting innovations to simplify installation. For example, multiple units can use a common vent system that reduces space needs, labor and materials, and building penetrations. Traditional tank gas water heaters vent through the roof through a natural draft, with the hot exhaust air rising up and out of the building. Tankless water heaters' vents, by contrast, can terminate on a side wall because their combustion fans blow exhaust from the units horizontally or vertically. That fact is particularly helpful when remodelers or professionals replace expensive-to-operate electric tanks (which don't require venting) with natural gas or propane tankless units.
Installing a tankless water heater outdoors in warmer climates is simple, with no additional venting required. Replacing a tank water heater with an outdoor tankless system can also free up indoor floor space, with up to 9 square feet freed up on the floor. Tankless units are designed to withstand below-freezing temperatures through self-warming capabilities that prevent freezing and cracking. However, indoor installations are a better option in freezing climates where electrical outages occur.
While commercial and large residential applications may use multiple tankless units, they don't necessarily require two vent penetrations per unit. Manufacturers have developed a common-venting system that uses a manifold to share the same exhaust and intake vents for multiple tankless units, a useful option for projects where architects and builders want to avoid extra penetrations in the building envelope for practical or aesthetic reasons.
Flexible systems for Various Applications
Here are examples that show the flexibility for various commercial scenarios:
Planning a Retrofit/Replacement Before an Emergency
Just as hot water demand typically peaks during a 24-hour period, the demands on the commercial operation also ebb and flow. In a dormitory, demand peaks during the school semester and lessens during holidays and seasonal breaks. In hospitality, demands are greatest during certain months and less during others, depending on the weather patterns, holidays, and nearby events. Because of this ebb and flow in demand, the retrofit or replacement of an aging or inefficient hot water system can be planned to correspond with the low season so that an emergency doesn't occur during the high season when the stakes are more significant. Planning the retrofit allows ample time to determine the right system for the application.
Planning a retrofit could mean the difference between intentionally upgrading the system to save energy and space and increase reliability or hastily replicating the old system in a crisis. The National Renewable Energy Laboratory (NREL) notes there are several barriers when a system replacement is not planned. "The often-immediate need for a new water heater can be a serious obstacle to the adoption of energy-efficient technologies. Thirty percent of all water heaters are purchased because the previous unit has failed catastrophically; a customer rarely performs an extensive search for an efficient water heater in this case and instead takes whatever is 'on the truck.'"
Before a planned replacement, here are the issues that are considered:
- What is being replaced?
- What space is available?
- What is the coldest water temperature inlet?
- What is the desired hot temperature outlet?
- What is the tankless unit BTU?
- What is the unit efficiency?
- What is the highest peak GPM (gallons per minute)?
- What is the building piping distribution sizing?
- What is the gas capacity available?
Because the planned retrofit will negatively impact fewer people than an emergency, a planned retrofit/replacement layout is less expensive than an emergency replacement.
TAX DEDUCTIONS
Under the Inflation Reduction Act of 2022, tax deductions may be available. As the provision states: "Building owners who place in service energy efficient commercial building property (EECBP) or energy efficient commercial building retrofit property (EEBRP) may be able to claim a tax deduction. An increased deduction may be available for increased energy savings or meeting prevailing wage and apprenticeship requirements. The deduction is allowed under Internal Revenue Code (IRC) Section 179D. It was expanded under the Inflation Reduction Act of 2022."2
EECBP must be installed on or in a building that is located in the U.S. and within the scope of a specified Reference Standard 90.1 of the American Society of Heating, Refrigerating, and Air Conditioning Engineers (ASHRAE) and the Illuminating Engineering Society of North America. It must be property for which depreciation or amortization is allowable, and installed as part of:
- the interior lighting systems,
- the heating, cooling, ventilation, and hot water systems, or
- the building envelope.
It must be certified as being installed as part of a plan to reduce the total annual energy and power costs for the above systems by 25 percent or more compared to a reference building meeting the minimum requirements of Reference Standard 90.1.
EEBRP must also be installed on or in a qualified building as part of:
- the interior lighting systems;
- the heating, cooling, ventilation, and hot water systems; or
- the building envelope.
A qualified building is a building located in the U.S. that was originally placed in service not less than five years before the establishment of a qualified retrofit plan for the building. EEBRP must be property for which depreciation or amortization is allowable, and it must be certified as meeting certain energy saving requirements."
MYTHS AND REALITIES OF TANKLESS HOT WATER SYSTEMS
Tankless systems have been well integrated into European and Japanese markets for decades. In North America, the transition to tankless is gaining traction. Still, there remain some misperceptions about the technology. Here are some common myths and corresponding realities about tankless hot water systems:
Myth: Tankless systems require complicated venting.
Reality: Tankless systems vent differently from tank systems, but it's not complicated. Tankless systems can vent directly out a side wall, preventing excess roof penetrations. In the southern part of the country, tankless systems can be mounted outside. For large arrays, several units can vent into the same configuration.
Myth: Zero-net-energy goals require all electric equipment.
Reality: Multiple energy sources working in partnership help achieve emissions goals. Propane, for example, is one such partner in achieving zero-net-energy goals.
Myth: Tankless systems are more expensive
Reality: Tankless systems can be more expensive initially. But savings in energy can recoup that investment in a few years. And when rebates and incentives are factored in, there may be no initial cost difference.
Myth: Electric water heating is the only option when a natural gas main is difficult or expensive to reach.
Reality: Many architects, builders, and property managers don't realize that propane can be available on any type of building site, making gas tankless water heaters a possibility even when natural gas isn't available. If desired, they can get their local propane company not just to bury underground tanks, but, in big developments, they'll put in the underground piping so that it works like a natural gas system. Virtually all tankless units are field-convertible from natural gas to propane or vice versa, so a facility could be developed or retrofitted with propane and switched to natural gas if it becomes available later.
INNOVATIONS AND THE FUTURE OF TANKLESS WATER HEATING
Innovations in tankless water heating systems will surely accelerate in the future as they have in the recent past. Consider these cutting-edge developments:
Commercial Hybrid Water Heaters
Commercial hybrid water-heating systems combine a tankless water heater's on-demand, continuous hot-water supply with a hot-water storage tank. Although tankless water heaters have made inroads in the commercial market in recent years, storage tank water heaters remain the predominant technology. Hybrid systems combine the best of both worlds—installing just like a storage tank to easily replace old units but performing like a tankless water heater with a continuous flow of hot water. That means hybrid units provide more hot water in the first hour than other systems on the market and have a faster recovery time than a traditional storage tank system.
Artificial intelligence (AI), Smart Controls, and Larger Capacities
Computerized controls allow even sizeable tankless water heater arrays to precisely track the water-heating load of a building and activate individual units accordingly. Those controls allow the tankless system to ramp up to meet a building's peak load and then ramp back down so just a single unit is active.
Today, commercial tankless water heaters have joined other building technologies in offering wireless connectivity and remote monitoring and controls. Many units offer smartphone or app-based connectivity to provide facility managers or contractors with mobile access to their units.
Tankless water heaters even utilize artificial intelligence. One manufacturer touts AI built into its units that analyzes a building's hot-water usage patterns, identifying and predicting the timing of peak loads so that the units can fire up and activate a building's recirculation system in preparation for the higher hot-water demand. The manufacturer also offers larger on-demand systems with individual unit heating capacity up to 3 million Btus.
CONCLUSION
Architects and contractors should consider tankless systems when specifying for new construction or renovations, as hot water is such a critical factor in commercial operations. Tankless systems, mainly propane or natural gas units, use less energy, require less space, and can last up to three times longer than conventional tank systems. Most importantly, when the system is sized correctly, there is never a shortage of hot water. The facts show that keeping hundreds of gallons of water heated day and night for a short-lived demand spike is inefficient. On-demand systems remove this problem. With today's thin margins and competition, commercial facilities cannot stand the stress of a failing hot water system. A propane or natural gas tankless system often creates the winning solution.
END NOTES
1 "Everything You Need to Know About Water Heaters". U.S. Dept. of Energy. 19 April 2013. Web. 11 April 2024.
2 "Energy Efficient Commercial Buildings Deduction". U.S. Internal Revenue System. 8 August 2023. Web. 11 April 2024.
Kathy Price-Robinson is a nationally known remodeling and construction writer. Her award winning remodeling series titled Pardon Our Dust ran for 12 years in the Los Angeles Times.