This CE Center article is no longer eligible for receiving credits.
There is a common misconception in the design and construction industry that insulated metal panels, often referred to as IMPs, are only suited to provide a solution for an exterior wall in the building envelope. This unfortunate misunderstanding unnecessarily limits designers to roof systems such as traditional built-up and single-membrane roofs with limited service life spans, or traditional metal roofs with independent thermal and moisture barriers that must be detailed and installed as separate materials and might suffer from installation mistakes that compromise the thermal performance or moisture management.
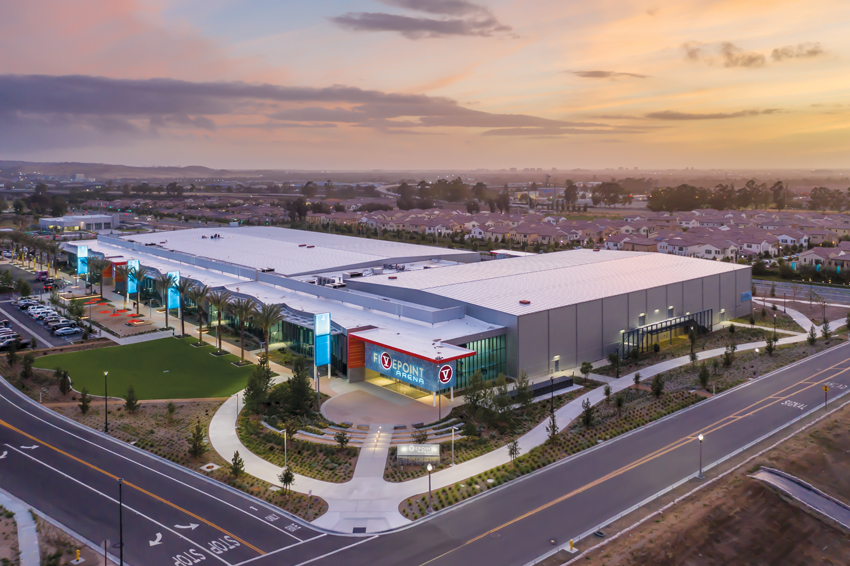
Photo courtesy of All Weather Insulated Panels
This $100-million, LEED Silver certified Great Park Ice & FivePoint Arena is the largest ice facility in California and one of the largest in the United States, and it features an IMP roof.
The truth is that IMPs can provide a high-performance roofing solution that offers exceptional thermal performance, unparalleled ease-of-installation, and gives the designer freedom to create building profiles rich in character. IMPs also meet or exceed multiple sustainable design criteria that contribute toward a project earning green building certifications or simply support the design and construction of healthier and more environmentally conscious buildings.
This course will explore the use of insulated metal panels as a roofing solution. Features of the panels, including their material construction, will be discussed as will the wide range of benefits that these products can offer a project. Multiple case studies will be profiled throughout showcasing how architects around the United States have successfully applied this IMP roofing system.
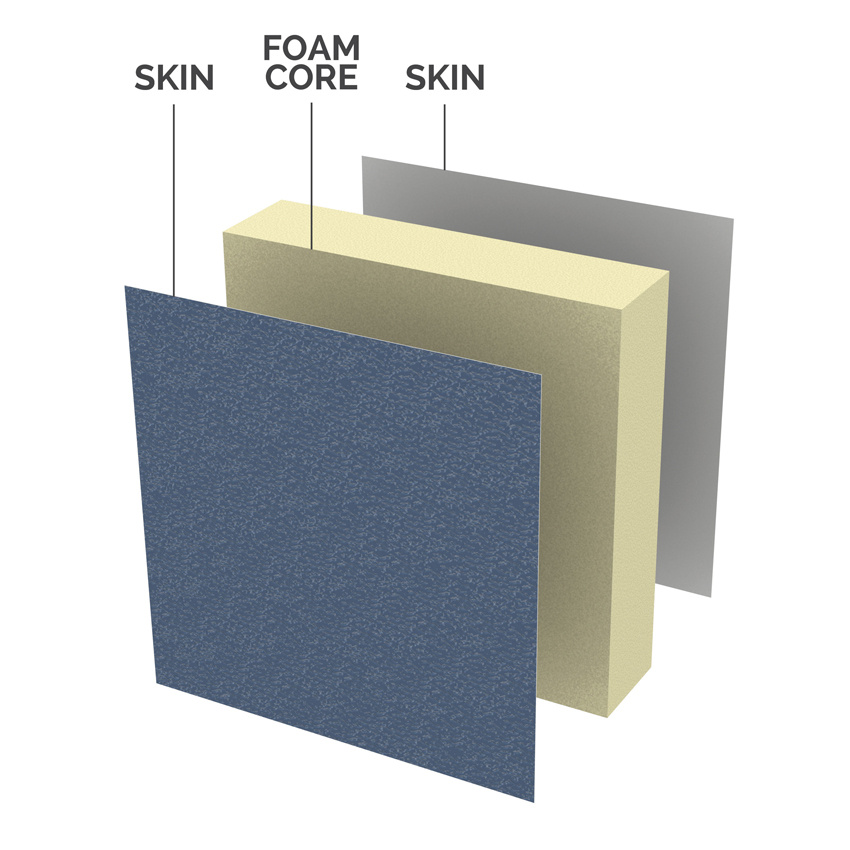
Image courtesy of Metal Construction Association
IMPs are lightweight sandwich panels comprised of exterior and interior metal skins that have an insulating foam core.
Introducing Insulated Metal Panel (IMP) Roofing
IMPs are lightweight sandwich panels comprised of exterior and interior metal skins that have an insulating foam core. The metal substrates most often used for the faces of painted IMPs are G90 galvanized steel or AZ50 aluminum-zinc coated steel, while unpainted roof panels are typically AZ55 aluminum-zinc. Many panels can also be manufactured from stainless steel or aluminum.
The interior-facing surface is typically finished with a nominal standard polyester coating in a light-reflective and easy-to-maintain color. The foam is injected or poured in place between the two metal sheets, where it expands, cures, and bonds to the metal skins in a matter of seconds. The insulation completely fills the cavity, allowing the solution to offer incredible thermal performance.
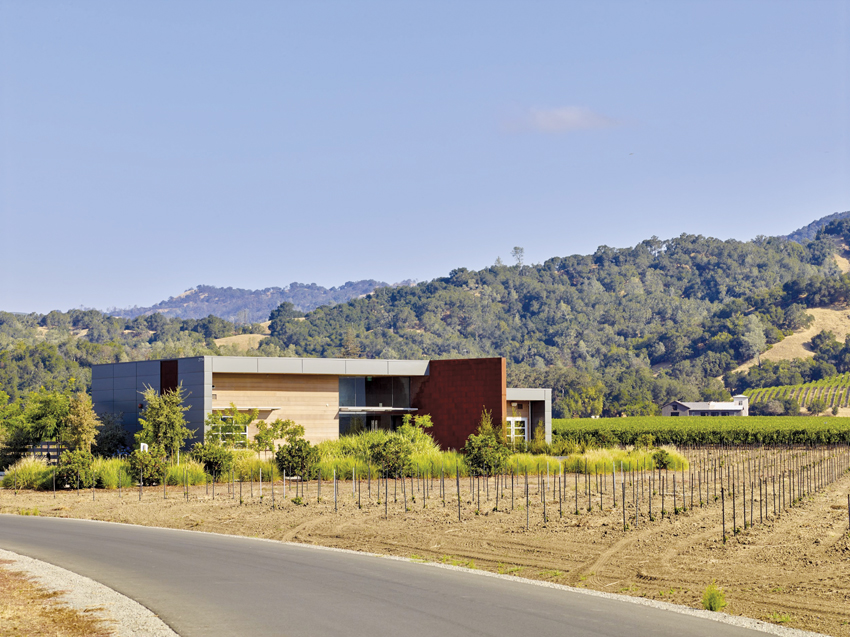
Photo courtesy of Metl-Span
The Zialena Winery production facility and hospitality a in Geyersville, California, was constructed using steel framing and insulated metal panels for the walls and roofing.
The combination of the two metal skins, the interior layer of insulation, and the embedded side joint sealant creates an assembly that serves as a water-control layer, air-control layer, and vapor control with a durable, UV-resistant exterior surface. The insulation provides the thermal control layer, and the interior metal face, in conjunction with the sealant, provide an air-control layer, and a vapor-control layer.
The location of these control layers makes an IMP assembly something of a perfect roof. The water-, air-, and vapor-control layers are all located on the exterior of the structure, with thermal control located inboard along with a duplicate air- and vapor-control layer. Because of their construction, IMPs can be used in all climate zones—cold, hot, humid, dry, mixed, or marine.
As a roofing solution, IMPs provide exceptional insulating properties, superior spanning capability, accelerated installation times, and recycled content. These systems can be installed on both low- and steep-slope roofs, allowing for use in most commercial and residential projects. IMP roofs beat competing roofing systems on weather-tightness and achieve a Class A rating for external fire. They can also be integrated with other wall and roof systems while maintaining proper control-layer continuity.
These panels can be designed to satisfy a variety of performance specifications, including insulation values, span lengths, and load/span capabilities. Their ability to be customized enables architects to find an IMP solution that is the right fit for any project.
History of IMPs
IMPs first emerged as a building product in the 1960s. While predominantly used as an exterior wall assembly, these panels were, even then, used as a roofing solution. Throughout the last 60 years, the materials and production methods have advanced considerably. IMP manufacturers were originally responsible for creating the individual components—the metal panels and the insulation—as well as assembling them. Today, there are major chemical companies invested in improving and producing foam core insulation with increasing levels of thermal performance and fire resistance. This has allowed IMP manufacturers to focus on improving the construction of the overall assembly. This divide-and-conquer approach has resulted in tremendous innovation within the IMP industry.
Wall Panels and Roofing Panel Profiles
Beyond performance improvements, IMPs are available in a wide variety of colors, widths, profiles, and finishes. For exterior wall applications, panel profiles are often described as ribbed, fluted, planked, or flat. These panels can have texture, be embossed, or feature a sprayed-on aggregate that creates a faux stone appearance. Panels can be applied vertically or horizontally, depending upon the joinery.
Roof panels also offer different types of joinery and profiles. There are two basic categories of roof panel profiles: standing seam profiles and through-fastened profiles. Each offers its own blend of benefits. Let’s take a closer look at how these profiles are different and the advantages that they offer on a project.
Roof panels with a standing seam profile are mechanically seamed together during installation. This delivers incredible weathertightness. Standing seam panels are also notable because there are no exposed fasteners within the envelope boundaries. The fasteners that connect the panel to the roof framing are covered when the next panel is joined to it.
Several IMP manufacturers offer distinctive profiles, giving architects several aesthetic options from which to choose. A traditional joinery is a standing seam panel with a 2-inch straight leg. Some manufacturers offer panels with a T-shaped joinery. There are also roof panels that feature a trapezoidal joinery. These panels have a 2-inch leg and a trapezoidal lower half, creating a panel installation with greater dimension across the face of the roof.
Through-fastened profiles refer to panels where the fasteners are exposed or visible. While these solutions may not provide the flawless aesthetic created by the standing seam panels, through-fastened panel systems can be installed quicker than the standing seam variety because they do not require that the installer mechanically seam the panels together.
There is a common misconception in the design and construction industry that insulated metal panels, often referred to as IMPs, are only suited to provide a solution for an exterior wall in the building envelope. This unfortunate misunderstanding unnecessarily limits designers to roof systems such as traditional built-up and single-membrane roofs with limited service life spans, or traditional metal roofs with independent thermal and moisture barriers that must be detailed and installed as separate materials and might suffer from installation mistakes that compromise the thermal performance or moisture management.
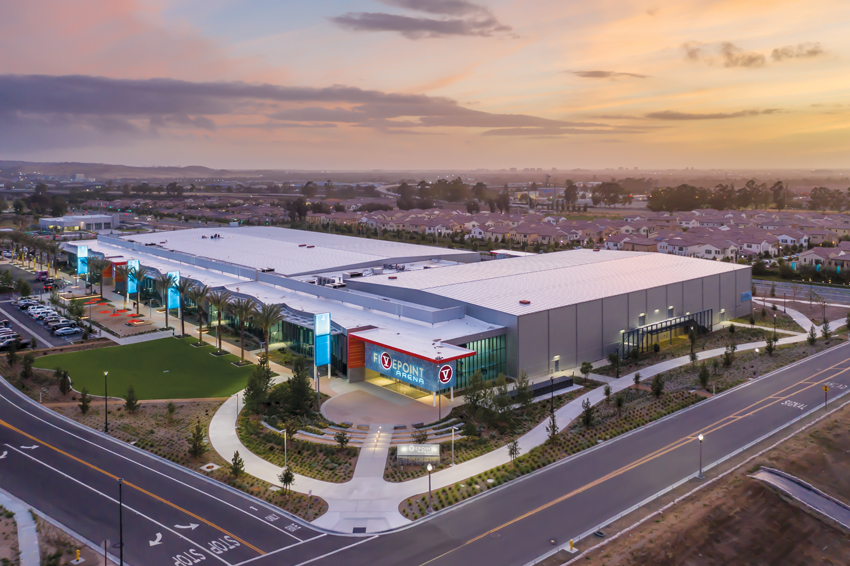
Photo courtesy of All Weather Insulated Panels
This $100-million, LEED Silver certified Great Park Ice & FivePoint Arena is the largest ice facility in California and one of the largest in the United States, and it features an IMP roof.
The truth is that IMPs can provide a high-performance roofing solution that offers exceptional thermal performance, unparalleled ease-of-installation, and gives the designer freedom to create building profiles rich in character. IMPs also meet or exceed multiple sustainable design criteria that contribute toward a project earning green building certifications or simply support the design and construction of healthier and more environmentally conscious buildings.
This course will explore the use of insulated metal panels as a roofing solution. Features of the panels, including their material construction, will be discussed as will the wide range of benefits that these products can offer a project. Multiple case studies will be profiled throughout showcasing how architects around the United States have successfully applied this IMP roofing system.
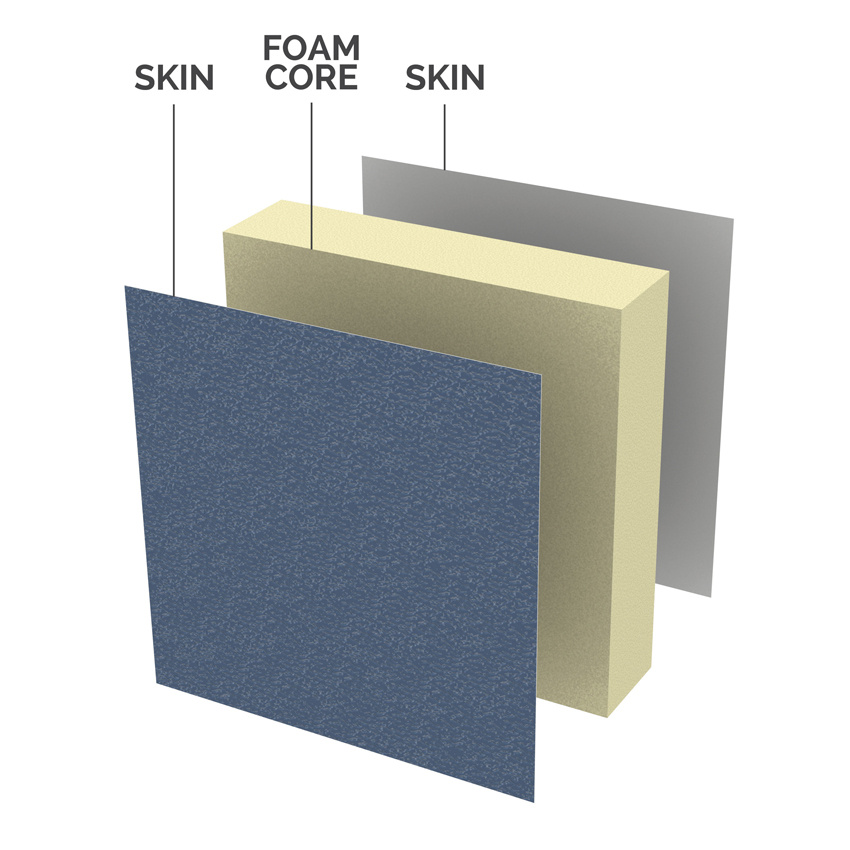
Image courtesy of Metal Construction Association
IMPs are lightweight sandwich panels comprised of exterior and interior metal skins that have an insulating foam core.
Introducing Insulated Metal Panel (IMP) Roofing
IMPs are lightweight sandwich panels comprised of exterior and interior metal skins that have an insulating foam core. The metal substrates most often used for the faces of painted IMPs are G90 galvanized steel or AZ50 aluminum-zinc coated steel, while unpainted roof panels are typically AZ55 aluminum-zinc. Many panels can also be manufactured from stainless steel or aluminum.
The interior-facing surface is typically finished with a nominal standard polyester coating in a light-reflective and easy-to-maintain color. The foam is injected or poured in place between the two metal sheets, where it expands, cures, and bonds to the metal skins in a matter of seconds. The insulation completely fills the cavity, allowing the solution to offer incredible thermal performance.
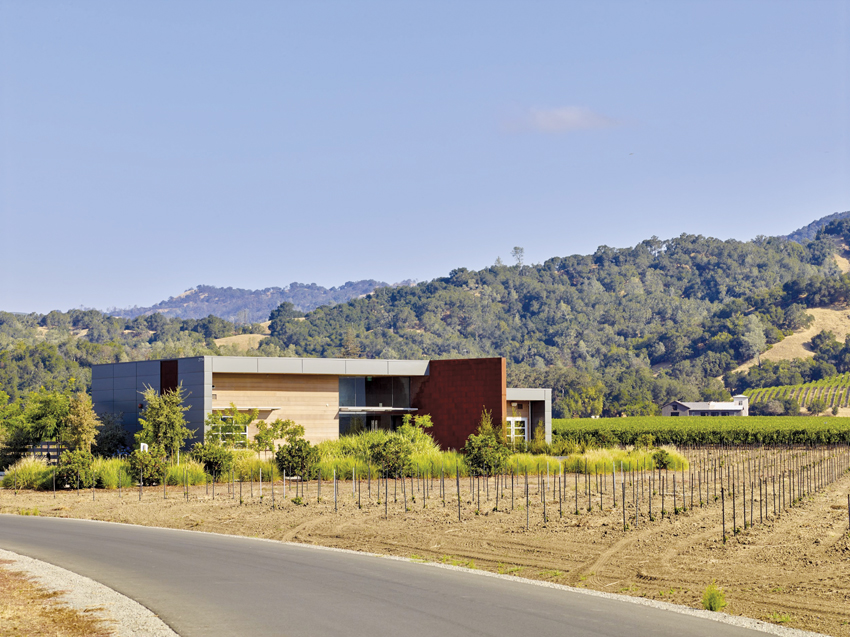
Photo courtesy of Metl-Span
The Zialena Winery production facility and hospitality a in Geyersville, California, was constructed using steel framing and insulated metal panels for the walls and roofing.
The combination of the two metal skins, the interior layer of insulation, and the embedded side joint sealant creates an assembly that serves as a water-control layer, air-control layer, and vapor control with a durable, UV-resistant exterior surface. The insulation provides the thermal control layer, and the interior metal face, in conjunction with the sealant, provide an air-control layer, and a vapor-control layer.
The location of these control layers makes an IMP assembly something of a perfect roof. The water-, air-, and vapor-control layers are all located on the exterior of the structure, with thermal control located inboard along with a duplicate air- and vapor-control layer. Because of their construction, IMPs can be used in all climate zones—cold, hot, humid, dry, mixed, or marine.
As a roofing solution, IMPs provide exceptional insulating properties, superior spanning capability, accelerated installation times, and recycled content. These systems can be installed on both low- and steep-slope roofs, allowing for use in most commercial and residential projects. IMP roofs beat competing roofing systems on weather-tightness and achieve a Class A rating for external fire. They can also be integrated with other wall and roof systems while maintaining proper control-layer continuity.
These panels can be designed to satisfy a variety of performance specifications, including insulation values, span lengths, and load/span capabilities. Their ability to be customized enables architects to find an IMP solution that is the right fit for any project.
History of IMPs
IMPs first emerged as a building product in the 1960s. While predominantly used as an exterior wall assembly, these panels were, even then, used as a roofing solution. Throughout the last 60 years, the materials and production methods have advanced considerably. IMP manufacturers were originally responsible for creating the individual components—the metal panels and the insulation—as well as assembling them. Today, there are major chemical companies invested in improving and producing foam core insulation with increasing levels of thermal performance and fire resistance. This has allowed IMP manufacturers to focus on improving the construction of the overall assembly. This divide-and-conquer approach has resulted in tremendous innovation within the IMP industry.
Wall Panels and Roofing Panel Profiles
Beyond performance improvements, IMPs are available in a wide variety of colors, widths, profiles, and finishes. For exterior wall applications, panel profiles are often described as ribbed, fluted, planked, or flat. These panels can have texture, be embossed, or feature a sprayed-on aggregate that creates a faux stone appearance. Panels can be applied vertically or horizontally, depending upon the joinery.
Roof panels also offer different types of joinery and profiles. There are two basic categories of roof panel profiles: standing seam profiles and through-fastened profiles. Each offers its own blend of benefits. Let’s take a closer look at how these profiles are different and the advantages that they offer on a project.
Roof panels with a standing seam profile are mechanically seamed together during installation. This delivers incredible weathertightness. Standing seam panels are also notable because there are no exposed fasteners within the envelope boundaries. The fasteners that connect the panel to the roof framing are covered when the next panel is joined to it.
Several IMP manufacturers offer distinctive profiles, giving architects several aesthetic options from which to choose. A traditional joinery is a standing seam panel with a 2-inch straight leg. Some manufacturers offer panels with a T-shaped joinery. There are also roof panels that feature a trapezoidal joinery. These panels have a 2-inch leg and a trapezoidal lower half, creating a panel installation with greater dimension across the face of the roof.
Through-fastened profiles refer to panels where the fasteners are exposed or visible. While these solutions may not provide the flawless aesthetic created by the standing seam panels, through-fastened panel systems can be installed quicker than the standing seam variety because they do not require that the installer mechanically seam the panels together.
Features and Benefits
It is very common to use IMP roof panels in Europe. They are not used as roofing solutions as much in the United States, but that is changing as architects here become more aware of the benefits of an IMP solution and as the building and energy codes evolve to require greater levels of thermal performance and continuous insulation. Also, IMPs support many sustainable design criteria and so they are often selected on projects that are either pursuing green building certifications or where the owners want the buildings designed to be green conscious.
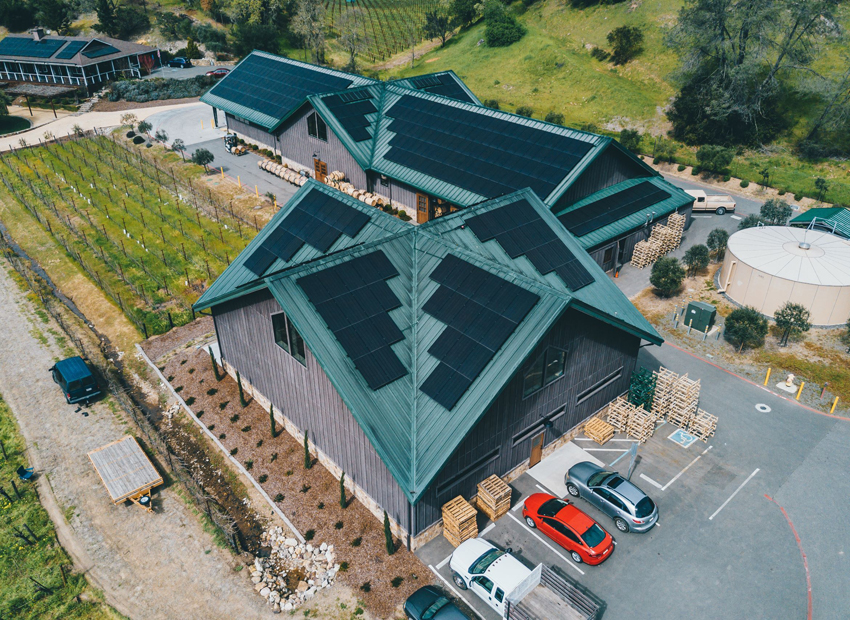
Photo courtesy of All Weather Insulated Metal Panels
The roof on the Theorum Winery offers the look of traditional standing-seam roof for a stylish appearance as well as the high R-value, energy efficiency, and outstanding fire rating that come with IMPs.
Impressive Thermal Performance
Energy codes are increasingly requiring that building envelopes be designed to deliver higher levels of thermal performance. This means that building envelopes must do a better job of minimizing the movement of thermal energy across the assembly in the form of thermal gains in the summer or thermal losses in the winter.
The metric used to describe a material’s ability to resist heat flow is the R-value. IMP foam cores are is typically tested at 1-inch thickness. The higher the R-value of a material indicates that the material is better at resisting the flow of heat and is a better insulator.
IMPs have a foam core that can provide a thermal performance of R-7 per inch or greater. This R-value is impressive when you look at the typical thermal resistance of other types of insulation. Mineral fiber and cellular glass have a typical R-value of R-3 to 3.5 per inch. Expanded polystyrene typically offers R-4 per inch. Extruded polystyrene another popular insulation solution has an R-value of R-5. Many IMPs are manufactured with a type of polyurethane insulation that can achieve R-values of R-7 or more per inch.
Energy codes today can require the commercial envelope to contain enough insulation to achieve R-values in the 40s. This better-performing insulation can be used to create panels that achieve R-values of up to 45 in dramatically thinner solutions than could be produced with mineral wool or extruded polystyrene. Generally speaking, as the thickness of an IMP wall system increases from 1 to 6 inches, the R-values increase from 7 to 48. The R-value of roof systems also ranges from R-10 to R-48, as the thickness of the panels ranges from 1.5 to 6 inches.
Beyond increasing requisite R-values, the thermal performance of the building envelope can be improved by eliminating any thermal bridges. A thermal bridge refers to a solid connection of higher thermal conductivity between the warm side and the cool side of an assembly that allows heat to flow freely between the sections where the insulation is present.
Research into the science behind the thermal performance of a building has revealed that the effect of thermal bridging plays an important role, even in well-insulated enclosures. The R-value often does not include the impact of specific thermal bridges, so the industry is moving toward designing building enclosures with fewer thermal bridges, and the major motivators behind this movement are the model code bodies.
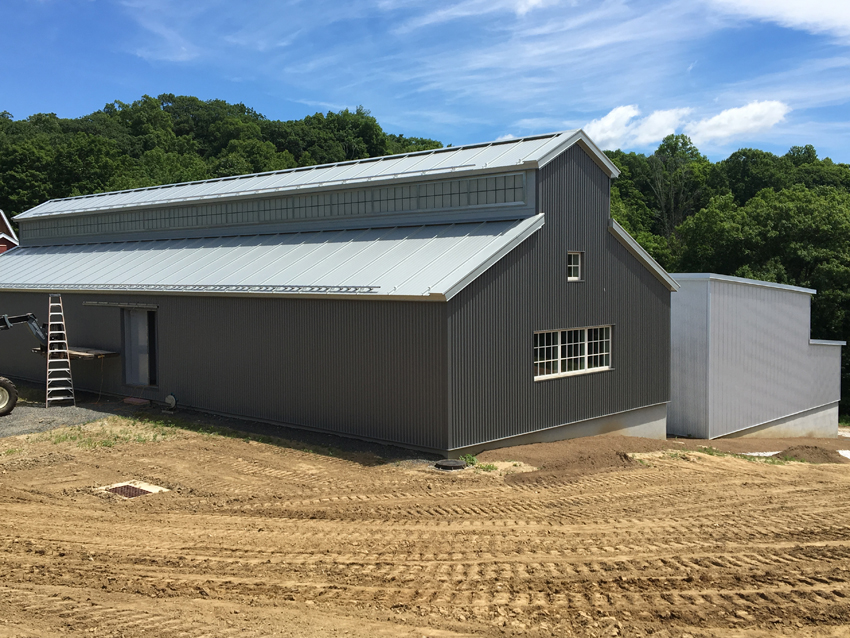
Photo courtesy of ATAS International, Inc.
IMPs on the walls and roof of this barn-style building provide superior insulating properties, and their outstanding spanning capabilities and one-pass installation makes them quick to install, saving costs compared to other wall assemblies.
Inherent Continuous Insulation
Code language is being modified to emphasize how important it is to avoid thermal bridges and the energy inefficiencies they create in the building envelope by requiring continuous insulation. Continuous insulation, or c.i., is defined by ANSI/ASHRAE/IES Standard 90.1-2019, Energy Efficiency Standard for Buildings Except Low-Rise Residential Buildings (ASHRAE 90.1) as, “Insulation that is uncompressed and continuous across all structural members without thermal bridges other than fasteners and service openings.” It is designed to minimize thermal bridging, primarily of wood- and steel-framed structures, and it can be installed on interior, exterior, or is integral to any opaque surface of the building envelope.
ASHRAE 90.1 shows a clear trend for requiring continuous insulation, specifically in climate zones 5-8. Properly installed, continuous insulation reduces thermal bridging, increases the effective R-value of the wall system, helps control condensation, and air/water infiltration.
IMPs have no compression of insulation and no thermal bridging. The joint geometry of IMP systems addresses thermal bridging in a more robust manner than typical site-built assemblies for walls and roofs, a design asset for maintaining thermal performance.
Sustainability Qualities
Code compliance and efficiency is one thing. Sustainability is another. The concept of sustainability goes deeper and demands more. Products that support sustainable design must do more than make interiors more efficient. They must simultaneously either improve, or at the very least not damage, the quality of the interior environment and the health of its occupants and minimize their environmental footprint. For that reason, green building programs consider criteria like the recycled content or recyclability of a product. They evaluate whether a solution off-gases chemicals that could be toxic to humans or deplete the ozone layer. IMPs support many of the sustainable criteria beyond improving the thermal efficiency of the project.
Recycled Content
Green building programs incentivize the use of products or materials with recycled content to increase the overall demand for building products that incorporate recycled content, reducing impacts on the Earth that result from the extraction and processing of virgin materials.
Recycled content is technically the content of a product or material that has been made from pre- and post-consumer material. Pre-consumer material is diverted waste from manufacturing. Post-consumer material is waste that is redirected from landfills after a consumer has used it and put to use in other forms.
The steel faces in an IMP contain a minimum total recycled content of 30 percent or more. The post-consumer recycled content is approximately 23 percent and pre-consumer recycled content is approximately 7.3 percent.
100 Percent Recyclable
An interest in whether a product is recyclable goes hand-in-hand with an interest in whether it contains recycled material. In both cases, waste is diverted from landfills and reused. A product is recyclable if it can be recycled.
The steel facings and foam core in insulated metal panels are virtually 100 percent recyclable at the end of their service life.
No Volatile Organic Compounds
Volatile organic compounds (VOCs) are gases emitted by products or chemicals that may have short- and long-term adverse health effects. According to the EPA, VOCs are emitted by an array of products numbering in the thousands. Examples include paints and lacquers, cleaning supplies, pesticides, building materials and furnishings, office equipment such as copiers, correction fluids and carbonless copy paper, and more.
IMPs and their accessories do not produce measurable VOCs. The paint is factory applied and baked on, and the sealants are generally more than 95 percent solid (non-skinning butyl) or moisture-cured polyurethanes. This means they can be incorporated into the building envelope and roof without negatively impacting the indoor air quality.
Zero Ozone Depletion Potential
Ozone depletion potential (ODP) measures the potential for a single molecule of refrigerant to destroy the ozone layer. Ozone-depleting substances are used in refrigeration, air conditioning, building insulation, and firefighting equipment in buildings. Unfortunately, according to the U.S. Green Building Council (USGBC), the newer ozone-friendly alternatives are potent greenhouse gases that are a threat to climate change. This creates the quandary where the solution to ozone protection is becoming a problem for climate change. The solution is to select zero-OPD and low-GWP alternatives. Global Warming Potential (GWP) is a value that quantifies the direct effect of global warming of a compound or gas. According to the USGBC, the direct effects of global warming are measured by comparing them to CO2, which has a GWP of 1.0.
Most IMPs have zero ODP, and there are no limits by the EPA or Environment Canada for its use today or in the future. Furthermore, many manufacturers offer foams using low-GWP options.
Low Global Warming Potential
Blowing agents are gases that expand foam insulation to its rigid shape. They are used to manufacture a few different types of insulation, including extruded polystyrene rigid panels and spray polyurethane. Previously, the blowing agents used in insulation were potent greenhouse gases and, as such, had a high level of global warming potential. Some blowing agents in common use years ago had a GWP in the range of 5,000. Several low-GWP alternatives have become available over the past few years.
The insulation used inside IMPs meets current EPA blowing agent requirements for the reduction of Global Warming Potential.
Net Zero Energy Targets
A net-zero energy building (NZEB) is a residential or commercial building with greatly reduced energy needs that supplements with on-site energy generation to the point that external energy use averages out to zero over the course of a year. IMPs contribute significantly toward net-zero energy targets by yielding as much as a 30 percent reduction in a building’s energy use.
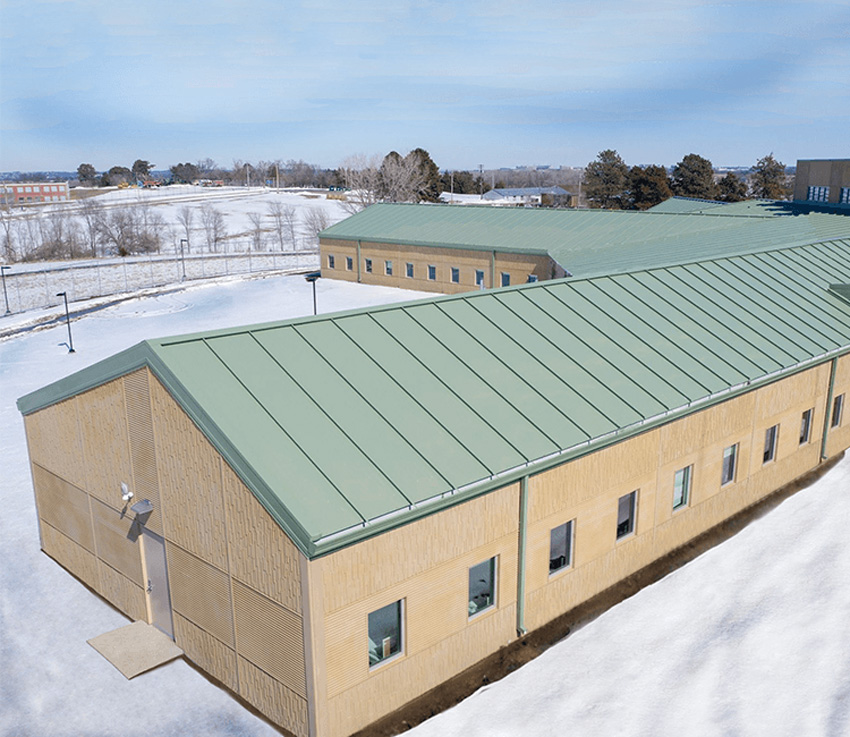
Photo courtesy of ATAS International, Inc.
The IMP roofing on Nebraska Correctional Center for Women in Lincoln, Nebraska, provides a low-maintenance, highly energy-efficient solution for the facility.
Design Flexibility
IMPs also offer designers an incredible level of flexibility in designing building envelopes and roofs. There are a wide variety of standard and custom colors available. Special print patterns can mimic the look of stone or weathered metal, and many manufacturers offer cool roof pigments for added building energy performance.
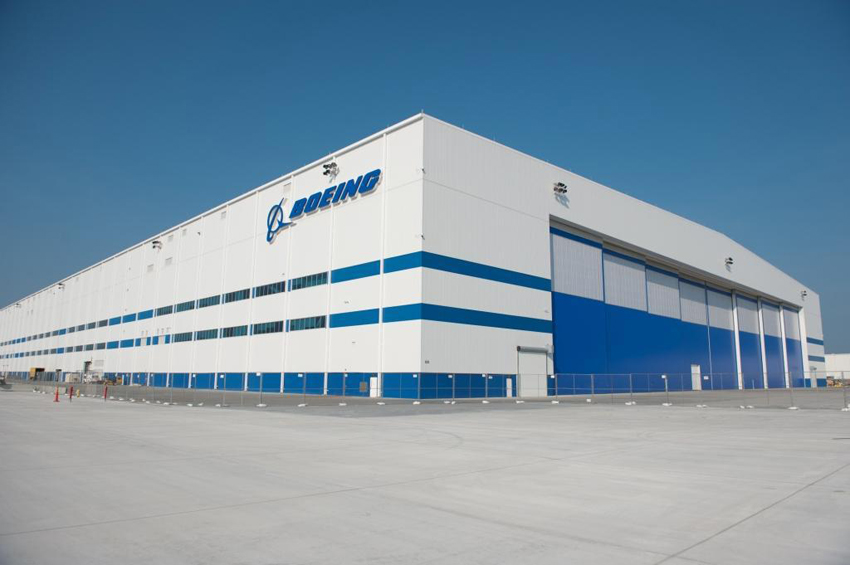
Photo courtesy of Centria
The need for a sleek, high-tech look combined with the aggressive timing made metal an ideal choice for the Boeing building in Charleston, South Carolina. IMPs were chosen for their aesthetic and inherent performance qualities.
High Strength-to-Weight Ratio
IMPs are very strong structurally due to the composite action between the flat metal facings and the foam core. The metal skin acts like the flange of a beam, resisting bending stresses. The foam core acts like the web of a beam, resisting the shear stresses. The result is that IMPs have a high strength-to-weight ratio.
This high strength-to-weight ratio gives IMPs excellent spanning capability between supports. For example, for a 2-inch panel, most wind load requirements in the 20 to 30 psf range can be met with 7- to 10-foot span conditions. Snow loads up to 30 psf can be met with this same span.
It should be noted that the thickness of the core, the panel profile, connection details, and the gauge of the metal facings all contribute toward determining the actual span capability of any specific panel. Manufacturers normally publish the span capabilities of their panels in load span tables. Many also have ICC-ES reports available for download. Architects can incorporate this increased span capability into the roof plan.
Structural load capacity should be verified by representative structural tests for positive as well as negative wind loads as shown in testing, such as ASTM E72: Standard Test Methods of Conducting Strength Tests of Panels for Building Construction and ASTM E330: Standard Test Method for Structural Performance of Exterior Windows, Doors, Skylights, and Curtain Walls by Uniform Static Air Pressure Difference. The maximum allowable deflection limits are set by building codes. They can be found in Table 1604.3 of the 2018 International Building Code (IBC 2018). The local building code should be referenced for the applicable limiting criteria. The effects of snow load and long-term loads on roof panels should be considered as appropriate in the structural analysis.
Compliance with the structural provisions of the code can be shown in two ways. The IMP manufacturer will provide calculations sealed by a professional engineer verifying that all factors affecting the load-carrying capacity of the panels have been analyzed and verified by testing, and that the structural capacity of the panels meets the project requirements or the IMP manufacturer will provide sufficient documentation to the engineer of record (EOR) demonstrating this performance. In the latter case, an evaluation report from a third-party agency such as ICC-ES or IAPMO showing compliance with ACO4 is normally used.
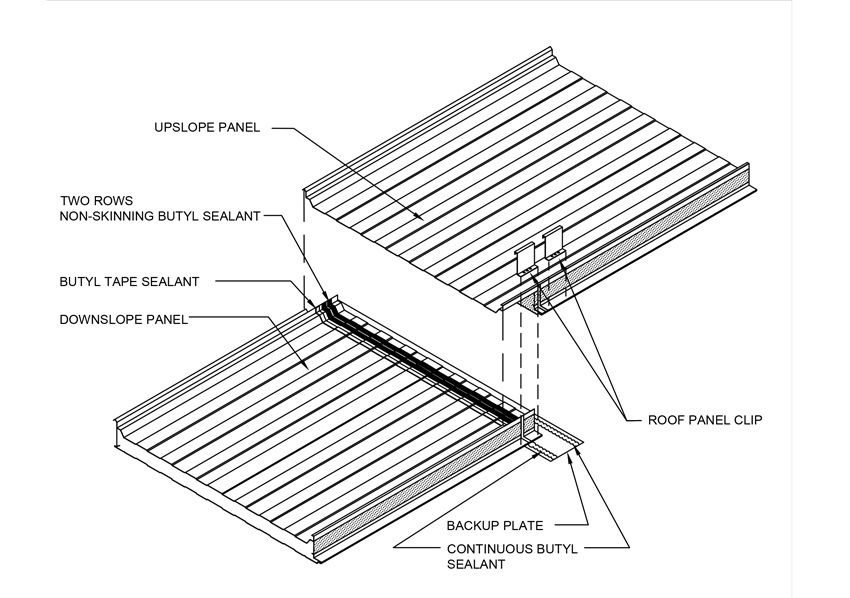
Image courtesy of Kingspan Metal Panels
Fast Installation
Another benefit of selecting an IMP roof is the speed with which it can be installed. Instead of the multi-piece field-assembled metal systems or built-up roof systems that require the addition of several individual layers and components, the IMP roof system installation is comprised of basically one installation step. The panel contains the exterior face, the insulation, the air and water barriers, and an interior face. Installers only need to install the panel. Now this is a rather simplified explanation, but it does correctly convey the comparative simplicity of the different installation processes.
This quicker installation results in labor cost savings and dramatically shorter project schedules. It also allows the inside finish work to begin sooner. Let’s take a closer look at how these panels are installed and how they are able to offer such a time-saving benefit.
The first step in the process is getting the panels to the elevation of the roof. Numerous lifting methods are available, but suction lifters are the safest and most efficient method.
One item to note about IMP roof panels is that thermal expansion is accommodated by thermal bow which induces thermal stress. Because IMPs are a composite sandwich with both the interior and exterior facings bonded to the core, there is no significant linear differential expansion between the interior and exterior facings. Instead, the expansion of the panel is distributed among the individual spans as curvature, called thermal bow, rather than linear expansion. Because the overall panel does not significantly elongate or contract, there is no need to install an insulated metal roof panel with slotted clips. Thermal bow does not adversely affect the performance of the panels in a properly detailed system.
One step that is unique to IMP installation is the creation of an end lap. An end lap can be necessary when the length of the panel installed at the perimeter of the roof must be adjusted to perfectly fit the size of the roof. To create an end lap, installers will typically cut away the inner facing (liner) and foam core, leaving a nominal exterior facing extension that will then lap over the lower panel. The length of the extension and end lap is dependent on the slope of the roof and the panel profile. The end lap joints are caulked and fastened according to the roof panel manufacturer’s recommendations.
Applications
The combination of the versatility, thermal performance, sustainable design qualities and speedy installation offered by IMPs, make them an attractive roofing solution for almost any type of application—retail, commercial, warehouse, recreational centers, entertainment venues, educational facilities, and residences are just a few of the places where IMP roofs have been installed. Even projects with the most demanding performance specifications, such as government buildings and climate-controlled facilities, can be satisfied with an IMP roof.
Summary
Here are a few of the key takeaways from this course exploring the benefits of IMP roofing.
Insulated metal panels, or IMPs as they are often called, are lightweight sandwich panels comprised of exterior and interior metal skins and an insulating foam core.
Every IMP contains the water-control layer, air-control layer, vapor control, and insulation for thermal control.
IMPs can be used to create exterior walls and roof assemblies.
IMP roofing panels have two types of profiles: a standing seam profile and a through-fastened profile. Panels with standing seam profiles are mechanically seamed together during installation and the fasteners are not visible. Panels with through-fastened profiles have fasteners that are exposed and visible.
IMP roofs can be designed to deliver an R-value of up to R-48.
IMPs offer continuous insulation inside the panel, with no compression of insulation and no thermal bridging.
This solution has several sustainability-related qualities including its recycled content and recyclability. Insulated metal panels do not produce VOCs, have zero ozone depleting potential, and meet current EPA blowing agent requirements.
IMP panels have high strength-to-weight ratios that allow for excellent spanning capability.
Another benefit of selecting an IMP roof is the speed with which it can be installed. The installation process is essentially one self-contained panel being installed in one step.
Ultimately, roofs constructed from IMPs offer architects a way to reliably meet the increasingly stringent thermal performance requirements demanded by building codes, complete with all necessary moisture and air barriers, because the installation is so straightforward and streamlined. Avoiding the layer-by-layer, trade-intensive installation process typically employed in built-up roof assemblies avoids a lot of potential mistakes and missteps that will compromise the performance of the roof.